W niniejszym artykule wyjaśniono, w jaki sposób płytka została zaprojektowana, uzasadniono podjęte decyzje projektowe i wskazano, jak płytka odpowiada na różne wymagania poszczególnych aplikacji. Płytka ze zbudowanym rozwiązaniem pomaga inżynierom szybciej rozpocząć własne prace projektowe i skrócić czas potrzebny na wprowadzenie na rynek gotowych, dobrze przemyślanych rozwiązań, ograniczając wysiłki wkładane w projektowanie i weryfikację.
Bezszczotkowe silniki stałoprądowe
Silniki stałoprądowe znane są już od czasów Michaela Faradaya, Josepha Henry’ego i Andrew Gordona, a więc od lat 40. XVIII wieku, kiedy to zademonstrowano, że prąd przepływający przez przewód w polu magnetycznym powoduje powstawanie siły. Pomimo tych wczesnych badań, dopiero w latach 80. XIX wieku silniki tego typu weszły do komercyjnego użycia.
Pierwsze z silników miały szczotki. To dlatego, że konieczne jest by co 180° odwracać polaryzację prądów, aby wirnik obracał się cały czas w tę samą stronę. Szczotki utrzymują kontakt z rozdzielonym komutatorem, co pozwala właśnie na zmianę kierunku przepływu prądu wewnątrz przewodnika (ilustracja 1). Kontakt mechaniczny jest realizowany z użyciem szczotek, ale to znowu sprawia, że powstają duże ilości zakłóceń elektromagnetycznych (EMI), iskier, a i żywotność silnika spada ze względu na stopniowe ścieranie się szczotek i samego komutatora.
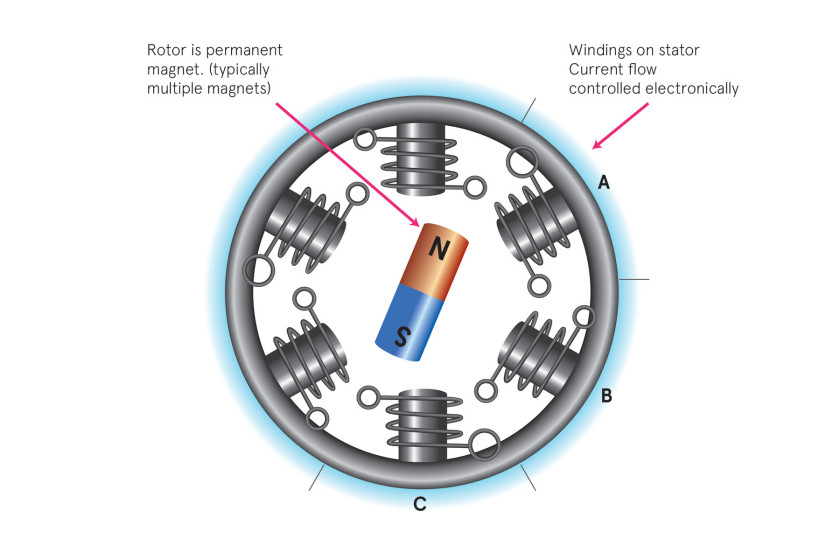
W 1962 roku, opracowanie technologii układów półprzewodnikowych pozwoliło T.G Wilsonowi i P.H. Trickey’owi na stworzenie pierwszego bezszczotkowego silnika stałoprądowego, w którym komutator został zastąpiony obwodem elektronicznym, eliminując tym samym wady szczotek i pozwalając na uzyskanie wyższego stosunku momentu do masy, a zarazem na zwiększoną sprawność silników. W silnikach BLDC wirnik ma magnesy stałe, a stator zawiera elektromagnesy, których polaryzację zmienia się elektronicznie, by napędzać wirnik (ilustracja 2). Silniki BLDC można budować w wersjach jednofazowych, dwufazowych i trójfazowych, z czego ta ostatnia jest najbardziej popularna.
Dziś bezszczotkowe silniki stałoprądowe to preferowana technologia, co pozwala poprawić wydajność wszelkiego rodzaju urządzeń, począwszy od twardych dysków komputerowych i robotów przemysłowych, a kończąc na pojazdach elektrycznych i wentylatorach.
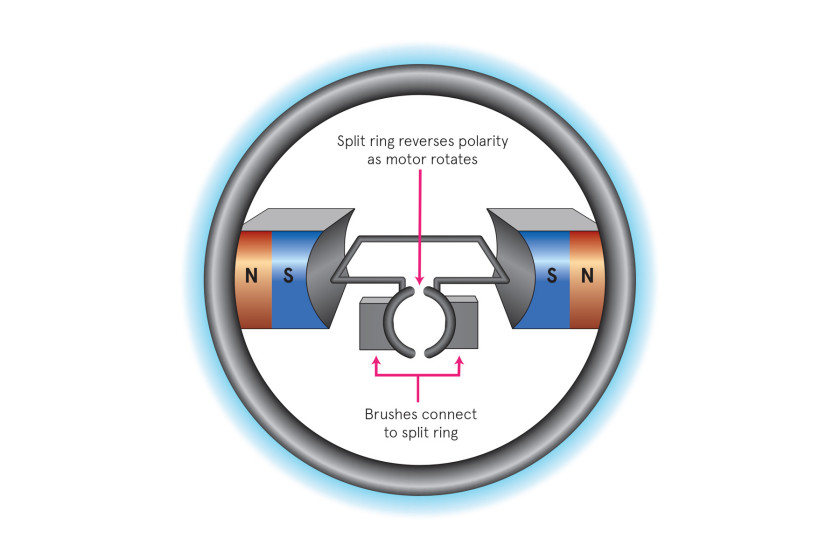
Sterowanie silnikami BLDC
Jako że komutacja jest sterowana elektronicznie, konieczne jest zapewnienie jakiegoś sposobu monitorowania pozycji wirnika. Tradycyjnie było to realizowane za pomocą czujnika Halla, ale jeśli pozycja kątowa wirnika jest znana z większą dokładnością, sterowanie staje się bardziej precyzyjne. Alternatywą jest pomiar prądu płynącego przez każde z uzwojeń, do czego używa się odpowiednich boczników. Aby mieć pewność, że przygotowana płytka demonstracyjna znajdzie zastosowanie w tak wielu różnych aplikacjach, jak to tylko możliwe, firma Renesas zdecydowała się zaimplementować rezystory bocznikujące oraz zamontować czujnik pozycji, dzięki któremu możliwe będzie testowanie projektów wymagających większej precyzji pomiaru.
Istnieje wiele różnych