Elementem tego programu jest wdrożenie zaawansowanych systemów kontroli, które sterują procesami produkcyjnymi w różnych instalacjach rafinerii. Jednym z dostawców takich rozwiązań, który od wielu lat współpracuje z Grupą Lotos, jest firma Honeywell. W artykule przedstawiamy złożony i wieloletni proces wdrażania przez nią w różnych częściach zakładu systemów APC (Advanced Process Control), opisujemy przebieg tworzenia aplikacji i osiągane korzyści, a także przedstawiamy zagadnienia dotyczące instalacji technologicznych znajdujących się w gdańskiej rafinerii.
CZĘŚĆ I: WPROWADZENIE DO APC
Czasy, kiedy operator ręcznie sterował zaworami w zakładach produkcyjnych, dawno odeszły w niepamięć. Obecnie sterowanie ręczne występuje jeszcze tylko w wyjątkowych wypadkach lub ewentualnie w systemach blokadowych mających wpływ na bezpieczeństwo danej instalacji. Pierwsze systemy regulacji automatycznej bazowały na regulatorach pneumatycznych PID (Proportional Integration Derivative).
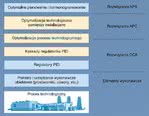
Rys.1 Poziomy możliwych rozwiązań sterowania procesami rafineryjno-petrochemicznymi
Następnie regulatory pneumatyczne zostały zastąpione elektronicznymi regulatorami PID, analogowymi i cyfrowymi. Obecnie kontrolę nad całymi grupami regulatorów na instalacji produkcyjnej zapewniają systemy sterowania DCS (Distributed Control System).
Właśnie dzięki wykorzystaniu DCS, powszechnie nazywanych rozproszonymi systemami sterowania, pierwsze próby zoptymalizowania kontroli procesów zachodzących w wybranych węzłach technologicznych w przemyśle rafineryjnym były możliwe i zakończyły się sukcesem. W systemach DCS tworzono logiki obsługujące kaskady regulatorów PID.
Programowano je tak, aby działały w sposób optymalny realizując sekwencje zadań. W DCS tworzono także algorytmy wyliczające optymalne wartości sterujące regulatorami PID, ale dopiero pojawienie się na rynku rozwiązań APC (Advanced Process Control) pozwoliło w pełni wykorzystać algorytmy optymalizacyjne oraz funkcjonalność systemów DCS nie tylko na poziomie jednego procesu, ale też wielu procesów jednocześnie. Poziomy możliwych rozwiązań sterowania procesami rafineryjno-petrochemicznymi firmy Honeywell przedstawiono na rysunku 1.
Dlaczego APC?
Jednoczesna możliwość optymalizacji wielu procesów technologicznych czyni rozwiązania APC bardzo atrakcyjnymi dla przemysłu rafineryjno-petrochemicznego, gdzie poszczególne procesy na różnych instalacjach są ściśle ze sobą powiązane i uzależnione jeden od drugiego. Warto w tym miejscu wspomnieć o rozwiązaniach optymalizacyjnych na poziomie planowania i ustalania harmonogramu produkcji APS (Advanced Planning and Scheduling), które służą do odpowiedniego rozdziału mocy przerobowych instalacji na poszczególne produkty w zależności od sytuacji rynkowej. Tak więc APC znajduje optymalne rozwiązanie na poziomie technologicznym (prowadzenie procesów), natomiast rozwiązania APS rozwiązują zagadnienia optymalizacji na poziomie wyższym - biznesowym, co przedstawia rysunek 1.
W przypadku instalacji z wieloma sprzężonymi ze sobą zależnościami procesowymi (coupling), klasyczne jednowymiarowe regulatory PID są często niewystarczające do zapewnienia poprawnego sterowania procesem. Dla tych przypadków (systemy MIMO - Multi Input Multi Output) stosuje się obecnie w algorytmach APC sterowanie z wykorzystaniem wielowymiarowych regulatorów. Firma Honeywell oferuje całą rodzinę rozwiązań z serii Profit Suite, wykorzystujących wymienioną powyżej technologię. Koncepcja tego typu rozwiązań została opracowana na początku lat 70 ubiegłego wieku.
Rozwiązanie układu macierzowego regulatora plus modelu wielowymiarowego jest znajdowane w czasie rzeczywistym z wykorzystaniem iteracji minimalizującej uchyb regulatora (least square error), wraz z predykcją trajektorii zmiennej sterowanej bazującej na otrzymanym modelu. Model obiektu otrzymywany jest w sposób empiryczny podczas tzw. step testów na pracującym obiekcie.
Step testy polegają na serii zaplanowanych i uzgodnionych z kierownictwem wymuszeń (zmian w wartościach sterujących procesem na tyle dużych, aby odbijały się w przebiegach zmiennych przewidzianych do kontroli i jednocześnie na tyle małych, aby nie zakłócały planów produkcyjnych). Znając zależności pomiędzy zadawanymi wymuszeniami i odpowiedziami instalacji oraz korzystając ze specjalistycznych narzędzi inżynierskich otrzymuje się model obiektu z reguły w postaci wielowymiarowej macierzy transmitancji.
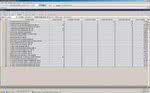
Rys.2 Jedna z tabel Profit Controllera służąca do jego konfiguracji
Dodatkowym atutem rozwiązania APC jest możliwość jego optymalizacji w zależności od funkcji celu stawianej przed algorytmem sterowania. Najpopularniejszymi rozwiązaniami regulatorów wielowymiarowych z możliwością optymalizacji są regulatory wykorzystujące równania Riccati'ego, np. LQR (Linear Quadratic Regulator) czy LQG (Linear- Quadratic-Gaussian).
Bazując na powyższych rozwiązaniach, firma Honeywell opracowała własny podobny algorytm regulacji połączonej z optymalizacją sterowania. Przeprowadzając optymalizację w module Profit Controller, definiuje się odpowiednie współczynniki optymalizacyjne dla poszczególnych zmiennych. Dzięki temu regulator potrafi maksymalizować lub minimalizować ich wartości.
Wagi dla optymalizacji określane są za pomocą założeń przygotowywanych przez dział planowania produkcji zakładu (mogą to być to być np. ceny danych produktów i surowców, ropy, benzyn, diesla, rafinatu, pary, gazu oleju opałowego itp.). Ewentualnie definiuje je technolog lub inżynier procesowy.
Dodatkowo Profit Controller ma wbudowane algorytmy pozwalające na unikanie "gwałtownych" odpowiedzi wielowymiarowego regulatora dzięki dekompozycji SVT (Singular Value Technique), natomiast dzięki algorytmowi RCA (Range Control Algorithm ) kontroler działa optymalnie z możliwością jego strojenia w zależności od aktualnej jakości regulacji. Algorytm RCA zapewnia również utrzymanie minimalnych "oszczędnych" zmian w wartościach wyliczanych wartości zadanych dla regulatorów podrzędnych PID (minimum move solution).
Wszystkie wymienione powyżej funkcje oraz wiele innych narzędzi dostępnych w produkcie APC firmy Honeywell są stabelaryzowane i przedstawione w oprogramowaniu regulatora w bardzo przejrzysty sposób, co ułatwia jego konfigurację. Każda za zmiennych procesowych zdefiniowanych w kontrolerze ma przypisane konkretne własności, do których inżynier opiekujący się aplikacją ma bezpośredni dostęp. W związku z łatwością programowania wymienionych wyżej regulatorów ich algorytmy i pochodne są bardzo popularne również w rozwiązaniach APC dla innych gałęzi przemysłu chemicznego.
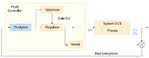
Rys.3 Struktura APC z użyciem Profit Controller
W rozwiązaniach APC regulator utrzymuje przebiegi zmiennych regulowanych (tzw. zmienne kontrolowane CV) w odpowiednich reżimach, natomiast korzystając z algorytmów optymalizacyjnych wylicza optymalne wartości zadane (SP) dla regulatorów PID już istniejących w DCS (tzw. zmienne manipulowane MV).
Dodatkowo, projektując regulator definiuje się zmienne zakłócające (DV) na które regulator APC nie ma wpływu (np. temperatura otoczenia, kaloryczność gazu/oleju opałowego, rodzaj i ilość wsadu), ale algorytm APC może uwzględnić ich wartości w rozwiązaniu zagadnienia optymalnego sterowania. Algorytm działania modułu Profit Controller przedstawia rysunek 3. Podstawowe dane o pracy APC są zwykle dostępne na konsoli operatorskiej.
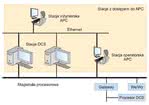
Rys.4 Hardware APC w strukturze DCS
Dane szczegółowe oraz możliwości strojenia APC dostępne są na oddzielnym komputerze lub oddzielnej konsoli z ograniczonym dostępem operatorskim. Taka stacja inżynierska APC może służyć obsłudze technicznej oraz technologom w celu wprowadzania nowych modeli procesu, współczynników optymalizacyjnych itp.
Typowa struktura rozwiązania przedstawiona jest na rysunku 4. Aplikacja APC pracująca na oddzielnej maszynie pozwala na stosunkowo szybkie realizowanie algorytmu. Co więcej, pozwala na bezpieczne prace serwisowe, podczas których po odłączeniu komputera APC operator może bezpiecznie prowadzić proces "klasycznie", wprowadzając ręcznie wartości SP do regulatorów PID w DCS.
Cechy APC
Analizator wirtualny (Inferential) – zestaw kalkulacji za pomocą których dokonuje się symulacji i predykcji wyników laboratoryjnych APC (Advanced Process Control) – system sterowania zaawansowanego pozwalający na jednoczesną kontrolę i optymalizację wielu parametrów pracy instalacji technologicznych zakładu APS (Advanced Planning and Scheduling) – system wykorzystywany do rozdziału mocy przerobowych instalacji CCR (Continuous Catalyst Regeneration) – reforming katalityczny benzyn, w wyniku którego uzyskuje się wzrost liczby oktanowej poprzez reakcje cyklizacji, aromatyzacji i izomeryzacji składników surowca CDU/VDU – podstawowy układ instalacji służący do przerobu ropy naftowej; składa się on z instalacji destylacji atmosferycznej CDU (Crude Distillation Unit) i instalacji destylacji próżniowej VDU (Vacuum Distillation Unit) DCS (Distributed Control System) – rozproszony systemem sterowania Destylacja atmosferyczna – proces fizykochemiczny wykorzystujący do rozdzielania mieszanin różnice w temperaturach wrzenia poszczególnych składników – w przypadku ropy naftowej: frakcji gazów, benzyn, nafty i olejów napędowych Destylacja próżniowa – proces analogiczny do destylacji atmosferycznej, prowadzony jednak przy zmniejszonym ciśnieniu; umożliwia separację destylatów próżniowych z pozostałości atmosferycznej Ekstrakcja furfurolem – technologia stosowana w celu podwyższania jakości bazowych olejów mineralnych poprzez redukcję węglowodorów aromatycznych, co prowadzi do zwiększenia indeksu lepkości Hydrokraking – proces technologiczny, które celem jest przetwarzanie ropy naftowej na różne frakcje; przeprowadza się go pod wysokim ciśnieniem poprzez reakcję destylatów próżniowych z wodorem na katalizatorze Izomeryzacja benzyn – proces rafineryjny, który prowadzi do podwyższenia liczby oktanowej frakcji benzynowej poprzez przekształcenie węglowodorów n-parafinowych do izoparafinowych LIMS (Laboratory Information Management System) – system zarządzania danymi laboratoryjnymi Step testy – testy polegające na serii zaplanowanych wymuszeń w systemie TBP (True Boiling Points) – punkty cięcia frakcji węglowodorowych |
Obecnie dostępne na rynku rozwiązania APC stosowane w przemyśle rafineryjno-petrochemicznym i, szerzej, w przemyśle chemicznym, bazują na nowoczesnych technologiach cyfrowych, a ich podstawowymi składowymi funkcjonalnymi są:
Rozwiązania z rodziny produktów Profit Suite firmy Honeywell spełniają wszystkie powyższe funkcje. Grupa Lotos S.A. zastosowała je na kilku swoich instalacjach w Rafinerii Gdańskiej jako narzędzia wspomagające do optymalizacji procesów.
CZĘŚĆ II : APC w rafinerii firmy Lotos
Grupa Lotos S.A. w Gdańsku to drugie co do wielkości przedsiębiorstwo rafineryjne w Polsce produkujące szeroki asortyment produktów pochodzących z przerobu ropy naftowej. Główny zakład produkcyjny to rafineria w Gdańsku, która sprzedaje i rozprowadza swoje produkty na w Polsce, jak również eksportuje je do międzynarodowych klientów na rynkach globalnych. W 2006 roku sprzedaż Grupy Lotos wyniosła 6,8 miliona ton produktów naftowych, przy nominalnej zdolności przerobu 6 milionów ton ropy naftowej rocznie.
Produkcja w GL S.A. bazuje głównie na przerobie ropy typu „Ural”. Rafineria w Gdańsku przerabia również ropę „Rozewie” wydobywaną przez firmę Petrobaltic (Grupa Kapitałowa GL S.A.) na szelfie bałtyckim. Każdy gatunek ropy naftowej charakteryzuje się innymi właściwościami fizyko-chemicznymi (tzw. assays), co implikuje potrzebę elastycznego prowadzenia procesów technologicznych.
Zdolność przerobowa instalacji destylacji atmosferycznej i próżniowej limituje rozmiar produkcji na pozostałych instalacjach rafineryjnych. Na przykład ilość destylatów ciężkich determinuje pracę bloku olejowego rafinerii. Z kolei wielkość przerobu na instalacji reformingu benzyn, która jest producentem wodoru, może limitować wielkość przerobu instalacji hydrokrakingu, a ilość izomeryzatu ma wpływ na planowanie szarż blendingu paliw, itd.
W GL S.A. zostały określone tzw. wąskie gardła instalacji produkcyjnych, mające wpływ na rozmiar produkcji i poziom uzyskiwanej marży rafineryjnej. Firma Honeywell zaproponowała Grupie Lotos rozwiązania zaawansowanego sterowania i optymalizacji z rodziny Profit Suite mające na celu odpowiednie sprofilowanie produkcji, tak aby zwiększyć rentowność spółki przy jednoczesnym ustabilizowaniu procesów technologicznych. Rozpoczęte w końcu lat 90. zeszłego wieku prace zakończyły się wdrożeniem rozwiązań Honeywell we wszystkich kluczowych instalacjach rafinerii.
Pomogło to zmaksymalizować zyski poprzez usprawnienia wynikające ze zwiększenia możliwości przerobowych, ze stabilniejszej pracy poszczególnych instalacji, zwiększenia wolumenu produktów bardziej opłacalnych, przy jednoczesnej redukcji kosztów związanych z zużyciem mediów oraz minimalizacją ilości produktów mniej opłacalnych.
Kolejność iorafinerii Grupy Lotos w Gdańsku nie była przypadkowa. Wdrożenia rozpoczęto od instalacji podstawowych, czyli destylacji atmosferycznej oraz próżniowej. Następnie projekt zaawansowanego sterowania zaimplementowano na instalacjach: hydrokrakingu, reformingu, izomeryzacji oraz ekstrakcji furfurolem.
APC w instalacjach destylacji atmosferycznej i próżniowej (CDU/VDU)
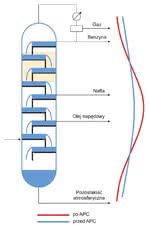
Rys.5 Przykład optymalizacji pracy kolumny destylacyjnej
Grupa Lotos zaangażowała firmę Honeywell do wdrożenia rozwiązania APC w instalacji destylacji atmosferycznej oraz próżniowej w 2000 roku. Instalacje destylacji atmosferycznej oraz próżniowej są szeroko opisane w literaturze fachowej.
Oczyszczona ropa naftowa przepływa przez piec technologiczny gdzie po podgrzaniu trafia do części ewaporacyjnej kolumny atmosferycznej, tutaj podlega odparowaniu i następuje jej rozdział na frakcje, które opuszczają kolumnę atmosferyczną jako strumienie szczytowe lub boczne w zależności od ich temperatury wrzenia.
Z dolnej części kolumny atmosferycznej odprowadzana jest pozostałość atmosferyczna, która poddawana jest procesowi destylacji w kolumnie próżniowej, w celu dalszego rozdziału na tzw. destylaty próżniowe.
Na potrzeby niniejszego artykułu warto jedynie wspomnieć, że sam proces destylacji ropy naftowej mimo szerokich zastosowań i dobrze znanej fizykochemii jest procesem złożonym o dużej ilości interakcji pomiędzy zmiennymi na poszczególnych sekcjach, poczynając od przygotowania i oczyszczenia surowca, sekcji wymiany ciepła, kolumny destylacji wstępnej, pieca podgrzewającego wsad do kolumny atmosferycznej, kolumny atmosferycznej, kolumn stripingowych, pieca podgrzewającego wsad do kolumny próżniowej, kolumny próżniowej i jej kolumn stripingowych.
Głównym celem dla projektowanego regulatora była maksymalizacja wielkości przerobu z 495 ton/h do maksymalnej w zakresie dopuszczalnym technologicznie oraz limicie wynikającym z wydajności pieca technologicznego. Ze względu na planowany wymianę pieca na instalacji destylacji atmosferycznej wdrożenie rozwiązania podzielono na dwie fazy, w pierwszej fazie zaimplementowano Profit Controller na kolumnie wstępnej, splitterze rozdziału benzyn oraz na kolumnie próżniowej, prace nad częścią atmosferyczna instalacji przewidziano na drugą fazę projektu.
Aby móc zwiększyć zdolność przerobową instalacji następnym celem implementacji APC było optymalne sterowanie „starym” piecem przed jego planowaną wymianą na nowy w 2002 roku. W pierwszej fazie projektu Honeywell wdrażając rozwiązania pass-balancing na strumieniach pieca, algorytmy optymalnego sterowania gazem/olejem opałowym, utrzymaniem odpowiedniej wartości % O2 w spalinach usprawnił działanie i dał możliwość ciągłej i bezpiecznej pracy na parametrach bliskich technologicznym ograniczeniom pieca.
Następnym celem aplikacji była optymalizacja pracy splittera rozdziału benzyn. Górny produkt kolumny to benzyna lekka, będąca wsadem do instalacji izomeryzacji, natomiast produkt odprowadzany z dolnej części kolumny to benzyna ciężka, która stanowi wsad do instalacji reformingu benzyn. Ważnym elementem kontroli splittera rozdziału benzyn było utrzymanie odpowiedniego poziomu benzenu i jego prekursorów we wsadzie kierowanym do instalacji reformingu benzyn. Zadanie te Profit Controller wykonywał za pomocą kontroli ciśnienia i temperatur góry i dołu splittera. Druga faza projektu rozpoczęła się po wymianie pieca technologicznego podgrzewającego wsad dla kolumny atmosferycznej.
Dzięki zmianom technologicznym wykonanym podczas postoju instalacja destylacji atmosferycznej mogła przerabiać dużo więcej surowca aniżeli instalacja destylacji próżniowej, stąd głównym zadaniem dla APC było zwiększenie uzysku frakcji średnich oraz zminimalizowanie ilości pozostałości atmosferycznej podawanej dalej do instalacji destylacji próżniowej.
Zainstalowano dwa wielowymiarowe kontrolery APC na instalacji destylacji atmosferycznej, jeden dla optymalnego prowadzenia pieca atmosferycznego, drugi dla optymalizacji pracy kolumny atmosferycznej. Instalacja dwóch rozwiązań Profit Controller przełożyła się na większą elastyczność rozwiązania przy jednoczesnym uproszczeniu diagnostyki. Główne cele operacyjne stawiane dla aplikacji APC to:
- minimalizacja pozostałości atmosferycznej (poprzez kontrolę lepkości),
- optymalizacja frakcjonowania pomiędzy kluczowymi komponentami w kolumnie,
- minimalizacja zakłóceń przy zmianach wsadu,
- minimalizacja strat na jakości produktu (produkcja „zbyt dobrych” frakcji),
- prowadzenie kolumny atmosferycznej w bezpiecznym zakresie parametrów technologicznych.
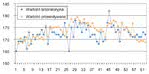
Rys.6 90% TBP dla benzyny w kolumnie wstępnej Preflash
Aplikacja ta miała głównie na celu maksymalizację odzysku produktów w kolumnie atmosferycznej oraz minimalizację ilości pozostałości atmosferycznej. Aby to uzyskać Profit Controller musiał prowadzić proces w taki sposób, aby odzyskiwać maksymalną ilość cennych frakcji dla różnych kombinacji wsadu. Odpowiednia jakość produktów była także sprawą priorytetową dla aplikacji APC.
Innym problemem, który należało rozwiązać było częste osuszanie się sekcji odbioru ciężkiego oleju opałowego – tzw. CON, co powodowało ciemnienie tej frakcji i nie spełnianie przez nią wymogów jakościowych. Powyższe trudności wynikające głównie z braku dostępności w czasie rzeczywistym parametrów jakościowych produktów rozwiązała część aplikacji Profit Controllera służąca do tworzenia i obsługi inferentiali, a mianowicie Profit Sensor Pro oraz Lab Update.
Analizatory wirtualne – inferentials

Rys.7 90% TBP dla benzyny w głównej kolumnie destylacyjnej
Nazwa inferentials określa obliczenia za pomocą, których dokonuje się symulacji i predykcji wyników laboratoryjnych. Wyliczenia inferentiali bazują na aktualnych, pobieranych z DCS parametrach procesu i w sposób ciągły informują operatora o przewidywanej wartości zmiennej symulowanej. W przypadku braku analizatorów na instalacji jest to bardzo wygodny sposób, aby utrzymać wysoką jakość parametrów jakościowych produktów, które są badane laboratoryjnie jedynie raz lub dwa razy na dobę.
Aby wirtualny analizator działał poprawnie operator lub laborantka wprowadza wyniki laboratoryjne do specjalnego programu statystycznego, który aktualizuje przesunięcie funkcji obliczeń danego inferentiala tzw. bias. W rozwiązaniu firmy Honeywell za obsługę i tworzenie inferentiali odpowiada dodatkowe narzędzie APC o nazwie Profit Sensor Pro lub Lab Update służący do uaktualniania wirtualnego analizatora.
W Grupie Lotos firma Honeywell wykorzystała dane pochodzące z LIMS (Laboratory Information Management System) w celu uaktualnienia parametrów wprowadzanych do aplikacji Lab Update i predykcji przy użyciu Profit Sensor Pro. Dzięki wykorzystaniu LIMS bias modelu inferentiala po wstępnej walidacji może być wprowadzany automatycznie, oczywiście w każdej chwili bias może być wprowadzany ręcznie przez operatora. Głównym zadaniem inferentiali dla produktów instalacji CDU/VDU było dostarczenie informacji on-line do aplikacji Profit Controllera w celu lepszej kontroli procesu i natychmiastowej reakcji w przypadku zmiany trendu lub jakichkolwiek zakłóceń technologicznych.
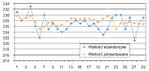
Rys.8 90% TBP dla MGO po głównej kolumnie destylacyjnej
W tym celu zamodelowano krzywe punktów cięcia frakcji (TBP True Boiling Point), które Profit Sensor Pro aktualizował co minutę. W przypadku zmiany warunków pracy kolumny, czy przykładowo przy zmianie wsadu natychmiast znajdowało to odzwierciedlenie w wartościach TBP.
Rozwiązanie z wykorzystaniem inferentiali pozwala szybko oszacować wzrost lub spadek produkcji poszczególnych frakcji naftowych wraz ze zmianą wsadu do kolumny lub zmianą jej parametrów jakościowych bez potrzeby długiego oczekiwania na analizy laboratoryjne.
Przykładowo z ekonomicznego punktu widzenia dla benzyny 90% TBP jest ważny ponieważ determinuje uzysk tej frakcji. Model TBP dla benzyny został opracowany z wykorzystaniem narzędzi firmy Honeywell Profit Design Studio bazując na dostępnych pomiarach, które wpływają na górne ciśnienie w kolumnie frakcjonującej. Rysunek poniżej przedstawia porównanie wartości laboratoryjnej 90% TBP benzyny w kolumnie wstępnej z wartością przewidywaną przez Profit Sensor Pro.
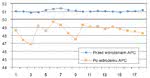
Rys.9 Pozostałość atmosferyczna przed i po implementacji APC
Punkty cięcia dla innych frakcji otrzymywanych z kolumny destylacji atmosferycznej m.in.: LGO90% oraz MGO90% także zostały zamodelowane z użyciem narzędzia Profit Design Studio i Profit Sensor Pro. Inferentiale pozwoliły zwiększyć uzysk frakcji olejów napędowych poprzez maksymalizację ich wartości w regulatorze Profit Controller.
Dzięki implementacji pakietu optymalizacyjnego APC firmy Honeywell (Profit Controller, Profit Sensor Pro oraz Lab Update) rafineria Grupy Lotos była w stanie znacząco poprawić i ustabilizować przebieg procesu, zwiększyć przepustowości kolumny destylacyjnej, poprawić kontrolę jakości produktów. Profit Controller był w stanie zredukować ilość pozostałości atmosferycznej o 1,3%, dzięki czemu uzyskano przyrost marży rafineryjnej o około 0,27 dol./bbl ropy naftowej. Powyższe wyliczenie nie zawiera zysków płynących ze zwiększenia przerobowości całej instalacji destylacji atmosferycznej.
CZĘŚĆ III : Instalacja hydrokrakingu
Instalacja hydrokrakingu ( HCU) w rafinerii w Gdańsku została wybudowana na licencji firmy Chevron. Jest to hydrokraking dwustopniowy z wysoką (99%) konwersją. Zadaniem instalacji jest przekształcenie frakcji próżniowych i ekstraktów furfurolowych na lżejsze i bardziej wartościowe produkty. Reakcje hydrokrakingu zachodzą na katalizatorach w dwóch reaktorach przy wysokiej temperaturze (360...440°C) i wysokim ciśnieniu (15...16 MPa).
Surowcem instalacji, oprócz węglowodorów ciekłych, jest też wodór. Podstawowe produkty instalacji to olej napędowy i nafta (łącznie około 80%) używane do komponowania olejów napędowych i paliwa lotniczego. Poza tym instalacja produkuje komponenty benzynowe oraz gazy opałowe, które są poddawane dalszej przeróbce na innych instalacjach rafineryjnych.
Pożądany stopień konwersji w instalacji hydrokrakingu uzyskuje się poprzez utrzymywanie odpowiednio wysokiego ciśnienia parcjalnego wodoru, pożądanych stosunków przepływu wodór/węglowodory oraz odpowiednich temperatur na poszczególnych złożach katalizatora w obu reaktorach. Mieszaniny poreakcyjne z obydwu reaktorów są separowane we wspólnej sekcji separacji, nadmiarowy wodór jest zawracany do procesu, a węglowodory ciekłe są kierowane do sekcji frakcjonowania i rozdziału lekkich destylatów, gdzie następuje rozdział na poszczególne produkty instalacji.
Cele wdrożenia
Hydrokraking jest instalacją bardzo dużą i skomplikowaną. Liczba urządzeń i aparatury kontrolno-pomiarowej jest znacznie większa niż na innych instalacjach rafineryjnych, co oczywiście ma określony wpływ na konstrukcję wdrażanego rozwiązania APC. Po wstępnej analizie danych procesowych określono cele, które powinno ono osiągnąć, oraz zidentyfikowano aktualne i potencjalne ograniczenia technologiczne instalacji.
W wyniku tej analizy zdecydowano się zaimplementować siedem regulatorów Profit Controller. Trzy z nich są w zasadzie niezależne i optymalizują pracę kolumn destylacyjnych: 150-C2 (striper produktowy), 150-C9 (kolumna stabilizacyjna) benzyn i 150-C10 (kolumna rozdziału benzyn). Cztery pozostałe: PR (wsad + wodór), R1 (reaktor 150-R1), R2 (reaktor 150-R2) i MF (kolumna frakcjonująca 150-C3) optymalizują pracę fragmentów instalacji, ale mogą też wzajemnie ze sobą współpracować i wymieniać dane, gdy jest włączony nadrzędny regulator OPT – Profit Optimizer.
Podstawowe zadania, za jakie odpowiada w instalacji hydrokrakingu Profit Optimizer, są następujące:
- maksymalizacja przepływu wsadu instalacji,
- optymalizacja konwersji (prowadzenie procesu przy minimalnych temperaturach w reaktorach wystarczających do uzyskania założonej jakości produktów),
- minimalizacja zużycia energii.
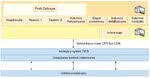
Rys.10 Struktura rozwiązania APC dla instalacji hydrokrakingu w rafinerii Grupy Lotos w Gdańsku
Z kolei cele cząstkowe dla siedmiu regulatorów Profit Controller to:
- regulacja temperatury katalizatora na poszczególnych złożach w obu reaktorach,
- utrzymanie założonego profilu temperatur w reaktorach,
- regulacja obciążenia pieców,
- utrzymanie bilansu cieplnego pomiędzy reaktorami,
- utrzymanie odpowiedniego stosunku wodór/węglowodory w reaktorach,
- maksymalizacja uzysku produktów o wyższej wartości,
- minimalizacja strumienia „overflash” w kolumnie frakcjonującej 150-C3,
- minimalizacja ciśnienia w kolumnie frakcjonującej 150-C3,
- maksymalizacja odzysku ciepła z kolumny frakcjonującej 150-C3 przez orosienie cyrkulacyjne,
- utrzymywanie poziomu w dole kolumny frakcjonującej 150-C3 w założonych granicach,
- utrzymywanie w założonym zakresie temperatury szczytu stripera produktowego 150-C2,
- kontrola zawartości C5 w LPG,
- utrzymywanie w założonym zakresie zawartości C7+ w benzynie lekkiej.
Wykorzystanie wirtualnych analizatorów
Podczas wdrażania APC na instalacji hydrokrakingu dwa zagadnienia okazały się niezmiernie istotne dla poprawnej implementacji sterowania zaawansowanego. Pierwszym było odpowiednie zamodelowanie wirtualnych analizatorów (inferential). Zaprojektowano sześć takich analizatorów „mierzących” kluczowe parametry trzech produktów instalacji. Używając narzędzia Profit Design Studio stworzono inferentiale określające:
Istotnym elementem umożliwiającym dobrą pracę tych wirtualnych analizatorów jest aplikacja Lab Update, która umożliwia wprowadzanie aktualnych oznaczeń laboratoryjnych, a tym samym dostosowanie wskazań inferentiali do rzeczywistych wartości. Drugim ważnym aspektem prac podczas wdrażania APC na instalacji hydrokrakingu była praca nad projektem przy różnych stanach obiektu.
Do budowy modelu instalacji wymagane są step testy (wymuszenia na kluczowych parametrach procesu). Na podstawie analizy trendu odpowiedzi parametrów kontrolowanych przez Profit Controller i ich relacji do wymuszeń (step testów) otrzymuje się modele instalacji (transmitancje widmowe). Wstępnie firma Honeywell planowała zakończyć projekt przed postojem instalacji, jednakże z uwagi na konieczność wcześniejszej wymiany katalizatora w jednym z reaktorów, projekt wdrażania APC przerwano zaraz po przeprowadzonych step testach.
Jego realizację wznowiono po uruchomieniu instalacji z nowym katalizatorem w reaktorze 150-R2. Zdecydowano pozostawić modele zidentyfikowane przed postojem instalacji, a wdrażana technologia okazała się być na tyle elastyczna, że bez problemów można było optymalizować proces. Pozwoliło to specjalistom z Honeywell wspólnie z pracownikami GLSA bez większych problemów doprowadzić do końca projekt wdrożenia rozwiązania sterowania zaawansowanego.
Wyniki wdrożenia
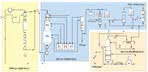
Rys.11 Ogólny schemat instalacji CCR z podziałem na sekcje optymalizacyjne APC
Po zakończeniu implementacji APC w bardzo krótkim czasie zaobserwowano korzyści płynące z pracy Profit Controllera. Proces przebiegał stabilniej, a odchylenie standardowe dla głównych parametrów jakościowych zmniejszyło się w sposób znaczący. Poniżej przedstawiono niektóre z otrzymanych wyników:
Grupa Lotos szacuje, że zyski płynące zastosowania na instalacji hydrokrakingu APC firmy Honeywell wynoszą około 2,3 mln dolarów na rok pracy instalacji.
CZĘŚĆ IV: Instalacje reformingu i izomeryzacji
Implementację APC na instalacji reformingu katalitycznego benzyn CCR (Continuous Catalyst Regeneration) wykonano w Rafinerii Gdańskiej w 2007 roku. Jednym z celów tej aplikacji było skoordynowanie pracy tego obiektu z instalacją hydrokrakingu, gdzie wodór z instalacji CCR może determinować możliwości produkcyjne instalacji HCU.
Reforming katalityczny
Proces technologiczny reformingu poddany optymalizacji bazował na rozwiązaniu UOP. Benzynę średnią poddaje się procesowi reformowania na katalizatorze platynowym, podczas którego uzyskuje się wzrost liczby oktanowej LO w wyniku reakcji cyklizacji, aromatyzacji i izomeryzacji składników surowca.
Proces konwersji niskooktanowych naftenów oraz parafin do wysokooktanowych aromatów odbywa się w wielostopniowych reaktorach w obecności katalizatora. Bardzo ważne jest zachowanie odpowiedniego profilu temperatury na reaktorach, co oprócz składu wsadu i ciśnienia wpływa znacząco na otrzymaną jakość produktu, czyli liczbę oktanowa reformatu. Produktem ubocznym tego procesu jest gaz wodorowy, zawierający oprócz wodoru o czystości ok. 92,5% objętości domieszki głównie lekkich węglowodorów (metan, etan, propan).
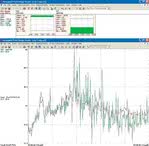
Rys.12 Przykład projektowania inferentiala dla prężności reformatu RVP
Gaz wodorowy bezpośrednio z reformowania przechodzi do procesu rekontaktingu, gdzie przy podwyższonym ciśnieniu jest wzbogacany (oczyszczany z lekkich węglowodorów). Po tym procesie oddziela się go w wysokociśnieniowym separatorze i kieruje do procesu izomeryzacji benzyny lekkiej, hydrorafinacji benzyny i olejów smarowych do hydroodsiarczania olejów napędowych. Nadmiar wraz z innymi strumieniami gazów wodorowych kieruje się do jeszcze głębszego oczyszczania na instalacji PSA, gdzie wzbogacony do 98-99% objętości jest przesyłany do instalacji HCU.
Dużą zaletą rozwiązania technologicznego UOP jest możliwość ciągłej regeneracji katalizatora, który podczas normalnej pracy instalacji podlega zakoksowaniu. W celu przedłużenia aktywności katalizatora w sekcji regeneracyjnej instalacji CCR, wypala się koks zachowując odpowiedni profil wypalania oraz odpowiednią ilość tlenu.
Tak uzdatniony katalizator zawracany jest z powrotem do reaktorów. Aby uprościć prowadzenie projektu dla tak kompleksowej instalacji, jaką jest reforming, zdecydowano o podziale instalacji na poszczególne sekcje. Za ich optymalizację pracy odpowiadają oddzielne regulatory Profit Controller, tak jak to miało miejsce w przypadku instalacji HCU (w tym przypadku nie zastosowano regulatora „spinającego” Profit Optimizer). Podział na sekcje przedstawiono na rys. 11. Pierwszy kontroler zaawansowanego sterowania odpowiada za optymalizację pracy sekcji reaktorowej, drugi za sekcję stabilizacyjną, a trzeci za regenerację katalizatora.
Cele wdrożenia
Główne cele stawiane przed regulacją APC dla poszczególnych sekcji instalacji zdefiniowano jak poniżej:
Reaktory:
- maksymalizacja wsadu,
- kontrola liczby RON,
- minimalizacja ciśnienia w reaktorach (większy uzysk),
- optymalna kontrola profilu temperatury wejściowej do reaktorów,
- maksymalizacja produkcji wodoru.
Sekcja stabilizacyjna:
- kontrola ilości frakcji C5 w LPG według zadanych norm,
- kontrola prężności par reformatu,
- maksymalizacja produkcji reformatu,
- optymalizacja zużycia mediów.
Sekcja regeneracji:
- optymalna kontrola ilości tlenu w komorze wypalania koksu,
- kontrola profilu temperatury wypalania. Całkowita
Całkowita liczba zmiennych dla wszystkich trzech kontrolerów CV wyniosła 59, zmiennych MV – 20, a zmiennych zakłócających – 12.
Cztery analizatory wirtualne
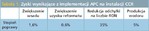
Tabela.1 Zyski wynikające z implementacji APC w instalacji CCR
Podczas tworzenia aplikacji wystąpiła, podobnie jak w przypadku wdrożenia w instalacji hydrokrakingu, konieczność stworzenia analizatorów wirtualnych, czyli inferentiali. Dla instalacji reformingu zaprojektowano 4 takie funkcje:
- wagowy rozkład temperatur na reaktorach dla zadanej liczny RON,
- wartość koksu odłożonego na katalizatorze przed regeneracją,
- ilość frakcji C5 w LPG,
- prężność reformatu RVP.
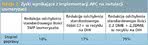
Tabela.2 Zyski wynikające z implementacji APC w instalacji izomeryzacji
Na rysunku 12 przedstawiono przykład projektowania inferentiala dla prężności reformatu bazującego na wartościach temperatury i ciśnienia w kolumnie debutanizera instalacji CCR. W górnej części rysunku pokazano zmienne składowe tworzące sztuczny pomiar RVP oraz ich korelacje ze zmienną symulowaną, natomiast w dolnej części rysunku program statystyczny Honeywell porównuje wynik RVP przewidywany z rzeczywistym.
Regulator zawansowanego sterowania APC z macierzą modelu wielkości 59 × 32 i czterema inferentialami był w stanie zoptymalizować proces w taki sposób, aby spełnić wszystkie wymogi stawiane przez rafinerię. Niektóre z rezultatów aplikacji są przedstawione w tabeli 1. W tym miejscu warto zwrócić uwagę, że produkcja wodoru wzrosła o 5% (dwukrotnie więcej od zakładanej).
Szacując zyski okazało się, że profity z zastosowania rozwiązań APC sięgnęły 750 tysięcy dolarów za rok pracy instalacji. Dla reformingu czas trwania aplikacji APC (step testy, instalacja oprogramowani, odpowiednia konfiguracja DCS, strojenie kontrolera) to okres około 6 miesięcy. Zyski uzyskane dzięki zastosowaniu zaawansowanego sterowania zostały osiągnięte w czasie krótszym niż rok.
Instalacja izomeryzacji benzyn
Równolegle do prac nad projektem APC dla instalacji reformingu wdrażane było rozwiązanie Profit Controller w instalacji izomeryzacji benzyn. Izomeryzacja to proces przekształcania węglowodorów n-parafinowych do izoparafinowych. Reakcja prowadzona jest w taki sposób, aby zwiększyć liczbę oktanową surowca, czyli de facto powiększyć liczbę rozgałęzionych izomerów. Głównymi celami dla rozwiązania APC w tym wypadku okazały się być:
- maksymalizacja przerobu świeżego wsadu,
- zwiększenie uzysku izomeryzatu,
- minimalizacja wysokooktanowych (2,2 DMB, 2,3DMB) oraz ciężkich komponentów (C7+) we frakcji zawracanej ponownie do procesu,
- kontrola frakcji 3MP w lekkim izomeryzacje,
- optymalizacja praca kolumny deizoheksanizera (DIH).
Zdecydowano się zaprojektować pojedynczy regulator Profit Controller obejmujący swoim działaniem części instalacji odpowiedzialne za przygotowanie wsadu, reaktory, kolumnę stabilizującą i kolumnę deizoheksanizera (DIH). Dodatkowo, w celu usprawnienia procesu sterowania instalacją zaprojektowano trzy wirtualne analizatory działające online ze skanem 1-minutowym, a mianowicie:
- inferential mierzący zawartość 2,2DMB oraz 2,3DMB w recyrkulacji kolumny DIH,
- inferential mierzący zawartość C7+ w recyrkulacji kolumny DIH,
- inferential określający zawartość 3MP w lekkim izomeryzcie z kolumny DIH.
Wielowymiarowy regulator APC dla instalacji izomeryzacji wylicza wartości optymalnych SP dla trzynastu regulatorów PID (13 MV), tak aby sterować 18 zmiennymi procesowymi (18CV) przy założeniu 10 zmiennych zakłócających. Profit Controller pracując bez przerw praktycznie od momentu oddania do użytku spowodował znaczną poprawę jakości produktu oraz przyczynił się do większej stabilizacji procesu.
W tabeli 2 przedstawiono niektóre ze wskaźników ilustrujących poprawę pracy instalacji. Dodatkowo, dzięki możliwości minimalizacji o ponad 10% ilości przepływu recyklu do wsadu, możliwe było znaczące zwiększenie obciążenia instalacji wsadem świeżym, co z kolei przełożyło się na zwiększenie rentowności obiektu o 860 tys. dolarów za rok pracy instalacji.
CZĘŚĆ V: Instalacja ekstrakcji furfurolem
Frakcje z destylacji próżniowej oraz deasfaltyzat DAO z instalacji odasfaltowania propanem zawierają węglowodory parafinowe, naftenowe i aromatyczne. Spośród nich aromaty mają bardzo negatywny wpływ na jakość olejów bazowych, pogarszając stabilność termo oksydacyjną (odporność na starzenie). Mają też niski wskaźnik lepkości (charakteryzują się bardzo dużą zmianą lepkości wraz ze zmianą temperatury). Dlatego też usuwa się je w procesie ekstrakcji furfurolem. W odróżnieniu od parafin i naftenów, aromaty bardzo dobrze rozpuszczają się w rozpuszczalnikach typu furfurolu.
Proces ten prowadzi się w ekstraktorze dyskowym. Dla każdego rodzaju surowca utrzymywana jest ściśle określona temperatura zarówno dołu, jak i góry kolumny ekstraktora oraz odpowiedni stosunek ilościowy rozpuszczalnika do wsadu. Górą odpływa roztwór furfurolu w rafinacie, zaś dołem roztwór ekstraktu o wysokiej zawartości aromatów w furfurolu. Każdy ze strumieni jest kierowany do sekcji odzysku rozpuszczalnika. Produkty uboczne, jakimi są ekstrakty, stanowią surowce do produkcji gumy (plastyfikatory), sadz technicznych, asfaltów i olejów napędowych.
Wykonanie wdrożenia
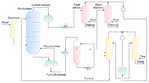
Rys.13 Schemat instalacji selektywnej ekstrakcji furfurolem
Implementacja APC dla instalacji ekstrakcji furfurolem została wykonana w Grupie Lotos w roku 2007 i również bazowała na rozwiązaniach firmy Honeywell. Aby zoptymalizować prowadzenie procesu ekstrakcji dla tej instalacji, projekt APC zakładał zdefiniowanie 42 zmiennych kontrolowanych, 15 zmiennych manipulowanych i 5 zmiennych zakłócających. Główne cele postawione przed technologią zaawansowanego sterowania były następujące:
- utrzymanie WL produktu w bardzo wąskich limitach jakościowych, maksymalizacja uzysku rafinatu.
Zdefiniowano też cele poboczne, które bazując na wielowymiarowości kontrolera były również możliwe do uzyskania:
- utrzymanie optymalnej temperatury wsadu do kolumny ekstraktora, maksymalnej różnicy temperatury na ekstraktorze (wydajność), utrzymanie odpowiedniego stosunku wsadu/rozpuszczalnika i optymalnego rozdziału strumieni na piecu (pass-balancing), a także utrzymanie odpowiedniej temperatury wyjściowej pieca,
- minimalizacja ilości pary dostarczanej do instalacji oraz ilości zużywanego oleju opałowego.
Podczas projektowania regulatora APC okazało się, że głównym problemem optymalizacyjnym jest praca instalacji na 7 różnych wsadach, tj. od bardzo lekkich SN-140 poprzez SAE-10/95, SAE-10/85, SAE- 30/95, SAE-30/80 do ciężkich (BS- 30/95 i BS-30/90). Charakterystyki pracy instalacji dla różnych wsadów były bardzo nieliniowe.

Tabela 3. Zyski wynikające z implementacji APC na instalacji ekstrakcji furfurolem
Reżimy pracy instalacji były na tyle różne, że rozpatrywano możliwość budowy zestawu 7 macierzy modeli dla instalacji, które miały być przełączane w APC przez operatora dla odpowiedniego rodzaju wsadu. Na potrzeby identyfikacji modelu (step testów) zdecydowano się na pracę ze wsadem o średniej lepkości, tj. SAE-30/95 i z tym też modelem uruchomiono po raz pierwszy regulator na pracującej instalacji.
Po wstępnym zestrojeniu aplikacji i dobraniu współczynników optymalizacyjnych okazało się, że rozwiązanie APC jest na tyle elastyczne, że regulator jest w stanie pracować na tym samym modelu procesu dla wszystkich siedmiu wsadów. Co więcej, zyski były dużo większe od oczekiwanych (tabela 3).
Elastyczność rozwiązania
W tym miejscu warto ponownie wspomnieć o algorytmach wbudowanych w rozwiązanie sterowania APC, które pozwalają na tak elastyczną pracę kontrolera. Są to miedzy innymi:
- wbudowany algorytm RCA pozwalający stroić regulator (zmniejszać przeregulowanie, czas regulacji, itp. – analogicznie do zmiennych Kp ,Ki ,Kd w przypadku regulatorów PID),
- skalowalność on-line poprzez metodę dekompozycji wielowymiarowej SVD
Technologia SVD powoduje, że regulator APC potrafi spośród wielu wektorów zmiennych w przestrzeni stanu rozdzielić je na poszczególne składowe oraz pogrupować ze względu na czas odpowiedzi, wzmocnienie i inne, co znacznie ułatwia sterowanie. Pozwala to na osiągnięcie nie tylko pozytywnych rezultatów osiągnięte w uzysku i jakości rafinatu dla różnych wsadów, ale również umożliwia utrzymywanie poziomów surowców i produktów w zbiornikach buforowych nawet dla najcięższych frakcji, co przed aplikacją sprawiało duże trudności operatorom.
Generalnie standardowa odchyłka zmiennych kontrolowanych dzięki APC zmniejszyła się o 52%, co w wymierny sposób wpłynęło na otrzymane pozytywne rezultaty. Dzięki zwiększeniu wydajności procesu szacuje się, że zyski płynące jedynie z uzysku rafinatu osiągnęły sumę około 2 mln dolarów rocznie.
Zyski liczone były wg zasad statystycznych „same limit rule” oraz „same percentage rule”. Dane do oszacowania zysków bazowały na przebiegach historycznych kolekcjonowanych z okresu przed i po zainstalowaniu aplikacji zaawansowanego sterowania, cenach rynkowych produktów i mediów oraz marżach uzyskanych z systemu PIMS. Dodatkowo wdrożenie zaawansowanego sterowania rozwiązało kilka problemów technologicznych nie będących w zakresie zadań zakładanych w projekcie.
Autorzy artykułu:
- Część I: Grzegorz Oleszczuk (Honeywell)
- Część II: Mariusz Zienkiewicz, Krzysztof Wrzesień (Grupa Lotos S.A.)
- Część III: Dariusz Kruk, Edmund Monkiewicz (Grupa Lotos S.A.)
- Część IV: Roman Kuk (Grupa Lotos S.A.)
- Część V: Kazimierz Kowalczyk, Aleksander Sobolewski (Grupa Lotos S.A.)