Przez lata dziedzina ta ewoluowała, rozwijając się od wykorzystania prostych metod umożliwiających określanie poziomu w sposób przybliżony, do użycia przetworników pozwalających na pomiary z dużą dokładnością. Pojawiły się też przyrządy służące do określania poziomu substancji agresywnych chemicznie oraz mogące być stosowane w miejscach trudno dostępnych. W dwuczęściowym artykule przedstawiamy informacje związane z fizyką pomiarów poziomu, najpopularniejsze rozwiązania metrologiczne oraz przykłady ich wykorzystania.
Elektromechaniczny miernik poziomuEE200 to przykład poziomomierza z linką. Urządzenie zawiera również przetwornik mikroprocesorowy, obciążnik, rolkę pomiarową oraz czujnik położenia. Opuszczany na lince obciążnik wprawia rolkę w ruch, a na podstawie sygnału z czujnika położenia obroty rolki są zliczane. Pozwala to zmierzyć odległość, jaką w czasie pomiaru przebywa linka. Przyrząd automatycznie sygnalizuje przypadek, gdy w czasie pomiaru linka została zerwana lub zatopiony został obciążnik. Czujnik zabezpieczony jest przed zamarzaniem oraz sygnalizuje błędne działanie. EE200 ma trzy wyjścia: analogowe oraz impulsowe przekaźnikowe i tranzystorowe, a także interfejs RS-485. EE200 znajdziemy w ofercie gliwickiej firmy Zach Metalchem.
|
Wymagania względem dokładności pomiarów poziomu są zróżnicowane. Czasami wystarczy ocena przybliżona, innym razem konieczne jest dokładne określenie poziomu substancji w zbiorniku, gdyż na jego podstawie obliczana jest objętość lub masa składowanego materiału. Stąd też przyrządy do pomiarów poziomu dzieli się zasadniczo na dwie grupy: czujniki do pomiarów ciągłych, które zapewniają dokładną informację o ilości przechowywanego materiału, oraz takie, które sygnalizują jedynie przekroczenie określonego poziomu.
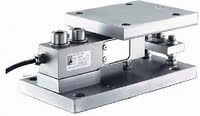
Fot. 1. Introl oferuje kilka modeli wag zbiornikowych, w tym GPA-NT
Na wybór metody pomiarowej wpływ mają także ograniczenia przestrzenne w zakresie montażu czujników oraz rodzaj substancji, której poziom ma być mierzony. To ostatnie powoduje, że w niektórych przypadkach można od razu wykluczyć przyrządy do pomiarów kontaktowych. Przykładowo gdy mierzony jest poziom cieczy lepkich lub żrących, zazwyczaj stosuje się takie metody, gdzie w trakcie pomiarów detektor nie wchodzi w bezpośredni kontakt z substancją.
W dwuczęściowym artykule charakteryzujemy wybrane metody pomiaru poziomu, w tym wykorzystujące czujniki pojemnościowe, ultradźwiękowe, radarowe, laserowe i izotopowe oraz sondy elektromechaniczne i wagi zbiornikowe, podając przykłady konkretnych czujników z oferty polskich i zagranicznych producentów. Przedstawiamy też przykłady procesów produkcyjnych w różnych dziedzinach przemysłu, w których czujniki poziomu są niezbędne.
POMIARY Z LINKĄ
Chociaż obecnie nie stosuje się tak prymitywnych i dostarczających jedynie podstawowych informacji metod jak uderzanie młotkiem w ścianę zbiornika albo rzucanie o nią kamieniami i określanie poziomu wypełnienia na podstawie odgłosu uderzenia, niektóre mechaniczne metody - np. pomiary z linką - jeszcze w latach 90. ubiegłego wieku w niektórych branżach traktowane były jako standardowe.
Sondy linkowe składają się z obciążonej linki, która jest odwijana z bębna przez silnik elektryczny aż do momentu, gdy ciężarek osiągnie powierzchnię materiału. Długość odwiniętej linki jest wyznaczana na podstawie liczby obrotów bębna, za zliczanie czego odpowiedzialny jest układ elektroniczny.
Case study: Pomiary poziomu w przemyśle farmaceutycznymZe względu na duże wymagania dotyczące dokładności, a przede wszystkim sterylności produkcji, większość procesów technologicznych w przemyśle farmaceutycznym jest zautomatyzowana. W branży tej wykorzystywane są też liczne czujniki, w tym mierniki poziomu, które stanowią nieodłączny element niektórych urządzeń używanych w produkcji leków. Na wybór czujnika w przemyśle farmaceutycznym wpływ ma wiele czynników. Oprócz dopasowania do specyfiki procesu i możliwości zintegrowania z instalacją, w której element ten będzie pracował, istotne jest, aby sam sensor nie był źródłem zanieczyszczeń. Ważne jest też, aby można go było wyczyścić w ramach procesów CIP (Cleaning In Place) i SIP (Sterilisation In Place), będących standardowymi dla tego typu linii produkcyjnych. Systemy wody WFI
Naturalnym wyborem czujników poziomu montowanych w tego typu instalacjach są mierniki bezkontaktowe - np. radarowe. Wybierając produkt, należy sprawdzić, czy antena w danym modelu jest odpowiednio zabezpieczona przed wpływem silnie zjonizowanej wody i możliwe jest jej czyszczenie w procesach CIP i SIP. Bioreaktory
Ponadto możliwość określenie aktualnego poziomu napełniania reaktora jest często ważnym wskaźnikiem poprawności przebiegu procesu, gdyż jest to zazwyczaj produkcja zamknięta, a zbiornik zostaje otwarty i opróżniony dopiero, gdy zajdą wszystkie planowane reakcje. Oprócz poziomu w bioreaktorach mierzy się też wiele innych wielkości - temperaturę, poziom pH, stopień natlenienia oraz ciśnienie. Mieszanie i składowanie
Parametry te bowiem w procesie mieszania składników leków nieustannie zmieniają się, podobnie jak i konsystencja produktu, w którym ponadto powstawać mogą pęcherzyki oraz, na skutek pracy mieszadeł, wiry. Czujniki poziomu w przemyśle farmaceutycznym są też wykorzystywane do monitoringu zbiorników z agresywnymi chemicznie substancjami - np. kwasami. Poza tym wiele substancji niezbędnych do produkcji leków jest przechowywanych w postaci proszków i granulatów. Zbiorniki są często napełniane pneumatycznie, co należy uwzględnić w związku z tym, że nie wszystkie typy czujników poziomu nadają się do pomiarów w takich warunkach. |
Wśród zalet tej metody wymienić można niski koszt oraz, w porównaniu do innych metod, duży zakres pomiarowy (do kilkudziesięciu metrów). Ponadto na wynik pomiaru nie mają wpływu takie czynniki jak zapylenie i wahania temperatury wewnątrz zbiornika oraz zmiany właściwości materiału. Przyrządy z linką są też proste w obsłudze.
Do ich wad zaliczane są z kolei koszty konserwacji (w przypadku środowisk silnie zapylonych pył oblepia linkę, co powoduje konieczność okresowego czyszczenia bębna), zużywanie się części mechanicznych oraz możliwość oberwania obciążnika lub zerwania linki. Stąd sondy tego typu nie mogą być używane np. w czasie napełniania silosu, gdyż grozi to ich uszkodzeniem pod ciężarem wsypywanego materiału.
PUNKTOWE POMIARY POZIOMU
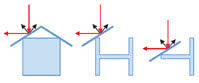
Rys. 1. Rozwiązaniem problemu z fałszywymi odbiciami zakłócającymi pomiary ultradźwiękami jest przykrycie elementów będących ich źródłem blachą lub płytami z tworzywa sztucznego nachylonymi pod odpowiednim kątem (źródło: Introl)
Innym przykładem prostych metod pomiarowych są te wykorzystujące punktowe poziomomierze przełącznikowe, które po raz pierwszy wprowadzono na rynek w latach 40. ubiegłego wieku. Ich kluczowymi elementami są instalowane na szczycie i u dołu, a czasem też pośrodku zbiornika czujniki (punkty przełączania), które aktywują się w momencie kontaktu z substancją przechowywaną. Przełącznik górny zapewnia ochronę przed przepełnieniem, które niezauważone, skutkować może np. rozsypaniem materiału.
Przełącznik dolny i pośrednie sygnalizują z kolei zmniejszanie się zapasów i potrzebę ich uzupełnienia. Instalacja poziomomierzy przełącznikowych jest prosta, a ich użycie relatywnie tanie. Głównym problemem jest natomiast to, że wchodzą one w kontakt z magazynowanym materiałem, który bywa lepki czy ścierny, przez co urządzenia te szybko ulegają zużyciu. Ponadto mierniki punktowe dostarczające informacji tylko z określonych poziomów zbiornika nie zawsze są optymalnym rozwiązaniem, nawet gdy punkty pomiarowe zostały wybrane starannie. Rozwiązaniem bywa dodawanie nowych punktów, to jednak zwiększa koszty.
WAGI ZBIORNIKOWE
Często zamiast mierzyć poziom materiałów składowanych w dużych zbiornikach, wyznacza się ich masę, wykorzystując do tego tzw. wagi zbiornikowe. Podstawowym ich elementem są czujniki tensometryczne przytwierdzane do podstawy silosu, które mierzą jej naprężenia wywołane zmianą obciążenia zbiornika. Ciężar substancji oblicza się następnie, odejmując od wyznaczonej masy ciężar pustego silosu. Zaletą tej metody jest relatywnie duża dokładność, chociaż uwzględnić trzeba wpływ naprężeń w czasie napełniania i opróżniania zbiornika.
Wadą jest natomiast trudna i kosztowna instalacja, która najczęściej wymaga uniesienia silosu. Przed wyborem tej metody pomiaru należy się też upewnić, czy w warunkach danej instalacji wagę zbiornikową będzie można efektywnie wykorzystać. Na przykład w sytuacji gdy kilka zbiorników jest ze sobą sztywno połączonych, niezależny pomiar masy ich zawartości tą metodą nie jest możliwy.
Elektroniczny wskaźnik poziomuPrzyrząd sygnalizuje przekroczenie pięciu poziomów cieczy przewodzącej (o minimalnej przewodności 10 μS) wyznaczonych przez elektrody zainstalowane na odpowiednich wysokościach w zbiorniku. Każda elektroda połączona jest z oddzielnym przekaźnikiem. Zespoły elektrod i przekaźników przypisane do konkretnych poziomów można wykorzystywać w dowolnych konfiguracjach. Przykładem jest system zabezpieczenia pompy przed suchobiegiem (rys. a) oraz system sterowania napełnianiem zbiornika z zabezpieczeniem przed przepełnieniem (rys. b). Elektrody czujnika zasilane są napięciem przemiennym 12V, a prąd płynący w ich obwodzie ma wartość nie większą niż 100μA. Dzięki temu zapobiega się zjawisku elektrokorozji elektrod. Wskaźnik WP-14.ac znaleźć można w ofercie poznańskiej firmy MikroBest.
|
Przyrządy takie jak omawiane znajdziemy m.in. w ofercie katowickiego Introlu, który dostarcza wagi zbiornikowe wykonywane na indywidualne zamówienie dla już istniejących lub dopiero projektowanych silosów. Firma sprzedaje różne modele wag zbiornikowych, w tym modele GPA-NT (fot. 1), GPA-C, GPA -T oraz GPA-NF. Są to kompletne zestawy do montażu pod nogami zbiornika.
Wagę stanowi zabudowa wyposażona w płytę dolną i górną z tłumiącym drgania w kierunku poziomym elastomerowym elementem przeniesienia obciążenia na przetwornik tensometryczny. Wagi wyposażone są ponadto w elementy zabezpieczające przed poderwaniem oraz przed przeciążeniem. Najczęściej stosowane podparcie zbiornika to 3 lub 4 wagi połączone ze skrzynką połączeniową.
POMIARY POJEMNOŚCIOWE
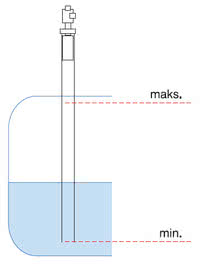
Rys. 2. Problem z tłumieniem sygnału przez pianę oraz zawirowania powierzchni rozwiązać można, umieszczając czujnik w pionowej rurze (źródło: Introl)
Kolejną bardzo popularną metodą wykorzystywaną w przemysłowych pomiarach poziomu jest użycie sond pojemnościowych. Mierzą one pojemność kondensatora, który tworzą dwie elektrody - ściana zbiornika i sonda czujnika odseparowane mierzonym materiałem. Pojemność ta zmienia się w zależności od ilości substancji w silosie. Znając różnicę między pojemnością pełnego i pustego zbiornika, określa się poziom jego napełnienia.
Zaletą techniki pojemnościowej jest możliwość jej wykorzystania do pomiarów różnych materiałów o różnych temperaturach i ciśnieniu. Istotna jest też swoboda instalacji, detektor może być bowiem instalowany w dowolnej części zbiornika (nie powinien on jednak dotykać ani dna, ani ścian zbiornika).
Wadą omawianej metody jest natomiast bezpośredni kontakt elektrod z mierzonym materiałem, co naraża je na zużycie, zwłaszcza przy materiałach ściernych. Ponadto ze względu na związek między pojemnością i stałą dielektryczną mierzonego produktu, wymagana jest kalibracja. Dlatego też na dokładność pomiaru tą metodą wpływa zawilgocenie materiału.
Case study: Pomiary poziomu w produkcji cementuW przeciwieństwie do przemysłu farmaceutycznego czy spożywczego, w których od przyrządów pomiarowych wykorzystywanych na różnych etapach produkcji wymaga się, aby przede wszystkim umożliwiały zachowanie dużego stopnia czystości, w produkcji cementu priorytetem jest duża wytrzymałość mechaniczna czujników oraz odporność na ekstremalne warunki, takie jak temperatury przekraczające 1000°C. Pomiary poziomu w kruszarkach
Ze względu na specyfikę procesu kruszenia skał, w tym głównie twardość obrabianego surowca oraz duże zapylenie, jak też wpływ czynników atmosferycznych, w pomiarze załadowania kruszarek sprawdzają się przede wszystkim czujniki bezkontaktowe. Ze względu na ogromny hałas towarzyszący temu procesowi nie zaleca się w tym wypadku jednak czujników ultradźwiękowych. Czujniki poziomu wykorzystuje się też do monitoringu zapełnienia zbiorników pomocniczych, które instaluje się wzdłuż taśmociągów transportujących skruszone skały. Te specjalne zbiorniki, do których zsypuje się i czasowo gromadzi nadmiar surowca, są niezbędne do regulowania przepustowości linii produkcyjnych. W tym przypadku też lepiej zdecydować się na czujnik bezkontaktowy lub o wzmocnionej konstrukcji, gdyż przyrządy pomiarowe w tym zastosowaniu są narażone na ciągły kontakt ze spadającymi skałami, które mogą je uszkodzić. Przygotowanie mieszanki, wypalenie w piecu, chłodzenie
Po opuszczeniu pieca klinkier ma temperaturę przekraczającą 1300°C i należy go ochłodzić do około 200°C. Najczęściej wykorzystuje się chłodzenie powietrzem. Aby proces ten był jak najbardziej efektywny, należy dokładnie określić grubość klinkieru przesuwającego się na przenośniku. Ze względu na wysoką temperaturę materiału jest to utrudnione. Dlatego w tym celu wykorzystuje się bezkontaktowe czujniki poziomu. Z powodu gorąca często dodatkowo chłodzi się sam czujnik, który musi być wykonany z odpowiednio wytrzymałych materiałów. Magazynowanie i rozdrabnianie klinkieru, produkcja cementu
|
Duży wybór czujników oraz sygnalizatorów pojemnościowych oferuje np. firma Introl. W jej ofercie znajdziemy m.in. produkty Vega, w tym sondy pojemnościowe do pomiaru cieczy przewodzących, nieprzewodzących, oblepiających, materiałów sypkich, w tym w bardzo wysokich zbiornikach, w dużych temperaturach (do 400°C) oraz cieczy chemicznie agresywnych (fot. 2).
ROZWIĄZANIA ULTRADŹWIĘKOWE
Przykładem bezkontaktowej metody pomiaru poziomu jest wykorzystanie ultradźwięków. Sondy tego typu transmitują do wnętrza zbiornika sygnał akustyczny o częstotliwości do kilkudziesięciu kHz, który odbija się od powierzchni składowanego materiału. Mierzony jest czas, jaki upływa od wysłania impulsu do jego ponownego zarejestrowania w czujniku sondy, i na tej podstawie określa się odległość między detektorem miernika i powierzchnią materiału. Dysponując taką informacją można, znając całkowitą głębokość zbiornika, wyznaczyć poziom jego zapełnienia.
Poziomomierze ultradźwiękowe - pomiary nie tylko w przemyśle![]() Tabela 2. Parametry omawianego systemu Inżynierowie z warszawskiej firmy SZTECH, która specjalizuje się w konstruowaniu urządzeń pomiarowych przeznaczonych do pomiaru nieczystości płynnych, opracowali ultradźwiękowy system kontroli poziomu cieczy, który wykorzystać można m.in. do pomiaru zapełnienia szamba. Schemat systemu przedstawiono na rysunku. W skład zestawu wchodzi ultradźwiękowa sonda pomiarowa, wyświetlacz LCD, centralka pomiarowa, adapter zasilający oraz zasilacz. Transmisja danych między centralką pomiarową a wyświetlaczem odbywa się za pośrednictwem okablowania sieci Ethernet. |
Zaletą tego typu pomiarów jest niski koszt drożenia, natomiast wadą sond ultradźwiękowych - wrażliwość na zapylenie. Powoduje to problemy w czasie napełniania zbiornika, gdy pył może całkowicie uniemożliwić pomiary. Korzystania z sond tego typu nie zaleca się też, jeżeli na powierzchni badanego materiału - na przykład podczas uzupełniania zawartości zbiornika - zbiera się piana.
Tłumi ona bowiem sygnał emitowany przez sondę. Gdy podziewamy się wystąpienia takich sytuacji, warto jest rozważyć wybór innego rodzaju poziomomierza. Najczęściej w zamian poleca się sondy mikrofalowe z falowodem, które opisane zostały w drugiej części artykułu. Na dokładność pomiaru ultradźwiękami wpływają też takie parametry ośrodka, w którym rozchodzi się sygnał akustyczny, jak temperatura i ciśnienie.
PROBLEMY Z CZUJNIKAMI ULTRADŹWIĘKOWYMI I ICH ROZWIĄZYWANIE
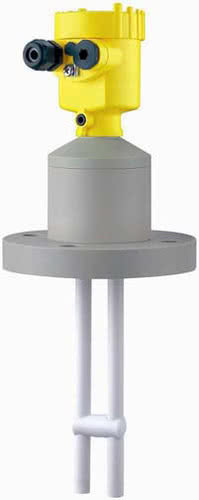
Fot. 2. W ofercie firmy Introl znajdziemy czujniki poziomu produkowane przez fi rmę Vega, m.in. sondę pojemnościową Vegacal 69 do pomiaru poziomu cieczy agresywnych
Skuteczność omawianej metody pomiarowej w dużym stopniu zależy również od układu kontrolera, który odbity sygnał przetwarza, wykrywając w nim sygnały echa powstałe na skutek odbić od drabinek, rozwarstwień materiału, spoin spawalniczych i spiral grzejnych, które nakładają się na sygnał użyteczny. Aby eliminować te zjawiska, podczas nastawiania przyrządu należy zaprogramować zapamiętywanie fałszywego echa.
Przeprowadzając programowanie, należy wcześniej dobrze poznać specyfikę instalacji, w jakiej czujnik będzie pracował. Gdy przykładowo w zbiorniku są zamontowane mieszadła, procedurę zapamiętywania fałszywego echa należy przeprowadzać, gdy mieszadła są w ruchu. Wówczas rozpoznane i zapamiętane zostaną sygnały odbierane wskutek niepożądanych odbić przy różnych ich położeniach.
Problemy z fałszywymi odbiciami można próbować eliminować, nie tylko inwestując w urządzenia, w których zaimplementowano odpowiednie algorytmy przetwarzania sygnału usuwające sygnał echa. Pomocniczym rozwiązaniem może też być przykrycie elementów, będących źródłem niepożądanych odbić, blachą lub płytami z tworzywa sztucznego, które umieszczone pod odpowiednim kątem będą odbijać impulsy ultradźwiękowe w innym kierunku (rys. 1).
![]() Tabela 3. Dane kontaktowe firm wymienionych w artykule |
Obejść można też inne ograniczenia metody ultradźwiękowej. Na przykład problem z tłumieniem sygnału przez pianę oraz wiry powstające na powierzchni medium rozwiązać można, umieszczając czujnik w pionowej rurze (rys. 2). Wstawienie rury nie zawsze jest możliwe - nie zaleca się stosowania tego rozwiązania w przypadku cieczy lepkich. Jeżeli jednak już zdecydujemy się na taką konstrukcję, należy zadbać, by rura sięgała do głębokości zbiornika odpowiadającej minimalnemu poziomowi materiału, który przyrząd ma sygnalizować. Pamiętać trzeba też, by w rurze był otwór do wyrównywania ciśnienia.
W drugiej części artykułuPrzedstawione zostaną radarowe czujniki poziomu, w tym sondy z falowodem, oraz poziomomierze laserowe, co obejmuje również laserowe skanery objętości zbiorników, i czujniki izotopowe. |
Krzysztof Pochwalski
Monika Jaworowska