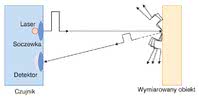
Rys. 1. Odległość w czujnikach typu TOF jest wyznaczana na podstawie pomiaru czasu przelotu impulsów świetlnych między czujnikiem i obiektem
W pomiarach wielkości geometrycznych w przemyśle wykorzystywane są sensory kontaktowe oraz, w przypadku gdy zetknięcie się z wymiarowanym obiektem jest utrudnione, niemożliwe lub niepożądane - czujniki bezkontaktowe.
Te ostatnie są niezastąpione na przykład w pomiarach wymiarów części o małych rozmiarach lub łatwo ulegających uszkodzeniu - m.in. obiektów miękkich, odkształcających się pod wpływem dotyku, łamliwych lub o powierzchni podatnej na zarysowania.
Czujników kontaktowych nie stosuje się również, jeżeli w zetknięciu z detalem mogłyby zostać uszkodzone lub zabrudzone. Może tak się zdarzyć w przypadku wymiarowania obiektów gorących, mokrych, klejących się oraz świeżo pomalowanych lub polakierowanych.
BEZKONTAKTOWE SENSORY ODLEGŁOŚCI
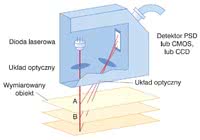
Rys. 2. Czujnik triangulacyjny
W bezkontaktowych pomiarach odległości używane są czujniki wiroprądowe, pojemnościowe, ultradźwiękowe, rentgenowskie oraz optyczne. Elementem pomiarowym w tych pierwszych jest cewka, wokół której na skutek przepływu prądu powstaje pole magnetyczne.
Jeżeli w jego zasięgu znajdzie się obiekt przewodzący prąd elektryczny, są w nim indukowane prądy wirowe, które również stają się źródłem pola magnetycznego. W efekcie proporcjonalnie do odległości dzielącej sensor i metalowy detal zmienia się też natężenie prądu cewki czujnika, co jest analizowane w kontrolerze sensora.
Czujnik pojemnościowy stanowi z kolei para elektrod tworzących kondensator. Jeżeli między nimi pojawia się obiekt wykonany z przewodnika, powstaje układ dwóch szeregowo połączonych kondensatorów. Ich pojemność zależy od odległości dzielącej elektrody i detal.
W czujnikach ultradźwiękowych odległość ta wyznaczana jest natomiast na podstawie pomiaru czasu przelotu impulsów ultradźwiękowych między sensorem a detalem i po odbiciu od obiektu z powrotem do detektora. W czujnikach rentgenowskich wykorzystuje się w tym celu zjawisko tłumienia promieni X po przejściu przez mierzony obiekt.
Wymiar obiektu określa się w tym przypadku, porównując natężenie promieniowania źródła umieszczonego z jednej strony z natężeniem promieniowania zarejestrowanym w detektorze znajdującym się po przeciwnej stronie obiektu.
Do grupy sensorów optycznych zalicza się z kolei czujniki laserowe triangulacyjne i typu TOF (Time Of Flight) oraz czujniki konfokalne. W tych ostatnich odległość wyznacza się, analizując długość fali odbitego od obiektu światła polichromatycznego, wcześniej rozszczepionego w układzie optycznym czujnika.
CZUJNIKI LASEROWE
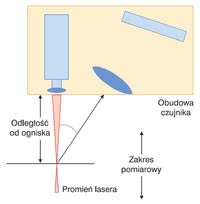
Rys. 3. Ognisko układu optycznego czujnika wyznacza środek zakresu pomiarowego
W sensorach typu TOF, podobnie jak w ultradźwiękowych, bezpośrednio mierzy się czas przelotu impulsu - w tym wypadku świetlnego - między czujnikiem i obiektem. Na tej podstawie z zależności: s = (c·t)/2, gdzie c - prędkość światła, a t to czas przelotu, oblicza się odległość s dzielącą sensor i wymiarowany detal.
Czujnik laserowy TOF (rys. 1) składa się z: lasera emitującego impulsy świetlne, detektora w postaci fotodiody PIN lub fotodiody lawinowej, wzmacniacza sygnału, układu pomiaru czasu oraz jednostki obliczeniowej. Odmianą czujników TOF są sensory fazowe (Phase-Shift TOF), w których wykorzystuje się wiązkę lasera modulowaną sygnałem o częstotliwości f.
Czas przelotu promienia świetlnego między detalem i detektorem oblicza się w tym typie sensorów na podstawie pomiaru przesunięcia fazowego Δφ wiązki odbitej, korzystając z formuły: t = Δφ / (2·π·f). Odległość dzielącą detal i czujnik wyraża wówczas wzór: s = (c·Δφ) / (4·π·f).
Główne komponenty sensorów triangulacyjnych to z kolei: źródło światła, układ optyczny i detektor (rys. 2). Promień lasera po przejściu przez układ soczewek w głowicy czujnika pada na wymiarowany detal. Obraz (A1) plamki świetlnej A wyświetlanej na powierzchni obiektu jest następnie rejestrowany w detektorze.
Na podstawie położenie punktu A1 wyznaczany jest kąt padania wiązki odbitej, co pozwala obliczyć odległość między czujnikiem i obiektem w oparciu o odpowiednie zależności trygonometryczne. Gdy dystans ten zmienia się, również obraz plamki świetlnej w detektorze ulega proporcjonalnemu przesunięciu (punkty B1 i B na rys. 2).
Pomiary wielkości geometrycznych w przemyśle - przykłady
Porównując ich wymiary ze wzorcem, można wykryć zniekształcenia powierzchni (wybrzuszenia, wypukłości, niewspółśrodkowość). Laserowe sensory odległości są również używane do monitorowania przebiegu procesu montażu układów scalonych oraz nanoszenia warstw kleju, lakieru lub farby. W tym drugim wypadku są wykorzystywane na przykład do pomiaru szerokości lub grubości nanoszonego spoiwa lub materiału. W ramach linii automatycznego spawania lub zgrzewania czujniki laserowe dostarczają z kolei informacji pozwalających wykryć brakujące spawy lub zgrzewy, podwójne spoiwa oraz sprawdzić ich grubość, szerokość i położenie. W ten sposób zapobiega się dalszej obróbce wybrakowanych wyrobów. Pomiary grubości są również przeprowadzane w ramach linii walcowania, gdzie umożliwiają sprawdzenie dokładności wykonania powierzchni arkuszy blach używanych m.in. do produkcji obudów AGD lub w przemyśle motoryzacyjnym.
Odzyskany w ten sposób surowiec może być wykorzystany ponownie. W produkcji wielu produktów spożywczych kluczowa jest ponadto grubość ciasta, z którego później formowane są na przykład ciastka lub placki na pizzę. Wybiórcza kontrola gotowych produktów nie jest optymalnym rozwiązaniem, ponieważ przy wadliwych ustawieniach maszyny może zostać wyprodukowana spora partia produktów. Lepiej sprawdza się ciągła kontrola z wykorzystaniem czujników odległości na przykład zamontowanych nad i pod przesuwającym się na rolkach ciastem, dzięki której praca urządzeń jest na bieżąco korygowana. Czujniki grubości są też instalowane w obrębie linii porcjowania lub cięcia na plasterki przykładowo mięsa, sera lub chleba. |
SENSORY LASEROWE - ZALETY...
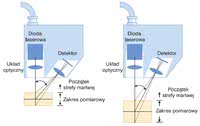
Rys. 4. Zakres pomiarowy i długość strefy martwej zależą od konstrukcji układu optycznego czujnika
Lasery, głównie z ośrodkiem czynnym w postaci ciała stałego lub lasery półprzewodnikowe wykorzystuje się jako źródło światła w czujnikach triangulacyjnych i tych mierzących czas przelotu ze względu na właściwości emitowanego przez nie promieniowania.
Istotna jest przede wszystkim możliwość uzyskania spójnej, silnie skoncentrowanej oraz monochromatycznej wiązki światła. To ostatnie zapewnia odporność na wpływ oświetlenia z otoczenia, natomiast dwie pierwsze właściwości gwarantują dużą rozdzielczość pomiaru.
Oprócz tego czujniki laserowe charakteryzuje większa odporność na warunki środowiskowe (na przykład zmiany wilgotności oraz ciśnienia) w porównaniu do sensorów pojemnościowych i ultradźwiękowych oraz brak ograniczeń pod względem właściwości elektrycznych wymiarowanych detali, które dotyczą czujników wiroprądowych.
Ponadto w przeciwieństwie do metody wykorzystującej zjawisko tłumienia promieniowania rentgenowskiego, w której do obliczenia grubości obiektu wymagana jest m.in. informacja o jego gęstości, w pomiarach laserowych nie jest konieczna znajomość fizykochemicznych parametrów mierzonego materiału.
Do zalet sensorów laserowych zalicza się też dużą dokładność, krótki czas pomiaru oraz przede wszystkim możliwość zamontowania w większej odległości od obiektu niż w przypadku pozostałych typów czujników bezkontaktowych.
To ostatnie ogranicza prawdopodobieństwo uszkodzenia czujnika w razie wystąpienia awarii lub innych nieprzewidzianych zdarzeń w obrębie linii produkcyjnej. Nie jest też dzięki temu konieczne modyfikowanie konfiguracji systemu pomiarowego w razie częstej i dużej zmienności rozmiarów mierzonych detali.
...I WADY
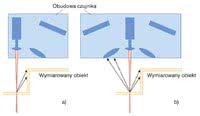
Rys. 5. Ze względu na kształt obiektu promienie odbite od jego powierzchni nie mogą dotrzeć do detektora (a); rozwiązaniem tego problemu jest czujnik z dwoma torami rejestracji obrazu (b)
Czujniki optyczne do prawidłowego funkcjonowania wymagają zachowania dobrej widoczności między źródłem światła a jego detektorem, w związku z czym na drodze promienia świetlnego nie mogą występować żadne przeszkody. Na wynik pomiarów negatywnie wpływają pyły i zadymienie, jak również zanieczyszczenia układu optycznego czujnika.
To ostatnie powoduje, że częste i dokładne czyszczenie oraz konserwacja elementów optycznych sensora powinny być obowiązkowe. Ponadto ze względu na komponenty elektroniczne będące częścią głowicy czujników tego typu, zakres ich temperatur pracy jest ograniczony (typowo do 40°C).
Oprócz tego integracja sensorów optycznych w ramach linii produkcyjnych nie zawsze jest prosta, a wszelkie niedociągnięcia na tym etapie skutkują zmniejszeniem dokładności pomiarów lub nawet nieprawidłowymi wynikami.
Dokładność pomiarów może też maleć na skutek drgań detalu. Poza tym niektóre typy powierzchni, na przykład odblaskowe lub różnokolorowe, wymagają zastosowania czujników o specjalnej konstrukcji.
PARAMETRY CZUJNIKÓW TRIANGULACYJNYCH
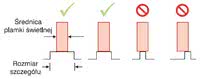
Rys. 6. Średnica plamki świetlnej powinna być mniejsza niż rozmiar najmniejszego szczegółu wymiarowanego detalu, który może mieć wpływ na dokładność pomiaru
Wybierając czujnik laserowy, należy przeanalizować jego parametry oraz szczegóły konstrukcji decydujące o jego przydatności w danym zastosowaniu, co przedstawimy na przykładzie sensorów triangulacyjnych. Ważnymi parametrami są zakres pomiarowy oraz długość tzw. strefy martwej.
Ta ostatnia to odległość między czujnikiem i początkiem zakresu pomiarowego, w której pomiar nie jest możliwy lub jego wyniki są niewiarygodne. Sensor powinien mieć wystarczająco duży zakres pomiarowy, by mógł zmierzyć odległość od obiektu w spodziewanym zakresie jej zmienności.
Długość strefy martwej warunkuje natomiast możliwość zainstalowania czujnika w dostępnych warunkach przestrzennych. Jeżeli wymagany odstęp między głowicą czujnika i początkiem zakresu pomiarowego jest zbyt krótki, może uniemożliwić zamontowanie go w bezpiecznej odległości, na przykład od taśmociągu.
Jeżeli z kolei konieczne jest zapewnienie dużej odległości instalacja czujnika może okazać się niemożliwa z powodu braku miejsca. Na oba te parametry wpływa konstrukcja układu optycznego czujnika. Odległość, w jakiej znajduje się jego ognisko (rys. 3), wyznacza środek zakresu pomiarowego.
W punkcie tym plamka światła jest najmniejsza, a jego obraz wyświetlany jest dokładnie na środku detektora. Zakres pomiarowy i długość strefy martwej zależą też od kąta nachylenia detektora. Im jest on mniejszy, tym zakres pomiarowy i strefa martwa są większe (rys. 4). Niestety jednocześnie wówczas rozdzielczość pomiarów jest mniejsza.
Ponadto jeżeli kąt ten jest zbyt mały (w czujnikach o małej rozdzielczości wynosić może zaledwie 10°) lub zbyt duży (przy dużej rozdzielczości nawet 45°), w danych warunkach pomiar może okazać się niemożliwy.
Może się tak zdarzyć, gdy na przykład ze względu na kształt obiektu promienie odbite od jego powierzchni nie dotrą do detektora rys. 5a. Rozwiązaniem jest wówczas zmiana ustawienia czujnika lub zastąpienie go sensorem z dwoma torami rejestracji obrazu (rys. 5b).
Czujniki laserowe 2D i 3D
W czujnikach tego typu wykorzystuje się specjalny układ soczewek, który pozwala uzyskać taki kształt promienia lasera jak na fotografii. Jeszcze pełniejszej informacji o wymiarach obiektu dostarczają skanery 3D. W ich wypadku na podstawie sekwencyjnie wykonywanych pomiarów punktowych gromadzony jest zbiór informacji o odległościach. Na tej podstawie w komputerze odtwarzany jest kształt obiektu. |
ROZMIAR PLAMKI ŚWIETLNEJ
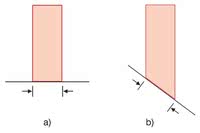
Rys. 7. Jeżeli promień lasera nie pada prostopadle do mierzonej płaszczyzny średnica plamki wydłuża się proporcjonalnie do kąta tego odchylenia (b)
Rozmiar plamki świetlnej ma duże znaczenie w pomiarach obiektów o małych rozmiarach, o drobnych szczegółach konstrukcji oraz zakrzywionej powierzchni, jest za to mniej istotny w przypadku powierzchni płaskich i jednorodnych.
Przyjmuje się, że średnica plamki powinna być mniejsza niż rozmiar najmniejszego spodziewanego elementu (rys. 6). Im jest mniejsza, tym lepiej, ponieważ wówczas rzadziej występują błędy spowodowane tym, że plamka pada na granicę dwóch obszarów o różnych współczynnikach odbicia, na przykład na styku powierzchni o różnych kolorach.
Rozmiar plamki najmniejszy jest w ognisku układu optycznego czujnika i to ta wartość najczęściej jest podawana w specyfikacji. Ponieważ na początku i na końcu zakresu pomiarowego średnica plamki jest większa niż w jego środku, niektórzy producenci w kartach katalogowych sensorów umieszczają także informację o tych dwóch wartościach.
Na rozmiar plamki wpływa też sposób zamontowania czujnika. Jeżeli promień lasera nie pada prostopadle do mierzonej płaszczyzny, średnica plamki wydłuża się proporcjonalnie do kąta odchylenia (rys. 7). Warto na to zwrócić uwagę, jeśli rozmiar plamki jest dla poprawności wyników pomiarów bardzo istotny.
Przegląd oferty producentów czujników laserowych![]() Tabela 1. Parametry czujników serii ZX2 firmy Omron Electronics Czujniki z serii ZX2 W ofercie firmy Omron Electronics znajduje się między innymi seria ZX2, w skład której wchodzą czujniki laserowe triangulacyjne z detektorem obrazu CMOS, zarówno punktowe - modele ZX2-LD50 i ZX2-LD100, jak i wyświetlające linię pomiarową - modele ZX2-LD50L i ZX2-LD100L. Częścią zestawu jest oprócz głowicy czujnika także wzmacniacz. Oddzielnie można ponadto dokupić moduł obliczeniowy. Źródłem światła we wszystkich czujnikach serii ZX2 jest laser półprzewodnikowy o długości fali 660nm (czerwony) i maksymalnej mocy wyjściowej 1mW (klasa 2). W tabeli poniżej zebrano najważniejsze parametry sensorów serii ZX2.
Czujniki laserowe firmy Leuze electronic Czujniki laserowe triangulacyjne oraz typu TOF oferuje też firma Leuze electronic. Do pierwszej grupy zaliczają się czujniki serii ODSL 9, natomiast sensory wykorzystujące metodę pomiaru czasu przelotu impulsu świetlnego można znaleźć wśród czujników serii ODS96B. W tabeli poniżej zebrano wybrane parametry przykładowego czujnika serii ODSL9. Laserowe sensory odległości firmy Balluff ![]() Tabela 4. Wybrane parametry OADM 20I6591, OADM 20I6592 oraz OADM 20I6593 firmy Baumer Różnią się one natomiast obszarem roboczym (maksymalną odległością od czujnika), która w czujnikach poszczególnych serii maksymalnie wynosi: BOD21M - 500mm, BOD26K - 300mm, BOD63M - 6000mm i BOD66M - 2000mm. W poniższej tabeli przedstawiono parametry przykładowego czujnika serii BOD66M. Czujnik do stosowania na zewnątrz firmy Baumer Spory wybór laserowych czujników do pomiaru odległości ma w swoim asortymencie również firma Baumer. Przykładem są sensory z serii OADM20, które na tle innych wyróżniają się dużą odpornością na wpływ oświetlenia z otoczenia, dzięki czemu można je wykorzystać w pomiarach na zewnątrz. Są to aktualnie trzy czujniki: OADM 20I6591, OADM 20I6592 oraz OADM 20I6593. Wszystkie wykorzystują linię pomiarową wyświetlaną przez czerwony laser (długość fali 650nm, klasa 2). Porównanie ich najważniejszych parametrów zamieszczono w poniższej tabeli.
Czujniki laserowe firmy Micro-Epsilon Na koniec przedstawiamy parametry wybranych czujników laserowych oferowanych przez firmę Micro-Epsilon. Jednymi z nich są sensory optoNCDT 1700BL z niebieskim laserem (o długości fali 405nm), szczególnie zalecane do pomiarów żarzących się metali i wyrobów z drewna. Drugim rodzajem są czujniki z czerwonym laserem o długiej strefie martwej, zalecane w przypadku gdy sensor nie może być zamontowany zbyt blisko mierzonego obiektu - na przykład ze względu na to, że może zostać uszkodzony lub nie ma miejsca lub możliwości zamontowania czujnika przy obiekcie (na przykład znajduje się on w komorze). Jeszcze większy odstęp od czujnika zapewnia sensor 1710-1000. W jego wypadku zakres pomiarowy wynosi 1m, jego początek wypada w odległości od czujnika również równej 1m, środek - 1,5m oraz koniec - 2m. |
CZUJNIKI DO POWIERZCHNI ODBLASKOWYCH
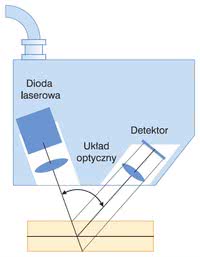
Rys. 8. Czujnik o konstrukcji zmodyfikowanej do pomiaru obiektów o powierzchni odblaskowej
Wybierając czujniki, uwzględnić należy też specyfikę powierzchni wymiarowanych obiektów. Problemem są szczególnie takie, które charakteryzuje duża refleksyjność. Pomiar odległości od obiektów o powierzchni tego typu jest w przypadku czujnika laserowego w konfiguracji jak na rysunku 2 niemożliwy.
Promień lasera, padając na taką powierzchnię po odbiciu padałby bowiem nie na detektor, ale z powrotem do punktu wyjścia. Rozwiązaniem tego problemu jest zastosowanie czujnika o konstrukcji zmodyfikowanej jak na rysunku 8. Promień lasera jest w nim kierowany na detal pod odpowiednim kątem, tak by po odbiciu od jego powierzchni padał wprost na detektor.
W przypadku czujników laserowych problemem jest też duża zmienność kolorów, a tym samym refleksyjności powierzchni wymiarowanego obiektu. W takim wypadku najlepszym rozwiązaniem jest wykorzystanie czujnika, w którym zaimplementowano rozwiązanie kompensujące wpływ zmian odblaskowości na dokładność pomiaru. Najczęściej polega to na zastosowaniu układu regulacji mocy lasera dostosowywanej do właściwości aktualnie mierzonej powierzchni.
Bezpieczeństwo użytkowania laserów
Naświetlenie narządu wzroku również powoduje poparzenia, uszkodzenia tkanek oraz w wyniku powikłań różne choroby oczu. Dlatego pracując z urządzeniami zawierającymi laser, trzeba stosować odpowiednie środki bezpieczeństwa. Dobierając je, należy opierać się na informacji o potencjalnym zagrożeniu przekazywanej przez producenta urządzenia, który powinien je odpowiednio oznakować. W tym celu laser wykorzystywany w danym urządzeniu należy przypisać do jednej z następujących klas bezpieczeństwa:
Lasery używane w czujnikach odległości najczęściej zaliczane są do klasy 2. |
DETEKTORY, DŁUGOŚĆ FALI
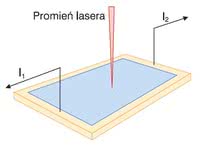
Rys. 9. Detektor PSD to przetwornik fotorezystancyjny, w którym położenie plamki świetlnej określa się na podstawie sygnałów prądowych na wyjściach układu
Warto też sprawdzić, jaki typ detektora wykorzystano w danym modelu czujnika. Najczęściej jest to albo światłoczuła matryca CMOS lub CCD, albo detektor PSD (Position Sensing Detector). Ten drugi wykonuje się jako przetwornik fotorezystancyjny, w którym położenie plamki świetlnej określa się na podstawie sygnałów prądowych na wyjściach detektora (rys. 9).
Jeżeli plamka znajduje się w środku detektora, natężenia prądów przetwornika są równe. W miarę przesuwania się plamki w kierunku krawędzi detektora jego prądy wyjściowe zmieniają się proporcjonalnie. Zaletą detektorów PSD jest krótki czas odpowiedzi, natomiast przetworniki CCD są dokładniejsze.
W przeciwieństwie do PSD matryce CCD są też niewrażliwe na zmianę natężenia padającego na nie światła na przykład na skutek zmiany koloru powierzchni lub jej tekstury. W specyfikacjach czujników laserowych producenci z reguły zamieszczają też informację o długości fali promieniowania lasera (kolorze światła).
Chociaż nie ma ona wpływu na dokładność lub inne znaczące parametry czujnika, w praktyce lepiej, gdy laser emituje promieniowanie w zakresie widzialnym (najczęściej jest to światło czerwone).
Oprócz tego, że operator może wówczas wizualnie stwierdzić, że laser jest włączony, łatwiej może też wychwycić wszelkie nieprawidłowości w działaniu lub ustawieniu czujnika. Barwa światła lasera może mieć jednak znaczenie w pewnych zastosowaniach.
Na przykład w przypadku pomiarów powierzchni żarzących się czujnik z czerwoną plamką świetlną nie jest odpowiedni i lepiej wykorzystać sensor z laserem emitującym promieniowanie o kolorze niebieskim (patrz ramka z przykładami czujników).
Monika Jaworowska
W drugiej części artykułu przedstawimy najpopularniejsze konfiguracje układów pomiarowych z czujnikami laserowymi wykorzystywanymi w pomiarach wielkości geometrycznych oraz wskazówki praktyczne na temat ich realizacji. |