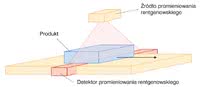
Rys. 1. Źródło i detektor promieniowania to główne komponenty stanowiska do inspekcji rentgenowskiej
Ciała obce są szczególnym problemem w produktach farmaceutycznych, kosmetycznych oraz spożywczych. Ponieważ wyroby te są konsumowane lub mają kontakt z ciałem człowieka, zanieczyszczenia w nich występujące mogą stanowić bezpośrednie zagrożenie dla zdrowia lub życia ludzi.
Wprowadzenie ich do obrotu uderza też w interesy producenta w przypadku, gdy musi on wycofać ze sprzedaży całą partię artykułów, rozpatrzyć masowo napływające reklamacje lub wypłacić odszkodowania. W przypadku poważniejszych skutków dla zdrowia lub życia konsumentów możliwe są też konsekwencje prawne.
Takie zdarzenia mogą pogorszyć wizerunek firmy na długie lata. Oprócz tego ciała obce w produkcie lub w jego składnikach mogą zablokować lub uszkodzić maszyny. Również to powoduje straty finansowe, gdy konieczne jest naprawienie urządzenia, zakup nowego lub wstrzymanie produkcji.
Przykłady systemów inspekcji rentgenowskiej. 1
Głównym elementem systemu jest ekranowana komora. Znajduje się w niej źródło promieniowania rentgenowskiego (lampa 225 kV lub 160 kV), układ zmian położenia źródła oraz stół do mocowania i manipulowania elementami. Częścią X-Cube jest również wzmacniacz obrazu Vistalux, który przetwarza promieniowanie rentgenowskie w obraz wideo oraz system poprawy jakości obrazu Vistaplus. Sterowanie całością odbywa się za pośrednictwem dotykowego pulpitu sterowniczego w technologii X-Touch. System kontroli radiograficznej X-Cube przeznaczony jest do zastosowań w przemyśle - przykładowo do kontroli jakości odlewów oraz elementów ze stali, z tworzyw sztucznych, ceramiki oraz stopów specjalnych. Dostępne są dwa modele tego urządzenia: X-Cube Compact oraz X-Cube XL. Ten drugi ma większą szafkę kontrolną, można też w nim poddawać kontroli elementy o większych rozmiarach (patrz tabela).
|
INSPEKCJA RENTGENOWSKA
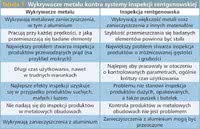
Tabela 1. Wykrywacze metalu kontra systemy inspekcji rentgenowskiej
Wykrycie zanieczyszczeń, zwłaszcza w produktach w płynie, w proszku, w formie masy plastycznej lub paczkowanych, nie jest niestety łatwym zadaniem. Ze względu na właściwości takich wyrobów, możliwość ich zniszczenia albo wymóg zachowania sterylności lub higienicznych warunków metody wymagające bezpośredniego kontaktu z produktem są bezużyteczne, a kontrola wizualna zwykle nieefektywna.
Alternatywą jest inspekcja rentgenowska. Stanowisko do badania jakości tą metodą składa się ze źródła oraz detektora promieniowania rentgenowskiego, między którymi umieszcza się badany obiekt (rys. 1). Jego częścią jest również system analizy wyników kontroli oraz powiadamiania, przykładowo sygnałem świetlnym lub dźwiękowym, o wykryciu produktów uszkodzonych lub zanieczyszczonych.
Niektóre stanowiska uzupełnia się też o system eliminowania takich wyrobów. W zależności od wymagań, zwłaszcza specyfiki obiektów poddawanych inspekcji, w tym celu są wykorzystywane m.in. systemy pneumatyczne do przemieszczania detali oraz klapy.
Klasyfikacja systemów inspekcji rentgenowskiejW zależności od konfiguracji oraz przeznaczenia systemy inspekcji rentgenowskiej podzielić można na trzy grupy. Pierwszą stanowią systemy zabudowane w linii produkcyjnej, których zadaniem jest wykrywanie zanieczyszczeń w produktach przesuwających się na taśmociągu. Rozwiązanie takie jest popularne zwłaszcza w przemyśle spożywczym, farmaceutycznym oraz kosmetycznym. Do grupy drugiej zaliczane są wydzielone stanowiska kontrolne zrealizowane w postaci kabin wolnostojących lub pomieszczeń ekranowanych. Przeprowadza się w nich zwykle kontrolę jakości produktów, w czasie której wykrywane są wady konstrukcyjne oraz weryfikowana jest kompletność, poprawność rozmieszczenia elementów oraz ich wymiary. Inspekcja rentgenowska realizowana jest zwykle w ten sposób w przemyśle ciężkim, lotniczym, motoryzacyjnym, elektronicznym oraz w przetwórstwie tworzyw sztucznych. W przypadku gdy konieczne jest poddanie badaniu elementu w czasie jego eksploatacji, a specyfika jego lub instalacji, w której pracuje, wyklucza transport do stanowiska inspekcji, wykorzystywane są systemy mobilne. Najczęściej w ten sposób kontroluje się elementy dużych maszyn, rurociągi oraz połączenia w konstrukcjach stałych, które w czasie eksploatacji mogą ulec uszkodzeniu lub po prostu się zużyć. |
PROMIENIOWANIE X, LAMPY RENTGENOWSKIE
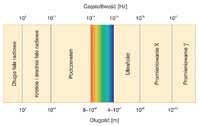
Rys. 2. Widmo promieniowania elektromagnetycznego
Promieniowanie rentgenowskie (promieniowanie X, RTG) to rodzaj promieniowania elektromagnetycznego o długości fali w przedziale od kilku pm do 10 nm (rys. 2). Ma ono specyficzną właściwość - może przenikać przez materiały nieprzezroczyste dla światła widzialnego.
Stopień tej przepuszczalności zależy od gęstości danego materiału - im jest ona większa, tym mniej promieni przez niego przenika. Pozwala to odróżnić od siebie na obrazie RTG produktu elementy o różnej gęstości, w tym na przykład zanieczyszczenia. Źródłem promieniowania w systemach inspekcji RTG są lampy rentgenowskie.
Ich zaletą jest to, że nie wykorzystują izotopów promieniotwórczych - wystarczy odłączyć je od zasilania, by promieniowanie nie było emitowane. Zwiększa to bezpieczeństwo użytkowania omawianych urządzeń. Lampa wykonywana jest w postaci szklanej banki próżniowej, wewnątrz której umieszcza się dwie elektrody: katodę i anodę połączone ze źródłem wysokiego napięcia.
Katoda, zwykle w postaci włókna wolframowego dodatkowo zasilanego z drugiego źródła niższego napięcia, żarząc się emituje elektrony. Cząstki te przyspieszane są w polu elektrycznym między elektrodami i bombardują anodę, w momencie zderzenia z nią emitując promieniowanie rentgenowskie.
Procesowi temu towarzyszy wydzielanie dużych ilości ciepła w anodzie, którą z tego powodu pokrywa się materiałem o dużej temperaturze topnienia (na przykład wolframem). Ponieważ wysoka temperatura skraca żywotność lampy wymagane jest też chłodzenie anody. Najczęściej realizuje się to montując w niej system odprowadzania ciepła. Zwykle ma on postać przewodu, przez który pompowana jest ciecz chłodząca.
Przykłady systemów inspekcji rentgenowskiej. 2
Główne elementy systemu:
Jako opcję można wybrać m.in.:
|
PODZIAŁ LAMP RTG
Lampy rentgenowskie charakteryzuje się podając ich napięcie, prąd oraz średnicę plamki ogniska wiązki promieniowania. Ten ostatni parametr jest jednym z kryteriów podziału tych urządzeń na konwencjonalne (z wiązką o średnicy powyżej 1 mm) oraz typów: fine-focus (o średnicy powyżej 50 μm), micro-focus (o średnicy poniżej 50 μm) i nano-focus (o średnicy mniejszej niż 1 μm).
Lampy rentgenowskie dzieli się też na hermetyczne (sealed tube) oraz otwarte (open tube). W tych pierwszych próżnia uzyskiwana jest fabrycznie, dzięki czemu są one gotowe do użycia zaraz po uruchomieniu systemu. Charakteryzuje je też dłuższy czas użytkowania. W przypadku gdy ulegną uszkodzeniu muszą być jednak odesłane do producenta, o ile naprawa jest w ogóle możliwa, lub wymienione.
W przypadku lamp otwartych próżnia w komorze, w której znajdują się elektrody jest tworzona każdorazowo po włączeniu zasilania urządzenia, przez co proces uruchomienia systemu inspekcji wydłuża się. Zaletą lamp tego typu jest jednak możliwość wymiany uszkodzonej katody lub anody "na miejscu". Niestety wymagają one takich działań zdecydowanie częściej niż lampy hermetyczne.
Przykłady wykorzystania inspekcji RTG w kontroli jakościW kontroli jakości komponentów z tworzyw sztucznych aparaty RTG używane są m.in. do wykrywania pęcherzy powietrza, wtopionych zanieczyszczeń, pęknięć lub zniekształceń. Defekty tego typu powodują osłabienie wytrzymałości mechanicznej części w miejscu, w którym się tworzą (fot. 1). Innym obszarem zastosowań inspekcji jest ocena jakości struktury drewna.
W tym przypadku najczęściej wykrywane wady to drzazgi, sęki, wgłębienia oraz nadgnicia (fot. 2). Inspekcja rentgenowska jest też użyteczna w detekcji pęknięć, zanieczyszczeń, porowatości i korozji rur oraz w pomiarach grubości ich ścianek. W przypadku rur z płaszczem oraz izolowanych jest to często jedyny sposób na przeprowadzenie efektywnej kontroli ich jakości (fot. 3). Kolejnym przykładem są tarcze do szlifierek. W tym wypadku prześwietlanie promieniami X pozwala wykryć mikropęknięcia, porowatość, rysy oraz wtopione zanieczyszczenia. Podczas użytkowania dysku takie defekty mogą powodować jego pęknięcie, co może skutkować zranieniem operatorów szlifierek (fot. 4). Kontrola rentgenowska jest też powszechnie wykorzystywana w przemyśle spożywczym. Systemy takie używane są do wykrywania zanieczyszczeń - przykładowo kości i ich odłamków w mięsie, ości w filetach, a także do weryfikacji zawartości zapakowanych produktów oraz do sprawdzania dokładności i szczelności opakowań (fot. 5).
Aparaty RTG są też używane do sprawdzania kompletności, poprawności oraz dokładności montażu różnych urządzeń. W ten sposób można przykładowo wykryć przerwane przewody, brakujące podzespoły, przerwane ścieżki, zwarcia na płytkach drukowanych, uszkodzone komponenty, deformację kształtu urządzenia lub jego elementów, brakujące śruby, przesunięcia elementów względem ich właściwej pozycji oraz za duże lub zbyt małe odstępy między komponentem lub obudową (fot. 6). |
DETEKTORY, INSPEKCJA 2D / 3D
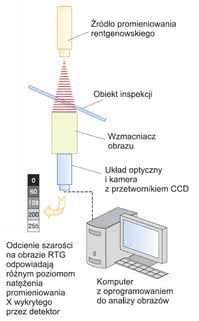
Rys. 3. Detektor promieniowania RTG składa się zwykle ze wzmacniacza obrazu oraz kamery
Detektor promieniowania RTG składa się zwykle ze wzmacniacza obrazu oraz kamery z przetwornikiem obrazu CCD. Pierwszy element pochłania promieniowanie rentgenowskie przetwarzając je na światło widzialne, które następnie kamera przetwarza na sygnał elektryczny. Na jego podstawie w komputerze odtwarzany jest monochromatyczy obraz obiektu.
Poszczególne odcienie szarości odpowiadają na nim konkretnym poziomom natężenia promieniowania X zarejestrowanego w detektorze. Obraz ten jest wyświetlany na monitorze (rys. 3). Jako detektor promieniowania mogą też być wykorzystywane płyty luminoforowe podobne do klisz stosowanych w klasycznej radiografii. Po naświetlaniu są one skanowane w specjalnych skanerach, w których uzyskuje się cyfrowy obraz obiektów.
Obiekty poddawane inspekcji są zwykle transportowane na przenośniku, a jeżeli jest to wymagane umieszcza się je w specjalnych uchwytach. Zwykle można nimi zdalnie manipulować, ustawiając element w odpowiedniej pozycji w czasie naświetlania. Dostępne są również urządzenia z ruchomym ramieniem, na którego przeciwległych końcach zamontowano układ pomiarowy (lampę i detektor).
Wówczas obiekt zwykle umieszczany jest na obrotowym stoliku ustawionym między źródłem i odbiornikiem promieni X. W ten sposób uzyskuje się obraz rentgenowski dwuwymiarowy (przekrój). Aby uzyskać obraz 3D najpierw tworzy się wiele obrazów 2D obiektu - na przykład odpowiednio nim obracając. Następnie dane te są przetwarzane w specjalistycznym oprogramowaniu.
Inspekcja 3D ma wiele zalet, ale również i wady. Przede wszystkim pozwala uzyskać dokładniejszy obraz obiektu, a dzięki jego przestrzennej wizualizacji łatwiej można wykryć szczególnie trudno dostrzegalne defekty oraz zanieczyszczenia. W ten sposób unika się też wzajemnego przesłaniania się części obiektu, na przykład tych z tyłu (lub pod spodem) przez te znajdujące się z przodu (lub na górze).
Problem ten dotyczy na przykład dwustronnych płytek drukowanych. Wadą inspekcji 3D, która ma kluczowe znaczenie dla możliwości jej wdrożenia w ramach linii produkcyjnych jest duża złożoność obliczeniowa. Z tego powodu tworzenie obrazu trójwymiarowego może trwać dłużej niż obrazu 2D.
|
ANALIZA OBRAZÓW RENTGENOWSKICH
Obrazy rentgenowskie są analizowane przez operatora lub w ramach automatycznego systemu. Każda z tych metod ma swoje wady i zalety. W pierwszym przypadku istnieje większe prawdopodobieństwo właściwej interpretacji obrazu RTG w razie wystąpienia na nim obiektów o nietypowych kształtach, bardzo małych rozmiarach oraz w sytuacjach, gdy gęstości ewentualnych ciał obcych i produktu mogą być zbliżone.
Koszt takiego rozwiązania jest też niższy niż w przypadku systemu komputerowego, chociaż wyszkolenie operatorów również kosztuje. Ponadto ich efektywność może się zmieniać na skutek takich czynników jak brak koncentracji, zmęczenie lub odwrócenie uwagi. W systemie automatycznym kluczowe jest ustalenie odpowiedniego poziomu gęstości powyżej lub poniżej którego dany element zarejestrowany na obrazie uznaje się za defekt.
Inspekcja taka jest najefektywniejsza w przypadku obiektów o stałej grubości oraz gęstości - w innym przypadku (przykładowo w czasie kontroli wyrobów opakowanych) mogą wystąpić problemy z interpretacją obrazu RTG.
Aby temu zapobiec zwykle wykorzystuje się specjalistyczne oprogramowanie, w którym zaimplementowano algorytmy przetwarzania obrazów uwzględniające zmienność grubości i gęstości obiektu oraz właściwości jego opakowania. Zazwyczaj wymagają one większej mocy obliczeniowej procesora, przez co mogą znacząco obciążyć system inspekcji, a nawet spowolnić cały proces kontroli jakości.
Przykłady systemów inspekcji rentgenowskiej. 3Separator zanieczyszczeń z produktów spożywczych X-Ray eXpurity 2000 z oferty firmy Innexim X-Ray eXpurity 2000 na podstawie obrazu rentgenowskiego produktów przesuwających się na taśmociągu wykrywa wyroby zawierające zanieczyszczenia, które następnie są usuwane z linii produkcyjnej. System ma możliwość detekcji m.in. ciał obcych o rozmiarze (długości boku) od 0,8 mm w przypadku zanieczyszczeń z żelaza i stali nierdzewnej oraz od 3 mm w wypadku zanieczyszczeń ze szkła, kamieni oraz kości. Oprócz tego urządzenie wykrywa też odchylenia wagi od wzorca oraz defekty mechaniczne, archiwizuje zdjęcia produktów i tworzy statystyki (wydajności, liczby badanych produktów, zestawienia na produkt, partię, itp.). Części X-Ray eXpurity 2000 są wykonane m.in. ze stali nierdzewnej, tworzyw sztucznych oraz materiałów dopuszczonych do użytku w przemyśle spożywczym. |
JAKOŚĆ OBRAZÓW RTG
Efektywność analizy wyników inspekcji zależy od jakości uzyskanych obrazów rentgenowskich. Charakteryzują ją głównie trzy parametry: stosunek sygnału do szumu (SNR), rozdzielczość oraz kontrast. Zależą one m.in. od konstrukcji aparatu RTG, sposobu przeprowadzania pomiaru oraz parametrów komponentów systemu rejestracji i odtwarzania tego obrazu, a także specyfiki badanego obiektu.
Na pierwszy parametr wpływają przede wszystkim tzw. szumy kwantowe (śrutowe) wynikające z losowości właściwości fotonów promieniowania X padających na detektor (czynnik ten ma decydujące znaczenie) i fotonów światła emitowanych przez detektor, a także ruchu ładunków w detektorze i elementach elektronicznych. Szumy te można zmniejszyć wydłużając czas naświetlenia.
Zwykle jednak w systemach kontroli, w których szybkość inspekcji jest jednym z priorytetów dąży się do tego, by był on jak najkrótszy. Na kontrast ma wpływ m.in. napięcie lampy - jeżeli będzie zbyt duże parametr ten maleje, co zmniejsza czytelność obrazu.
Rozdzielczość obrazu rentgenowskiego zależy z kolei m.in. od średnicy wiązki promieniowania, odległości źródło - detektor oraz odległości obiekt - detektor. By uzyskać jak największą rozdzielczość bez efektu cienia (rys. 4) należy zapewnić jak najmniejszą średnicę wiązki promieniowania (idealnie powinno to być źródło punktowe), możliwie największy dystans źródło - detektor oraz jak najmniejszą odległość dzielącą badany obiekt i detektor.
Przykłady systemów inspekcji rentgenowskiej. 4
Wybrane cechy:
|
CZY INSPEKCJA RTG JEST BEZPIECZNA?
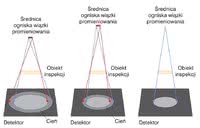
Rys. 4. Rozdzielczość obrazu rentgenowskiego zależy m.in. od odległości źródło - detektor
Bezpieczeństwo użytkowania systemów inspekcji rentgenowskiej wzbudza spore kontrowersje. Dotyczy to zarówno negatywnego wpływu promieniowania X na zdrowie obsługi lub personelu pracującego w pobliżu, jak i na jakość produktów. To drugie odnosi się szczególnie do wyrobów spożywczych. Okazuje się, że w obu przypadkach obawy te są bezzasadne.
Według WHO (World Health Organization) napromieniowanie żywności do poziomu 10 tys. Sv nie powoduje jej skażenia, ani też utraty wartości odżywczych. Tymczasem dawka promieniowania, jaką produkt absorbuje w czasie naświetlania trwającego zwykle około kilkuset ms jest rzędu ułamka mSv. Jest to w przybliżeniu dziesięć milionów razy mniej niż dopuszczalna wartość graniczna.
Poddanie produktów spożywczych badaniu z wykorzystaniem promieni X nie wpływa też na ich smak, kolor, konsystencję oraz świeżość. Zwykle maksymalna moc dawki promieniowania RTG w bezpośrednim otoczeniu włączonego systemu inspekcji rentgenowskiej nie przekracza 0,001 mSv / h.
Oznacza to, że operator danego stanowiska obsługujący je przez średnio czterdzieści godzin tygodniowo i pięćdziesiąt tygodni w roku otrzyma dawkę promieniowania 2 mSv rocznie. Dla porównania w ciągu roku średnio każdy człowiek absorbuje dawkę promieniowania o wartości około 2,4 mSv, która pochodzi z różnych źródeł.
Jest to m.in. promieniowanie emitowane w wyniku rozpadu radu, promieniowanie kosmiczne oraz promieniowanie emitowane przez aparaty do wykonywania zdjęć rentgenowskich organów wykorzystywane w medycynie.
Przykłady systemów inspekcji rentgenowskiej. 5
RayScan jest niemieckim producentem urządzeń do inspekcji rentgenowskiej przeznaczonych do stosowania w różnych dziedzinach przemysłu. Firma skupia się na rozwiązaniach pozwalających na badania nowych materiałów i złożonych komponentów, w szczególności wymagających pomiarów o wysokiej dokładności. Przykładowe systemy inspekcyjne wraz z parametrami podano w tabeli.
|
ŚRODKI BEZPIECZEŃSTWA
Ilość promieniowania przenikającego z systemu inspekcji RTG do otoczenia można ograniczyć izolując źródło promieniowania przez zachowanie odpowiednich odstępów ochronnych oraz stosując ekranowanie.
Skuteczność pierwszego sposobu wynika z zależności między natężeniem promieniowania i odległością od jego źródła - to pierwsze maleje przy wzroście tego dystansu. Ze względu na zwykle ograniczone warunki przestrzenne, które należy uwzględnić w projekcie systemu nie w każdym przypadku jest to najefektywniejsze rozwiązanie.
Także przy organizacji stanowiska w ramach danej linii produkcyjnej zapewnienie dużych odstępów od aparatu RTG nie zawsze jest możliwe. Dlatego w systemach tego typu jako podstawowe zabezpieczenie stosuje się ekranowanie. Jego skuteczność zależy od gęstości materiału, z jakiego wykonano ekran - im jest większa, tym lepiej (rys. 5).
Stąd zwykle systemy inspekcji RTG dostępne są w obudowach ze stali nierdzewnej. Dodatkowo wykorzystywane są też pomocnicze zabezpieczenia, takie jak wszelkiego rodzaju blokady, na przykład uniemożliwiające przypadkowe załączenie zasilania urządzenia, wyłączniki bezpieczeństwa oraz oświetlenie ostrzegawcze.
Przykłady systemów inspekcji rentgenowskiej. 6
XC-160 jest przeznaczony do detekcji defektów i zanieczyszczeń (pęcherzy, pęknięć, oceny jakości spawów, wykrywania zniekształceń form, wtrąceń i porowatości) oraz wyznaczania wymiarów przede wszystkim dużych i ciężkich odlewów (o wadze do 60 kg). System pracować może w trybie ręcznym lub półautomatycznym, który polega na automatycznej rejestracji obrazów i ich wizualnej ocenie przez operatora. Główne komponenty systemu to: lampa rentgenowska typu sealed o napięciu 160 kV, maksymalnej mocy ciągłej 640 W, prądzie 0 - 4 mA i rozmiarze wiązki promieniowania 1 mm (według EN 12543) oraz ruchome ramię, na którym umieszczono elementy układu pomiarowego i stolik obrotowy. Dostępne jest też odpowiednie oprogramowanie do przetwarzania oraz prezentacji rejestrowanych obrazów. |
INSPEKCJA RENTGENOWSKA - CZY WARTO?
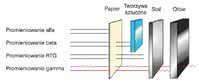
Rys. 5. Skuteczność blokowania różnych rodzajów promieniowania przez ekrany z różnych materiałów
Jedną z głównych zalet systemów inspekcji rentgenowskiej jest ich wielozadaniowość. Poza detekcją ciał obcych można je także wykorzystać m.in. w pomiarach masy i wymiarów detali, wyznaczaniu zawartości tłuszczu w produkcie, zliczaniu detali, monitorowaniu poziomu napełnienia pojemników, sprawdzaniu szczelności ich zamknięć oraz wykrywaniu uszkodzonych opakowań lub innych defektów produktów (pęknięć, ułamań, zgnieceń).
Opisywana metoda pomiarowa nie wymaga ponadto, w przeciwieństwie na przykład do inspekcji optycznej, zapewnienia bezpośredniej widoczności pomiędzy obiektem i detektorem. Dzięki temu można poddać badaniu m.in. produkty paczkowane. W przeciwieństwie zaś do wykrywaczy metali systemy inspekcji promieniami X pozwalają też, oprócz różnych metali, wykryć na przykład zanieczyszczenia szklane, z tworzyw sztucznych, resztki kości, itp.
Zastosowanie inspekcji rentgenowskiej nie jest jednak w każdym z przypadków rozwiązaniem optymalnym. System taki może mieć przykładowo trudność z wykryciem zanieczyszczeń z tektury, włosów, insektów, papieru, chrząstek oraz drewna, co wynika z małej gęstości tych obiektów. Ponadto, w zależności od typu urządzenia, procedury jego programowania i regulacji mogą zniechęcać do zastosowania.
Dodatkowo systemy inspekcji rentgenowskiej są bardzo drogie - liczyć się trzeba z wydatkiem rzędu kilkudziesięciu, a nawet kilkuset tysięcy złotych. Nie zawsze jest to opłacalne. Jeżeli na przykład produkt ma być poddany kontroli pod kątem wyłącznie obecności metalowych ciał obcych, lepiej zainwestować w wykrywacz metali.
Urządzenie takie należy zastosować zwłaszcza, gdy zanieczyszczenia mogą być aluminiowe. Metal ten bowiem ze względu na małą gęstość może zostać niewykryty przez system inspekcji RTG.
Z drugiej strony, jeżeli opakowanie produktu lub jego część są wykonane z aluminium - na przykład jest to metalizowana powłoka lub korytko z folii aluminiowej - wykorzystać można fakt dużej przepuszczalności tego materiału dla promieniowania X. W takim wypadku system inspekcji rentgenowskiej "ignorując" opakowanie umożliwi wykrywanie innych metalowych ciał obcych w danym produkcie, co byłoby niemożliwe w przypadku wykrywaczy metali.
Monika Jaworowska