Podstawowym narzędziem kontroli jakości w wielu gałęziach produkcji są systemy wizyjne. Są to czujniki wizyjne, kamery inteligentne albo połączenie kamery z komputerem. Wybór konfiguracji i konkretnych urządzeń jest obecnie bardzo duży, aby był właściwy, przeanalizować trzeba szereg ich cech. Przedstawiamy to na przykładzie interfejsów komunikacyjnych kamera-komputer oraz kamer inteligentnych.
Standardy przesyłu danych między kamerą a PC porównuje się ze sobą, zestawiając przepustowość, obciążenie procesora, długość kabla łączącego kamerę z komputerem, stopień trudności w realizacji systemu wizyjnego w oparciu na danym interfejsie, możliwość implementacji rozwiązań wymaganych w układach złożonych z kilku kamer (synchronizowania wyzwalania, zarządzania dostępem do łącza) oraz koszty. W ramce porównano wymienione cechy popularnych standardów, tj.: FireWire (IIDC DCAM), Camera Link, GigE Vision oraz USB3 Vision.
A MOŻE KAMERA INTELIGENTNA?
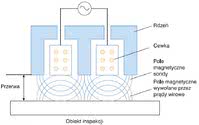
Rys. 1. Sonda do badania jakości prądami wirowymi
Smart camera to połączenie kamery, programowalnej jednostki przetwarzającej obraz i interfejsu komunikacyjnego w jednej obudowie. Żeby móc spełnić swoją funkcję smart camera musi mieć moc obliczeniową odpowiednią do złożoności algorytmów obróbki obrazu, z których korzysta dana aplikacja. Z drugiej strony urządzenie to, które często jest montowane na przykład na ramieniu robota, powinno być małe i lekkie. Mały rozmiar utrudnia jednak odprowadzanie ciepła, co z kolei ogranicza wydajność obliczeniową.
Ważne jest też, aby taka zintegrowana jednostka montowana bezpośrednio przy monitorowanym procesie była odporna na warunki, w których będzie pracować: temperaturę, pyły, wibracje, wodę oraz zaburzenia elektromagnetyczne. Odpowiednio zabezpieczona powinna być nie tylko obudowa kamery, ale i okablowanie, które łączy ją z innymi elementami systemu. Ważne jest również, by proces konfiguracji i programowania smart camery był maksymalnie uproszczony. Te urządzenia stanowią bowiem alternatywę połączenia kamera-komputer właśnie przede wszystkim ze względu na szybkość i łatwość ich uruchomienia.
WYBRANE ALGORYTMY PRZETWARZANIA OBRAZÓW
Nawet korzystając z rozwiązań plug and play, warto znać podstawy narzędzi do obróbki obrazów. To dzięki nim z danych zarejestrowanych w systemie wizyjnym wyodrębniane są te użyteczne w ocenie jakości monitorowanych obiektów.
W oprogramowaniu systemów wizyjnych implementowane są różne algorytmy, m.in. te, których zadaniem jest wykrycie krawędzi. Wykorzystuje się je do detekcji konturów w celu lokalizacji na obrazie detalu jego poszczególnych elementów takich jak na przykład otwory i śruby. Krawędzie wykrywa się, wyszukując takie miejsca, w których sąsiadują ze sobą piksele znacznie różniące się jasnością. Efektywność tej metody zależy od ustalenia właściwej wartości progowej tej różnicy. Jeżeli będzie zbyt mała, nawet niewielkie zmiany jasności zostaną błędnie uznane za kontury. Gdy z kolei wartość progowa będzie za duża, utrudni to detekcję mniej wyraźnych albo małych otworów.
W oprogramowaniu systemów wizyjnych powszechnie wykorzystywany jest również z algorytm rozpoznawania elementów obrazu przez ich porównanie ze wzorcem. Jest to proces dwuetapowy. Najpierw określane są charakterystyczne cechy wzorca, które są zapamiętywane. Z nimi później zestawiane są atrybuty elementów na obrazie.
Na skuteczność tej metody decydujący wpływ ma wybór wzorca. Przykładowo, jeśli ważna jest orientacja poszukiwanej części, powinien on być na tyle asymetryczny, by dało się wyróżnić jego cechy w danym położeniu. Dla pewnych elementów (na przykład otworów) ważne jest także, aby wzorzec obejmował odpowiednio duży fragment otoczenia.
Przykłady systemów do inspekcji wizyjnej i rentgenowskiej
Jednym z nich jest użycie górnoprzepustowego filtru częstotliwości przestrzennych obrazu, który wzmacnia częstotliwości odpowiadające rysom oraz pęknięciom, tłumiąc niższe, występujące w widmie obrazu z powodu jego nierównego oświetlenia. Niestety wzmocnieniu przy okazji ulega tekstura powierzchni, co utrudnia wykrycie skaz. Alternatywą jest zastosowanie na kopii obrazu filtru dolnoprzepustowego. Wynik należy odjąć od oryginału. Rezultatem będzie obraz rys oraz pęknięć na równomiernie oświetlonym tle. Jeszcze inne podejście wymaga wzorca powstałego przez uśrednienie sekwencji obrazów tła bez detalu. który odzwierciedlać będzie rozkład oświetlenia. Właściwe obrazy obiektu są następnie dzielone przez to odniesienie. Wzorcem może być również uśrednienie serii obrazów obiektu inspekcji bez skaz. Wówczas eliminuje się wpływ nie tylko niejednorodności oświetlenia, ale również odblasków na powierzchni detalu.
OD CZEGO ZALEŻY DOKŁADNOŚĆ POMIARÓW WSPÓŁRZĘDNOŚCIOWYCH?Kształt i wymiary produktów kontrolowane są również z wykorzystaniem maszyn współrzędnościowych. Pomiar w tym wypadku polega na określeniu współrzędnych punktów na powierzchni obiektu. Na ich podstawie w specjalnym oprogramowaniu wyznaczane i wymiarowane są figury geometryczne, które składają się na dany detal, oraz odległości między nimi. Współrzędne punktów na obiekcie określa się, wyznaczając współrzędne głowicy pomiarowej w chwili jej zetknięcia z badaną powierzchnią. Sondy maszyn współrzędnościowych zbudowane są z czujników dotykowych lub bezdotykowych. Głowice stykowe dzieli się na impulsowe, na przykład elektostykowe, oraz skaningowe, których częścią są układy sprężyn albo elektroniczne generatory siły nacisku. Sondy bezstykowe to natomiast najczęściej laserowe czujniki triangulacyjne. Na dokładność pomiarów przy użyciu maszyn współrzędnościowych ma wpływ szereg czynników. Można je podzielić na trzy grupy: rodzaj figury, która ma zostać zwymiarowana, specyfikę obiektu, nastawy maszyny i warunki otoczenia. Na przykład średnica zaokrąglonej części detalu jest zwykle wyznaczana z mniejszą dokładnością niż średnica okręgu. Z kolei właściwości obiektu różnie wpływają na precyzję maszyny w zależności od tego, jaki typ głowicy jest używany. Przykładowo, gdy korzysta się z czujnika optycznego, znaczenie ma odblaskowość powierzchni, na którą z kolei ma wpływ sposób jej wykończenia albo kolor. Dokładność pomiaru przy użyciu głowicy dotykowej jest natomiast mniejsza, jeśli detal pod jej naciskiem ulega deformacji. Może to wynikać z właściwości obiektu inspekcji i niedostosowania do nich siły, z jaką sonda jest przykładana do powierzchni detalu. Spośród czynników zewnętrznych najdokuczliwsza jest temperatura. Pod wpływem jej wahań zmieniać się może długość obiektów, zwłaszcza tych wykonanych z tworzyw sztucznych. Gdy współczynnik rozszerzalności temperaturowej tych ostatnich oraz skali maszyny współrzędnościowej się nie różnią - co jest rzadkością - wydłużenia te wzajemnie się kompensują. W przeciwnym wypadku, jeżeli wahania temperatury w otoczeniu stanowiska pomiarowego są spodziewane, wybrać należy maszynę, w której zastosowano korekcję temperaturową. Warto także próbować ograniczyć wpływ otoczenia, m.in. chroniąc stanowisko pomiarowe przed ciągami powietrza oraz bezpośrednim naświetleniem i zapewniając odpowiedni dystans między nim a ścianami lub innymi źródłami ciepła.
|