JAK WYZNACZYĆ KONTURY DETALU?
Łatwo to uzyskać przy obiektach płaskich, trudniej natomiast przy zakrzywionych. Przykładem takich są łopatki turbin wiatrowych. Detale takie można albo skanować etapowo, jeżeli uda się wyróżnić kilka ścieżek o prostych kształtach, albo zastosować metodę pozwalającą na przemieszczanie sond po ich wypukłościach. Drugie rozwiązanie jest lepsze, ponieważ zapewnia pełne pokrycie skanowanej powierzchni oraz powtarzalność inspekcji. Jest jednak dużo trudniejsze w realizacji.
Warunkiem koniecznym jest znajomość modelu 3D obiektu badania oraz jego odniesienie do osi współrzędnych skanera. Innym sposobem jest pozyskanie informacji o kształcie, orientacji oraz położeniu detalu przy użyciu samego urządzenia do inspekcji. Wykorzystuje się wówczas fakt, że amplituda fali odbitej osiąga maksymalną wartość wtedy, kiedy fala pada na badaną powierzchnię pod kątem prostym. Trójwymiarowy model obiektu można zatem uzyskać, poznając kolejne kąty nachylenie głowicy, przy których amplituda fali odbitej jest największa. Odległość dzielącą sondę od detalu wyznacza się natomiast, znając czas odbioru sygnału odbitego. Na bazie tych informacji wyznaczana jest trajektoria skanera.
W inspekcji jakości zastosowanie znajduje również zjawisko indukcji elektromagnetycznej. Jest ono podstawą metody prądów wirowych (rys. 1). W ramce podsumowujemy jej wady i zalety.
Badanie jakości prądami wirowymiZalety:
Wady:
|
CO WPŁYWA NA SKUTECZNOŚĆ KONTROLI PRĄDAMI WIROWYMI?
Cewki sondy pomiarowej zasilane prądem przemiennym generują zmienne pole magnetyczne. Po zbliżeniu ich do detalu wykonanego z materiału przewodzącego prąd powstają w nim prądy wirowe. Te generują własne pole magnetyczne, które oddziałuje na cewkę sondy. Zmiany grubości lub defekty w obiekcie zmieniają amplitudę i rozpływ prądów wirowych, a w efekcie wpływają na rozkład pola oraz prądy w cewkach sondy. Gęstość prądów wirowych jest największa na wierzchu detalu, w tym obszarze zatem uzyskiwana jest największa rozdzielczość pomiarowa. Przyjmuje się, że głębokość penetracji tej metody odpowiada odległości od brzegu obiektu, na której gęstość prądów wirowych wynosi około 40% tej wartości na jego powierzchni.
Na efektywność kontroli jakości prądami wirowymi ma wpływ kilka czynników. Na przykład im większa jest przewodność elektryczna materiału, tym skutecznej można wykryć defekty na jego powierzchni, ale równocześnie głębokość inspekcji będzie mniejsza. Analogiczny wpływ ma też większa częstotliwość testowa, natomiast im jest ona mniejsza, tym łatwiej wykryć skazy znajdujące się w głębi obiektu inspekcji. Im większe są cewki sondy pomiarowej, tym większą objętość detalu można skontrolować, te mniejsze z kolei dokładniej wykrywają drobne defekty.
O ile na cechy materiału operator systemu nie ma wpływu, to częstotliwość testowa, rodzaj oraz rozmiary cewki powinny być dobrane do specyfiki obiektu badania. Dlatego, aby zapewnić jak największą rozdzielczość oraz wymaganą głębokość penetracji, w urządzeniach stosowanych w przemyśle można przestrajać częstotliwości i korzystać z sond różnego typu.
Spektroskopia ramanowska kontroluje jakość leków i demaskuje podróbki
Stosuje się różne techniki rozpoznawania fałszywych leków. Przykładem są testery wykrywające podróbki konkretnych medykamentów. Badanie polega w tym wypadku na zmieszaniu próbki lekarstwa ze specjalną substancją chemiczna i obserwacji zmiany jej koloru. Alternatywą, bardziej uniwersalną i nieniszczącą, jest spektroskopia ramanowska. Do jej zalet zalicza się również możliwość pomiaru lekarstw w opakowaniach szklanych, plastikowych i kapsułkach żelowych. W metodzie tej próbkę naświetla się monochromatycznym światłem (laserem), a potem obserwuje widmo promieniowania przez nią rozproszonego. Pojawienie się w nim składowych o określonych częstotliwościach świadczy o występowaniu w obiekcie badań konkretnych związków. Demaskowanie fałszywych leków to nie jedyne zastosowanie spektroskopii ramanowskiej w farmacji. Ta metoda jest również wykorzystywana w kontroli jakości w zakładach produkujących leki. Przykładowe jej zastosowanie to kontrola rozkładu substancji w tabletce, ważna zwłaszcza w przypadku lekarstw, które są dawkowane przez podział na części. Na zdjęciu obraz ramanowski zarejestrowany w systemie StreamLine Plus firmy Renishaw przedstawiający rozkład i rozmiar poszczególnych składników leku przeciwbólowego (czerwony - kofeina, zielony - aspiryna, niebieski - paracetamol). |
PROMIENIE X POZWALAJĄ ZAJRZEĆ DO ŚRODKA
Promieniowanie rentgenowskie to promieniowanie elektromagnetyczne o długości fali od kilku pm do 10 nm. W kontroli jakości wykorzystuje się jego zdolność do przenikania materiałów, które są nieprzezroczyste dla światła widzialnego. Stopień przepuszczalności zależy od gęstości detalu - im jest ona większa, tym mniej promieni przez niego przenika. Dzięki temu na obrazie rentgenowskim rozróżnialne są elementy o różnej gęstości - na przykład zanieczyszczenia. Stanowisko do badania jakości z wykorzystaniem promieni X składa się z ich źródła i detektora, między którymi znajduje się obiekt inspekcji.
Tym pierwszy są lampy rentgenowskie w postaci szklanej banki próżniowej, w której umieszcza się dwie elektrody: katodę i anodę połączone ze źródłem wysokiego napięcia. Katoda w postaci włókna wolframowego zasilanego z drugiego źródła niższego napięcia żarzy się i emituje elektrony. Cząstki te, przyspieszane w polu elektrycznym między elektrodami, bombardują anodę. W chwili zderzenia z nią emitują promieniowanie X.
Detektor promieniowania rentgenowskiego składa się natomiast ze wzmacniacza obrazu i kamery. Pierwszy element pochłania promienie X i przetwarza je na światło widzialne rejestrowane przez kamerę. W ten sposób powstaje monochromatyczny obraz obiektu. Odcienie szarości odpowiadają na nim konkretnym poziomom natężenia promieniowania RTG odebranego w detektorze.
Inspekcja rentgenowska wykrywa wadliwe akumulatory
|
CZY INSPEKCJA RENTGENOWSKA JEST BEZPIECZNA?
Kontrola jakości przy użyciu promieni RTG znajduje zastosowanie w różnych gałęziach przemysłu, na przykład w branży spożywczej. Informacja o tym może budzić pewne obawy klientów o wpływ promieniowania na obiekt inspekcji. Kontrowersyjne jest również jego oddziaływanie na zdrowie obsługi systemów tego typu.
Jak jednak zbadała Światowa Organizacja Zdrowie, wystawienie żywności nawet na duże, ale krótkotrwałe promieniowanie, nie powoduje jej skażenia ani utraty wartości odżywczych. Dawka promieniowania, jaka jest absorbowana w czasie naświetlania trwającego zwykle ledwie kilkaset milisekund, wynosi około ułamka mSv. Poddanie produktów spożywczych takiemu badaniu nie wpływa również na ich smak, kolor, konsystencję ani świeżość.
Zwykle maksymalna dawka promieniowania RTG w bezpośrednim otoczeniu włączonego systemu inspekcji rentgenowskiej nie przekracza 0,001 mSv. Oznacza to, że operator danego stanowiska obsługujący je przez średnio czterdzieści godzin tygodniowo i pięćdziesiąt tygodni w roku otrzyma dawkę promieniowania 2 mSv rocznie. Dla porównania w ciągu roku średnio każdy człowiek absorbuje dawkę promieniowania o wartości około 2,4 mSv, która pochodzi z różnych jego źródeł w naszym otoczeniu (m.in. z kosmosu, rozpadu radu, medycznych aparatów RTG).
Przykłady systemów do inspekcji wizyjnej i rentgenowskiej
Przykładowo, w produkcji sera, można wyróżnić następujące zagrożenia: wystąpienie antybiotyków w mleku, przeżycie pasteryzacji przez mikroflorę chorobotwórczą, jej wzrost i rozwój oraz obecność kawałków metalu w produkcie końcowym. Aby im zapobiec: surowiec (mleko) z każdej cysterny dostarczającej go do zakładu bada się pod kątem obecności antybiotyków, monitoruje się temperaturę pasteryzacji oraz temperaturę w dojrzewalniach, a każde opakowanie z serem poddaje się kontroli na obecność metali przy użyciu wykrywacza metali. |
HEL SPRAWDZA SIĘ NAJLEPIEJ
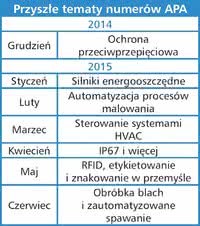
Przyszłe tematy numerów APA
W ostatniej metodzie obiekt kontroli wypełniony specjalnym gazem umieszcza się w komorze próżniowej. Stężenie medium znakującego jest mierzone przy użyciu spektrometru masowego, który zapewnia dużą czułość pomiaru i przede wszystkim, inaczej niż w metodzie "bąbelkowej", pozwala ilościowo określić ubytek gazu. Oprócz tego do zalet tej metody zalicza się: krótki czas inspekcji rzędu kilku sekund, który, co ważne, zazwyczaj nie rośnie znacząco wraz ze zwiększeniem objętości detalu, niezależność od temperatury i łatwość automatyzacji. Z drugiej strony, chociaż gazy znakujące są tanie, to sam sprzęt pomiarowy jest drogi, wymaga też kalibracji i zwykle specjalnego czyszczenia.
Gazem znakującym może być hel lub wodór. Preferowany jest zwłaszcza ten pierwszy ze względu na jego liczne zalety. Jest on przede wszystkim nietoksyczny, niepalny oraz nie tworzy mieszanin wybuchowych. Jest to gaz obojętny, czyli nie reaguje z innymi substancjami i nie ma wpływu na właściwości powierzchni, z którymi ma kontakt. Można go używać w szerokim zakresie temperatur oraz ciśnień. Ponadto w powietrzu występuje w minimalnej ilości, która nie wpływa na dokładność pomiaru. Ze względu na mały rozmiar cząstki hel pozwala na wykrycie nieszczelności o bardzo małych rozmiarach. Jest też stosunkowo tani.
Monika Jaworowska