Systemy wizyjne są wykorzystywane w sterowaniu robotami pakującymi. W obrębie automatycznych linii technologicznych (nie tylko pakowania) są ponadto używane w kontroli jakości. Monitorują różne właściwości produktów - na przykład kolor, kształt i rozmiary, a w procesie pakowania również m.in. dokładność zamknięcia opakowania, na przykład nakrętki na butelce lub zgrzewu folii, kompletność wypełnienia blistrów, poprawność treści nadruku na etykiecie oraz jej umieszczenia na pudełku.
Zalety systemów wizyjnych to przede wszystkim: szybkość i dokładność inspekcji oraz brak bezpośredniego kontaktu z produktem. Nieinwazyjność tej metody jest ważna zwłaszcza w branży spożywczej. Niestety czasem zdarza się, że system wizyjny przepuszcza uszkodzone produkty, natomiast te zapakowane poprawnie uznaje za wybrakowane. Są to symptomy awarii, której przyczyny mogą mieć charakter mechaniczny, elektryczny albo optyczny. Źródłem problemów bywa nawet sam obiekt inspekcji. Dalej podpowiadamy, jak wykryć oraz zaradzić usterkom systemów wizyjnych.
"UTRZYMANIE RUCHU" SYSTEMÓW WIZYJNYCH
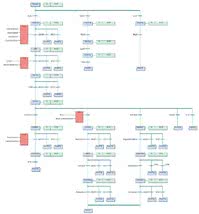
Rys. 1. Uproszczony diagram stanów PackML zapisany w języku SFC
Sprawność PackML - dlaczego warto?
- ułatwiona integracja maszyn w obrębie linii pakowania dzięki: modułowości sprzętowej (plug and play), standardowym danym wejściowym i wyjściowym (sprawna komunikacja),
- ujednolicone środowisko programowe dla operatorów,
- uproszczone specyfikacje maszyn,
- szybszy rozwój oprogramowania i łatwiejsze jego testowanie,
- komponenty sprzętowe i programowe wielokrotnego użytku to tańsza budowa (tzn. niższa cena), eksploatacja oraz konserwacja maszyn,
- producenci mogą się skupić na rozwoju funkcjonalności, która wyróżni ich urządzenie na tle konkurencji, zamiast tracić czas na implementację jego podstawowych funkcji.
PRZECZYTAJ, ZANIM OZNAKUJESZ TAGIEM RFID!
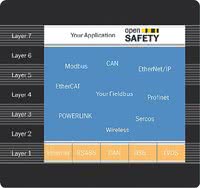
Rys. 2. Główną zaletą openSAFETY jest niezależność od platformy komunikacyjnej (protokołu i medium transmisyjnego)
Do identyfikacji oraz śledzenia przepływu produktów w branży opakowaniowej (i nie tylko) coraz częściej zamiast kodów kreskowych używa się znaczników RFID (Radio Frequency Identification). Są one zbudowane z układu scalonego, w pamięci którego zapisane są informacje o produkcie oznakowanym w ten sposób oraz anteny do komunikacji z czytnikiem. Znaczniki RFID dzieli się na aktywne oraz pasywne.
Te drugie energię zasilającą czerpią z sygnału z czytnika, natomiast tagi aktywne wyposażone są w baterię. Znaczniki RFID klasyfikuje się również ze względu na częstotliwość pracy, m.in. HF (13,56 MHz), UHF (433 MHz, 860-960 MHz) i w paśmie mikrofalowym. Tagi UHF można odczytywać z większej odległości, dlatego to najczęściej nimi znakowane są pojemniki zbiorcze oraz palety. W zakresie oznaczania pojedynczych produktów rywalizują one głównie ze znacznikami HF.
Ponieważ tagi RFID działają w paśmie radiowym, na możliwość ich odczytu wpływ mają różne czynniki, m.in. stała dielektryczna materiału opakowania, produktu lub powietrza. Zależy od niej częstotliwość pola elektromagnetycznego. Tworzywa sztuczne zmniejszają ją nawet o od 40% do 50%, szkło jeszcze bardziej, a woda nawet aż dziewięciokrotnie (proporcjonalnie do jej zawartości).
W rezultacie znacznik dostrojony do pasma 915 MHz będzie działał na znacznie niższej częstotliwości, w szkle i w wodzie odpowiednio 800 MHz i nawet 100 MHz. Inne problemy to: tłumienie pola elektromagnetycznego (na przykład przez wodę) lub zmiana impedancji anteny (przykładowo przez metal) powodująca niedopasowanie między nią a układem scalonym znacznika.
Chociaż nie jest przesądzone, że
Rys. 3. Diagram stanów PackML