Wózki samojezdne (Automated Guided Vehicles, AGV) to bezzałogowe pojazdy wyposażone w napęd elektryczny. Są zasilane z akumulatorów. Wykorzystuje się je do transportu ładunków w obrębie zakładów przemysłowych, magazynów i między nimi. Mają przeważnie ładowność od kilku kilogramów do kilkuset ton.
AGV są użytkowane od lat 50. zeszłego wieku. Postęp techniki sprawia, że są sukcesywnie ulepszane. Obecnie celem jest przede wszystkim rozwijanie nowych metod nawigacji wózków samojezdnych tak, aby nie były zdolne wyłącznie do jazdy z punktu A do punktu B, podążając narzuconą trasą, lecz aby były w stanie samodzielnie wytyczyć swoją ścieżkę ruchu i w razie potrzeby mogły ją samodzielnie modyfikować odpowiednio do zmian zachodzących w ich otoczeniu.
PRZEGLĄD METOD NAWIGACJI AGV
Tradycyjne wózki samojezdne poruszają się po z góry określonych trasach, które zostały zoptymalizowane pod kątem jak najefektywniejszego przepływu ładunków, które przewożą. Realizuje się to różnymi metodami. Ich cechą wspólną jest to, że na terenie, po którym pojazd się porusza, umieszczane są znaczniki, które AGV rozpoznaje.
Przeważnie wymaga to ingerencji, mniej lub bardziej inwazyjnej, w elementy konstrukcyjne zakładu, to zaś ma wpływ na łatwość zmiany ścieżki. W przypadku niektórych metod jest to bardziej pracochłonne i kosztowne niż w innych, lecz generalnie stanowi utrudnienie, jeżeli przestrzeń produkcyjną trzeba przeorganizować.
Najpopularniejsze metody tego typu to: pętli indukcyjnej, pętli magnetycznej, optyczna i laserowa. W pierwszej z nich pod podłogą umieszcza się kabel. Na skutek przepływu prądu elektrycznego dookoła przewodu wytwarzane jest pole magnetyczne. Wózek wyposażony jest z kolei w układ odbiorczy, który mierzy jego natężenie. Sterownik koryguje kierunek, w jakim AGV się porusza, tak aby wartość ta była cały czas jak największa.
W metodzie pętli magnetycznej wykorzystuje się namagnesowaną taśmę, którą nakleja się na podłodze. Ścieżkę, po której powinien poruszać się wózek, można również namalować, zaś jej przebieg śledzić przy użyciu kamery na pokładzie AGV. Chociaż w porównaniu do metody pętli indukcyjnej techniki pętli magnetycznej oraz optyczna są mniej inwazyjne i tańsze w realizacji, to znaczniki wytyczające trasę, którą podąża wózek, nie są zbyt trwałe. W związku z tym wymagają okresowego odnawiania.
W metodzie laserowej z kolei wózek wyposaża się w skaner laserowy montowany na jego wieży, zaś znaczniki mocuje się na ścianach budynku. Powinny być one umieszczone na jednakowej wysokości i cały czas znajdować się w zasięgu skanera.
Roboty w paletyzacji worków
Jeżeli chodzi o podnoszenie worków przez personel, to jest uciążliwe przede wszystkim dlatego, że zwykle w opakowaniu tym umieszczane są produkty o konsystencji sypkiej, które nie zawsze są w nich rozłożone równomiernie i przeważnie są ciężkie. Przykładem są pakowane w worki materiały budowlane, jak cement czy kleje. Poza tym, że podnoszenie nieporęcznych ciężarów spowodować może urazy, na przykład uszkodzenie kręgosłupa, zadanie to ręcznie wykonywane jest dość wolno i nietrudno jest przy tym o uszkodzenie worka oraz rozsypanie jego zawartości. Do operowania zaokrąglonymi, odkształcającymi się oraz mogącymi się rozrywać przy kontakcie z ostrymi krawędziami obiektami, nie są również zwykle przystosowane tradycyjne linie paletyzacji. Dlatego chętnie w tym celu używa się robotów przemysłowych. Automatyzacja tego zadania przy użyciu tych maszyn jest stosunkowo prosta, a nawet łatwiejsza do zrealizowania niż na przykład układanie w stosy skrzynek. Wynika to stąd, że w przypadku worków, choć oczywiście wszystko zależy od właściwości produktu w nie zapakowanego, prawdopodobieństwo uszkodzenia w wyniku uderzenia o podłoże albo kolizji generalnie jest mniejsze. Jak są zbudowane chwytaki widłowe? Dzięki temu robot może po prostu postawić / położyć worek, zamiast podążać skomplikowaną trajektorią, którą zaplanowano w taki sposób, by nie zniszczyć skrzynek przy ich układaniu jedna na drugiej lub w wyniku ich zderzenia z innymi obiektami, na przykład elementami konstrukcyjnymi linii produkcyjnej. Prostszy tor ruchu ułatwia programowanie robota i skraca czas paletyzacji. Na to ostatnie ma także wpływ fakt, że worki nie wymagają zazwyczaj układania przekładek pomiędzy ich kolejnymi warstwami. Do zrobotyzowania tego zadania zachęcać może dodatkowo fakt, że dostępne są końcówki robocze zaprojektowane pod kątem jego wykonywania. Chwytaki widłowe zbudowane są z dwóch ramion z zębami przypominającymi zakończenie grabi. Ich rozstawienie można zmieniać, dostosowując je do różnych rozmiarów worków. W celu ich podniesienia chwytaki rozchylają się, wsuwają się pod nie, a następnie się na nich zaciskają. Zadanie to jest łatwiejsze do realizacji, gdy worki transportowane są na przenośnikach rolkowych, gdyż zęby chwytaka wsuwając się pod worek, mogą zagłębić się w przerwy pomiędzy wałkami transportera. Chwytaki widłowe charakteryzuje niezawodność i duża szybkość pracy. |
WÓZKI AUTONOMICZNE
Wymienione metody są obecnie uzupełniane o rozwiązania, które zwiększają autonomię wózków samojezdnych. W tym celu wyposaża się je w różnego typu czujniki. Nieodzownym elementem systemów nawigacji, dzięki którym mogą się przemieszczać po dowolnie wybranej ścieżce, niewytyczonej wcześniej na trwale, jest też oprogramowanie, które przetwarza dane z sensorów.
Nowe techniki nawigacji AGV można zasadniczo podzielić na trzy grupy. Korzysta się w nich z: laserów, kamer oraz laserów i kamer stereo. Poza tą klasyfikacją producenci wprowadzają także własne modyfikacje.
Najpopularniejszą metodą jest aktualnie nawigacja konturowa. W jej przypadku, żeby "nauczyć się" poruszania po terenie danego zakładu, wózek wykonuje próbny przejazd, podczas którego wysyłając impulsy laserowe, skanuje otoczenie na określonej wysokości w zakresie od kilku do kilkudziesięciu centymetrów nad podłogą.
Po trafieniu promienia w obiekt stanowiący dla AGV potencjalną przeszkodę, którą powinien omijać, światło odbite jest wykrywane przez detektor w pojeździe. Informacja o tym zostaje przetworzona w specjalnym oprogramowaniu. Algorytmy, które w nim zaimplementowano wykrywają wolną przestrzeń.
Na tej podstawie, po przeskanowaniu przez wózek całego terenu i powrocie do punktu wyjścia, powstaje mapa pustych korytarzy. Podążanie wyznaczonymi na niej szlakami, przy wsparciu pokładowego systemu detekcji kolizji, gwarantuje bezpieczną jazdę. W razie przeorganizowania przestrzeni w zakładzie wystarczy powtórzyć przejazd próbny, aby mapę zaktualizować.
PRZYSZŁOŚĆ AGV
Na podobnej zasadzie działa nawigacja z wykorzystaniem technologii LIDAR (Light Detection and Ranging). W przypadku trzeciej z wymienionych technik przykładowa realizacja może polegać na umieszczeniu na wieży pojazdu kilku kamer stereo. Powinno się je rozmieścić w taki sposób, aby rejestrowały obraz dookoła wózka. Dane pozyskane w ten sposób służą do stworzenia mapy, na której zaznaczone są obiekty znajdujące się na trasie przejazdu pojazdu.
Autonomiczne AGV są we wczesnym stadium rozwoju. Dlatego występują w ich przypadku problemy w tak ważnych kwestiach, jak: przepustowość transportu, powtarzalność ruchu, jego precyzja oraz koordynacja floty wielu takich pojazdów.
Na tych właśnie kwestiach skupiają się obecnie projektanci tych pojazdów. Przewiduje się, że jeżeli zostaną one rozwiązane, to liczne korzyści, jakie zapewniają wózki autonomiczne (m.in. skalowalność, elastyczność, szybkość instalacji), sprawią, że za około 10 lat ich rynek będzie wart przynajmniej tyle, na ile obecnie wyceniany jest rynek tradycyjnie nawigowanych AGV.
WÓZKI WIDŁOWE STANOWIĄ ZAGROŻENIE
W transporcie wewnętrznym korzysta się też z wózków widłowych kierowanych przez operatorów. Ważnym aspektem ich użytkowania jest bezpieczeństwo. Aby ani kierowcy, ani pozostały personel zakładu nie ucierpieli w wypadkach z udziałem tych pojazdów, trzeba przestrzegać kilku zasad.
Niektóre wydają się oczywiste, jednak warto o nich przypomnieć, ponieważ wciąż dochodzi do incydentów, w których ceną za ich nieprzestrzeganie jest ludzkie zdrowie lub życie. Na przykład amerykańska agencja OSHA (Occupational Safety and Health Administration) szacuje, że co roku w Stanach Zjednoczonych ma miejsce 35 tys. zdarzeń z udziałem wózków widłowych, których uczestnicy doznają poważnych obrażeń oraz ponad 60 tys. incydentów o lżejszych skutkach. Corocznie przydarzają się też niestety wypadki śmiertelne. Na przykład w 2015 roku w takich okolicznościach zginęło 96 amerykańskich pracowników.
Pierwszym warunkiem, który trzeba bezwzględnie spełnić, jest dopuszczenie do kierowania wózkami widłowymi wyłącznie osób, które zostały w tym kierunku przeszkolone i posiadają wymagane uprawnienia. Na szkoleniach często omawia się różnice między tymi pojazdami a samochodami osobowymi. Chociaż pod pewnymi względami są podobne, różnice są zasadnicze, dlatego powinno się je uświadomić kandydatom na operatorów wózków posiadającym "zwykłe" prawo jazdy.
Najważniejsze z nich to: otwarta konstrukcja, przez co kabina nie ochrania kierowcy, prędkość poruszania się poniżej 8 m/s, czyli zbliżona do tempa marszu, trzypunktowe zawieszenie, tendencja do przechylania się bez, jak i z obciążeniem, łatwość utraty stabilności oraz mniejszy promień skrętu, który ułatwia wykonanie tego manewru w ciasnej przestrzeni. Na szkoleniach porusza się także zagadnienia, które można podzielić na kilka kategorii, w tym dotyczące: przygotowania do jazdy, jej przebiegu i ładunku.
JAK BEZPIECZNIE KORZYSTAĆ Z WÓZKÓW WIDŁOWYCH?
Do pierwszej zalicza się m.in. kwestię odzieży. Kierowcy i reszta załogi powinni być bowiem odpowiednio ubrani. Ważne elementy ich stroju to: kask, buty robocze i ubranie, dzięki któremu będą dobrze widoczni. Nie wolno obsługiwać tych pojazdów brudnymi rękoma, na przykład pokrytymi smarem, które mogłyby się przez to ześlizgnąć z elementów sterowania.
Przed uruchomieniem kierowca powinien sprawdzić stan techniczny pojazdu. Nie wolno mu też prowadzić bez zapiętych pasów, a przed włączeniem wózka musi mieć pewność, że pewnie siedzi w kabinie, a żadna część jego ciała nie znajduje się poza nią.
W czasie jazdy trzeba przestrzegać znaków, zwłaszcza z informacją o maksymalnych wartościach obciążenia podłoża i wysokości pojazdu. Nie wolno przekraczać dopuszczalnej prędkości. Trzeba omijać nierówności, śliskie powierzchnie i obiekty, które mogą spowodować utratę kontroli nad pojazdem albo przemieszczenie się ładunku, na przykład drewniane klocki porozrzucane po podłodze. Nie powinno się gwałtownie ruszać, hamować ani skręcać. Niedopuszczalne jest również wysiadanie na chwilę z wózka bez wcześniejszego zatrzymywania go, a później wskakiwanie do niego w biegu.
ZASADY BEZPIECZEŃSTWA
Należy zachować bezpieczną odległość od innych wózków, a hamując, upewnić się, że wystarczy miejsca do bezpiecznego zakończenia tego manewru, zaś na zakrętach zwalniać, żeby uniknąć przewrócenia się. Operator powinien dobrze orientować się w przestrzeni, po której się porusza, jeśli ładunek ogranicza mu widoczność oraz używać klaksonu w razie potrzeby, na przykład wyjeżdżając zza rogu. Znajdując się na rampie, nie może załadowywać wózka, rozładowywać go ani skręcać.
Przed podniesieniem ładunku trzeba sprawdzić, czy nie jest uszkodzony, a jego wymiary pozwalają na bezpieczny transport. Nie należy go przesuwać ani podnosić końcówką wideł. Nie wolno go też podnosić ani przesuwać, jeśli nie obciąża równomiernie obu ramion wideł, ani podnosić na jednym ramieniu. Warto się też zastanowić, czy pozycja, która jest wygodna przy jego unoszeniu, będzie też taka przy jego odkładaniu w miejscu docelowym.
Trzeba pamiętać, że wózek widłowy nie służy do transportu (czy raczej podwożenia) ludzi. Nikt nie powinien znajdować się pod uniesionym ładunkiem. Przebywając w pobliżu masztu, należy uważać, żeby ręka albo noga nie zostały przycięte.
Więcej informacji można znaleźć w odpowiednich normach. W ramce natomiast przedstawiamy przykład zdarzenia, do którego doszło przez nieprzestrzeganie fundamentalnych zasad bezpiecznego użytkowania wózków widłowych.
WYZWANIA PAKOWANIA
Między poszczególnymi etapami produkcji i transportu produkty umieszcza się w opakowaniach, najpierw jednostkowych, na przykład butelkując napoje, a potem zbiorczych. Przykładem są skrzynki, w które pakuje się kartony z sokiem. Opakowanie pełni wieloraką funkcję.
Jednym z jego zadań jest ochrona zawartości przed uszkodzeniem na skutek zewnętrznych oddziaływań podczas transportu oraz magazynowania. Nienaruszone opakowanie ma też, w przypadku produktów do użytku osobistego, gwarantować, że nikt z nich wcześniej przed kupującym nie korzystał. Poza tym pełni funkcję informacyjną - na opakowaniu umieszczane są najważniejsze dane, które mogą zainteresować kupującego, i informacje wymuszone przepisami. Powinno być również atrakcyjne wizualnie, żeby zachęcić do zakupu.
Celem projektantów opakowań jest zatem osiągnięcie kompromisu pomiędzy ich funkcjonalnością a wyglądem. Utrudnia to coraz silniejsza konkurencja, która sprawia, że samo opakowanie staje się wyróżnikiem produktu, który powinien nadążać za trendami kształtowanymi przez zmieniające się gusta kupujących. Trzeba również pamiętać, że kupujemy coraz więcej.
Dla producentów maszyn pakujących wszystko to razem oznacza jedno - urządzenia, które projektują, muszą spełniać coraz bardziej wyśrubowane wymogi w zakresie zarówno wydajności pakowania, jak i łatwości ich przestawiania na inny model opakowania. Ich klienci bowiem nie są skłonni do zakupu nowej pakowarki za każdym razem, kiedy zamierzają coś zmienić w sposobie pakowania swoich produktów (format, sposób zamknięcia, szatę graficzną). Taką elastyczność zapewnia modułowość konstrukcji maszyn pakujących. Ma ona również wiele innych zalet.
Wypadek w tartaku
Feralnego dnia pracownika oddelegowano do wsparcia zespołu, któremu zlecono realizację specjalnego zamówienia. Pomagał on w cięciu drewna, a za każdym razem kiedy gotowa była kolejna partia desek, jego zadaniem było ich wywiezienie wózkiem widłowym na zewnątrz hali produkcyjnej. Groźna niefrasobliwość Po ułożeniu pierwszej partii, przyjeżdżając na miejsc jej składowania z kolejnym ładunkiem, kierowca wysiadł z wózka, aby między kolejnymi warstwami desek ułożyć przekładkę. Opuścił on pojazd, nie wyłączając go, w takim pośpiechu, że nawet nie zauważył, że nie zaparkował go poprawnie. Nie opuścił też w dół wideł z ładunkiem. Następnie, nie spodziewając się niczego złego, kierowca stanął pomiędzy stosem desek a w pełni załadowanym wózkiem. Kiedy schylił się, aby umieścić przekładkę, pojazd ruszył, zakleszczając kierowcę między deskami na stosie a tymi na widłach. Poszkodowany nie był w stanie krzyczeć, tymczasem ucisk się zwiększał. Na szczęście na plac akurat wtedy przyjechała ciężarówka. Prowadzący ją zdziwił się widząc pozostawiony bez opieki wózek widłowy, z wysokości swojej kabiny nie był bowiem w stanie dostrzec uwięzionego pracownika. Ponieważ była to niecodzienna sytuacja, nie odjechał, aby kontynuować swoje zadania, lecz podjechał bliżej i wówczas zauważył poszkodowanego. Natychmiast opuścił swój pojazd i ruszył na ratunek. Chociaż pechowy, a raczej nieostrożny, kierowca nie miał żadnych widocznych obrażeń, to został przewieziony do szpitala. Dokładne badania wykazały, że na skutek wypadku doznał złamania żeber i miał uszkodzone płuca. Wnioski Jak wykazało dochodzenie przeprowadzone po tym incydencie, pojazd był całkowicie sprawny. W związku z tym z tego wypadku wyciągnięto następujące wnioski: jeśli kierowca wysiada z wózka powinien obniżyć widły z ładunkiem zawsze musi wyłączać pojazd, jeżeli zamierza z niego wysiąść bez względu na to, jak krótko planuje poza nim przebywać, musi zaciągnąć hamulec, a pracownicy powinni zawsze się wzajemnie pilnować. |
ZALETY MODUŁOWOŚCI
Ogólnie, jeśli chodzi o sprzęt produkcyjny, modułowość wydaje się obecnie cechą konieczną. W praktyce oznacza to, że składa się on z komponentów, które można, tak jak klocki, zestawić ze sobą w różnych konfiguracjach, zmieniając funkcjonalność lub parametry pracy maszyny w zależności od bieżących potrzeb produkcji. Trend ten dotyczy także maszyn pakujących. I choć realizacja systemu modułowego może być trudniejsza niż tego o wąskiej funkcjonalności, poniesiony na początku trud jest rekompensowany przez zalety tego pierwszego. Dalej wymieniamy najważniejsze z nich.
Modułowe maszyny pakujące m.in. pozwalają w pełni wykorzystać dostępną przestrzeń zakładu. Jest to szczególnie odczuwalne wtedy, kiedy jest ograniczona. Przykładem jest sytuacja, w której linia pakowania składająca się z modułów ustawionych w linii nie mieści się i przestawia się je w taki sposób, żeby jej poszczególne komponenty utworzyły kształt litery L. Efektywne wykorzystanie dostępnej przestrzeni pozwala uniknąć kosztownej rozbudowy albo przebudowy zakładu. Ma to też wpływ na komfort, wydajność oraz bezpieczeństwo pracowników.
Kolejną zaletą jest łatwiejsza integracja różnych operacji. Wybierając modułową maszynę pakującą, zyskujemy również dwa w jednym - z jednej strony korzystamy ze zestandaryzowanych modułów, a równocześnie możemy je bardzo łatwo dostosować do swoich unikalnych potrzeb. Dzięki temu zyskujemy na zaletach obu tych rozwiązań.
To pierwsze zapewnia nam wszystkie korzyści, które uzyskujemy, kupując urządzenia produkowane na masową skalę, czyli m.in. konkurencyjną cenę oraz łatwość naprawy lub wymiany. Jednocześnie maszyna pakująca spełnia specyficzne wymagania, tak jakby została zaprojektowana na specjalne zamówienie.
MASZYNY PAKUJĄCE - PRZYSZŁOŚĆ 4.0
Rynku maszyn pakujących nie ominą z pewnością zmiany, jakie nadciągają wraz z rozwojem Industry 4.0. Przewiduje się, że w tym segmencie rację bytu znajdzie kilka rozwiązań, które według prognoz mają zmienić w nadchodzących latach oblicze przemysłu.
Jednym z nich jest Przemysłowy Internet Rzeczy (Industrial Internet of Things, IIoT). Przykłady zastosowań IIoT, w którym urządzenia będą korzystać z Internetu bez udziału ludzi, można mnożyć. Za jego pośrednictwem maszyny, nie tylko lokalnie w obrębie zakładu, ale i między fabrykami, będą się mogły wymieniać danymi konfiguracyjnymi, będą wysyłać e-maile ze zgłoszeniem naprawy albo sprawdzać w magazynie dostępność danej części zamiennej i ją zamawiać.
Przewiduje się również, że dzięki tak ogromnej liczbie węzłów sieci, które będą komunikować się autonomicznie nie tylko z Internetem, ale i za jego pośrednictwem między sobą, tradycyjne systemy sterowania o architekturze scentralizowanej i hierarchicznej będą zastępowane przez te rozproszone i płaskie.
Warto w tym miejscu zaznaczyć, że w związku z tym, że maszyny pakujące są urządzeniami, które kupuje się z nadzieją na ich długoletnie użytkowanie, nie należy spodziewać się, że z powodu upowszechniania się Przemysłowego Internetu Rzeczy stosunkowo niedawno zakupiony sprzęt zostanie wymieniony na nowy, fabrycznie przygotowany do pracy w sieciach IIoT. Alternatywą są moduły plug and play, które zapewniają połączenie z Internetem. Mają je w ofercie m.in. firmy Bosch Rexroth, Siemens oraz Advantech.
Technologie wykorzystywane do sterowania i nawigacji AGV
Do sterowania i nawigowania robotami AGV wykorzystuje się takie metody jak: pętla indukcyjna, nawigacja laserowa, linia refleksyjna, metoda żyroskopowa, ultradźwiękowa, układ współrzędnych, GPS, RFID, systemy wizyjne oraz odometria. Wśród nich najpopularniejsze są systemy refleksyjne, magnetyczne, indukcyjne. Na rynku natomiast pojawiają się coraz częściej metody laserowe. Metody refleksyjne są łatwe w implementacji oraz bardzo szybko można zmienić układ trasy w obiekcie, niestety wymagają utrzymania podłoża w czystości i wymiany/napraw uszkodzonych odcinków. System laserowy natomiast jest bardzo elastyczny, lecz na tą chwilę jest droższy od pozostałych metod nawigacji. W robotach MOBOT AGV stosujemy trzy metody nawigacji: linię magnetyczną + tagi RFID, linię kolorową + kody QR/tagi RFID oraz nawigację laserową.
Podstawą nawigacji laserowej jest wykorzystanie skanerów laserowych w celu orientacji w przestrzeni. Robot jest wyposażony w dalmierze laserowe służące do analizy otoczenia, z których dane są zapisywane w pamięci robota i przetwarzane przez oprogramowanie. Przełom w przypadku pozycjonowania laserowego polega na zmianie skali analizy przestrzeni oraz metody zbierania danych. Nie stosujemy kamery, jak w przypadku nawigacji z linią kolorową, gdzie nawigujemy względem ograniczonego obiektu - linii. Metoda ta polega na wysyłaniu wiązek laserowych w różnych kierunkach od robota, a następnie pomiarze czasu, w którym wrócą. Przykładowo: jeżeli wiązka wysłana pod kątem 30 stopni od głowy robota wróciła po 0,001 ns, to wiemy, że przeszkoda w tym kierunku znajduje się ~ 300m od nas. Wysyłając setki takich wiązek na sekundę, robot jest w stanie stworzyć w swojej pamięci chmurę punktów układających się w ściany, półki, krzesła, itd., czyli wirtualną mapę przestrzeni, w której się porusza. Do pomiaru otoczenia wykorzystujemy skanery laserowe o częstotliwości pomiarowej 120 skanów na sekundę i kącie skanowania 270°. Zebrane dane z czujników są przesyłane do komputera umieszczonego w robocie, wyposażonego w oprogramowanie do analizy pozycji, na podstawie skanów otoczenia. Za jego pośrednictwem generowana jest wstępna mapa otoczenia. Cały proces określania pozycji wykonywany jest kilku- lub kilkusetkrotnie, w celu uzyskania określonej precyzji pozycjonowania. Po wczytaniu danych do oprogramowania człowiek nanosi poprawki na mapę oraz usuwa błędy powstałe w wyniku poślizgów czy błędnej odometrii. Ostatnim etapem procesu tworzenia mapy jest weryfikacja poprawności nawigacji, po czym robot jest gotowy do pracy. Poruszając się w przestrzeni po stworzeniu mapy, robot skanuje otoczenie i porównuje zebrane informacje z zapamiętaną mapą, powtarzając proces tak długo, aż precyzja będzie wystarczająca. Działania te są konieczne w środowisku ciągle zmieniających się hal produkcyjnych. W rezultacie pozwala mu to na dojazd do wyznaczonego punku z dokładnością do ± 1 mm. Metoda ta daje największą elastyczność w dostosowywaniu tras przejazdów robota, zapewniając przy tym wysokie bezpieczeństwo jego pracy. |
ROBOTY WSPÓŁPRACUJĄCE
Maszyny pakujące znajdują zastosowanie przede wszystkim w nakładaniu opakowań bezpośrednio na produkt. Przykładami takich czynności są: zawinięcie batonu lub cukierka w folię, zafoliowanie mięsa na tacce.
W drugim etapie pojedyncze wyroby pakuje się do zbiorczego pojemnika mieszczącego zazwyczaj dużo sztuk. Na przykład batony i bombonierki przekładane są do kartonowego pudełka, natomiast butelki do skrzynek. Opakowania zbiorcze, które mają ułatwić transport i ochronić produkt przed zniszczeniem, układa się na paletach. W tej fazie procesu pakowania są zatem wykonywane głównie operacje pick and place i paletyzacji.
O tej ostatniej piszemy dalej. Jeśli natomiast chodzi o zadanie typu podnieś - połóż, to w jego realizacji chętnie wykorzystuje się roboty przemysłowe. W ramce przedstawiamy wytyczne na temat organizacji w pełni zrobotyzowanego stanowiska pick and place.
Od niedawna w tym zadaniu (i nie tylko, bowiem inną ważną aplikacją jest montaż) ludzi już nie tyle zastępują, co bardziej wspierają lub wykonują inne zadania w bezpośrednim sąsiedztwie, roboty współpracujące (collaborative robots, corobots, cobots). Tytułowe urządzenia są pierwszym przykładem wdrażania koncepcji Przemysłu 4.0 w środowisku przemysłowym.
Maszyny te charakteryzuje: kompaktowa budowa, lekka konstrukcja, zaokrąglone krawędzie, miękko wykończone powierzchnie, ukryte okablowanie i inne oprzyrządowanie. Ponadto inaczej, niż inne roboty przemysłowe, reagują one na zderzenie z innymi obiektami. Dzięki implementacji funkcji szybkiego hamowania i algorytmów detekcji kolizji w kontrolerze i serwonapędom o małej inercji natychmiast się zatrzymują.
Ważnym powodem, dla którego warto jest linię pakowania wyposażyć w robota właśnie tego typu, jest fakt, że może on, jak zresztą każdy robot przemysłowy, wyręczać pracowników w wykonywaniu czynności powtarzalnych oraz zadań wymagających dużej precyzji albo użycia dużej siły, a jednocześnie nie trzeba stosować dodatkowych zabezpieczeń ani zatrzymywać całej linii, aby personel mógł interweniować, gdy wystąpi jakiś problem, który spowoduje przerwanie pracy. W takich przypadkach zdolność ludzi do analizowania sytuacji i znajdowania rozwiązania jest uzupełnieniem możliwości siłowych i wytrzymałościowych robota.
WYBIERAMY PRZENOŚNIK
Surowce i zapakowane produkty są przewożone nie tylko przy użyciu AGV i wózków widłowych. Nieodzownym elementem linii transportowych są również przenośniki. Cechy, na które powinno się zwrócić uwagę przy wyborze tego urządzenia, to: modułowość, możliwość zamontowania elementów systemów dodatkowych, na przykład wizyjnych, znakujących oraz zliczających, uniwersalność, skalowalność, bezpieczeństwo, ergonomiczność i niezawodność. Ważna jest również łatwość jego konserwacji oraz energooszczędność.
Dzięki modułowości, podobnie jak w przypadku maszyn pakujących, z gotowych komponentów strukturalnych i napędowych łatwo można zbudować system transportu dopasowany do potrzeb aplikacji, a w razie potrzeby go przebudować. Segmentowa konstrukcja ułatwia też czyszczenie, konserwację oraz inspekcję przenośnika.
Uniwersalność oznacza, że taśmociąg jest przystosowany do przenoszenia produktów o różnych rozmiarach oraz właściwościach - na przykład dzięki zdejmowanym ogranicznikom bocznym i specjalnym nakładkom. Ta cecha w połączeniu z modułowością zapewnia skalowalność systemu transportu, tzn. łatwość dostosowania do zmian w produkcji, zarówno w zakresie asortymentu, jak i jej ilości.
Przenośnik powinien mieć wbudowane zabezpieczenia, na przykład uniemożliwiające jego przypadkowe uruchomienie. Urządzenia, które zaprojektowano zgodnie z zasadami ergonomii, zapewniają z kolei środowisko pracy przyjazne ich operatorom. Rzadziej też ulegają oni wtedy wypadkom. Możliwość niezależnego sterowania częściami systemu transportowego, czyli jego zatrzymywania lub spowalniania, przekłada się natomiast bezpośrednio na oszczędność energii zasilającej.
Jak zorganizować stanowisko pick and place?
15% - 30% czasu cyklu zajmuje z kolei podniesienie, a później odłożenie przenoszonego obiektu. Dlatego tu też można szukać oszczędności, wybierając odpowiedni rodzaj chwytaka. Ważne, aby pamiętać przy tym, że robot rozpędza się, a następnie hamuje z przyspieszeniem wynoszącym nawet kilkunastokrotnie więcej niż grawitacyjne. Wpływa to na stabilność oraz delikatność trzymania detalu. Chwytaki i kontroler Chwytaki dzieli się na dwie grupy: próżniowe i mechaniczne. Te pierwsze są lżejsze, dzięki czemu operuje się nimi łatwiej (i szybciej). Mają prostszą budowę niż te mechaniczne oraz nie zawierają części ruchomych, dlatego ich konserwacja jest tańsza. Chwytaki drugiego typu mają natomiast pewniejszy chwyt oraz łatwiej je pozycjonować. Kiedy wymagana jest większa precyzja, są to zalety, które mogą rekompensować to, że operuje się nimi wolniej i częściej się psują. Uwagi wymaga również kontroler. Wybrana platforma sterowania ruchem robota powinna umożliwić precyzyjną kontrolę jego kierunku i przemieszczenia oraz regulację jego prędkości i przyspieszenia. Ważna jest łatwość integracji z innymi komponentami linii pakowania (systemem wizyjnym, przenośnikiem, nadrzędnym systemem nadzoru). Prostota obsługi i programowania to kolejne istotne kwestie. Sterowanie wizyjne Zadania pick and place robot nie wykona bez wyraźnego wskazania, gdzie znajduje się obiekt, jak należy go podnieść i dokąd odłożyć. Za naprowadzanie ramienia manipulatora odpowiada zwykle system wizyjny. Rejestruje on, a potem przetwarza obrazy detalu, żeby wyznaczyć ścieżkę ruchu robota. Do sterowania maszyną, która będzie manipulowała płaskim obiektem, wykorzystuje się system wizyjny 2D. W tym celu trzeba powiązać jego układ współrzędnych z układem odniesienia stanowiska zrobotyzowanego. W związku z tym, że elementy układu optycznego, oświetlenie i inne czynniki zewnętrzne zniekształcają obraz rejestrowany przez kamerę zamontowaną nad obszarem roboczym manipulatora, należy wykonać kalibrację na obiekcie testowym o znanych wymiarach. Obrazy rejestrowane przez kamerę (lub kilka rozmieszczonych w różnych punktach w zależności od rozmiarów obszaru roboczego) są analizowane przez specjalistyczne oprogramowanie wizyjne. Z wykorzystaniem metody na przykład dopasowania wzorca są na nich wyszukiwane elementy charakterystyczne, jak brzeg lub róg detalu. Następnie wyznaczane jest ich położenie względem punktu odniesienia o znanych współrzędnych na przenośniku. Dane te są dalej wykorzystywane do zaprogramowania ścieżki ruchu robota. Kiedy system 3D? Okablowanie Jeżeli robot ma podnosić obiekty o określonej wysokości - na przykład z pojemnika, w którym są one rozmieszczone w sposób nieuporządkowany - trzeba go nakierować za pośrednictwem systemu wizyjnego 3D. Planując zrobotyzowane stanowisko pick and place sterowane wizyjnie, trzeba rozważyć szereg dodatkowych kwestii. Do takich należą m.in. : czy typ powierzchni obiektu (na przykład odblaskowej) może utrudnić jego zlokalizowanie, czy będzie on widoczny na tle taśmy przenośnika i czy równocześnie będzie kontrolowana jego jakość. Ważne jest także okablowanie, którym przesyłane będą dane z systemu wizyjnego, jeżeli kamera zamontowana będzie na ramieniu manipulatora. Źle dobrane utrudni jego ruch, jak również samo pod wpływem powtarzających się naprężeń szybko się uszkodzi. Dlatego w tym zastosowaniu powinno się używać specjalnych, elastycznych przewodów. Aby do minimum ograniczyć ich liczbę, warto rozważyć technologię Power over Ethernet, w której do zasilania oraz transmisji danych korzysta się z jednego kabla. |
PRZEGLĄD RODZAJÓW TRANSPORTERÓW
Ważny jest także typ przenośnika. Ze względu na rodzaj powierzchni nośnej dzieli się je na: taśmowe, łańcuchowe, pasowe, rolkowe, modularne oraz płytkowe. Transportery taśmowe są zalecane do przenoszenia pojedynczych i odpowiednio zapakowanych produktów, łańcuchowe w wypadku obiektów o dużej masie i szerokości, zaś pasowe - do przenoszenia produktów o dużych rozmiarach, lecz lekkich.
Wspólną zaletą tych trzech typów przenośników jest cicha praca. Dzięki temu mogą być używane na liniach produkcyjnych, w obrębie których ludzie pracują przez dłuższy czas. Do transportu produktów dużych i ciężkich używane są też przenośniki rolkowe. Modułowe sprawdzają się, gdy wymagana jest odporność na wysokie temperatury, chemikalia i uszkodzenia mechaniczne. Zaletą taśmociągów płytkowych jest natomiast łatwość naprawy.
W zależności od sposobu organizacji przestrzennej wyróżnia się przenośniki: poziome, pionowe i łukowe. Najpopularniejsze są systemy transportu poziomego. Przenośniki pionowe są natomiast używane na stanowiskach o ograniczonej powierzchni lub w wypadku, gdy produkty muszą być transportowane między piętrami lub dostarczane na odpowiednią wysokość. Oszczędność miejsca zapewniają także taśmociągi łukowe.
PRZENOŚNIKI PODWIESZANE
Oddzielną kategorię stanowią przenośniki podwieszane. Dostępne są różne modele tych urządzeń. Najpopularniejsze są dwie konstrukcje: te, w których przenoszone obiekty są zawieszane bezpośrednio na rolkach ruchomego łańcucha pociągowego oraz przenośniki z wózkami przesuwanymi po oddzielnym torze za pomocą elementów popychających, które są z kolei przymocowane do ruchomego łańcucha pociągowego (typ power & free).
Przenośniki podwieszane są dostępne w wersjach o różnym udźwigu, od kilkudziesięciu kilogramów do nawet kilku ton. Dzięki temu, zastosowane w transporcie mniejszych i lżejszych podzespołów, takich o średnich rozmiarach oraz wadze, jak na przykład wytłoczonych części metalowych, które przewożą pomiędzy blacharnią a stanowiskiem robota spawalniczego, jak również większych i cięższych obiektów. Przykładem tych ostatnich są zespawane szkielety samochodów transportowane do lakierni.
Przenośniki podwieszane mają wiele zalet. Na przykład w przypadku stanowisk malowania czy lakierowania dzięki nim aplikacja tych powłok jest łatwiejsza, uzyskuje się bowiem dostęp do malowanego obiektu ze wszystkich stron. Transport napowietrzny ułatwia też jego suszenie. Przenośniki podwieszane ułatwiają także organizację przestrzenną zakładu i pozwalają na oszczędność miejsca. Wynika to stąd, że nie blokują dróg komunikacyjnych.
Projektując system transportu podwieszanego, należy jednak pamiętać, że jeżeli jego konstrukcja będzie połączona z elementami konstrukcji budynku, trzeba sprawdzić, czy dana hala produkcyjna została zaprojektowana w taki sposób, że będzie w stanie wytrzymać powodowane tym dodatkowe obciążenie.
AUTOMATYZACJA PALETYZACJI
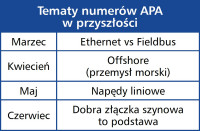
Tematy numerów APA w przyszłości
Paletyzacja oraz depaletyzacja, czyli załadunek oraz rozładunek palet opakowaniami zbiorczymi, czyli na przykład skrzynkami, workami, kontenerami i pudełkami kartonowymi to sztandarowe zadania, które się obecnie w przemyśle automatyzuje. Bierze się stąd, że z wykonywania ich przez pracowników zakładu nie wynikają żadne dodatkowe korzyści, a nawet wręcz przeciwnie - może to nawet przynieść szkody.
Powodem jest duże obciążenie fizyczne, na które są oni narażenia na takich stanowiskach. W dłuższej perspektywie czasu niekorzystnie odbijają się one na ich zdrowiu, a w efekcie na ich wydajności w realizowaniu innych czynności, nie wspominając już o nagłych urazach, do których dochodzi przy podnoszeniu dużych ciężarów w niewłaściwy sposób, które prowadzić mogą nawet do trwałego kalectwa.
Nie wolno też zapominać o innych zaletach zautomatyzowanej paletyzacji. Są to: większa precyzja oraz powtarzalność załadunku palet, układanie ładunków w sposób zapewniający oszczędność przestrzeni na palecie oraz uniemożliwiający przesuwanie się pojemników podczas transportu i większa wydajność.
W paletyzacji wykorzystuje się linie paletyzujące i roboty przemysłowe. Te pierwsze sprawdzają się zarówno w szybkim załadunku, nawet kilkuset pojemników w ciągu minuty, jak i w wolnej paletyzacji, od kilku do 10 pojemników na minutę. Roboty przemysłowe przeważnie pracują nieco wolniej.
Z drugiej strony wykorzystując je, łatwiej można zrealizować bardziej złożone schematy załadunku, w którym na przykład każda kolejna warstwa pojemników układana jest nieco inaczej albo są one różnie układane naprzemiennie, niż korzystając na sztywno zorganizować tradycyjnych paletyzatorów. Oprócz tego robot sterowany wizyjnie jest w stanie szybko dostosować się do zmian, na przykład rozmiarów pojemników, którymi manipuluje, zaś paletyzator w takim przypadku wymagać może kompletnego przeorganizowania.
Poza tym w niektórych typach opakowań zbiorczych roboty przemysłowe sprawdzają się lepiej niż konwencjonalne paletyzatory. Przykład przedstawiamy w ramce, w której opisujemy specyfikę paletyzacji worków.
Monika Jaworowska