W drugiej części artykułu przedstawiamy kolejne komponenty EMS, w tym m.in. czujniki używane do detekcji strat energii w systemach chłodzenia i grzania oraz produkcji i dystrybucji sprężonego powietrza oraz pary wodnej.
Proces produkcji pary wodnej, która jest wykorzystywana w różnych gałęziach przemysłu - m.in. do zasilania turbin, podgrzewania, czyszczenia lub sterylizacji, jest bardzo energochłonny. Szacuje się, że w tym celu użytkowana jest prawie połowa całego paliwa zużywanego w przemyśle. Aby zmniejszyć tę ilość, należy przede wszystkim ograniczyć produkcję nadmiarową oraz zwiększyć efektywność energetyczną instalacji wytwarzania i dystrybucji omawianego medium.
Najszybciej można to osiągnąć przez wyeliminowanie nieszczelności. Oprócz tego warto izolować rurociągi, którymi para jest przesyłana w celu uzyskania jak najmniejszych strat ciepła. Komponentem ważnym z punktu widzenia efektywności energetycznej tych systemów są również tzw. odwadniacze.
Są to specjalne zawory służące do usuwania skroplin oraz powietrza z rurociągów z parą. Ich usterki, na przykład z powodu zanieczyszczeń uniemożliwiających zamknięcie lub otwarcie przepływu, są przyczyną dużej utraty ciepła.
Innym elementem systemów produkcji i dystrybucji pary wodnej wymagającym kontroli są wymienniki ciepła oraz kotły parowe. W ich wypadku jedną z głównych przyczyn obniżenia sprawności energetycznej są osady tworzące się wewnątrz, w wypadku kotłów, oraz wewnątrz i na zewnątrz, w przypadku wymienników ciepła.
EFEKTYWNOŚĆ INSTALACJI SPRĘŻONEGO POWIETRZA
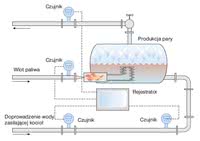
Rys. 1. Monitorowanie efektywności energetycznej systemu produkcji i dystrybucji pary wodnej wymaga rozmieszczenia czujników na wszystkich etapach tego procesu (na przykład w instalacji dostarczania wody), kontroli sprawności kotła oraz szczelności rurociągów, którymi para jest przesyłana
Usunięcie osadów ze zbiorników i rurociągów, ograniczenie nieszczelności oraz izolacja rurociągów to również najskuteczniejsze sposoby na zwiększenie efektywności energetycznej instalacji grzania i chłodzenia. Innym, również bardzo energochłonnym procesem jest produkcja sprężonego powietrza.
Szacuje się, że wytwarzanie tego medium, które jest w przemyśle wykorzystywane powszechnie, głównie jako napęd pneumatyczny różnych narzędzi i maszyn, w pneumatycznym sterowaniu maszynami oraz w urządzeniach czyszczących, pochłania nawet kilkanaście procent całkowitej energii zużywanej w tym sektorze gospodarki.
Analizę efektywności systemów produkcji i dystrybucji sprężonego powietrza należy rozpocząć od określenia sprawności używanych sprężarek, charakteryzowanej przez ilość energii elektrycznej wymaganej do wytworzenia danej objętości sprężonego powietrza. Następnie trzeba ustalić, czy rzeczywiste zapotrzebowanie na gaz w tej postaci nie jest mniejsze niż aktualna wydajność jego produkcji.
Oszczędności energii można uzyskać również, utrzymując w systemie dystrybucji powietrza możliwie najniższe ciśnienie oraz ograniczając nieszczelności. Straty ciśnienia można też zmniejszyć m.in. kontrolując stopień czystości filtrów sprężonego powietrza.
Należy również unikać pozostawiania włączonych sprężarek, gdy sprężone powietrze nie jest wykorzystywane, na przykład w czasie awarii lub przestoju produkcji. Chociaż zasada ta jest oczywista, nie zawsze jest przestrzegana.
Poprawa efektywności linii chłodzenia w przemyśle spożywczym
Temperatura chłodzenia pierwszego z nich była utrzymywana na poziomie -42°C, natomiast drugi zapewniał schładzanie do temperatury -12°C. Analizując specyfikę procesów produkcyjnych przeprowadzanych na różnych etapach przetwarzania żywności zauważono, że po niedawno przeprowadzonej modernizacji zakładu już tylko jeden z nich, na dodatek realizowany nieregularnie, wymagał zapewnienia temperatury -42°C. Aby zapobiec dalszemu marnowaniu energii, pierwszy stopień systemu chłodzenia podzielono na dwie oddzielne instalacje. Pierwsza z nich zapewnia chłodzenie w temperaturze do -42°C i można ją wyłączyć niezależnie od pozostałych, natomiast druga w temperaturze -36°C, która jest wymagana w większości zadań produkcyjnych. Drugi stopień systemu chłodzenia pozostawiono bez zmian. Dzięki wprowadzonym zmianom zużycie energii elektrycznej w tym zakładzie udało się ograniczyć o 16%, co wprost przełożyło się na koszt działalności całego przedsiębiorstwa. |
JAK MIERZYĆ?
W kontroli szczelności rurociągów przesyłowych pary wodnej oraz instalacji grzewczych i chłodniczych można wykorzystać przykładowo kamery termowizyjne. Przyrząd te wykrywają oprócz nieszczelności także uszkodzenia rurociągów, nieprawidłowe ustawienia zaworów odwadniaczy oraz osady w kotłach i wymiennikach.
Ponadto instalując czujniki temperatury na wlocie i wylocie medium, można określić sprawność wymienników ciepła oraz systemów grzania i chłodzenia. Do monitorowania efektywności energetycznej instalacji wytwarzania i przesyłu sprężonego powietrza oraz pary wodnej używane są też przepływomierze. Przykładem są przepływomierze masowe.
Ze względu na małą stratę ciśnienia oraz wysoki współczynnik turndown czujniki te nadają się do pomiaru przepływu sprężonego powietrza transmitowanego z małą prędkością w rurociągach o dużej średnicy. Dlatego są wykorzystywane do kontroli szczelności i pomiaru zużycia tego gazu. Również w przypadku pary wodnej, porównując w kilku punktach instalacji parametry przepływu tego medium, można wykryć nieszczelności.
W tym zastosowaniu najlepiej sprawdzają się przepływomierze wirowe, które dzięki swojej wytrzymałości szczególnie nadają się do pomiaru mediów o bardzo dużej temperaturze i dużym ciśnieniu. W pomiarach parametrów przepływu mediów transmitowanych rurociągami o dużych średnicach oraz tam, gdzie ingerencja w przebieg procesu jest niepożądana, zaleca się stosować przepływomierze ultradźwiękowe.
Przepływomierze są również wykorzystywane do kontroli efektywności procesu spalania paliw zasilających kocioł, w którym wytwarzana jest para wodna. W tym zastosowaniu używane są przepływomierze masowe, zwłaszcza w pomiarach zużycia gazu ziemnego oraz przepływomierze Coriolisa. Zaletą tych ostatnich jest to, że oprócz parametrów przepływu mierzą też temperaturę, gęstość oraz lepkość medium.
Poprawa efektywności energetycznej instalacji sprężonego powietrza
Na podstawie analizy wyników pomiarów udało się wyodrębnić kilka przyczyn niskiej efektywności energetycznej tej instalacji, w tym dwie najważniejsze, czyli straty powietrza w wyniku nieszczelności (około 446 tys. kWh) oraz niedopasowanie wydajności produkcji tego gazu do rzeczywistych potrzeb zakładu (ponad 633 tys. kWh rocznie). Podjęto m.in. następujące działania:
Całkowity koszt inwestycji wyniósł 350 tys. dol., z czego najdroższe były sprężarki, które zakupiono za blisko 90% tej sumy. Oszacowano, że całkowity zwrot tych wydatków nastąpi w ciągu 2,5 roku. Udało się bowiem zaoszczędzić 1,4 MWh rocznie, dzięki czemu wydatki na energię zmalały o ponad 147 tys. dol. rocznie. |
REJESTRACJA I TRANSMISJA WYNIKÓW POMIARÓW
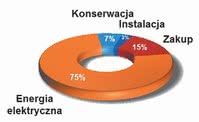
Rys. 2. Aż 75% całkowitego kosztu wykorzystania sprężarek stanowi koszt energii elektrycznej je zasilającej
Następnym krokiem po rozmieszczeniu odpowiednich czujników, liczników, na przykład energii elektrycznej, ciepła, wody i mierników parametrów elektrycznych we właściwych punktach monitorowanej instalacji lub urządzania jest organizacja systemu rejestracji wyników pomiarów. Najlepiej, aby odbywała się ona w regularnych odstępach czasu, przy czym bardzo ważny jest wybór częstotliwości pomiarów.
Zbyt częste odczyty wartości mierzonych wielkości mogą dostarczyć nadmiaru informacji, na podstawie których trudno będzie w czasie analizy wykryć na przykład trend zmienności danego parametru. Z drugiej strony większa ilość informacji może być pomocna w zrozumieniu szczegółów przebiegu procesu i występujących w nim anomalii powodujących nadmierne zużycie energii.
Wyniki pomiarów z różnych czujników są zwykle rejestrowane przez specjalne urządzenia. Rejestratory takie są często wyposażone w panel operatorski z wyświetlaczem. Są na nim prezentowane wyniki pomiarów (zwykle również w postaci graficznej) z poszczególnych urządzeń pomiarowych lub wartości parametrów obliczonych na ich podstawie.
Za pośrednictwem tych urządzeń dane te są też przesyłane dalej, na przykład do systemu sterowania lub do komputera w ramach lokalnej sieci zakładowej, na którym jest zainstalowane oprogramowanie do ich analizy. Niektóre rejestratory można skonfigurować w taki sposób, aby automatycznie odczytywały dane okresowo i zapisywały je w swojej pamięci lub na różnych zewnętrznych nośnikach danych (karty SD, pamięci USB), z których później można je skopiować.
Dostępne są też urządzania, które transmitują wyniki pomiarów w czasie rzeczywistym, za pośrednictwem różnych interfejsów komunikacyjnych. Są to m.in. standardowe wyjścia analogowe, na przykład prądowe, wyjścia impulsowe oraz interfejsy przemysłowych sieci komunikacyjnych, na przykład HART, M-Bus, Modbus, Profibus DP/PA, Foundation Fieldbus.
Na wypadek problemów z komunikacją w sieciach kablowych rejestratory są również wyposażane w interfejs bezprzewodowy, na przykład WirelessHART lub jest możliwość ich uzupełnienia o urządzenia sieciowe umożliwiające taką łączność. Dodatkowo niektóre rejestratory dzięki zintegrowanym sterownikom logicznym mogą zdalnie i automatycznie wyłączać lub zmieniać ustawienia maszyn, których parametry przekroczą zaprogramowane, dopuszczalne wartości.
PowerLogic ION firmy Schneider Electric
Wybrane informacje można grupować, dzięki czemu użytkownik programu uzyskuje dostęp do wszystkich niezbędnych wskaźników jednocześnie. Ponadto w PowerLogic ION można też określić wartości graniczne różnych wielkości, po przekroczeniu których generowane są alarmy, oraz tworzyć raporty. Te ostatnie mogą zawierać informacje przykładowo o sumarycznym zużyciu energii, profilach obciążenia oraz zgodności parametrów jakości energetycznej z odpowiednimi normami. Dane do programu mogą być importowane m.in. z liczników mediów użytkowych (wody, gazu, energii elektrycznej, pary wodnej) firmy Schneider Electric oraz innych producentów. Transmisja może być realizowana za pośrednictwem sieci kablowych oraz bezprzewodowo. Informacje gromadzone oraz przetwarzane w oprogramowaniu PowerLogic ION mogą być również przesyłane do innych zakładowych systemów, przykładowo SCADA. |
OPROGRAMOWANIE W SYSTEMACH GOSPODAROWANIA ENERGIĄ
Aby można było podjąć odpowiednie kroki w celu zwiększenia efektywności energetycznej urządzania lub instalacji, trzeba przeanalizować zarejestrowane wyniki pomiarów. W tym celu zwykle wykorzystuje się specjalistyczne oprogramowanie, w którym implementowane są różne funkcje ułatwiające to zadanie.
Służą one przede wszystkim do obliczania różnych parametrów, m.in. zużycia energii na jednostkę wytworzonego medium - na przykład jednostkę objętości sprężonego powietrza, kosztów w oparciu o dane z taryfy opłat oraz innych wskaźników efektywności.
Można w nich też tworzyć różne zestawiania, przykładowo porównania wskaźników wydajności różnych instalacji i sprawności poszczególnych urządzeń, zestawienia danych z różnych okresów oraz przy różnych obciążeniach, na przykład w zależności od wydajności produkcji.
Dostępne są też funkcje analizy czasu zwrotu z inwestycji, która mogłaby dany proces zoptymalizować, prognozowania zapotrzebowania energetycznego i kosztów energii na podstawie aktualnych cen oraz przy założeniu zmiany cen surowców energetycznych, a także tworzenia profili obciążenia i analizy jego zmian. Dane prezentowane są zwykle również w postaci graficznej, na przykład wykresów, diagramów.
eSight firmy Endress+Hauser
Aplikacja eSight składa się z kilku modułów. Jednym z nich jest moduł wykorzystywany do analizy zużycia energii, w którym zaimplementowano m.in. funkcję SEC (Specific Energy Consumption). Służy ona do wyznaczania ilości energii zużytej do wytworzenia jednostki produktu, na przykład pary wodnej lub sprężonego powietrza oraz porównywania tych wyników z danymi na temat efektywności podobnych procesów w innych branżach. Moduł ten pozwala również wyznaczyć zależność między zużytą energią a wydajnością produkcji. Częścią oprogramowania eSight jest także moduł do analizy finansowej, który służy do analizy danych archiwalnych o zużycia energii w przeliczeniu na jej koszt, na podstawie aktualnej taryfy opłat. Program monitoruje również bieżący pobór mocy, generując alarmy w przypadku gdy wcześniej ustalone wartości graniczne zostaną przekroczone. |
AUDYTY, SZKOLENIA
Dostępność szerokiej oferty coraz prostszych w instalacji i bardziej intuicyjnych w obsłudze narzędzi do rejestracji, transmisji i analizy danych pomiarowych oraz samych czujników pozwala na zastosowanie w zakładzie odpowiedniego systemu zarządzania energią.
Dodatkową motywacją do wdrożenia mogą stać się też wymierne korzyści, jakie może przynieść taka inwestycja głównie dzięki mniejszym wydatkom na energię pozwalającym na obniżenie kosztów działalności zakładu. Ponadto oszczędności energii oznaczają też łatwiejsze dostosowanie się do regulacji określających dopuszczalne normy emisji do atmosfery szkodliwych związków powstających w procesie spalania paliw kopalnych.
Sprawia to, że koszt inwestycji w system gospodarowania energią zwraca się zwykle w przeciągu kilku lat, a nawet szybciej. Innym rozwiązaniem są też tzw. audyty energetyczne, które na zlecenie przeprowadzane są w zakładzie przez firmy wyspecjalizowane w tym zakresie.
Uzupełnieniem tych działań powinny być też szkolenia personelu, uświadamiające konieczność oraz możliwości oszczędzania energii w przemyśle. Na działania zwiększające efektywność energetyczną przedsiębiorstwa można uzyskać dofinansowanie, przykładowo taki program wsparcia w 2011 roku został uruchomiony przez Narodowy Fundusz Ochrony Środowiska i Gospodarki Wodnej.
Monika Jaworowska