Na czym polega kraking?
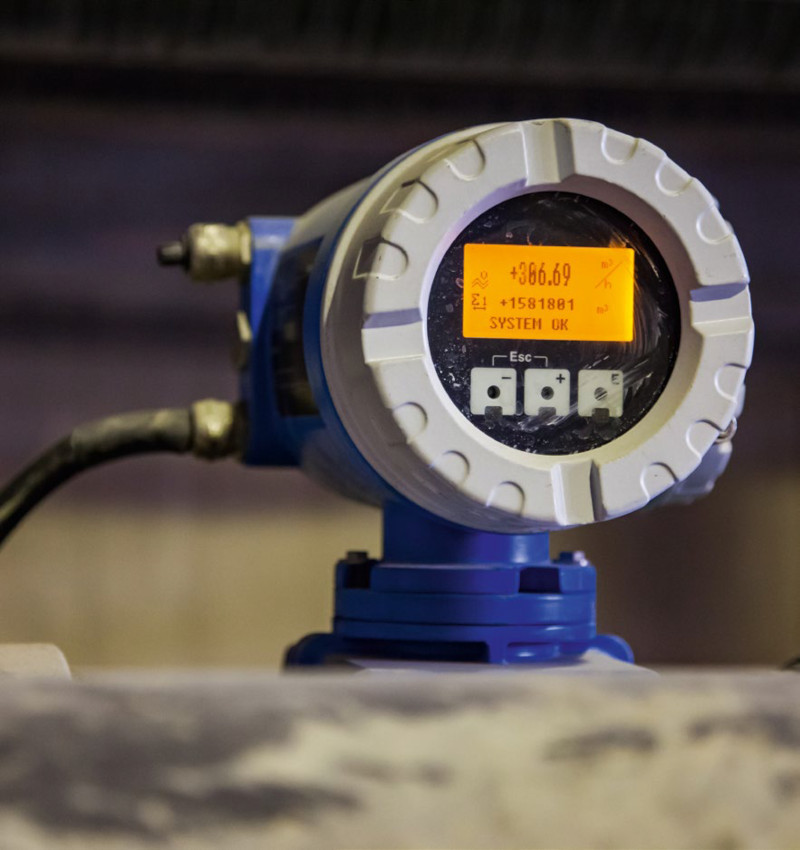
Kolejnym procesem w ramach przetwórstwa ropy naftowej jest kraking. Polega na przekształcaniu (fragmentacji) ciężkich paliw o dużej masie cząsteczkowej w lżejsze, wartościowsze produkty, jak benzyna i olej napędowy. W tym celu te pierwsze poddawane są działaniu wysokich temperatur i ciśnienia, w tym w obecności katalizatora. Wyróżnić można kilka metod krakingu.
Kraking termiczny polega na podgrzewaniu węglowodorów do wysokich temperatur (około +500...+700°C). Do tej kategorii metod zaliczane są dwie techniki. Jest to kraking parowy, w którym węglowodory przed ogrzaniem poddaje się oddziaływaniu pary, co przyspiesza rozkład cząsteczek. Druga metoda polega na podgrzewaniu węglowodorów bez dostępu powietrza.
Kolejną metodą jest kraking katalityczny. W tym przypadku wykorzystuje się katalizator w celu przyspieszenia procesu fragmentacji cząsteczek w niższych temperaturach (około +450...+500°C). Jest to zwykle zeolit lub tlenek glinu.
Generalnie kraking termiczny jest prosty i wydajny, ale generuje również dużo odpadów i wytwarza produkty gorszej jakości. Z kolei kraking katalityczny jest wydajniejszy oraz wytwarza produkty lepszej jakości, ale jest również bardziej złożony i droższy, choć zużywa mniej energii.
Pomiary pH w krakingu
Produkt uboczny reakcji z katalizatorem to koks. Jest on spalany w celu zapewnienia niezbędnego ciepła do utrzymania wysokiej temperatury potrzebnej w procesie krakingu. Gaz wylotowy ze spalania koksu przed uwolnieniem do atmosfery przechodzi przez osadnik i skruber. Pierwszy usuwa cząstki stałe, a skruber – związki siarki.
W skruberze gorące spaliny zawierające, oprócz związków siarki, też resztkowe cząstki katalizatora, wpływają do absorbera. Jest to zbiornik z wbudowanymi dyszami, które rozpylają odczynnik na wchodzące spaliny. Środek ten, którym często jest wodorotlenek sodu o właściwościach żrących lub związki wapnia, neutralizuje związki siarki w gazie wylotowym. Odczynnik oraz pozostałe drobne cząstki katalizatora zbierają się na dnie absorbera. Roztwór ten jest następnie recyrkulowany do dysz rozpylających, aby mógł dalej reagować z kolejną porcją wchodzących spalin.
Po przejściu spalin przez absorber przepuszcza się je jeszcze przez szereg filtrów, żeby wychwycić wszelką resztkową wilgoć. Ostatecznie oczyszczony gaz, wolny od związków siarki i cząstek stałych, jest uwalniany do atmosfery.
Odczynnik poddany recyklingowi musi być monitorowany pod kątem zmian współczynnika pH. W miarę bowiem jak stężenie siarki w cieczy zebranej na dnie absorbera rośnie, jej odczyn staje się bardziej kwaśny. Tymczasem celem jest utrzymanie pH na poziomie jak najbliższym neutralnego, zwykle 6,5 do 7. Aby zrównoważyć kwaśny odczyn siarki, odpowiednio dostosowuje się skład oraz ilość dodatkowo dozowanego odczynnika.
Pomiar pH recyklingowanego odczynnika jest z kilku powodów trudny. Przede wszystkim drobiny katalizatora są silnie ścierne i mogą uszkodzić elektrodę sondy pH. Mogą też zatkać jej porowate złącze, a związki siarki, tworząc siarkowodór, mogą ją zatruć, podobnie jak w przypadku pomiarów w procesie destylacji. W związku z tym w tym zastosowaniu wykorzystuje się specjalne sondy, na przykład z płaską szklaną elektrodą – taka konstrukcja ogranicza jej ścieranie przez drobne cząstki katalizatora, z materiałami złączy odpornymi na zatykanie.