- ASKOM jest obecnie firmą znaną z produkcji oprogramowania przemysłowego, aczkolwiek od samego początku działacie też jako twórca systemów automatyki i ich integrator. Jaka była tego geneza?
Rzeczywiście mamy kilka filarów działalności, przy czym pojawiały się one w sposób dla nas naturalny. W latach 90. zeszłego wieku rozpoczęliśmy od oferowania systemów automatyki i prac integratorskich. Już wtedy, aplikując rozwiązania z obszaru sterowania, mieliśmy pewien problem z systemami SCADA. Oprogramowanie dostępne na rynku nie spełniało naszych wymagań, co w szczególności dotyczyło systemów dla energetyki. Regularnie bywaliśmy też w obiektach przemysłowych i rozmawialiśmy z klientami, dzięki czemu wiedzieliśmy, jakich funkcjonalności SCADA potrzebują. Zdecydowaliśmy, że chcemy wyprodukować własny system sterowania nadrzędnego i kontroli - i to taki, dla którego założenia stworzą nie informatycy, a automatycy. Ci ostatni, w pełni świadomi potrzeb operatorów, a jednocześnie braków ówczesnych systemów sterowania, mogli dać precyzyjne wytyczne, co warto wdrożyć, aby zapewnić niezawodność i wygodę użytkowania oprogramowania.
Przystępując do prac nad systemem Asix, nie rozpoczynaliśmy od zera. Pracownicy ASKOM-u wcześniej tworzyli oprogramowanie SCADA w przedsiębiorstwie zagranicznym i o ile prawa autorskie naturalnie pozostały przy tym przedsiębiorstwie, o tyle same te osoby miały sporą wiedzę i doświadczenie praktyczne. Mogliśmy się więc na starcie odnieść do cech tego software'u oraz wcześniej wymienionych kontaktów z branżą, tak aby lepiej zdefiniować funkcjonalność naszego nowego oprogramowania.
Opracowany system, który dostarczaliśmy jako integrator, cieszył się rosnącym powodzeniem. Korzystali z niego coraz więksi klienci, z czasem pojawiły się też głosy, że chcieliby móc w jeszcze większym zakresie zarządzać swoją działalności operacyjną. W efekcie 15 lat temu rozpoczęliśmy prace nad systemami zarządzania produkcją, czyli MES. Głównym inspiratorem była tu dla nas opolska firma Nutricia.
- Czyli rozwój oprogramowania był wprost odpowiedzią na potrzeby rynku…
Dokładnie tak. Klienci chcieli otrzymać z jednego źródła zarówno rozwiązanie z zakresu automatyki, jak też zarządzania produkcją. Aczkolwiek, zaangażowani w projekt systemu SCADA, nie byliśmy jeszcze gotowi na tak duży temat, jakim była produkcja własnego systemu MES. Szukając na rynku odpowiednich narzędzi, zwróciliśmy się ku naszemu wieloletniemu partnerowi - firmie Siemens i zostaliśmy jedynym w Polsce integratorem ich oprogramowania do zarządzania produkcją - Simatic IT. Bazując na tym rozwiązaniu, wykonaliśmy wiele wdrożeń w różnych branżach przemysłu, co również dołożyło się do naszych doświadczeń w zakresie poznania rzeczywistych wymagań klientów odnośnie do takiego oprogramowania.
Po czasie wróciliśmy do rozwoju Asixa, rozszerzając go o pewne, wybrane funkcje z obszaru zarządzania. Od kilku lat nasz produkt nie jest już zamkniętym systemem SCADA, lecz platformą, na której budujemy specjalizowane moduły - gotowe rozwiązania. Takimi są m.in. Asix OEE, czyli rozwiązanie do monitorowania efektywności pracy maszyn, Asix Energy - do monitorowania i rozliczania mediów, Asix4Wago - system BMS zarządzania inteligentnymi budynkami czy też uszyte na miarę funkcjonalności typu tracing&tracking do śledzenia produkcji. Zwróciłbym też uwagę na moduł do zbierania danych o produkcji z wielu zakładów, który pozwala na optymalizację działalności przedsiębiorstwa o wielu lokalizacjach produkcyjnych.
Nasz rozwój został, jak sądzę, doceniony przez klientów. O ile dawniej kojarzono nas z systemem SCADA/HMI, o tyle od czasu, gdy zaczęliśmy oferować moduły Energy, OEE czy BMS, odbiorcy zaczęli traktować Asixa jako uniwersalny system, który stanowi podstawę do tworzenia rozwiązań dopasowanych do różnych zastosowań.
- Czy rozwijacie oprogramowanie również pod kątem specjalizacji branżowej?
Raczej nie patrzymy na rynek pod względem określonych branż - staramy się mieć spojrzenie szerokie, tworząc oprogramowanie na podstawie potrzeb klientów z rynku i przyglądając się konkurencji. Chcemy rozwijać narzędzie, które może być elastycznie dopasowywane do wymogów różnych sektorów. Aczkolwiek wiele jego funkcji powstało rzeczywiście jako bezpośrednia odpowiedź na potrzeby użytkowników z konkretnych branż. Na przykład moduł AsTrend - prezentacji i analizy trendów pomiarów, został stworzony na bazie sugestii pracowników Elektrowni Bełchatów, którzy potrzebowali narzędzia do analizy historycznej bardzo dużych ilości danych z bloków energetycznych. Rozwój jest też pochodną zmieniających się możliwości technologicznych. Tak było z wprowadzeniem wersji webowej, a niedawno też Asix Mobile.
Dzisiaj, w epoce Industry 4.0, na czoło listy wymagań wysuwa się komunikacja, w tym udostępnianie danych. Trzy lata temu wprowadziliśmy do naszego oprogramowania serwer OPC UA, później dodaliśmy też serwery i klientów REST oraz MQTT. Dzisiaj Asix ma około 120 drajwerów protokołów komunikacyjnych. Gdy pojawiają się nowe potrzeby odbiorców, opracowujemy kolejne.
- W sektorze MES działa grupa dużych firm będących globalnymi dostawcami automatyki - jakie miejsce na tym rynku zajmujecie?
Wdrożenia oprogramowania MES/MOM to de facto dwa odrębne obszary rynku. Systemy takie są przede wszystkim wykorzystywane przez duże koncerny, mające globalnie wiele zakładów. Takie firmy właściwie nigdy nie postawią na rozwiązania zindywidualizowane i wybierają software Siemensa, GE czy systemy Wonderware. Ich celem jest ujednolicenie rozwiązań stosowanych w koncernie, z globalnym wsparciem dostawcy. Najpierw wykonują pilotaż w jednym zakładzie, a następnie, na zasadzie roll-outu, powielają sprawdzone rozwiązanie w innych lokalizacjach, tak aby na koniec osiągnąć zunifikowany podgląd produkcji i raportowanie z zakładów, a także aby móc je benchmarkować. Często też przedsiębiorstwa takie rozpoczynają od wykorzystywania modułów do raportowania oraz Business Intelligence.
Na powyższe potrzeby odpowiedzieliśmy oferując oprogramowanie Simatic IT, obecnie Siemens Opcenter. Jest ono komplementarne do wdrażanych przez nas systemów automatyki Siemensa. Przykładowo stosując PCS 7 + Simatic Batch i właśnie Simatic IT, zostaliśmy włączeni do projektów jednego z koncernów m.in. we Francji i w Anglii (w tym z wdrożeniem MES w inwestycji typu greenfield), a także różnych modernizacji w zakładzie w Polsce.
Inaczej jest w przypadku mniejszej i średniej wielkości firm. Przedsiębiorstwa te bardzo liczą koszty i takie podmioty zawsze było trudno przekonywać do wdrożeń w zakresie MES. Aczkolwiek w ostatnich dwóch latach i to się zmienia. Firmy otwierają się na pewne projekty, sięgając stopniowo po elementy MES - np. rozpoczynając od monitoringu OEE czy też zużycia mediów. Tutaj jest obszar do działania dla mniejszych dostawców, ale pod warunkiem ich odpowiedniego doświadczenia, udokumentowanego historią wdrożeń. W takich projektach nie proponujemy oprogramowania Simatic IT, ale za to świetnie sprawdza się tu Asix z jego specjalizowanymi modułami. W kontekście rynku, gdzie karty rozdają najwięksi gracze, my obsługujemy pewien rodzaj niszy rynkowej.
Dodałbym, że niezależnie od skali działalności firmy produkcyjnej i jej potrzeb, nie powinno się jej oferować rozwiązań zamkniętych i trudnych do wdrożenia oraz utrzymania. Stąd też stworzyliśmy wizardy - kreatory aplikacji, które pozwalają na łatwe wdrożenie docelowego systemu. W projektach zaczynamy od wyspecyfikowania istotnych dla klienta parametrów (kluczowych atrybutów) w postaci bazy zmiennych, a następnie, korzystając z kreatora, budujemy standardową aplikację z obrazami, raportami i całą resztą. Niesamowicie oszczędza to czas projektowania i wdrażania. A ponieważ platforma software'owa jest otwarta, możemy też zrealizować dodatkowo specyficzne funkcjonalności, aczkolwiek składają się one zazwyczaj na nie więcej niż 20‒30% całego projektu.
- Czyli nie zawsze potrzebny jest duży, kompleksowy system. Czy zatem wdrożenia MES można wykonywać stopniowo, etapami?
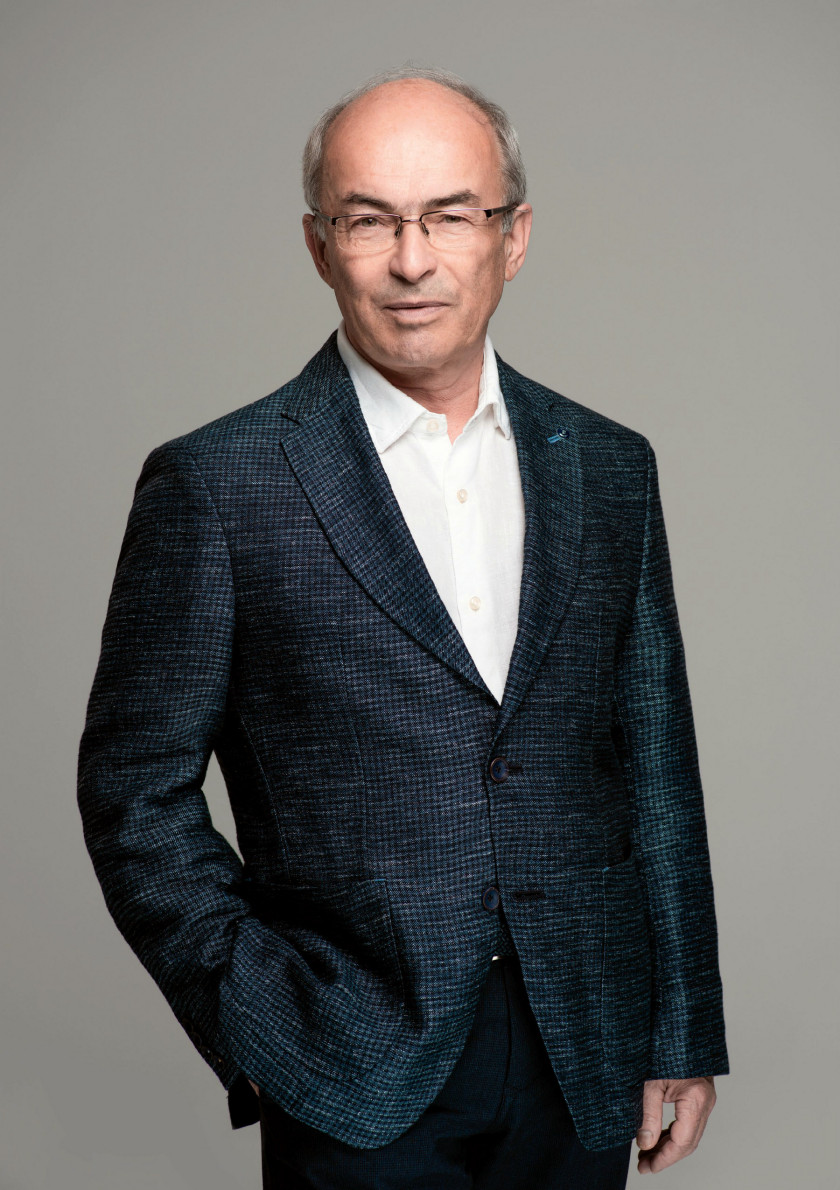
Tak - i jest to częsta praktyka. Wynika to zresztą z konieczności przekonania klienta, że dane rozwiązanie sprawdzi się u niego i przyniesie oczekiwane korzyści. Stąd też wielokrotnie zaczynamy od wdrożenia typu proof-of-concept, który jest czasami wykonywany przez kilku konkurencyjnych dostawców.
Tutaj wracamy jednak do mierzenia sił na zamiary. Przykładowo robimy obecnie projekt dla międzynarodowej firmy, która, pomimo posiadania sporej wielkości parku maszynowego, wyposażona jest w bardzo nieliczne rozwiązania do monitorowania jego pracy. Firma potrzebuje kontrolować zupełnie podstawowe parametry produkcji, tak aby później je benchmarkować, móc wykonywać porównania pomiędzy maszynami, pracownikami, zestawiać ze sobą produktywności na różnych zmianach i w różnych krajach. W tym przypadku już podstawowa wiedza o produkcji może im dać spore oszczędności. Przy okazji zlikwidowane jest papierowe notowanie informacji o zdarzeniach oraz parametrach produkcyjnych, które może rodzić przekłamywanie danych i subiektywizację ocen.
Chciałbym dodać, że o ile jedną sprawą jest usprawnianie produkcji, sygnalizowanie usterek czy analiza pracy maszyn, to równie ważne jest coś tak pozornie prozaicznego, jak porównywanie wyników bieżącej produkcji z tzw. targetem - wyznaczonym celem. Nawet pokazywanie tej zależności w postaci kolorowych słupków na ekranie przy stanowisku produkcyjnym jest wielkim ułatwieniem dla operatorów oraz menedżerów. I nie chodzi tu o dokładne liczenie mikroprzestojów czy szukanie ich powodów - już taki niewielki element wdrożenia, dzięki któremu widać porównanie wytwarzania w stosunku do wyznaczonego celu czy np. zużycie mediów w stosunku do prognozowanego - stanowi bardzo duże usprawnienie i przekłada się na zwiększanie efektywności produkcji.
- Czy pozyskiwanie danych z linii technologicznych we wdrożeniach jest problemem?
Jest to temat na osobną opowieść. Dawniej wielokrotnie mierzyliśmy się z tym problemem podczas wdrażania systemu monitoringu maszyn. Będąc inżynierami, chcieliśmy pozyskiwać ze sterowników maszyn maksimum informacji o powodach przestojów. O ile technicznie było to wykonalne, o tyle firmy produkujące maszyny były bardzo niechętne, aby do takich zmiennych zapewniać dostęp. A nawet gdy się zgadzały, to otrzymywane dane często zawierały sporo błędów. Co więcej - w procesie składania ofert na wdrożenie systemu monitoringu OEE okazywało się, że sporymi kosztami były właśnie te związane z pozyskiwaniem informacji z maszyn. W polskich zakładach park składa się często z maszyn w różnym wieku, pochodzących od różnych firm, przez co pobieranie z nich informacji jest po prostu trudne. Temat można oczywiście zrealizować, ale rzadko który klient aprobuje związane z tym podwyższone koszty.
Po owych doświadczeniach przekonaliśmy się, że znacznie łatwiej jest zbierać wymagane informacje dodatkowymi czujnikami i uzupełniać je o dane wprowadzane na panelu przez operatora maszyn. W przypadku tych pierwszych pozyskujemy dane dotyczące stanu pracy, liczby produktów dobrych i braków, zużycia materiałów czy też energii. Z kolei operator podaje takie informacje jak np. powody zatrzymania maszyn.
Przykładowo w firmie Unilever wdrożyliśmy najbardziej złożony system OEE. Jest nim objętych blisko osiemdziesiąt maszyn i pozyskujemy z nich dane pozwalające określać kilkadziesiąt przyczyn mikroprzestojów. System jest fantastyczny, ale jego wdrożenie trwało ponad dwa lata. Klient się na niego zdecydował, bowiem takiej funkcjonalności potrzebował. Gdzie indziej, przykładowo w firmie Nutricia, w przypadku jednej linii niedawno skończyliśmy na zasadzie proof-of-concept system, który ma zapewniać przede wszystkim informacje o tym, jak blisko targetu produkcyjnego jest stanowisko, a także podawać kilka podstawowych informacji. I to też działa bardzo dobrze, spełniając potrzeby odbiorcy.
Po latach, gdy mieliśmy okazję wykonywać wszystkie warianty wdrożeń, mogę stwierdzić, że zawsze trzeba dostosować tworzone rozwiązanie do potrzeb klienta. Oceniam też, że spore korzyści można osiągać ze zbierania wybranych, istotnych informacji. Szczególnie gdy jest wiele zakładów, które powstawały w różnych okresach i mają zróżnicowany park maszynowy - wtedy niewielki zewnętrzny koncentrator danych i zbieranie wybranych informacji jest najlepszym rozwiązaniem. A co więcej - doskonale otwiera to drogę do aplikacji chmurowych! Czy bowiem prześlemy zebrane informacje do lokalnego serwera, czy też skorzystamy z urządzenia krawędziowego i wyślemy dane do aplikacji w chmurze - to już nie ma różnicy i zależy od preferencji użytkownika.
- Czy firmy z tego korzystają?
Jeżeli chodzi o cloud computing, to tutaj na zmiany musimy pewnie jeszcze poczekać kilka lat. Dzisiaj wielu przedstawicieli przedsiębiorstw wciąż mówi: "nigdy nie przejdziemy do chmury ze względu na poufność danych". Aczkolwiek sądzę, że warto, aby przemyśleli oni kilka kwestii. Przede wszystkim to, ile można zaoszczędzić na kosztach utrzymywania własnego działu IT i własnego centrum obliczeniowego. Jeżeli dodatkowo firma ma wiele zakładów produkcyjnych, to koszty te są powielane i można je zoptymalizować, przenosząc się do chmury obliczeniowej. Dzisiaj jest wiele globalnych providerów udostępniających takie zasoby, którzy robią to profesjonalnie.
Jak najbardziej rozumiem, że przekonanie się do chmury trwa, bo sami mieliśmy taki problem. Dziś używamy jej m.in. w zarządzaniu sprzedażą i kontaktach z klientami. Dodam, że w przełamaniu się do wdrożenia cloud computingu pomaga często jego wykorzystanie przez inne firmy w branży. A jest o co się starać, bo zmienia to koszty utrzymania infrastruktury oraz zapewnia wyższy poziom cyberbezpieczeństwa. Myślę, że outsourcing do chmury to przyszłość.
- Czy takie lub podobne wdrożenia wykonywaliście?
Pierwsze jaskółki już są, choć w tym przypadku nie dotyczyły one zewnętrznej chmury obliczeniowej. Byliśmy natomiast jednymi z pionierów wykorzystania zupełnie nowej koncepcji wdrożenia systemów SCADA. Miało to miejsce w spółce SGL Carbon, gdzie zrealizowaliśmy upgrade SCADA przez migrację wszystkich serwerów systemu do klastra komputerowego w centralnym dziale IT. Przy węzłach produkcyjnych pojawiły się jedynie panele klasy "thin client", zaś cała komunikacja pomiędzy nimi, klastrem a sterownikami, odbywa się poprzez redundantną sieć ethernetową. Całość zrealizowaliśmy dla 27 produkcyjnych serwerów SCADA przy około 65 tys. zmiennych dla całej fabryki.
Stworzone rozwiązanie pozwoliło na wdrożenie dodatkowych wirtualnych serwerów w klastrze - m.in. dwujęzycznego serwera webowego, a także aplikacji diagnostycznych. System zapewnia też pełną redundancję, ujednolicone interfejsy oraz możliwość komunikowania zdarzeń drogą SMS-ową i mejlową. W jego wdrożeniu działy IT oraz OT blisko współpracowały ze sobą, co de facto stanowiło realizację wizji fabryki Industry 4.0. Pokazaliśmy podobne rozwiązania u innych klientów i mamy kolejne projekty, gdzie firmy będą przechodziły do systemów SCADA opartych na klastrze komputerowym.
- Wracając do ASKOM-u - dzisiaj macie nadal te dwie podstawowe nogi działalności...
Trzy! Są to: automatyzacja, produkcja systemów SCADA oraz integracja systemów zarządzania produkcją. Obszary te naturalnie się zazębiają. W przypadku oprogramowania naszym celem od samego początku było nie tylko wykorzystywanie go we własnych aplikacjach, ale też stanie się dostawcą produktu komercyjnego, integrowanego przez inne firmy. I to się udało! Obecnie współpracuje z nami ponad 50 integratorów systemów, którzy świetnie sobie radzą i dają nam spore zamówienia na licencje. Coroczne wzrosty w tym zakresie wynoszą po kilkanaście procent.
Integratorzy to nie tylko nasza forpoczta na rynku, ale też ważni partnerzy biznesowi. Co roku spotykamy się na warsztatach i jest to wydarzenie bardzo cenne również dla nas. Dostajemy wtedy feedback dotyczący nowych oczekiwań względem oprogramowania i na tej podstawie rozwijamy jego funkcje. Zawsze wsłuchujemy się w głosy z rynku, niezależnie od proponowania naszych własnych rozwiązań.
Integratorzy są naszymi klientami, ale też, teoretycznie, konkurentami we wdrożeniach. Ale sytuacje, gdy ze sobą konkurujemy, są bardzo rzadkie i nie powodują problemów. Umiemy się porozumieć, mamy też jasno poukładane reguły dotyczące polityki rabatowej - w tym zakresie staramy się być bardzo transparentni. Sądzę, że udało nam się tak zorganizować całość biznesu, aby określić jasno reguły współobecności na rynku.
- Czy współpraca ze sporą grupą integratorów jest dla Was sposobem na konkurowanie na rynku z dużymi koncernami oferującymi automatykę przemysłową?
Raczej nie patrzymy na to w ten sposób, bowiem nasza perspektywa związana jest bardziej z samym produktem. Opracowanie i oferowanie profesjonalnego systemu SCADA wymaga posiadania sporego zespołu, który tworzy nowe wersje oprogramowania, a także zapewnia wsparcie klientów i serwis. Generuje to spore koszty, których ponoszenie nie miałoby uzasadnienia, gdybyśmy korzystali z systemu jedynie we własnym zakresie. Stąd też, znalezienie na rynku odbiorców sprzedających nasze licencje było niejako biznesową koniecznością. Obecnie sami sprzedajemy około 30% wszystkich licencji, drugie tyle oferują integratorzy systemów. Na pozostałą sprzedaż składają się obroty pośredników, dystrybutorów i innych podmiotów.
Drugą przyczyną szerokiej działalności na rynku jest konieczność specjalizowania się w wielu branżach. O ile automatyka jest sama w sobie czymś uniwersalnym, o tyle w różnych aplikacjach dochodzi specjalistyczne know-how, które jest wymagane do wykonywania jej optymalnych wdrożeń. Działając samemu, nigdy nie mielibyśmy w każdym z obszarów topowych kompetencji, natomiast współpracując z grupą kilkudziesięciu integratorów, z dużym prawdopodobieństwem znajdziemy firmę mającą tu odpowiednie umiejętności. Przykładami są m.in. działalność w dostarczaniu systemów automatyki dla branży górniczej, do zastosowań wodociągowo-kanalizacyjnych, budynkowych czy też oferowanie rozwiązań geoSCADA do systemów dyspozytorskich. Są to niektóre ze specjalizacji naszych partnerów.
Jako ciekawostkę dodam, że dla firmy WAGO-ELWAG wyprodukowaliśmy rozwiązanie do zastosowań w automatyce budynkowej. Stworzyliśmy wspólny projekt, który zawiera pakiet bibliotek po stronie sterowników WAGO i kreatora aplikacji BMS na platformie Asix. Procedury sterowników WAGO są automatycznie przekładane na obrazy w systemie SCADA. Dystrybutorem tego pakietu jest WAGO-ELWAG, my jesteśmy zaś producentem OEM i jest to dla nas świetny rodzaj kooperacji. Można powiedzieć, że powstała tu nasza czwarta noga na rynku i bardzo cieszylibyśmy się, gdyby udało się to rozwinąć. Takie specjalizowane rozwiązania możemy budować dla producentów maszyn, oferentów systemów BMS i innych firm.
- Czy aktywnie działacie również na rynkach zagranicznych?
Tutaj możemy sobie wiele zarzucić. Mamy pojedynczych integratorów - m.in. w Kanadzie, Izraelu, mamy też partnera obsługującego rynek rosyjski. Robimy pewien biznes za granicą, ale raczej na niewielką skalę. Wykonywaliśmy też i nadal robimy aplikacje za granicą, w tym wschodnią, co tworzy kolejne przyczółki, natomiast nigdy nie dokonaliśmy ekspansji na dużą skalę. Może sposobem na tę ostatnią będzie przejście na sprzedaż platformy SCADA w sklepie internetowym, co pewnie wiązałoby się z ukierunkowaniem systemu w stronę klientów OEM.
Powyższy pomysł jest do zrealizowania, bowiem w takim przypadku podstawą jest oferowanie oprogramowania wielojęzycznego, gdzie łatwo zmieniać wersje językowe - np. na potrzeby realizowania serwisu w różnych krajach. Wymóg ten jak najbardziej spełniamy. Oferujemy również szkolenia, mamy też dział wsparcia serwisowego pracujący w trybie 24/7, który na bieżąco wspiera użytkowników naszych wdrożeń. I nie chodzi tu o zdalne usuwanie usterek, ale pomaganie klientom w prowadzeniu codziennej obsługi oprogramowania, wykonywanie maintenance'u baz danych, serwerów, itd. Również bardzo szybko reagujemy na ewentualne usterki. Dział serwisu w naszej organizacji moglibyśmy w naturalny sposób rozszerzyć o wsparcie dla zagranicznych użytkowników Asixa. Technicznie jesteśmy więc do tego przygotowani.
- Gdzie jesteście dzisiaj, po wielu latach rozwoju oprogramowania Asix? Jaki był klucz do sukcesu na rynku software'u przemysłowego?
Jako ASKOM mamy bardzo długą listę referencyjną - obejmuje ona ponad 600 wdrożeń i właściwie wszystkie sektory rynku. Sam zaś Asix to ponad 12 000 wdrożonych licencji. Potwierdza to fakt, że jest on postrzegany jako dojrzały technicznie i jednocześnie ekonomicznie konkurencyjny produkt, który można dopasowywać do potrzeb różnych klientów. A te ostatnie rosną. Dzisiaj polscy integratorzy tworzą coraz bardziej rozbudowane konfiguracje, które obejmują duże ilości zmiennych, systemy z redundancją i zaawansowanymi protokołami. Cieszy mnie, że Asix jest narzędziem, które daje takie możliwości.
Patrząc zaś na całość naszego biznesu, sądzę, że od początku kluczowe było pozostanie firmą, która umie kompleksowo obsługiwać odbiorców - od poziomu obiektu, opomiarowania, poprzez sterowniki i ich programowanie, wdrażanie SCADA, aż po systemy MES. Rozbudowa oferty i kompetencji w stronę oprogramowania była też zbieżna z rozwojem samego rynku. Dzisiaj coraz większą wagę mają właśnie projekty MES/MOM, zaś obszar automatyki jest wprawdzie nadal ważny, bowiem software musi skądś otrzymywać dane, jednak biznes z tym związany jest coraz trudniejszy. Coraz ciężej jest tu utrzymać satysfakcjonującą marżowość, co potwierdzają również nasi partnerzy i inni dostawcy, z którymi rozmawiamy.
W tej sytuacji oferowanie MES i rozwiązań z pogranicza OT/IT jest sposobem nie tylko na utrzymywanie odpowiedniego poziomu biznesu, ale też doskonałym punktem wyjścia w przyszłość. Dzisiaj na rynku dynamicznie rozwija się tematyka przemysłowego IT i, jak sądzę, będzie tak też w kolejnych latach. Planujemy kontynuować działania w tym zakresie, tworząc - tak jak dotychczas - rozwiązania bazujące na dobrym zrozumieniu potrzeb użytkowników, wspierając je know-how doświadczonych praktyków branżowych.
- Dziękujemy za rozmowę.