Coboty, AGV/AMR i nowoczesna intralogistyka
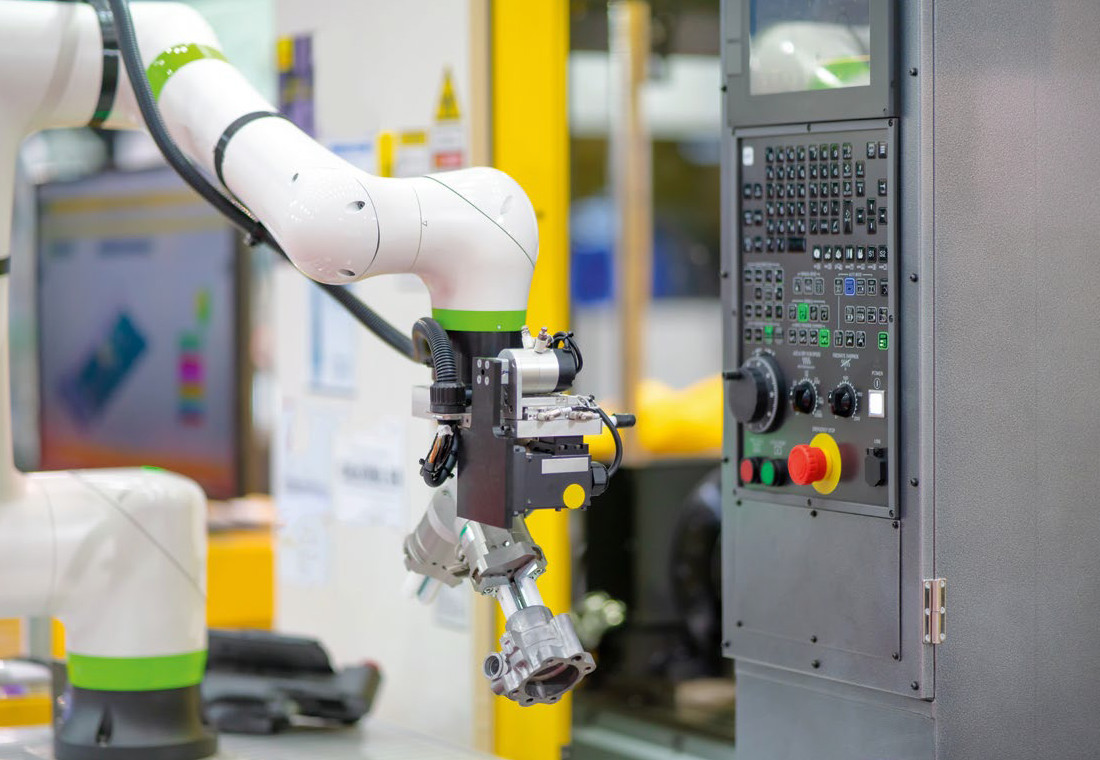
Krajowy rynek robotów mobilnych i współpracujących jest coraz bardziej dojrzały. Dynamika wzrostu sprzedaży spowolniła w porównaniu do lat ubiegłych, a konkurencja znacznie nasiliła się z uwagi na pojawianie się nowych dostawców. Firmy te albo konsekwentnie dążą do zdetronizowania dotychczasowych liderów, albo skutecznie odnajdują swoje miejsce w specjalistycznych niszach. Zmienia się również podejście klientów, którzy zdobyli większe doświadczenie w korzystaniu i wdrażaniu cobotów oraz AGV, co ułatwia im realną ocenę ich możliwości. Nieustające pozostają jednak obawy dotyczące bezpieczeństwa w pracy z robotami oraz lęk przed tym, że coraz doskonalsze i inteligentniejsze maszyny mogą zastąpić ludzi w pracy.
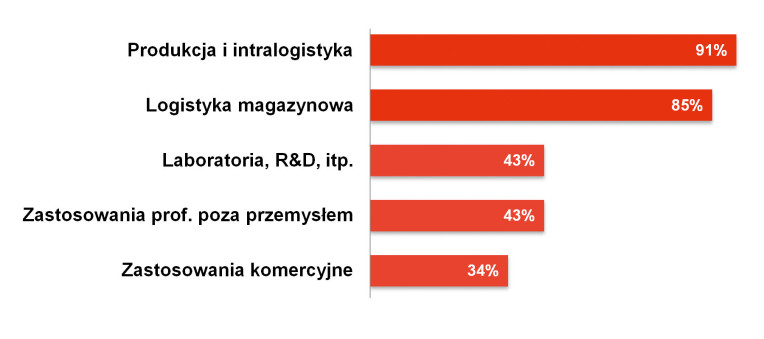
Rynek robotów współpracujących
Zacznijmy od kompleksowego przeglądu branży cobotów na bazie informacji branżowych i redakcyjnego badania rynku. Jego respondenci szacują krajowy rynek cobotów na 150‒600 sztuk rocznie, a tempo jego wzrostu – od 5% do 60%. Trzy lata temu wartość rynku oceniana była na 100‒500 sztuk rocznie, natomiast przyrosty – od 3% do 150%. Wyraźna tendencja wzrostowa raportowana przez naszych ankietowanych znajduje także potwierdzenie w trendach światowych. Według raportu "Collaborative Robot Market" wykonanego przez Markets and Markets globalny rynek robotów współpracujących wzrośnie z 1,1 mld dol. w 2022 do 9,2 mld dol. w 2028 roku, przy średnim wzroście rocznym (CAGR) na poziomie 41,5%.
Najczęstsze zastosowania robotów współpracujących na rynku polskim to: pick & place (wskazane przez 90% ankietowanych), pakowanie (84%) oraz paletyzacja (83%). Do nieco mniej popularnych aplikacji należą montaż (71% wskazań), machine tending i obsługa gniazd (68%) oraz montaż elektroniki (63%).
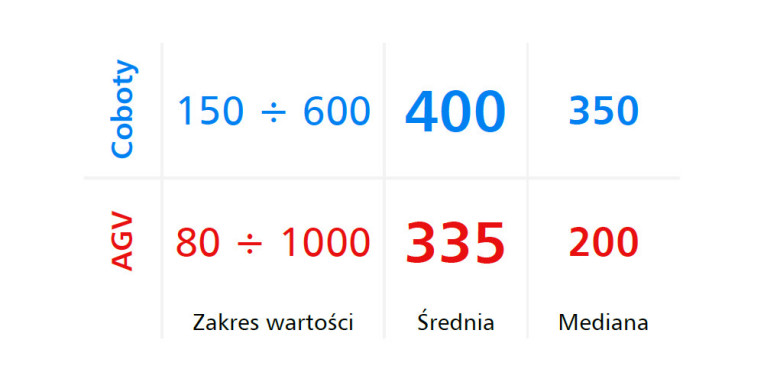
Porównując obecną popularność poszczególnych aplikacji ze wskazanymi przez naszych respondentów w poprzednich badaniach, nie dostrzeżemy zbyt dużych różnic. Dwa lata temu, podobnie jak obecnie, na pierwszym miejscu znajdowało się pick & place. Nieznacznie mniej popularnym zastosowaniem, w porównaniu do obecnych odczytów, był montaż oraz machine tending i obsługa gniazd. Jednak zarówno w dawnym badaniu, jak też obecnie, pierwsza piątka najpopularniejszych aplikacji zawiera te same pozycje.
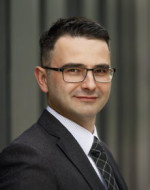
Artur Wojewoda
Yaskawa Polska
Czy coboty to dodatek do ofert dostawców robotów, czy naturalny kierunek rozwoju całej branży?
Początkowo w coboty generalnie nie wierzono, wieszczono wręcz rychły upadek koncepcji. Bo przecież roboty muszą być zamknięte w klatce, żeby mogły działać szybko i wydajnie, a pomysł, aby uczynić je towarzyszami człowieka, stanowił zaprzeczenie wszystkich obowiązujących zasad!
To jednak diametralnie się zmieniło. Dzisiaj coboty są coraz powszechniejsze, mogą one montować, obsługiwać maszyny, pakować i paletyzować, a nawet spawać. My również oferujemy tego typu roboty współpracujące – tą to maszyny łatwe do zaprogramowania i niezawodne. Do tego wyposażone są w solidnie wykonany programator. Ma on formę nowoczesnego tabletu z przyciskami i wyposażony jest w czujnik położenia, co znacząco ułatwia interakcje z maszyną.
Dziś już właściwie wszyscy uwierzyli w coboty i duża część naszego firmowego planu rozwoju jest z nimi związana. W 2022 roku na świecie sprzedało się ponad 500 tys. robotów wszystkich typów, z czego ponad 50 tys. było wersjami współpracującymi. To dużo. Przecież jeszcze np. pięć lat temu na wykresach sprzedażowych słupek dotyczący modeli współpracujących był w stosunku do reszty praktycznie niezauważalny! Marketing w stylu "kup robota, zaprogramujesz go w 10 minut i już będzie dla Ciebie produkował" zadziałał!
A co z bezpieczeństwem cobotów?
Jest ono kluczowe i świadomość odbiorców w tym zakresie stale rośnie. Aczkolwiek, powiedzmy szczerze, jeżeli chodzi o roboty współpracujące, to z bezpieczeństwem było różnie. Wprawdzie producenci od początku powtarzali, niczym mantrę, jak łatwy do zaprogramowania i bezpieczny jest cobot, ale jednocześnie wiele tych maszyn instalowanych było w klatkach!
Dzisiaj zauważam, że do tematu bezpieczeństwa podchodzi się z pewną ostrożnością. Odbiorcy edukują się, nabierają świadomości, że stanowisko może jednak być niebezpieczne i zadają pytania, co trzeba zrobić, aby to zmienić. Owszem, pojęcia takie jak "triada bezpieczeństwa" jeszcze nie wszędzie są znane, ale coraz więcej osób ma już tę podstawową świadomość, że wprawdzie robot współpracujący jest konstrukcją wewnętrznie bezpieczną, ale tak jak każdy system ma jakiś swój pierwotny poziom ryzyka. Gdy dołożymy do robota chwytak, np. uchwyt spawalniczy, musimy dokonać analizy ryzyka stanowiska całego urządzenia, bo ono zawsze jakieś jest. I dopiero wtedy należy je minimalizować.
Czasami trzeba w pewnych obszarach tempo pracy robota zwolnić, a czasem przeciwnie – może w naszej aplikacji okaże się, że robot musi działać szybciej, więc aby był bezpieczny, trzeba dodać np. skaner. Nawet wtedy jednak zawsze zostaje jakieś ryzyko resztkowe, o którym musimy poinformować użytkownika, czyli stworzyć dobrą instrukcję obsługi jego stanowiska. Wszystko to dzieje się z pożytkiem dla branży, bo trend dotyczący łatwej robotyzacji za pomocą cobotów jest silny.
Do najbardziej znanych marek cobotów w kraju należą: Universal Robots, FANUC i KUKA. Do tego grona aspirują nieco mniej rozpoznawalne w tym segmencie rynku: Omron, ABB i Yaskawa. W porównaniu do odczytu z 2021 roku (poprzednie badanie branży) czołówka w tej grupie pozostaje bez zmian. Można jednak zauważyć poprawę popularności marki KUKA, w każdym razie jeżeli chodzi o wskazania respondentów.
Najważniejsze powody, dla których zdaniem respondentów klienci decydują się na stosowanie robotów współpracujących, to: bezpieczeństwo, brak konieczności odgradzania cobotów, elastyczność aplikacyjna i łatwość programowania. Wszystkie wymienione cechy odróżniają je od tradycyjnych robotów, które w mniejszym stopniu spełniają te oczekiwania. Porównując przekazywane przez naszych respondentów argumenty przemawiające za cobotami obecnie do tych z poprzedniego badania, należy ocenić, iż nie zmieniły się one istotnie i bezpieczeństwo odgrywa wśród nich rolę najważniejszą.
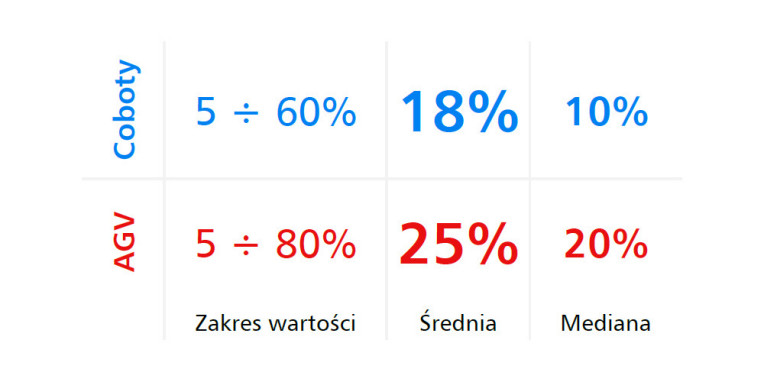
Do branż, które w największym stopniu wykorzystywać będą możliwości robotów współpracujących, należą zdaniem naszych respondentów: motoryzacja, sektor spożywczy i elektroniczny. W nieco mniejszym stopniu coboty popularne są w branżach: FMCG, tworzyw sztucznych oraz w logistyce. Pod tym względem postrzeganie poszczególnych sektorów przez respondentów praktycznie niczym się nie różni w porównaniu do wyników sprzed dwóch lat.
Z kolei na pytanie "w jakich aplikacjach najefektywniejsza i najczęstsza jest współpraca z ludźmi lub zamiast ludzi?" respondenci zwykle udzielali odpowiedzi: przy paletyzacji, montażu, spawaniu, pakowaniu oraz pick & place. W porównaniu do 2021 roku widzimy po raz pierwszy pojawienie się w tym zestawieniu aplikacji związanej ze spawaniem, której jeszcze dwa lata temu nie wymieniono.
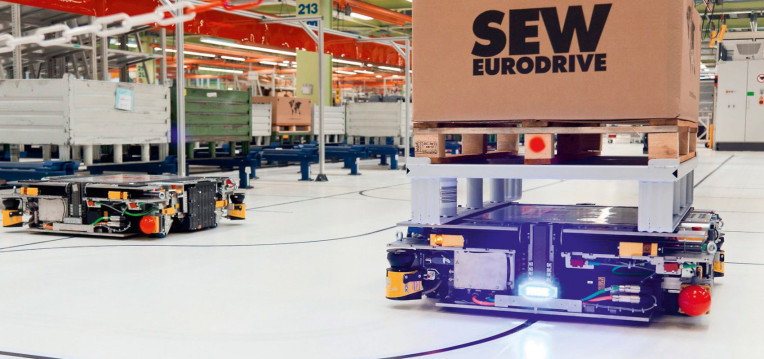
Zastosowania cobotów oraz kwestie wdrożeniowe
Nośność typowych cobotów zaczyna się już od 0,5 kg, a kończy na wartości 40 kg. Maksymalny typowy zasięg wynosi od około 600 mm do około 2000 mm. Poza nielicznymi wyjątkami maszyn specjalizowanych, większość dostawców cobotów oferuje rozwiązania nadające się do wszelkiego rodzaju prac, takich jak spawanie i zgrzewanie, malowanie, montaż, pakowanie, paletyzacja, przenoszenie, uszczelnianie oraz mycie i czyszczenie. Większość robotów dostosowana jest także do manipulowania towarami delikatnymi – występującymi m.in. w przemyśle spożywczym.
Roboty i coboty – od aplikacji standardowych do nietypowych
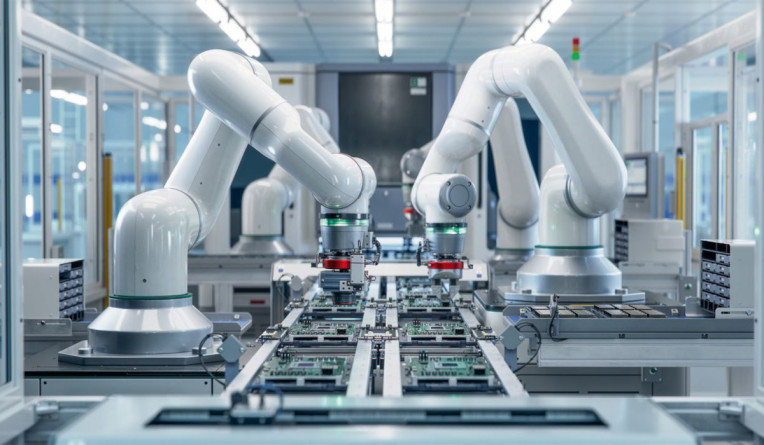
Starzenie się społeczeństw i braki pracowników, których można oddelegować do zadań powtarzalnych i obciążających fizycznie, takich jak montaż czy pakowanie, to dzisiaj częste problemy w przemyśle oraz logistyce magazynowej. Odpowiedzią jest automatyzacja oraz robotyzacja, w przypadku których ma miejsce szybki postęp technologiczny. Dzięki niemu, poza tradycyjnymi robotami przemysłowymi, odgrodzonymi i zaprogramowanymi do wykonywania konkretnego zadania, przybywa tych pracujących z ludźmi ramię w ramię oraz takich, które podejmują decyzje autonomicznie. Roboty popularyzują się również poza fabrykami i magazynami – przykładowo w medycynie. Polecamy znajdujący się w serwisie www.automatykaB2B.pl artykuł o tytule jak powyżej, w którym omawiamy powyższe zagadnienia.
Oferowane urządzenia nadają się także bardzo często do obróbki mechanicznej i polerowania oraz montażu elektroniki i naturalnie obsługi gniazd produkcyjnych. Dostawcy dostarczają bogate wyposażenie dla swoich modeli, m.in. chwytaki, czujniki, osłony i elementy wizyjne.
Naszych respondentów zapytaliśmy o to, jakie obawy żywią pracownicy zakładów, w których wdrażane są roboty współpracujące. Jak można było się spodziewać – najczęściej wymieniana była niepewność własnego zatrudnienia. Tego rodzaju niepokój wśród pracowników potwierdza blisko połowa zapytanych przez nas respondentów.
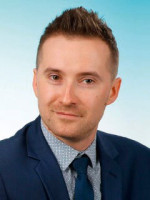
Marcin Śleziak
TFM Robotics
Jakie są najczęstsze zastosowania robotów współpracujących na naszym rynku i w jakich aplikacjach zastępują one standardowe maszyny? Jaka jest motywacja do ich wykorzystywania?
Polska jest jednym z tych krajów Europy, który doświadcza znaczącego wzrostu wskaźnika robotyzacji. Powodem tego jest nie tylko wzrost świadomości u osób odpowiedzialnych za planowanie rozwoju i optymalizację kosztów produkcji w firmach, lecz także ciągle postępujący wzrost płacy minimalnej. Zainteresowanie robotyzacją jest ogromne i będzie w dalszym ciągu wzrastać.
Niestety podmioty z sektora MŚP nie zawsze mają w swoich szeregach odpowiednio wykwalifikowanych pracowników. Mowa tutaj o obsłudze stanowisk zrobotyzowanych pod kątem utrzymania ciągłości ich pracy czy też samego przezbrojenia w razie wystąpienia takiej potrzeby. W takim przypadku idealnym wyborem do rozpoczęcia przygody z robotyzacją jest cobot. Poza możliwością bezpiecznej pracy w bliskim kontakcie z operatorem, roboty współpracujące odznaczają się także prostotą w zakresie ich programowania. Osoba wstępnie przeszkolona po kilku dniach obcowania z nim czuje się już na tyle pewnie, że jest w stanie tworzyć podstawowe aplikacje i realizować założenia procesowe.
Zaprogramowanie odbioru elementu i przeniesienia go w inne miejsce, przejazd po określonej trajektorii z wykonaniem zamierzonych czynności czy też zdefiniowanie prostego procesu z wykorzystaniem systemu kamery 2D do celów detekcji lub kontroli jakości to zakres, którego przyswojenie zajmuje stosunkowo niewiele czasu. W efekcie zastosowania takie jak: załadunek i rozładunek maszyn CNC, montaż, spawanie, paletyzacja czy kontrola jakości produktów, stają się najbardziej popularnymi aplikacjami robotów współpracujących.
Co zmieniły roboty współpracujące, szczególnie w kontekście robotyzacji w niewielkich przedsiębiorstwach oraz firmach, które dotychczas nie stosowały robotów w ogóle?
Roboty współpracujące stanowią obecnie idealną alternatywę dla tradycyjnych robotów przemysłowych, szczególnie w małych i średniej wielkości firmach, które swoją przygodę z robotyzacją dopiero rozpoczynają. Oczywiście ich zastosowanie nie zawsze jest możliwe. Podstawowym uwarunkowaniem jest głównie udźwig ich ramienia, który w porównaniu do robotów przemysłowych jest typowo mniejszy. Niemniej jednak roboty współpracujące cieszą się ostatnio w Polsce coraz większą popularnością, głównie za sprawą wspomnianej łatwości programowania. Prosty i czytelny interfejs graficzny daje każdemu możliwość zaprogramowania mniej lub bardziej skomplikowanej aplikacji w stosunkowo krótkim czasie.
Oczywiście o wiele prościej jest do tematu obsługi systemu cobota podejść osobie technicznej o odpowiednich kwalifikacjach – czuje się ona pewniej i odważniej podchodzi do powierzonych jej zadań. Operator, który z ramieniem robota "podaje sobie rękę" po raz pierwszy, będzie potrzebował dłuższego okresu adaptacji lub alternatywnie dodatkowego szkolenia w zakresie obsługi, które pomoże mu zrozumieć podstawy oraz przyswoić pomocne nawyki.
Chociaż roboty współpracujące słusznie mają opinię maszyn względnie bezpiecznych dla człowieka – nie tylko ze względu na liczne stosowane zabezpieczenia, ale także mniejszą masę i rozmiary w porównaniu do tradycyjnych robotów, nie wszyscy pracownicy czują się w ich pobliżu rzeczywiście bezpiecznie. Inne wątpliwości wyrażone przez naszych respondentów w imieniu pracowników zakładów produkcyjnych to: możliwa awaryjność tych maszyn, trudne serwisowanie i konfiguracja oraz obawy o posiadane przez serwis zakładowy kompetencje w zakresie ich programowania i konfiguracji.
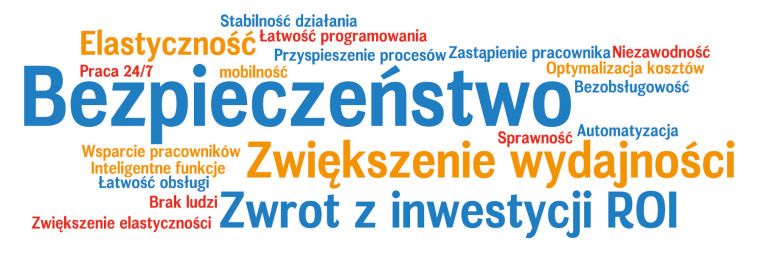
Branża robotów mobilnych
Drugi z obszarów rynku omawianych w bieżącej analizie związany jest z maszynami AGV i AMR. Szacunki ankietowanych dotyczące rynku robotów mobilnych znacząco się różnią między sobą. Oceny liczby dostarczanych maszyn wahają się od 80 do aż 1000 sztuk rocznie, a tempo wzrostu rynku krajowego – od 5% do 80%. W 2021 roku wartość rynku szacowana była przez naszych ankietowanych na 30‒500 sztuk rocznie, natomiast szacunki rocznego wzrostu podawane były w granicach od 10% do 250%. Jednak wyrażane przez pewną część naszych ankietowanych bardzo optymistyczne prognozy przyspieszenia sprzedaży wpisują się w światowe trendy na rynku robotów mobilnych. Z kolei według raportu badawczego wykonanego w 2022 roku przez Market Research Future (MRFR) "Mobile Robotics Market Research Report" do 2030 roku należy spodziewać się wartości rynku AGV wynoszącej 25,3 mld USD przy średnim rocznym tempie wzrostu (CAGR) na poziomie 21,4%. Z kolei według Interact Analysis globalny rynek robotów mobilnych odnotował w 2022 roku aż 53-procentowy wzrost dostaw. Analitycy tej firmy badawczej spodziewają się, że w najbliższych latach przychody na światowym rynku będą rosły średnio o 30‒40% rocznie.
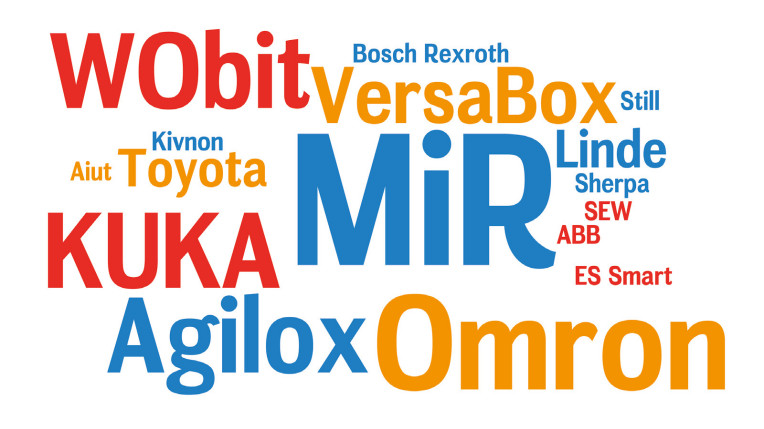
Zdaniem respondentów ankiety do najczęstszych zastosowań AGV należą dwie aplikacje wyróżniające się w sposób szczególny. Pierwsza to produkcja i intralogistyka (91% wskazań respondentów), natomiast drugą jest logistyka magazynowa (85%). Roboty mobilne występują także, choć są już mniej popularne, w takich zastosowaniach jak laboratoria i R&D oraz inne aplikacje komercyjne oraz te poza przemysłem. Porównując sytuację z 2021 rokiem, nie widać znaczących różnic. Wyjątkiem jest pojawienie się w tegorocznym zestawieniu po raz pierwszy pozycji "Laboratoria, R&D, itp.".
Wybierając AGV, klienci zwykle kupują je pojedynczo, aby sprawdzić możliwości tych maszyn, a następnie rozbudowują swoją flotę o nowe jednostki. Taki model inwestycyjny wskazało 75% respondentów, natomiast 19% ankietowanych skłania się ku opcji, w której klienci planują od razu złożony system składający się z wielu AGV pracujących wspólnie. Według 6% ankietowanych klienci kupują te roboty pojedynczo, na sztuki. W porównaniu do 2021 roku widać znaczącą zmianę w zachowaniach odbiorców. Dwa lata temu klienci częściej (45%) planowali od razu zakup całego systemu AVG złożonego z wielu jednostek pracujących wspólnie. Różnicę tę można traktować jako anomalię, wynik zbyt małej próbki danych lub interpretować w ten sposób, że obecnie więcej przedsiębiorstw wprowadza eksperymentalnie AGV do swoich zakładów, tak by sprawdzić ich użyteczność.
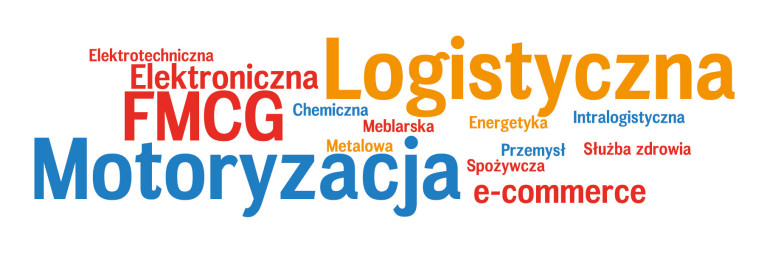
Zdaniem naszych respondentów do najbardziej popularnych producentów AGV oferowanych w Polsce należą marki: MiR, Omron, KUKA, Agilox i WObit. W porównaniu z poprzednim badaniem nie widać żadnej różnicy w czołówce zestawienia.

Według krajowych dostawców cechą, która w pierwszej kolejności przekonuje klientów do korzystania z AGV, jest bezpieczeństwo. Wśród innych ważnych własności robotów mobilnych wymieniane są także: szybki zwrot z inwestycji i poprawa wydajności produkcji. Porównując te wskazania z poprzednim badaniem, nie widać istotnej różnicy. Także dwa lata temu na pierwszym miejscu znajdowało się bezpieczeństwo, natomiast pozostałe cechy plasujące się dość wysoko to: obniżenie kosztów, zwiększenie wydajności i optymalizacja procesów, które można traktować jako synonimy cech wskazanych w bieżących badaniu.
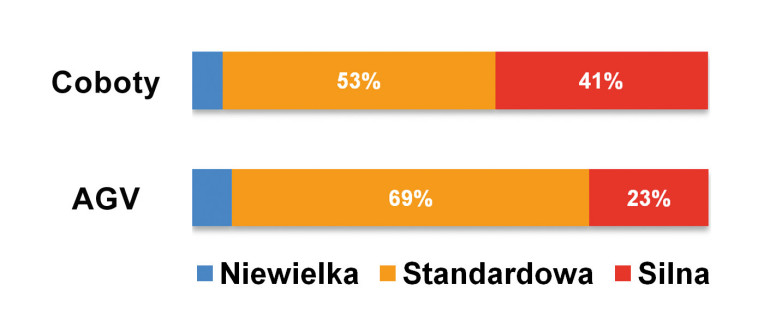
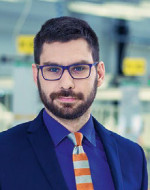
Kamil Niemyjski
igus
Gdzie stosowane są coboty? Co decyduje o wyborze konkretnego rozwiązania przez użytkownika?
Najczęstsze zastosowania to aplikacje typu pick & place, pakowanie i malowanie/lakierowanie. W połączeniu z odpowiednim chwytakiem takie roboty mogą przenosić delikatne elementy, co jest szczególnie istotne w branży spożywczej. Wypierają standardowe roboty przemysłowe w miejscach, gdzie niezbędna jest praca w interakcji z człowiekiem, co ma znaczenie w aplikacjach trudnych do pełnej automatyzacji.
Coraz więcej klientów decyduje się na samodzielne programowanie robotów i samodzielną integrację z maszyną, więc istotne jest zapewnienie odpowiedniego szkolenia. O wyborze konkretnego rozwiązania decyduje w dużej mierze znajomość marki i dostępność rozwiązania na naszym rynku. W dalszej kolejności istotna jest cena i łatwość programowania/integracji oraz zapewnione wsparcie techniczne.
Co zmieniły roboty współpracujące, szczególnie w kontekście robotyzacji niewielkich przedsiębiorstw? Jakie są perspektywy z nimi związane dla ich dostawców i integratorów?
Użytkownicy postrzegają coboty jako rozwiązania stosunkowo proste do wdrożenia i niedrogie – szczególnie jeśli weźmiemy pod uwagę czas zwrotu z inwestycji. W związku z tym firmy, które dotychczas nie stosowały w ogóle robotów, teraz decydują się automatyzować z ich pomocą pierwsze procesy w swoich fabrykach. Rynek automatyzacji stale się rozwija, problem z pozyskaniem pracowników nadal jest aktualny, a jednocześnie próg wejścia w inwestycję nie podnosi się, a nawet obniża. W efekcie widać coraz więcej szans na rozwój branży robotów współpracujących w Polsce.
Parametry AGV i przyszłość branży
Jednym z najważniejszych parametrów AGV jest ich udźwig. Naszych respondentów zapytaliśmy o to, jakie rodzaje robotów są najpopularniejsze. Okazuje się, że większość klientów zainteresowana jest udźwigiem do 1 tony, ale część dostawców otrzymuje także zapytania o rozwiązania z udźwigiem powyżej tej wartości – nawet o maszyny pracujące z masami około 10 ton.
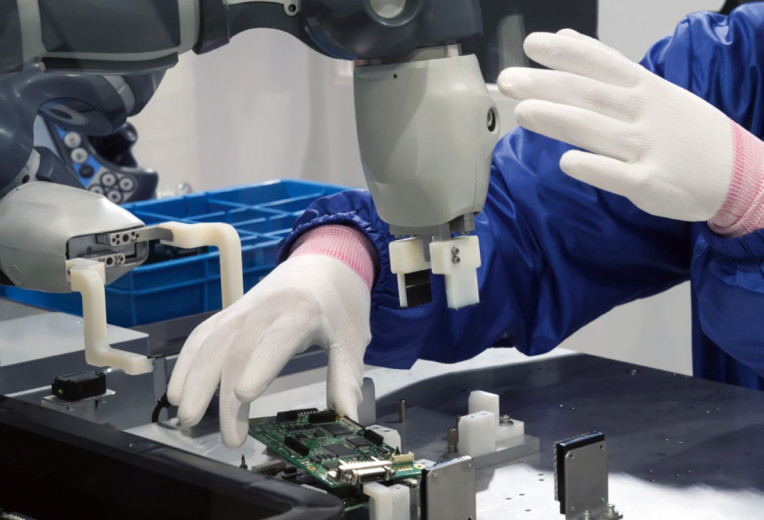
Obecnie wszyscy dostawcy oferują możliwość pracy w systemie wielu wózków jednocześnie w liczbie powyżej 100 maszyn. Zrobotyzowane wózki prawie wszystkich prezentowanych w naszym zestawieniu dostawców mają także dostępną funkcję dowolnego ruchu kół (koła omnikierunkowe). Większość oferuje też dodatkowe wózki transportowe do palet, wózki z podajnikami rolkowymi lub z regałami oraz adaptery do montażu robotów na AGV / inne adaptery.
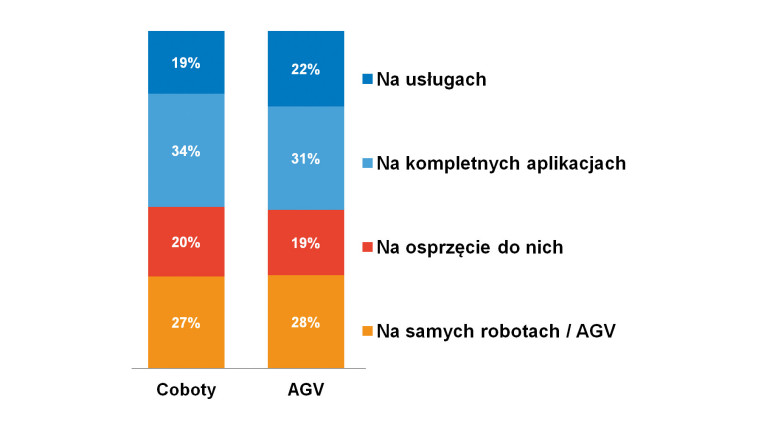
Naszych respondentów zapytaliśmy w dalszej części badania o to, czy AGV zastępują ich zdaniem przenośniki. Zadaliśmy także pytanie o to, co zapewnia przewagę robotom mobilnym nad tradycyjnymi sposobami transportu wewnątrzzakładowego. Odpowiadając, respondenci zwrócili uwagę na fakt, iż AGV są bardziej elastyczne aplikacyjnie i pozwalają obniżyć koszty. Do istotnych zalet AGV należy także zdolność do łączenia gniazd produkcyjnych w ciągach komunikacyjnych bez kosztownych wind, dzięki czemu można łatwo dopasować je do procesu produkcyjnego.
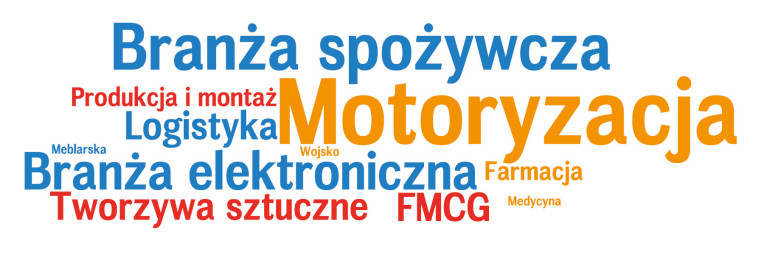
Sławomir Kowalski
Bosch Rexroth
Jakie są cechy charakterystyczne cobotów?
Roboty współpracujące mają wiele znaczących cech odróżniających je od tradycyjnych robotów przemysłowych. Przede wszystkim chodzi o bezpieczeństwo, jakie zapewniają one w interakcji z człowiekiem. Postęp technologiczny i zastosowane systemy bezpieczeństwa sprawiły, że pracownik może bezpiecznie współpracować z takim robotem. Warto również zaznaczyć, że coboty cechuje bardzo duża elastyczność w dostosowaniu się do warunków produkcyjnych. W przeciwieństwie do robotów przemysłowych, zmiana miejsca pracy i przeprogramowanie cobota jest możliwe w bardzo krótkim czasie, nawet bez angażowania wykwalifikowanych automatyków.
Jak dobrać robota współpracującego?
Przy wyborze konkretnego rozwiązania warto dokonać wstępnej analizy potrzeb produkcyjnych i warunków tam panujących. Czynności wymagające ciągłej i powtarzalnej pracy to najlepsze miejsca, w których można wykorzystać takie maszyny. Cobot idealnie sprawdzi się we współpracy z centrami obróbczymi i maszynami CNC – w podawaniu i odbieraniu elementów z obrabiarki, a także w aplikacjach pakowania produktów do opakowań zbiorczych i w paletyzowaniu.
Jak istotne są kwestie wsparcia ze strony dostawcy i serwisu?
Ostatnią kwestią związaną z inwestycją w robota współpracującego jest jego uruchomienie na linii produkcyjnej oraz gwarancja i serwis posprzedażowy. O ile gwarancja jest sprawą uregulowaną prawnie, o tyle serwis i uruchomienie robota pozostają kwestią, o której kupujący powinien rozmawiać z dostawczą. Uruchomienie samego robota nie jest trudne. To sprawy związane z podłączeniem robota do linii produkcyjnej i współpracy w cyklu produkcyjnym mogą być problematyczne. Dlatego, biorąc pod uwagę zakup robota, konieczne jest przeanalizowanie swojej decyzji pod kątem współpracy wybranego rozwiązania z linią produkcyjną.
W kwestii pytania zasadniczego, tj. czy AGV zastąpią przenośniki, większość respondentów skłania się ku tezie, że przyszłość należy wyłącznie do robotów mobilnych, bo maszyny te dają zakładom nowe możliwości, które z każdym rokiem zyskują na znaczeniu. Automated Guided Vehicles zapewniają m.in. elastyczność oraz pozwalają na transport przez miejsca, których nie można zabudować – takie jak np. bramy czy drogi pożarowe. Nie zabrakło jednak głosów, że AGV nie są w stanie zastąpić tradycyjnych środków transportu i jedynie będą je uzupełniać.
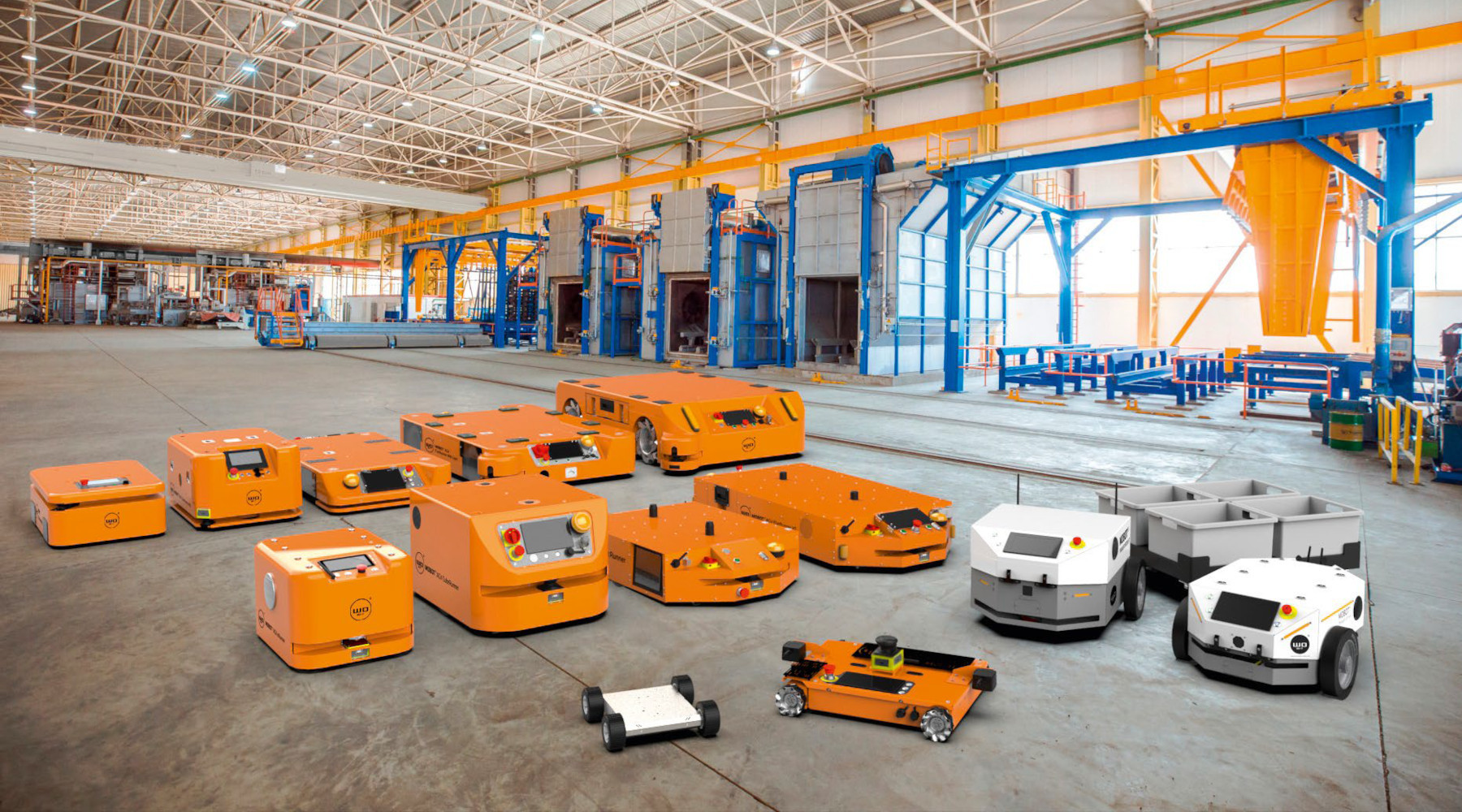
Obawy związane z AGV są podobne jak w przypadku robotów współpracujących. Najczęściej powtarza się niepokój o miejsca pracy, które nowe, coraz bardziej inteligentne i działające niezależnie od człowieka maszyny będą zabierać ludziom zajmującym się obecnie transportem towarów tradycyjnymi wózkami. Pojawiają się także obawy o bezpieczeństwo działania tych maszyn i pytania, czy nie będą one powodować kolizji z obiektami lub, co ważniejsze – z ludźmi poruszającymi się lub pracującymi w pobliżu ciągów komunikacyjnych.
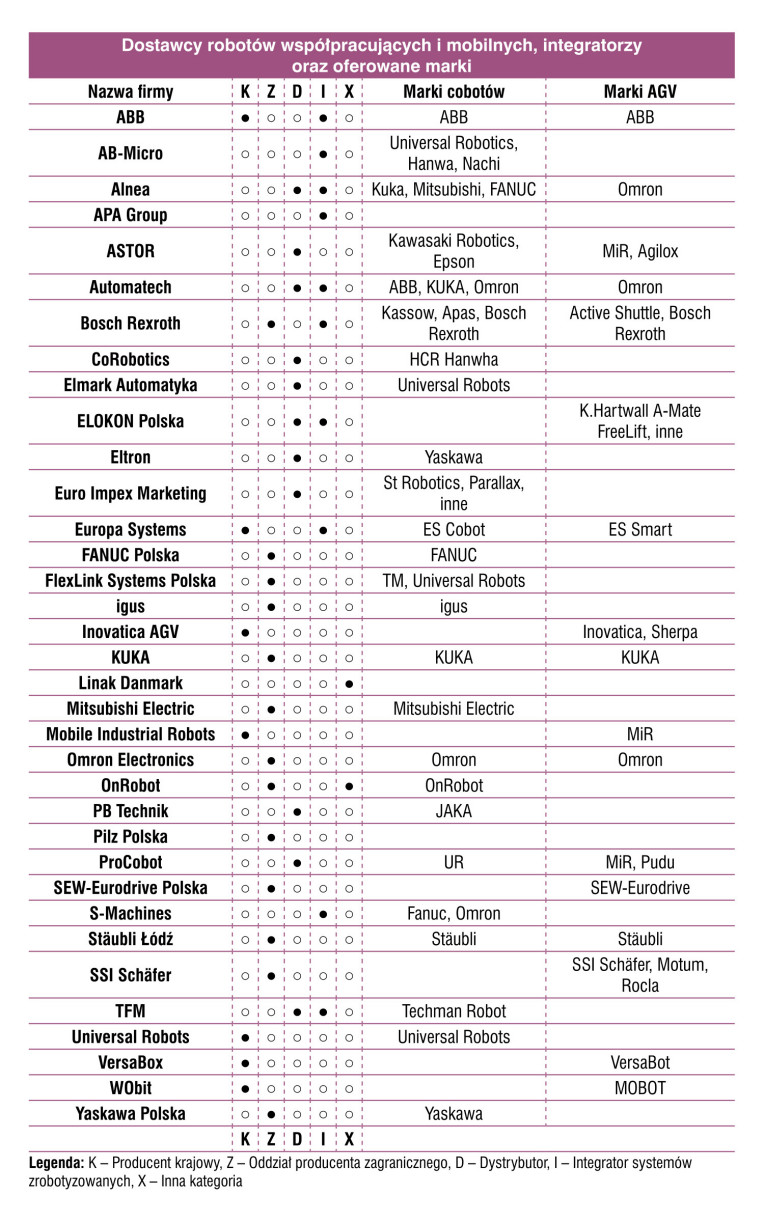
Finalnie krótko o przyszłości, a dokładniej o branżach, które są dla dostawców robotów najbardziej perspektywiczne. Zdaniem respondentów są nimi: logistyka, motoryzacja i, w nieco mniejszym stopniu, FMCG. Uzupełniając te spostrzeżenia, warto dodać, że identyczne branże wskazywali dostawcy w poprzednim badaniu rynku.
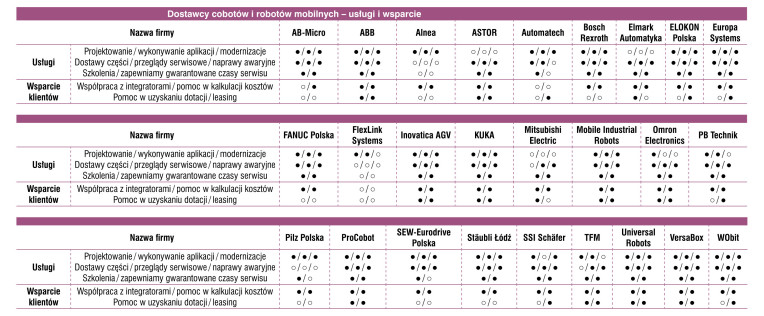
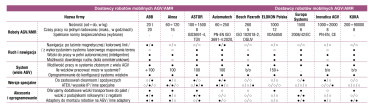
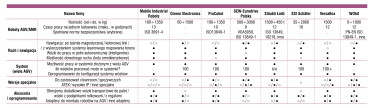