ATEX oraz bezpieczeństwo pracowników
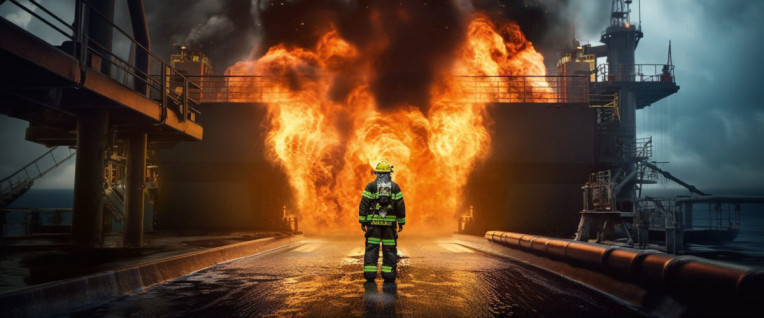
Branże procesowe, w szczególności chemiczna i petrochemiczna, gazownicza oraz wydobywcza, to obszary częstego występowania zagrożeń spowodowanych istnieniem atmosfery wybuchowej. Wymagane jest w nich stosowanie różnorodnych technicznych środków zabezpieczających, którymi są komponenty oraz urządzenia ATEX, a także odpowiednie tworzenie i użytkowanie systemów czy instalacji technicznych. Tematyka z tym związana jest wysoce specjalistyczna, zaś na obsługę tych rynków ukierunkowała się spora grupa firm branżowych.
Bezpieczeństwo pracowników w przemyśle
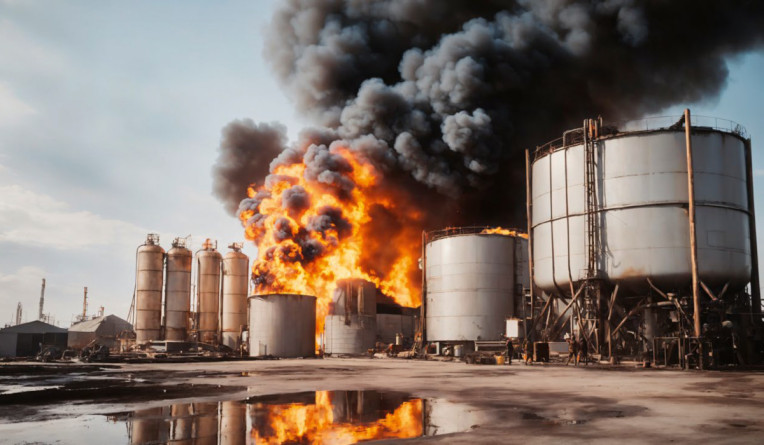
Pracownicy w przemyśle narażeni są na uciążliwe warunki pracy i wypadki. Ich skutkiem są choroby zawodowe, obrażenia, urazy, a w skrajnych przypadkach nawet śmierć. By poprawić bezpieczeństwo na stanowiskach pracy, wprowadza się zabezpieczenia i procedury, a personel wyposaża w środki ochrony indywidualnej, jak okulary, maski, rękawice, odzież. W artykule dokonujemy przeglądu tych rozwiązań, w tym nowych technologii, które także coraz częściej wykorzystuje się w BHP. Polecamy znajdujący się w serwisie www.automatykaB2B.pl artykuł "Bezpieczeństwo pracowników w przemyśle" , w którym omawiamy powyższe zagadnienia.
Dyrektywy ATEX
Zanim omówimy wyniki badania rynku, krótkie wprowadzenie do przepisów dotyczących tematyki związanej z obszarami zagrożonymi wybuchem oraz stosowanymi zabezpieczeniami. Przez lata w krajach Unii Europejskiej kluczowe były tu dwie dyrektywy. Pierwsza, 94/9/WE (ATEX 95), zawierała wytyczne dla producentów sprzętu używanego w miejscach zagrożonych wybuchem. Szczegółowe wymagania odnajdziemy w normach zharmonizowanych z tą dyrektywą, takich jak PN-EN 60079 Atmosfery wybuchowe oraz PN-EN 13463 Urządzenia nieelektryczne w przestrzeniach zagrożonych wybuchem. Druga dyrektywa, 99/92/WE (ATEX 137), skupiała się na minimalnych wymaganiach w zakresie bezpieczeństwa i ochrony zdrowia pracowników w miejscach, gdzie istnieje ryzyko atmosfery wybuchowej. Ustalono w niej również procedury oceny ryzyka wybuchu oraz klasyfikację miejsc pracy pod kątem ryzyka eksplozji.

W 2016 roku dyrektywa 94/9/WE została zastąpiona przez 2014/34/UE (ATEX 114), która dotyczy urządzeń i systemów ochronnych używanych w miejscach o potencjalnym ryzyku wybuchu. Nakłada ona wymagania na producentów urządzeń, zaś polskie prawo dostosowano do tych nowych wytycznych poprzez Rozporządzenie Ministra Rozwoju. Warto podkreślić, że choć ATEX 114 zastąpił wcześniejszą dyrektywę, nie wprowadził znaczących zmian w kwestii produktów, ich klasyfikacji czy procedur oceny zgodności. Zmiany dotyczyły głównie obowiązków jednostek notyfikowanych i firm wprowadzających produkty na rynek.

Z kolei dyrektywa 99/92/WE mówiąca o warunkach pracy w miejscach o potencjalnym ryzyku wybuchu, znana od 1999 roku jako ATEX 137, została zaktualizowana i funkcjonuje obecnie jako ATEX 153. Oznacza to, że w ciągu lat przepisy dotyczące bezpieczeństwa w miejscach zagrożonych wybuchem były sukcesywnie dostosowywane do nowych wymagań i technologii, dbając o optymalne zabezpieczenie osób oraz urządzeń. Dyrektywa ta, podobnie jak ATEX 137, nakłada wymania na użytkowników urządzeń oraz pracodawców.
Duża czystość i urządzenia specjalistyczne
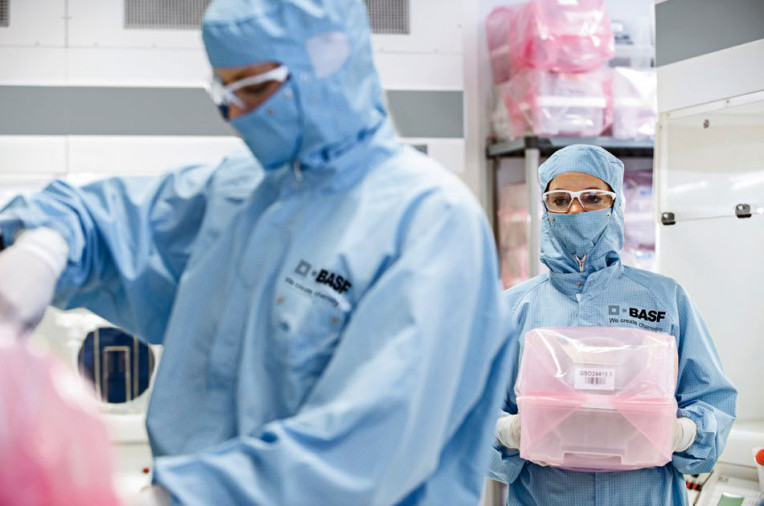
Duża czystość i urządzenia specjalistyczne
Produkty do spożywania, wyroby inwazyjne w kontakcie z ciałem oraz te, których jakość pogarsza zanieczyszczenie surowców i procesów (żywność, leki, wyroby medyczne, jak igły iniekcyjne, układy scalone) wymagają, aby w produkcji przestrzegać standardów higieny, a nawet zapewnić dużą czystość. Chcąc spełnić te warunki, wprowadza się specjalne procedury, techniki obróbki i korzysta z urządzeń w wersji higienicznej, czystych pomieszczeń i specjalistycznych maszyn.
W wielu branżach zagrożenie stanowią nie tylko drobnoustroje chorobotwórcze i brud, ale wszystkie cząstki, nawet te niewidoczne gołym okiem o rozmiarach rzędu mikro-, a nawet nanometrów. Przykład to przemysł półprzewodnikowy, w którym okazują się większe niż rozdzielczość procesów technologicznych, dlatego gdy zanieczyszczą sprzęt lub płytkę półprzewodnikową, mogą zniszczyć miliony podzespołów. Duża czystość jest także wymagana w biotechnologii, nanotechnologii, produkcji elementów optycznych, jak miniaturowe kamery smartfonów oraz lasery do zastosowań specjalnych (medycznych, kosmicznych), branży medycznej, szczególnie w badaniach na przykład nad wykorzystaniem komórek macierzystych, w terapii genowej i branży farmaceutycznej, na przykład produkcji szczepionek. By takie warunki zapewnić, korzysta się z izolowanych pomieszczeń – cleanroomów. Dużą czystość pozwalają w nich uzyskać i utrzymać stosowane rozwiązania konstrukcyjne i materiały, sposób organizacji przestrzeni, procedury użytkowania i kontrola warunków środowiskowych (temperatury, wilgotności, ciśnienia, przepływu powietrza). Dzięki nim w cleanroomach ogranicza się przenikanie z zewnątrz cząstek zanieczyszczeń i eliminuje ich źródła wewnętrzne oraz zapobiega ich zatrzymywaniu.
Elementy konstrukcyjne cleanroomów
Standard wykonania cleanroomów musi być wyższy od przeciętnego. Dotyczy to typu i wykończenia powierzchni ścian, sufitów, drzwi, zapewniających łatwe czyszczenie. Popularne są modułowe systemy ścienne wykorzystujące panele z powlekanej stali lub aluminiowe. Spotykane są także ściany betonowe odpowiednio wykończone farbami o wyższej odporności na zmywanie, trwałości, ograniczonym pyleniu. Niedozwolone są ostre kąty, zastępowane przez zaokrąglone rogi, które można skuteczniej wyczyścić, a kanty trzeba zabezpieczyć przed obijaniem. Wykończenie sufitów musi być takie jak ścian. Jeśli chodzi o podłogi, popularne są winylowe płytki z wklęsłymi narożnikami zapewniającymi ciągłość połączenia ze ścianą. Okna wewnętrzne z kolei muszą być wykonane ze szkła lub szkła akrylowego odpornego na uderzenia. W cleanroomach panuje na ogół nadciśnienie, wchodzi się więc do nich zwykle przez śluzy powietrzne wymagane do utrzymania różnicy ciśnień. Uszczelnienia drzwi muszą być hermetyczne. W tym zastosowaniu popularne są uszczelki neopremowe, niezalecane są natomiast te z pianki gumowej, które szybko się niszczą i kruszą. Drzwi wahadłowe powinny mieć mechanizm samozamykający. Przesuwane, z których korzysta się w razie ograniczeń przestrzennych i by usprawnić przejście między pomieszczeniami o tej samej klasie czystości, muszą być specjalne zaprojektowane, ponieważ ich mechanizm może być źródłem zanieczyszczeń.
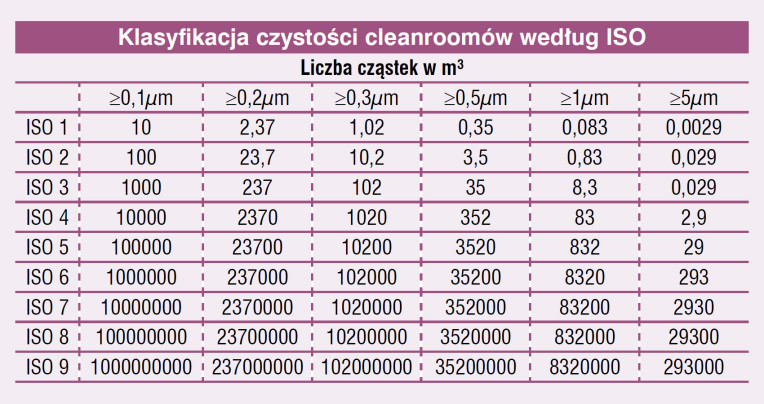
Projektowanie cleanroomów
W sektorach najbardziej sterylnych (ISO 1) akceptowalne są tylko 2 i 10 cząsteczek o średnicach odpowiednio 0,2 μm i 0,1 μm na metr sześcienny powietrza, natomiast na przykład w tych zaliczanych do ISO 7 dopuszczalna jest obecność tych w rozmiarze 0,5 μm, 1 μm i 5 μm w liczbie odpowiednio 352 tys., ponad 83 tys. oraz prawie 3 tys. W tabeli przedstawiamy poziomy czystości zalecane dla różnych zadań produkcyjnych – przykładowo w produkcji półprzewodników jest to ISO 5, a w pakowaniu wyrobów medycznych ISO 7–8. Pomiędzy sąsiadującymi, połączonymi przestrzeniami różnica poziomów czystości nie może być większa niż dwa rzędy wielkości. Określić też trzeba optymalną różnicę ciśnień między strefami o różnej czystości. Musi być wystarczająca, żeby zapobiec przenikaniu zanieczyszczeń, lecz zarazem za wysoka oznacza wyższe koszty, trudności w kontroli i konieczność używania większej siły do otwierania i zamykania drzwi. Kolejna decyzja projektowa dotyczy szybkości wymiany powietrza, która zależy od: stopnia zajętości i aktywności w pomieszczeniu, nasilenia generowania w nim cząstek i różnicy ciśnień względem pomieszczenia przylegającego. Trzeba także znaleźć i oszacować nieuniknione wycieki powietrza z/do cleanroomu (przez gniazdka elektryczne, oprawy oświetleniowe, ramy okienne, ramy drzwi). Ważne kwestie to też: optymalne dla potrzeb procesów i komfortu pracowników temperatura, wilgotność, z uwzględnieniem jej wpływu na elektryczność statyczną (i wpływ tej na przyczepność cząstek) i wrażliwość komponentów i materiałów wykorzystywanych w cleanroomie, poziom hałasu i wibracji.
Zasady zachowania w cleanroomach
Nie tylko projektując cleanroomy, ale także w nich przebywając, trzeba przestrzegać zasad wymuszanych ich specyfiką. Przede wszystkim personel zobowiązany jest nosić specjalne ubrania, które zakłada w przedsionku. Z niego do strefy czystej przechodzi przez śluzę powietrzną wyposażoną w prysznic powietrzny. Rękawiczki i maseczki na twarz oraz nakrycia głowy są standardem w prawie każdym pomieszczeniu czystym. Noszone są także fartuchy i kombinezony. Pracownicy muszą też przestrzegać określonych zasad zachowania. Na przykład nie mogą wnosić rzeczy osobistych, jak klucze, portfele, telefony, biżuteria, a jeśli jest to naprawdę konieczne, muszą je zakrywać odzieżą ochronną. Zakazane jest jedzenie, picie, palenie i żucie gumy, a ponadto noszenie makijażu i używanie perfum. Palić nie wolno także bezpośrednio przed wejściem – powinno się odczekać co najmniej 20 minut, żeby resztki dymu mogły się ulotnić z ubrania i skóry. Obowiązuje też wymóg stosowania płynów i mydeł zmniejszających łuszczenie się naskórka. Zabronione jest wykonywanie szybkich ruchów, jak bieganie i szybkie chodzenie, by nie wzburzać powietrza. Pracownik nie powinien wchodzić, jeżeli źle się czuje albo podejrzewa, że jest chory. Zakazane jest siadanie na i opieranie się o sprzęty i powierzchnie robocze. Dotykać należy tylko tych niezbędnych do wykonania pracy. Nie wolno dotykać twarzy ani włosów dłońmi w rękawiczkach. Zabronione jest pisanie na sprzęcie, odzieży i noszenie odzieży ochronnej poza cleanroomem. Od personelu wymaga się też oczywiście przestrzegania zasad higieny osobistej.
Więcej informacji
Powyższe informacje to część treści zawartych w artykule "Wysoka czystość i urządzenia specjalistyczne". Polecamy to opracowanie, można jest znaleźć w serwisie www.automatykaB2B.pl.
Koniunktura na rynku
Ostatnie lata nie przyniosły większych zmian koniunktury w branży. Pandemia, przypomnijmy na podstawie wyników badań sprzed kilku lat, jedynie w pewnym stopniu wpłynęła na omawiany rynek. Według 40% uczestników tamtego badania sytuacja pozostawała stabilna, choć też część respondentów wskazała na problemy z dostawami, szczególnie w zakresie komponentów elektronicznych. Obecnie sytuacja na omawianym rynku jest pozytywna – ponad 90% respondentów oceniło ją jako dobrą lub bardzo dobrą.
Tradycyjnie trudne było określenie wartości rynku, głównie ze względu na różnorodność oferowanych na nim produktów. Tworzą one szerokie spektrum urządzeń automatyki i sterowania, elektrycznych oraz elektrotechnicznych. Respondenci, zapytani o roczne obroty w branży dystrybucji produktów ATEX w Polsce, podawali tu kwoty od kilku milionów do ponad miliarda złotych (w tym w zależności od grupy, tj. I lub II). Takie wskazania w oczywisty sposób nie dają możliwości wyliczenia średniej czy jakiejkolwiek innej miary statystycznej.
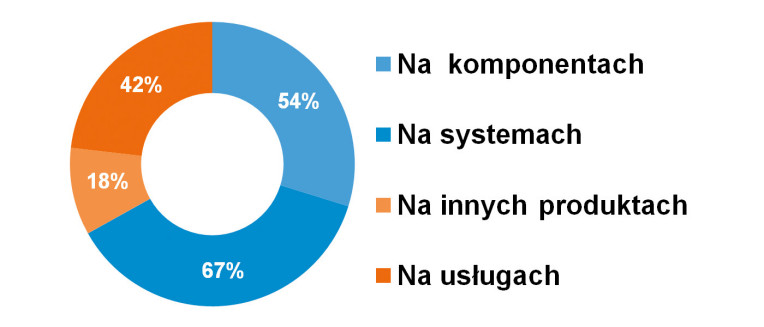
Udało się natomiast uzyskać pojedyncze oszacowania wartości sprzedaży wybranych grup produktów. Takimi są przykładowo: tablety przemysłowe ATEX (2 mln zł rocznie), obudowy dla AKPiA (5 mln), sygnalizatory (50 mln). Dodajmy do tego wyniki z poprzednich analiz: bariery separacyjne sygnałów (kilkadziesiąt mln zł rocznie), przetworniki pomiarowe ATEX (10‒20 mln), przekaźniki (5 mln), silniki do pracy w strefach zagrożonych wybuchem (50 mln). Wartości te należy jednak traktować z dużą rezerwą, bowiem są to w istocie pojedyncze wskazania ankietowe.
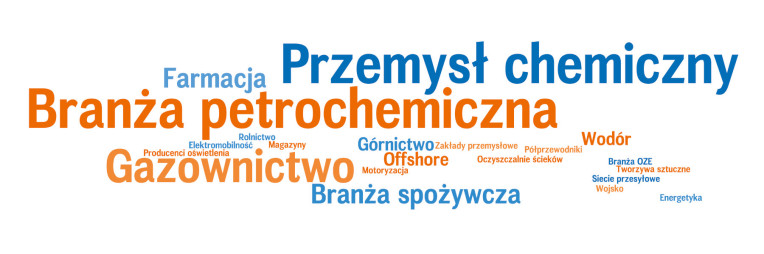
Rozwój i przyszłość branży
Jakie są trendy technologiczne w branży? Ze względu na fakt, że obejmuje ona wiele grup produktów i rynków końcowych, trudno wskazać tu konkretne – takie jak energooszczędność w przypadku napędów czy rozwój Ethernetu przemysłowego w domenie urządzeń komunikacyjnych. Respondenci pytani o zmiany w tym zakresie wskazywali m.in. miniaturyzację urządzeń i komponentów, zwiększanie zakresu temperatur pracy oraz ogólny rozwój elektroniki i innych aspektów technologicznych. Pojawiły się też kwestie komunikacyjne – zarówno zwiększanie możliwości pracy bezprzewodowej, jak też łączności z systemami nadrzędnymi.
Chociaż zmiany są widoczne, część respondentów naszych badań zauważa, że w omawianym zakresie branża rozwija się stosunkowo powoli. Według nich innowacje to często de facto modyfikacje i unowocześnianie już istniejących rozwiązań, zaś rynek jest ostrożny we wprowadzaniu gruntownych zmian. Aczkolwiek jest to zrozumiałe, biorąc pod uwagę specyfikę i wymagania stawiane produktom przeznaczonych do pracy w strefach zagrożonych wybuchem.
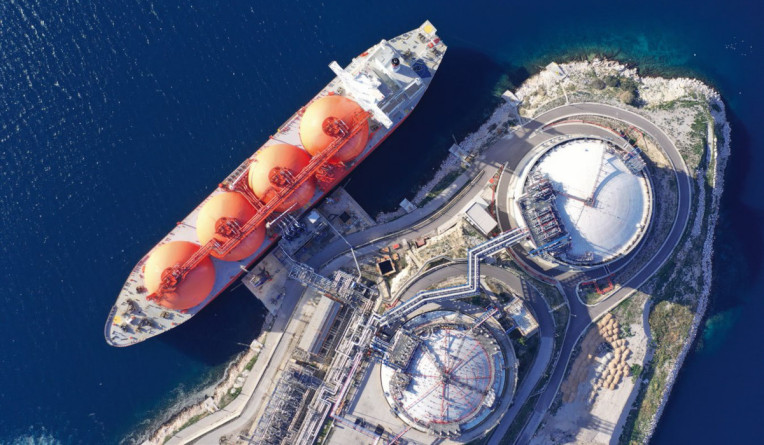
Jak określane są wymagane poziomy zabezpieczeń?
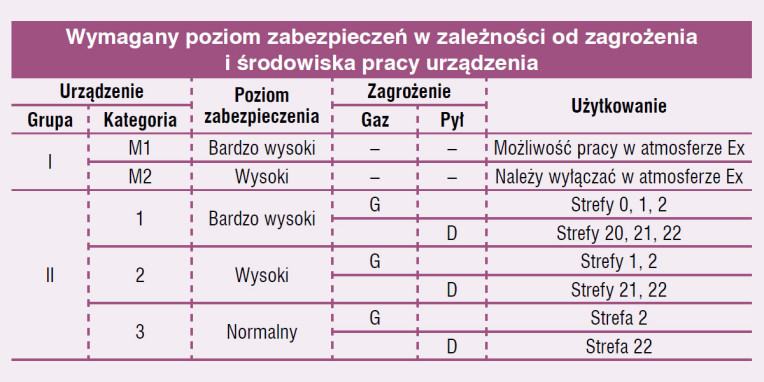
W celu zapewnienia bezpieczeństwa pracowników i infrastruktury, w miejscach możliwego występowania atmosfery wybuchowej stosuje się odpowiednie zabezpieczenia techniczne. Są one tak projektowane i produkowane, aby spełniać konkretne, ściśle określone wymogi. Jednocześnie urządzenia i inne produkty mają oznaczenia, które informują o ich specyfikacji i możliwościach funkcjonowania w określonych warunkach.
Podstawowym narzędziem związanym z doborem jest określona w dyrektywie klasyfikacja miejsc pod względem zagrożenia występowaniem atmosfery wybuchowej. Wyróżnia się tu strefy: 0, 1 i 2 dla gazów i par oraz 20, 21 i 22 dla pyłów. Każda strefa oznacza różne poziomy zagrożenia, począwszy od miejsc, w których atmosfera wybuchowa jest obecna prawie stale (strefa 0 i 20), po miejsca, gdzie takie zagrożenie jest minimalne (strefa 2 i 22).
W dalszej kolejności wskazać można dwie główne grupy urządzeń. Grupa I przeznaczona jest głównie do górnictwa, gdzie głównym zagrożeniem jest metan i pył węglowy. Grupa II to urządzenia do zastosowań w innych sektorach przemysłu, poza górnictwem. W ramach tych dwóch głównych grup urządzeń dokonuje się dalszej specyfikacji, oznaczanej kategoriami M1, M2 w grupie I oraz odpowiednimi kategoriami w grupie II. Kategorie te odnoszą się do poziomu bezpieczeństwa, jakie urządzenie zapewnia w sytuacji awaryjnej.

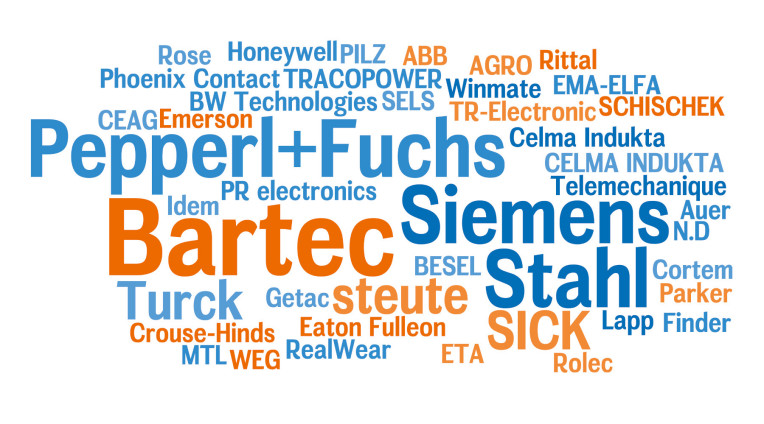
Rozwój branży ATEX w Polsce jest nierozerwalnie związany z kilkoma kluczowymi sektorami gospodarki. Do takich należy przede wszystkim sektor chemiczny, gdzie charakter produkcji oraz wykorzystywane substancje wymagają stosowania technologii przeciwwybuchowych. Tak samo jest w branży petrochemicznej, która, ze względu na specyfikę produkcji oraz potencjalne zagrożenia, wymaga zapewnienia najwyższego poziomu bezpieczeństwa pracowników i infrastruktury. Trzeci z kluczowych rynków to branża gazownicza, co obejmuje wydobycie, przetwarzanie, przechowywanie oraz transport i przesył gazów.
Powyższe trzy sektory wymieniane były najczęściej również jako najbardziej perspektywiczne rynki z punktu widzenia dostawców produktów i usług działających w kraju. Do tego należy dodać przemysł wydobywczy. Górnictwo, choć mierzy się z wieloma wyzwaniami, wciąż stanowi ważny sektor dla branży ATEX – szczególnie w kontekście istniejącej już infrastruktury. Wymieniane tu były również inne branże jak spożywcza i farmaceutyczna. Dodatkowo, co stanowi pewne nowum, zaobserwowaliśmy kilka wskazań dotyczących technologii wodorowych.
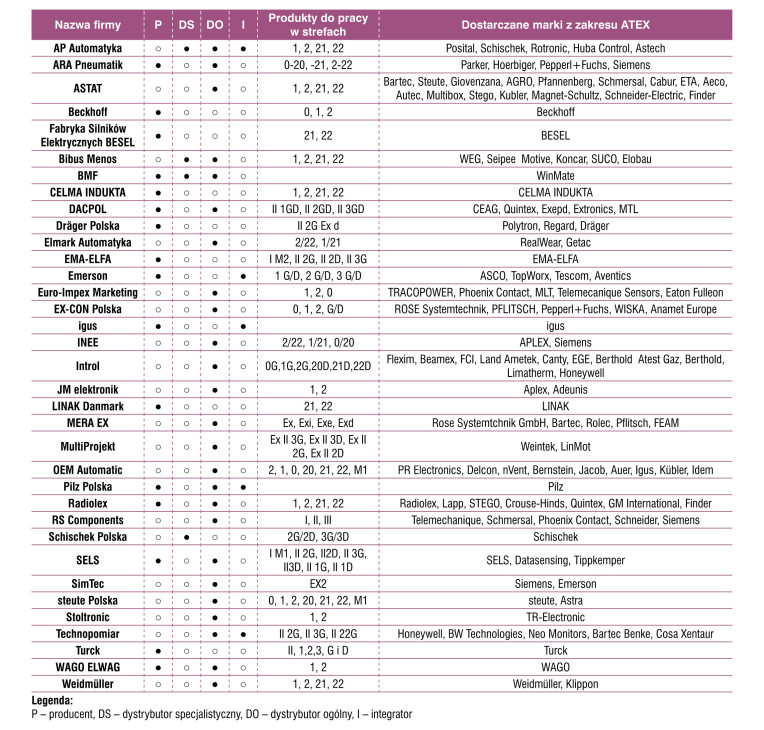