CZĘŚĆ II: SYSTEM USUWANIA CO2 - WDROŻENIE
Zakład KRIO Odolanów zbudowany został na początku lat 70. zeszłego wieku i jest oddziałem spółki Polskie Górnictwo Naft owe i Gazownictwo S.A. Usytuowanie i cel jego istnienia zdeterminowały odkrycia na Niżu Polskim złóż zaazotowanego gazu ziemnego o niskiej zawartości metanu. Zakład głównie zajmuje się przetwarzaniem zaazotowanego gazu ziemnego w gaz wysokometanowy, ponadto w procesie uzyskiwane są takie produkty jak: skroplony gaz ziemny LNG, gazowy i ciekły hel oraz ciekły azot.
Technologia stosowana w zakładzie opiera się na procesach kriogeniczne (niskotemperaturowych). Kriogeniczne przetwarzanie polega na schładzaniu gazu do niskich temperatur (poniżej temperatury wrzenia), dzięki czemu możliwe jest w kolumnie destylacyjnej odseparowanie z mieszaniny gazów czystego azotu i helu. Zanim gaz trafi do kolumny kriogenicznej, wcześniej musi przejść przez trzystopniowy proces wstępnej obróbki, którego celem jest eliminacja: CO2, wilgoci oraz zawartości ciężkich węglowodorów.
Proces przygotowawczy wymagany jest ze względów technologicznych - kolumna kriogeniczna przystosowana jest do pracy z gazem o odpowiednich parametrach, w przeciwnym wypadku może dojść do zanieczyszczenia kolumny i w konsekwencji zatrzymania całego procesu. Poniżej opisano projekt automatyzacji sekcji usuwania CO2 (nazywaną sekcją MEA), która jest pierwszym stopniem procesu wstępnej obróbki.
SEKCJA MEA
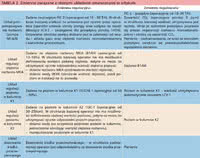
TABELA 2. Zmienne związane z różnymi układami omawianymi w artykule
Zadaniem sekcji jest usunięcie dwutlenku węgla z mieszaniny gazu. W tym celu w strumień gazu w przeciwprądzie podawany jest strumień monoetanoloaminy, która ma zdolności absorpcji dwutlenku węgla. Absorpcja następuje w kolumnie K1 (patrz rys. 1), skąd bogaty w CO2 roztwór monoetanoloaminy (nazywany MEA) przelewany jest do kolumny K2.
Tam z kolei bogate MEA podgrzewane jest do temperatury wrzenia, w wyniku czego uwalniane jest CO2 (roztwór MEA jest regenerowany). Następnie ubogie, oczyszczone z CO2, MEA przepompowywane jest ponownie do kolumny K1.
Proces oczyszczania monoetanolaminy wymaga ciągłego dostarczania energii w postaci ciepła na podgrzanie bogatego w CO2 MEA do temperatury wrzenia (regeneracja MEA). Zadanie optymalizacji pracy sekcji MEA rozumiane jest jako usprawnienie pracy procesu mające przynieść korzyści ekonomiczne w postaci:
- zmniejszenie ilości zużytego gazu na każdym z ciągów technologicznych o 5%,
- obniżenie średniej temperatury roztworu monoetanoloaminy o około 1°C, co przekłada się na mniejszą ilość ciepła wprowadzanego do układu i tym samym podwyższenie sprawności części zimnej instalacji oczyszczania gazu oraz zwiększenie elastyczności procesów technologicznych w konsekwencji umożliwiające zwiększenie produkcji LNG,
- spowolnienie degradacji roztworu MEA.
Ponadto w pełni zautomatyzowany i zoptymalizowany proces podwyższy komfort pracy operatora oraz bezpieczeństwo pracy instalacji. Zautomatyzowanie pracy układu odciąży operatora od ciągłego monitorowania procesu i konieczności dokonywania ręcznej modyfikacji parametrów. Optymalne parametry pracy to również, oprócz zalet finansowych, korzyści wynikające z minimalizacji ryzyka wystąpienia awarii instalacji.
GŁÓWNE PĘTLE REGULACYJNE
Sekcja usuwania CO2 z punktu widzenia automatyki jest obiektem wielowymiarowym, co oznacza, że poprawny przebieg procesu uzależniony jest od wielu czynników (zmiennych procesowych). Stworzenie struktury regulacji zdolnej do poprawnego prowadzenia procesu w sposób w pełni automatyczny i jednocześnie optymalny wymagało zidentyfikowania krytycznych pętli regulacyjnych oraz zmiennych procesowych.
Dodatkowo konieczne było określenie zależności pomiędzy zmiennymi procesowymi oraz zdefiniowanie limitów wartości, które zmienne procesowe mogą przyjmować. Poniżej dokonano analizy obiektu pod kątem instalacji układu optymalizacji pracy, przy czym zmienne regulacyjne oznaczają zmienne, które będą wyliczane przez nadrzędny układ, jakim jest optymalizacja.
Układ podgrzewania (podgrzewacz E1)
Jest to układ odpowiedzialny za dostarczenie ciepła do procesu w celu regeneracji roztworu monoetanoloaminy. Ciepło dostarczane jest przez piec gazowy (podgrzewacz E1), który podgrzewa olej (nośnik energii). Ten ostatni ogrzewa roztwór MEA przez układ specjalnych wymienników (patrz tabela 1).
Układ przepompowywania roztworu (pompa M1A/B)
Odpowiada on za przepompowywanie roztworu z kolumny regeneracyjnej K2 do kolumny K1, a więc tej, w której następuje oczyszczanie gazu (absorpcja CO2 z gazu wsadowego). Zmienne związane z tym układem oraz kolejnymi niżej omówionymi przedstawiono w tabeli 2.
Układ regulacji stężenia roztworu MEA
W układzie bazowym stężenie roztworu MEA utrzymywane jest ręcznie przez operatorów w zakresie 13 do 16%. Wartość stężenia jest zmienna, a dynamika zmian jest bardzo złożona, zależna od kilku czynników. Bardzo powolny spadek stężenia (około 1% na 2 tygodnie) następuje w wyniku naturalnego procesu degradacji MEA.
Spadek ten jest korygowany przez cykliczne (na rozkaz operatora, zazwyczaj nie częściej niż raz na 2 tygodnie) dolewanie koncentratu 85% MEA, co powoduje gwałtowny wzrost stężenia proporcjonalny do ilości dolanego koncentratu. Operatorzy dolewają zazwyczaj około 200 litrów koncentratu MEA, co powoduje wzrost stężenia o 1%, który następuje w ciągu kilku minut.
Powolny wzrost stężenia (około 0,3% na 8 godzin) następuje wraz z odparowywaniem wody z roztworu MEA (woda wyparowuje z instalacji). Wzrost ten jest samoistnie korygowany poprzez cykliczne (na rozkaz operatora, zazwyczaj nie częściej niż raz na zmianę) dolewanie zdemineralizowanej wody (DEMI) , co powoduje gwałtowny spadek stężenia proporcjonalny do ilości dolanej wody.
Operatorzy dolewają zazwyczaj około 200-300 litrów wody, co powoduje w kilka minut spadek stężenia o około 0,3%. Optymalnym podejściem z punktu widzenia efektywności procesu jest utrzymywanie stężenia na poziomie stężenia górnego (14,5-15,5%) i częste (w małych ilościach) uzupełnianie wody DEMI oraz koncentratu MEA.
Układ regulacji poziomu w kolumnie K1
Odpowiada on za utrzymywanie poziomu w kolumnie K1 - w strukturze bazowej zadana wartość poziomu ustawiana jest ręcznie przez operatora na poziomie 85 %. Wartość zadana utrzymywana jest automatycznie poprzez zawór LCV-1. W przypadku wystąpienia pienienia, kiedy roztwór MEA osadza się na półkach kolumny K1, wypływ z niej automatycznie zmniejsza się i następuje zachwianie bilansu cieplnego w wymienniku E3 spowodowane spadkiem przepływu zimnego roztworu MEA z kolumny K1 do kolumny K2.
W konsekwencji strumień z kolumny K2 nie jest wystarczająco schładzany, co jeszcze bardziej nasila efekt pienienia. W celu uniknięcia tej niekorzystnej sytuacji wartość zadana na poziom w kolumnie K1 jest zaniżana (w strukturze bazowej ręcznie przez operatora, w strukturze po wdrożeniu optymalizacji będzie się to odbywało automatycznie), co powoduje schłodzenie strumienia z kolumny K2 i stłumienie zjawiska pienienia.
Układ regulacji poziomu w kolumnie K2
W strukturze bazowej za utrzymywanie poprawnego poziomu roztworu w kolumnie K2 odpowiedzialny jest operator, który w sposób ręczny dopuszcza wodę do układu albo działa doraźnie, obniżając poziom roztworu w kolumnie K1 i przesuwając tym samym w czasie konieczność dolewania wody. Po wprowadzeniu układu optymalizacji zakłada się, że utrzymywanie poziomu w kolumnie K2 będzie realizowane przez system optymalizacji.
Układ dozowania środka przeciwpieniącego
Układ współodpowiedzialny za zapobieganie zjawisku pienienia. Praca układu polega na wstrzykiwaniu do roztworu MEA małej ilość (100ml) specjalnego oleju, który ma właściwości przeciwpieniące. Wstrzykiwany preparat zapobiega pienieniu, ale jednocześnie obniża właściwości absorpcyjne roztworu MEA, dlatego też środek ten używany jest jako ostateczność, gdy inne metody zwalczania pienienia nie przyniosą rezultatów.
CZĘŚĆ III: OPTYMALIZACJA SYSTEMU
Optymalizacja procesu została zrealizowana poprzez opracowanie oraz wprowadzenie nowej struktury regulacji lepiej dostosowanej do właściwości procesu. Ta ostatnia oparta została na strukturze MFC (Model Following Control), a główne pętle regulacji realizowane są w pętli otwartej przez nieliniowe charakterystyki modelowane przez zaawansowany blok FuzzyFire systemu Ovation.
Jako regulatora korekcyjnego użyto regulatorów PID o zmiennych nastawach uzależnionych od punktu pracy, w jakim układ się znajduje. Szczegóły wykonanego wdrożenia opisane zostały w drugiej części artykułu, która opublikowana zostanie w przyszłym numerze APA.
Andrzej Kociemba, Sebastian Plamowski, Marian Rachwał, Sławomir Wieczorek