W pierwszej części artykułu zostały zaprezentowane podstawy teoretyczne związane z pracą systemów serwonapędowych oraz aspekty doboru komponentów do nich. W kontynuacji tej tematyki przedstawiamy wybrane aplikacje oraz zagadnienia związane z kwestiami komunikacji i bezpieczeństwa tytułowych systemów.
CZĘŚĆ III - KOMUNIKACJA W STEROWANIU RUCHEM
Oczekiwania wobec sieci komunikacyjnych w systemach sterowania ruchem są wyśrubowane. Wymagane jest m.in. zapewnienie synchronizacji wielu węzłów i czas aktualizacji danych rzędu milisekund z opóźnieniami w przedziale mikrolub nawet nanosekund. W razie wystąpienia problemów w transmisji, w wyniku których przesyłane dane zostają zafałszowane lub utracone, urządzenia sieciowe powinny wykryć oraz odpowiednio zareagować na takie zdarzenie.
Przykładem maszyny, w wypadku której przerwa w transmisji może spowodować poważne problemy, jest obrabiarka sterowana numerycznie. Jeżeli informacja o danym kroku nie dotrze do jej sterownika, powtórzony zostanie krok poprzedni lub brakujące dane zostaną obliczone na podstawie wcześniejszych oraz następnych kroków.
Może to negatywnie wpłynąć na jakość produktu końcowego. Oczywiście w algorytmie sterowania obrabiarką można przewidzieć taką sytuację i w razie utraty części danych zresetować maszynę, a później rozpocząć obróbkę od początku. Wydajność w ten sposób zorganizowanego systemu w razie częstych kłopotów z komunikacją byłaby jednak bardzo mała. Lepszym rozwiązaniem jest retransmisja danych.
Inną ważną kwestią, która ułatwia na przykład rozbudowę sieci, jest możliwość podłączania i odłączania węzłów sieci podczas jej pracy (hot plug and play). Oprócz tego od sieci w sterowaniu ruchem oczekuje się, podobnie jak od wielu innych sieci przemysłowych, dużej prędkości transmisji, małych kosztów budowy oraz łatwości konserwacji i modernizacji sprzętu.
ETHERNET DOMINUJE
Obecnie wiele sieci komunikacyjnych w sterowaniu ruchem bazuje na Ethernecie. Związane jest to z jego licznymi zaletami, takimi jak duża prędkość transmisji danych (rzędu Gb/s), dostępność urządzeń i kompatybilność bez względu na producenta oraz stosunkowo niska cena komponentów sieciowych wynikająca z popularności i dużej podaży na rynku.
O tym, czy spełnione zostaną wszystkie wymagania danej aplikacji, decyduje wybór konkretnego protokołu transmisji. Używane są tutaj różne protokoły czasu rzeczywistego (tematykę tę poruszaliśmy m.in. w kwietniu tego roku w raporcie rynkowym publikowanym w APA). Poniżej omówiono dwa popularniejsze z nich - EtherCAT i Sercos III.
Pierwszy z wymienionych opracowała firma Beckhoff. Protokół ten umożliwia pracę w trybie full duplex, w systemie o konfiguracji master-slave w dowolnej topologii. Zapewnia on wymianę informacji do kontroli nawet 100 osi serwo w czasie 100 µs. Dzięki wykorzystaniu specjalnej techniki distributed clock, która jest podobna do tej stosowanej w przypadku standardu IEEE 1588, osie można zsynchronizować z jitterem poniżej 1 µs. Opóźnienia transmisji są w tym wypadku minimalne również dzięki mechanizmowi przetwarzania ramki w locie kolejno przez wszystkie węzły. Przepustowość sieci wynosi do około 90%, EtherCAT zapewnia funkcjonalność hot plug and play.
Z kolei Sercos III umożliwia deterministyczną, dwukierunkową transmisję z prędkością 100 Mb/s w topologii liniowej lub pierścienia. Można też za jego pośrednictwem komunikować się w sieciach o strukturze hierarchicznej, zsynchronizowanych i sprzężonych w czasie rzeczywistym. Minimalny czas cyklu wynosi 31,25 µs, natomiast maksymalna liczba węzłów slave w jednej sieci wynosi 511.
Dopuszczalne są zaawansowane schematy komunikacji, tzn. zarówno slave-slave, jak i kontroler-kontroler (tzw. machine-machine). Przydatne cechy tego protokołu to również wsparcie dla funkcji bezpieczeństwa do SIL 3 według IEC 61508 (CIP Safety for Sercos), profile energetyczne, w których zdefiniowane są parametry, oraz komendy, dzięki którym można ograniczyć pobór mocy i profil dla enkoderów. Ponadto, podobnie jak w wypadku protokołu EthetCAT, dla Sercos III dopuszczane jest dodawanie i odłączanie węzłów sieci przy zachowaniu ich synchronizacji bez konieczności resetowania połączenia.
Oprócz Ethernetu swój udział w rynku sieci komunikacyjnych w systemach sterowania ruchem mają magistrale CAN oraz RS-485. Ta pierwsza znajduje zastosowanie głównie w komunikacji w obrębie maszyny. RS-485 jest z kolei medium transmisyjnym w różnych sieciach, w tym np. Profibus. W przypadku ostatniego standardu komunikacyjnego w sterowaniu ruchem wykorzystywany jest m.in. profil PROFIdrive. Transmisja za pośrednictwem magistrali CAN jest szybsza niż RS-485, ale wolniejsza niż w sieciach ethernetowych.
System sterowania maszyną wieloosiową
Jego częścią są serwonapędy sterujące jedną lub wieloma osiami z serii Lexium LXM 62, ILM 62, LXM 52 (na rys. nr 1), które za pośrednictwem sieci Sercos komunikują się ze sterownikiem PacDrive 3 (nr 2), który łączy w sobie funkcjonalność sterownika ruchu oraz sterownika PLC. Ten ostatni komunikuje się z resztą systemu, w tym z panelem operatorskim (nr 3), za pośrednictwem sieci Ethernet. Częścią systemu są też przemienniki częstotliwości (nr 4) oraz moduły Safe I/Os TM5/TM7 (nr 5). |
CZĘŚĆ IV - BEZPIECZEŃSTWO ZINTEGROWANE
Duża szybkość to cecha charakterystyczna dla większości systemów sterowania ruchem. Osiąga się dzięki niej dużą wydajność, jednak równocześnie takie maszyny stanowią zagrożenie dla ich obsługi oraz innego personelu znajdującego się w pobliżu. O wypadek w pobliżu przykładowo latającej piły lub wirującego noża nietrudno, zwłaszcza gdy z różnych przyczyn nie są przestrzegane zasady bezpieczeństwa lub zaistnieją inne okoliczności, w tym zdarzenia losowe. Wypadki zdarzają się również na skutek awarii maszyn lub ich błędnych ustawień. Aby minimalizować liczbę takich zdarzeń, w serwonapędach realizuje się różne funkcje bezpieczeństwa.
Najpowszechniejsze z nich to (pełny opis znajduje się w temacie numeru w APA 2/2013):
- bezpieczne wyłączenie momentu (Safe Torque Off, STO),
- bezpieczny stop 1 oraz 2 (Safe Stop 1, Safe Stop 2, SS1, SS2),
- bezpieczne zatrzymanie pracy (Safe Operating Stop, SOS),
- bezpiecznie ograniczona prędkość (Safely Limited Speed, SLS),
- bezpieczny zakres prędkości (Safe Speed Range, SSR),
- bezpieczny kierunek ruchu (Safe Direction, SDI),
- bezpiecznie ograniczona długość kroku (Safe Limited Increment, SLI),
- bezpieczne wysterowanie hamulców (Safe Brake Control, SBC),
- bezpieczny test hamulców (Safe Brake Test, SBT).
Pierwsza z wymienionych funkcji odłącza zasilanie od silnika. Jest ona użyteczna, gdy dopuszczalne jest, aby system napędowy w wyniku tarcia, inercji silnika oraz obciążenia "naturalnie" wyhamował. Zanim to nastąpi, możliwe są niekontrolowane ruchy elementów maszyn, które również mogą (na przykład ze względu na ich dużą wagę lub wysokość, na jakiej się zatrzymały) zranić obsługę. Ta ostatnia powinna być zatem albo ostrzeżona o takiej możliwości, albo wdrożyć trzeba dodatkowe rozwiązania, które zapobiegną niekontrolowanemu przemieszczaniu się obciążenia serwonapędu.
Funkcja SS1 składa się z dwóch etapów. W pierwszym stopniowo zmniejsza się prędkość silnika. W momencie, gdy przekroczy ona określoną wartość graniczną lub po wcześniej ustalonym czasie, dobranym pod kątem wymogów aplikacji (w zależności od sposobu realizacji tej funkcji), aktywuje się funkcję bezpiecznego wyłączenia momentu lub funkcję SBC. Bezpieczny stop 1 sprawdza się zwłaszcza wtedy, gdy priorytetem jest najszybsze zatrzymanie maszyny. Dotyczy to głównie ciężkich oraz wirujących urządzeń, na przykład szlifierek.
Funkcja bezpiecznego stopu 2 również składa się z dwóch kroków. Najpierw silnik jest hamowany, a później aktywuje się funkcję SOS, czyli bezpiecznego zatrzymania pracy. Zasilanie elementu wykonawczego nie jest w związku z tym odłączane, a w zamian silnik zatrzymuje się w określonej pozycji.
Przyspiesza to ponowny restart serwonapędu. Jest to cenną zaletą podczas konserwacji maszyny, uzupełniania w niej surowców (na przykład założenia nowej szpuli) lub sprzątnięcia resztek materiałów (na przykład po cięciu). Z kolei funkcja bezpiecznego ograniczenia prędkości nie dopuszcza do wzrostu prędkości obrotowej powyżej zadanej wartości.
W tym celu w takim momencie załączana jest funkcja STO, która wyłącza silnik. Z funkcji SLS korzysta się przykładowo wtedy, gdy nie jest możliwe lub nie opłaca się całkowite zatrzymanie maszyny. Funkcja SSR nie dopuszcza także do spadku szybkości napędu poniżej określonej minimalnej prędkości.
Omawiane funkcje wbudowywane są w standardowe przemienniki częstotliwości oraz serwonapędy i mogą być parametryzowane na etapie konfiguracji systemu. Ich wykorzystanie upraszcza późniejszy proces zapewniania bezpieczeństwa maszyny lub instalacji technologicznej, zazwyczaj też zwiększa szybkość i efektywność jej pracy.
Z przykładowych serwonapędów mających zintegrowane funkcje bezpieczeństwa wymienić można: urządzenia z serii Accurax G5 firmy Omron, serwonapędy serii SINAMICS S110 firmy Siemens, serwonapędy IndraDrive Cs od Bosch-Rexroth oraz serwonapęd MicroFlex e150 firmy ABB (patrz ramka z produktami w pierwszej częś ci artykułu).
CZĘŚĆ V - APLIKACJE
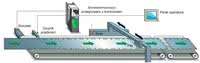
Rys. 1.
Serwonapędy używane są m.in. w aplikacjach, gdzie konieczne jest wykonywanie ruchów o określoną wartość przemieszczenia. Przykładem jest wykorzystanie w stole obrotowym - silnik obraca go o zadany kąt, a następnie zatrzymuje i wówczas wykonywana jest jakaś operacja - na przykład wywiercenie otworu w metalowym bloczku lub dozowanie substancji do fiolki.
Innym przykładem jest ten związany z taśmociągiem, na którym w równych odstępach ustawione są obiekty - przykładowo pudełka. Przenośnik przemieszcza się o określony odcinek i hamuje - wtedy wykonywana jest inna akcja. Taką może być na przykład wkładanie do pojemnika towaru, a następnie zaklejenie tego ostatniego. Wówczas taśmociąg przemieszcza się, a sekwencja zdarzeń powtarza.
W ten sposób można także zrealizować cięcie materiałów. Częścią takiej maszyny jest szpula - po odwinięciu materiału o określonej długości jest ona zatrzymywana. Kontroler, który analizuje prędkość szpuli, uruchamia wtedy ostrze, które odcina fragment materiału. Następnie szpula jest ponownie wprawiana w ruch.
Maszyny takie są używane m.in. w przemyśle drukarskim do cięcia kartonów, w produkcji elementów z tworzyw sztucznych lub cięciu metalowych arkuszy. W każdej z opisanych aplikacji pojedynczy krok polegający na przebyciu drogi o określonej długości składa się z etapu przyspieszania, przemieszczania ze stałą prędkością i zwalniania. Dlatego też najczęściej ruch ten odbywa się zgodnie z profilem trapezowym.
Systemy zintegrowane coraz popularniejszeDostawcy komponentów systemów sterowania ruchem, reklamując swoje produkty, ich konstrukcje charakteryzują jako zintegrowane, modułowe oraz kompaktowe. Dzięki tym cechom uproszcza się proces realizacji systemu sterowania ruchem, mniejsze są również wydatki z tym związane - przykładowo przeznaczane na okablowanie łączące rozproszone komponenty. W praktyce oznacza to, że pomału zacierają się granice nie tylko między poszczególnymi podzespołami tych systemów, ale również między nimi a innymi poziomami sterowania pracą zakładu. Nie chodzi już tylko o połączenie w jednym urządzeniu serwowzmacniacza i sterownika ruchu, ale również integrowanie funkcji sterowania ruchem w specjalnych modułach sterowania osiami ruchu w sterownikach programowalnych. Dzięki tej tendencji wiele narzędzi do programowania systemów sterowania ruchem jest również zgodnych z normą IEC61131-3, która definiuje języki programowania PLC. |
LATAJĄCA PIŁA, WIRUJĄCY NÓŻ
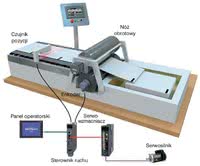
Rys. 2.
Gdy wymagana jest większa wydajność oraz szybkość maszyny, materiał musi być rozcinany "w biegu". Cięcie bez konieczności zatrzymywania przenośnika jest realizowane z wykorzystaniem tzw. latającej piły (rys. 1). Prędkość pracy ostrza musi być zsynchronizowana z prędkością przemieszczania się taśmociągu.
W tym celu mierzona jest ta ostatnia, a wynik pomiaru przetwarzany w kontrolerze napędu piły. Po odcięciu fragmentu materiału ostrze jest zatrzymywane i przemieszczane z powrotem do pozycji wyjściowej. Latające piły są używane m.in. w obrębie linii cięcia prętów stalowych lub drewna.
Cięcie "w biegu" umożliwia również tzw. wirujący nóż (rys. 2). Głównym komponentem tego urządzenia jest obracający się cylinder, wzdłuż którego zamontowane jest ostrze. Od prędkości, z jaką wiruje nóż, zależy długość odciętego materiału. Im większa jest ta pierwsza, tym krótszy kawałek zostanie ucięty.
Serwonapędy są też używane m.in. w sterowaniu chwytakami maszyn pick & place oraz w kapslowaniu butelek. W tym ostatnim najpierw nakrętki są nakładane na szyjki butelek, a następnie zakręcane z dużą prędkością. Parametry pracy tego ostatniego są tak dobrane, aby nie zniszczyć gwintu butelki ani samej nakrętki. Rozwiązania takie jak omawiane są powszechnie używane w przemyśle spożywczym i farmaceutycznym.
Monika Jaworowska