WYMAGANIA USTAWOWE
Na podstawie rozporządzenia Ministra Gospodarki z dnia 21 października 2008 r. w sprawie zasadniczych wymagań dla maszyn, wdrażającego postanowienia dyrektywy 2006/42/WE, można wyszczególnić kilka wymagań dotyczących podstawowych funkcji bezpieczeństwa:
- Maszyny powinny być wyposażone w urządzenia sterujące umożliwiające całkowite i bezpieczne zatrzymanie maszyny. [§23.1.]
- Każde stanowisko robocze powinno być wyposażone w urządzenia sterujące umożliwiające zatrzymanie […]. Sterowanie zatrzymaniem powinno mieć pierwszeństwo w stosunku do sterowania uruchomieniem. [§23.2.]
- Z chwilą zatrzymania maszyny lub jej niebezpiecznych funkcji, zasilanie odpowiednich napędów uruchamiających powinno zostać odłączone. [§23.3.]
- W przypadku, gdy z przyczyn eksploatacyjnych wymagany jest element sterowniczy zatrzymujący, który nie odłącza zasilania odpowiednich napędów uruchamiających, stan zatrzymania musi być monitorowany i utrzymywany. [§23.4.]
- W przypadku, gdy operator może znaleźć się w strefie niebezpiecznej, zanim ustanie ryzyko związane z niebezpiecznymi funkcjami maszyny, ruchome osłony muszą być połączone z urządzeniem ryglującym osłony stanowiącym uzupełnienie urządzenia blokującego, aby:
- zapobiec uruchomieniu niebezpiecznych funkcji do chwili zamknięcia i zaryglowania osłon
oraz
- osłony pozostawały zamknięte i zaryglowane, dopóki nie ustanie ryzyko urazów wynikające z niebezpiecznych funkcji maszyny. [§23.4.]
- W uzasadnionych przypadkach, pomimo odłączenia zasilania energią, niektóre obwody mogą pozostać podłączone do swoich źródeł energii, między innymi po to, aby utrzymać położenie określonych części, zachować informacje, oświetlić wnętrza. W takim przypadku należy podjąć odpowiednie działania w celu zapewnienia bezpieczeństwa operatorowi. [§51.4.]
- Maszyna powinna być tak skonstruowana i wyposażona, aby ograniczyć interwencję operatora. [§52.1.] Jeżeli interwencji, o której mowa w ust. 1., nie można uniknąć, należy zapewnić możliwość przeprowadzenia jej w łatwy i bezpieczny sposób. [§52.2.]
Na podstawie przytoczonych powyżej fragmentów można zdefiniować szereg funkcji bezpieczeństwa, które powinny zostać zastosowane w nowo budowanych czy dostosowywanych maszynach. Do funkcji tych należeć mogą (w obrębie części elektrycznej) m.in.:
- kontrola stref niebezpiecznych przez nadzór osłon ruchomych i drzwi (oraz ich blokowanie),
- bezpieczne monitorowanie prędkości obrotowej oraz zatrzymania napędu (często powiązane z kontrolą dostępu do stref niebezpiecznych).
TECHNICZNE ŚRODKI BEZPIECZEŃSTWA - OSŁONY I URZĄDZENIA Z NIMI WSPÓŁPRACUJĄCE
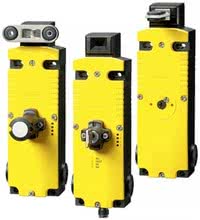
Fot. 1. Przykładowe wyłączniki pozycyjne z funkcją ryglowania
Według dyrektywy maszynowej osłony dzielimy na: stałe, ruchome i nastawne. Od strony elektrycznej z funkcjami bezpieczeństwa są związane w zasadzie wyłącznie osłony ruchome. Jeżeli eliminacja zagrożenia, przed którym chronią osłony ruchome, jest natychmiastowa, wystarczy użyć sprzęgniętego z osłoną wyłącznika pozycyjnego (lub dwóch w zależności od wymaganego poziomu PL/SIL). Jeżeli natomiast konieczne jest utrzymanie osłony zamkniętej przez czas dłuższy, konieczna jest funkcja ryglowania.
W takim wypadku w jednej obudowie mamy dwa elementy: wyłącznik pozycyjny i zamek (w zależności od wersji elektryczny lub mechaniczny - ryglowanie napięciem lub sprężyną). Rygle mogą być wyposażone w dodatkowe funkcje umożliwiające np. odryglowanie awaryjne lub pomocnicze bezpośrednio z urządzenia.
Układ sterujący realizujący funkcje bezpieczeństwa musi uwzględniać funkcję ryglowania (jeżeli takowa jest funkcją bezpieczeństwa) i odblokowywać rygle po zniknięciu zagrożenia - w najprostszym przypadku po upływie określonego czasu lub po fizycznym stwierdzeniu zniknięcia zagrożenia (ruchomych elementów).
KONTROLA PRĘDKOŚCI OBROTOWEJ I MONITOROWANIE ZATRZYMANIA
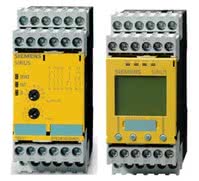
Fot. 2. Wygląd zewnętrzny przekaźników bezpieczeństwa służących do monitorowania stanu zatrzymania silnika elektrycznego
Na fotografii 2 przedstawiono dwa przekaźniki bezpieczeństwa służące do monitorowania prędkości obrotowej silnika indukcyjnego. Pierwszy, (3TK2810-0) monitorujący zatrzymanie, działa na zasadzie pomiaru szczątkowej siły elektromotorycznej indukowanej (dzięki zjawisku remanencji magnetycznej i obracającemu się wirnikowi) w uzwojeniu silnika. Drugi (3TK2810-1) kontroluje prędkość (funkcja SLS - Safety Limited Speed) i monitoruje zatrzymanie z wykorzystaniem pomiaru ruchu za pomocą czujników indukcyjnych lub enkodera.
Wykorzystanie przekaźnika kontrolującego prędkość umożliwia zrealizowanie funkcji SLS przy zastosowaniu przekształtników częstotliwości niemających takich funkcji.
Budując układ realizujący funkcje bezpieczeństwa, musimy obliczyć ich poziom PL/SIL. W wypadku zastosowania enkodera powinien on również mieć znane dane niezawodnościowe i diagnostyczne. Na fototografii 3 pokazano takie urządzenia - tego typu enkodery mogą być stosowane we współpracy z przekaźnikami 3TK2810-1.
ROZWIĄZANIA BEZPIECZEŃSTWA DLA PILAREK DO DREWNA
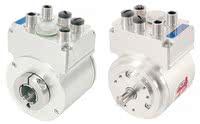
Fot. 3. Enkodery inkrementalne (sin/cos) firmy Stoltronic Polska
Za jedne z najniebezpieczniejszych maszyn uważane są pilarki do drewna. Na taką opinię składają się prawdopodobnie czynniki, takie jak: powszechne ich wykorzystywanie przez operatorów mających często niskie kwalifikacje, specyfika obrabianego materiału oraz typowe rodzaje budowy (często dość otwartej) wynikające z zapotrzebowania technologicznego. Ponieważ maszyny te są wymienione w załączniku IV dyrektywy maszynowej, w normie szczegółowej PN-EN 1870-11:2014-03 dostępne są dość dokładne opisy rozwiązań bezpiecznych.
W przypadku maszyn obsługiwanych ręcznie, o jakich mowa powyżej, możliwości zmniejszenia ryzyka są z natury ograniczone. Więcej możliwości daje automatyzacja procesu obróbki drewna, co jednak nie zmienia występujących zagrożeń oraz ryzyka pierwotnego, które musi być ograniczone w stopniu znacznym, aby maszyny mogły być uznawane za bezpieczne.
Jednym z głównych elementów obróbki drewna jest jego rozkrój poprzeczny. Chociaż wciąż często wykorzystuje się w tym celu pilarki ręczne, warto zwrócić uwagę na korzyści płynące z procesu automatyzacji:
- zwiększenie bezpieczeństwa pracy - wiele ręcznych, stosowanych ciągle jeszcze pilarek poprzecznych jest po prostu niebezpiecznych i dlatego w wielu krajach rezygnuje się z ich użycia albo też ich doposażenie jest kosztowne; poprzeczna pilarka podstołowa zaopatrzona w osłony bezpieczeństwa z obydwu stron piły nie nadaje się już do szybkiego cięcia poprzecznego;
- wzrost wydajności pracy.
Zastosowanie osłon po obu stronach strefy cięcia przy ich odpowiednim gabarycie (długość każdej z osłon bocznych przekraczająca 850 mm uniemożliwia sięgnięcie ręką do strefy - patrz norma PN-EN 953+A1:2009) redukuje skutecznie ryzyko związane z obcięciem palców lub kończyny w czasie normalnej pracy.
Pozostaje jednak zastanowić się nad problemem uzyskiwania dostępu do strefy cięcia w celu:
- czyszczenia,
- wymiany narzędzia (piły),
- czynności regulacyjnych,
- czynności serwisowych.
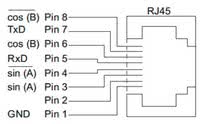
Rys. 1. Sposób podłączenia sygnału enkodera do przekaźnika 3TK2810-1
W takim przypadku wygodnie jest przynajmniej jedną z osłon zaprojektować jako ruchomą osłonę ryglowaną oraz należy koniecznie zaopatrzyć pilarkę w kilka niezbędnych funkcji bezpieczeństwa związanych z wykonywaniem czynności w strefie zagrożenia, takich jak na przykład zapobieganie niespodziewanemu uruchomieniu czy blokowanie ruchu w czasie, gdy osłona jest otwarta.
Piła do drewna jako metalowa, relatywnie masywna tarcza o znacznej średnicy charakteryzuje się znacznym momentem bezwładności. Samohamowność napędu piły zależy przede wszystkim od tego, czy ostrza znajdują się w drewnie, czy też nie. Po zakończeniu cięcia piła obraca się w powietrzu (bez kontaktu z drewnem).
Gdyby operator chciał w tym czasie przykładowo wymienić ostrze, natychmiastowe otwarcie osłony mogłoby doprowadzić do wypadku. Konieczne jest zatem odczekanie ustalonego wcześniej czasu niezbędnego do wyhamowania piły lub zamontowanie czujnika ruchu dającego zezwolenie na otwarcie komory piły.
Biorąc pod uwagę, że ostrza mogą być różne, poruszać się ze zmienną prędkością oraz mogą występować losowe czynniki hamujące spowodowane zanieczyszczeniem komory piły itd., najkorzystniejszym rozwiązaniem jest ustalenie poprzez pomiar, czy piła (lub sprzężony z nią sztywno silnik) już jest nieruchoma i pod takim warunkiem układ sterowania zezwoli na otwarcie osłony.
BEZPIECZEŃSTWO OBSŁUGI FREZAREK
Norma szczegółowa PN-EN 13128+A2:2011 typu "C" opisująca bezpieczne projektowanie frezarek, jak każda z norm związanych z grupą maszyn, wymienia i opisuje znaczące zagrożenia, których istnienie generuje ryzyko konieczne do zniwelowania. Zagrożenia związane z ruchem, szczególnie w sytuacji, gdy napędy są sterowane (regulacja prędkości i/lub położenia), wymagają monitorowania.
W typowych układach realizujących funkcje bezpieczeństwa układy identyfikujące istnienie ruchu (prędkość niezerowa) lub określonej (bezpiecznej) wartości prędkości spełniają funkcję czujników pozwalających na wypracowanie systemom logicznym sygnałów dla elementów wykonawczych, takich jak rygle czy hamulce elekromagnetyczne.
W powyższej normie wyróżniono czynności wykonywane przez operatora wewnątrz strefy zagrożenia w sytuacji, gdy przynajmniej jedna osłona jest otwarta i ręce lub większa część ciała operatora są bezpośrednio zagrożone ruchem, czyli samo zablokowanie możliwości otwarcia osłony w powiązaniu z monitorowaniem braku ruchu nie jest możliwe.
W tych sytuacjach konieczne jest zaprojektowanie układów pozwalających na poruszanie się napędów, układów przenoszenia napędu lub części czynnych maszyny z prędkościami bezpiecznymi, często w powiązaniu z blokadą ruchu niektórych napędów (np. dopuszcza się ruch jednego, wybranego napędu naraz). Niekiedy stosuje się funkcje bezpieczeństwa z podtrzymywaniem ruchu (np. pilot ręczny i ograniczenie prędkości).
Do podstawowych, stosowanych tu funkcji bezpieczeństwa należy zaliczyć ponadto:
- wybór trybu pracy (praca automatyczna, nastawianie, regulacja, inne elementy procesu),
- zapobieganie niespodziewanemu uruchomieniu,
- zatrzymanie awaryjne,
- reset ręczny.
Ocena ryzyka wskazuje, że układy sterowania funkcjami bezpieczeństwa w zakresie głównego obszaru obróbki powinny być realizowane w przypadku poziomu bezpieczeństwa PL d lub e (SIL 2 lub SIL3). W zależności od potrzeb zatrzymanie może być realizowane w kategorii 0 lub 1, oczywiście w powiązaniu z dopuszczeniem do otwarcia osłon po wyeliminowaniu zagrożenia ruchem.
Funkcje te mogą być realizowane w oparciu o specjalizowane przekaźniki bezpieczeństwa z rodziny 3TK2810, również we współpracy z programowalnymi przekaźnikami bezpieczeństwa 3RK3, ewentualnie w oparciu o funkcje bezpieczeństwa zintegrowane w falownikach sterujących osiami napędowymi i sterowaniu NC.
PODSUMOWANIE
Z czasem rosną oczekiwania użytkowników wobec producentów maszyn. Dotyczy to z jednej strony wzrostu wydajności, a z drugiej bezpieczeństwa pracy. Spełnienie tych po części sprzecznych oczekiwań jest trudne i wymaga stosowania coraz doskonalszych systemów sterowania. Maszyny, statystycznie rzecz biorąc, są z czasem osłaniane w coraz większym stopniu, co zmusza producentów do zwiększania poziomu ich automatyzacji. Niekiedy nawet urządzenia dotąd uznawane za proste nagle stają się skomplikowane.
Rozwiązanie problemu prędkości bezpiecznej dla napędów regulowanych czy pomiarów monitorujących stan zatrzymania elementów czynnych napędu bardzo pomogło w pokonywaniu tych codziennych problemów projektantów.
Pozostaje tylko pytanie, z jakim poziomem bezpieczeństwa trzeba dane funkcje realizować. Oferowany przez przekształtniki częstotliwości poziom PL/SIL w przypadku maszyn szczególnie niebezpiecznych może być zbyt niski - pozostaje konieczne wówczas blokowanie napędu do czasu całkowitego zatrzymania.
Siemens
www.automatyka.siemens.pl