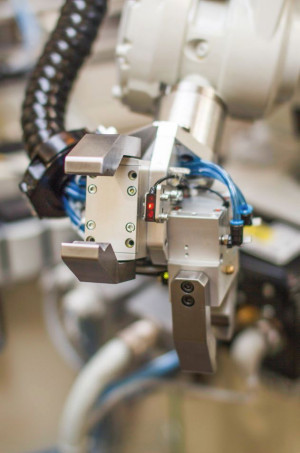
Fot. 1. Chwytak robota wyposażony w optyczny czujnik Balluff
Jej producentem jest firma Hydrapress (www.hydrapress.pl), a system automatyki zaprojektowała i oprogramowała firma L.K. Control (www.lkc.com.pl). Linia składa się z dwóch zrobotyzowanych cel, dwóch robotów, trzech pras hydraulicznych, podajnika wejściowego, podajnika pośredniego (znajdującego się pomiędzy celami), obrabiarki CNC oraz urządzenia do sztaplowania gotowych elementów w koszach.
Cała linia produkcyjna jest nadzorowana przez 3 komputery przemysłowe oraz cztery sterowniki PLC, które obsługują m.in. liczne sygnały, rozproszone w ramach całego systemu. Ponadto każda z maszyn wchodzących w skład wyżej opisanej linii produkcyjnej, umożliwia również pracę autonomiczną.
Przy projektowaniu wyżej opisanej linii jednym z założeń było umożliwienie łatwiej zmiany jej konfiguracji (poprzez usunięcie niektórych maszyn lub dodanie innych). Oprócz tego inwestor planował wykorzystanie maszyn wchodzących w skład linii do innych projektów.
Oznaczało to, że cały system maszyn i urządzeń musi zostać wyposażony w takie rozwiązania z zakresu automatyki przemysłowej, które umożliwią optymalizację produkcji, przestrzeni w fabryce oraz łatwą adaptację linii do obrabiania różnorodnych produktów. Oprócz tego wybrane rozwiązania miały zagwarantować łatwe przezbrajanie urządzeń i skrócenie czasu pracy całej linii.
OPTYMALIZACJA LINII PRODUKCYJNEJ Z WYKORZYSTANIEM ROZWIĄZAŃ BALLUFF
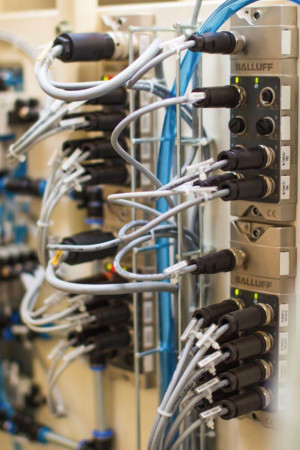
Fot. 2. Koncentrator sygnałów wejściowych
W celu usprawnienia procesu przezbrajania urządzeń na linii produkcyjnej zastosowano technologię RFID do kontroli pracy narzędzi. Rozwiązanie objęło umieszczenie tagów RFID na konkretnych narzędziach, zamontowanie głowic odczytu/zapisu oraz implementację procesora RFID BIS013W (do którego możliwe jest podłączenie 4 głowic).
Po odczytaniu nośników RFID, informacje dotyczące weryfikacji poprawności doboru narzędzia do danej aplikacji, przekazywane są poprzez procesor do sterownika PLC, która steruje konkretną maszyną. Szczegółowa weryfikacji danych, umożliwiających określenie zużycia narzędzia oraz przekazywanie ich do systemu nadrzędnego umożliwia właściwą konfigurację urządzeń (zarówno w zakresie doboru narzędzi jak i ich zużycia), niezależnie od aktualnie produkowanego detalu.
Dodatkowo takie rozwiązanie z zastosowaniem technologii RFID eliminuje możliwość pomyłki operatorów obsługujących maszyny, która mogłaby skutkować produkcją wadliwych detali, uszkodzeniem narzędzia, a w najgorszym wypadku - awarią linii.
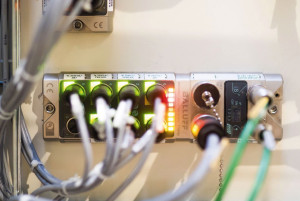
Fot. 3. Master IO-Link Profinet
Kolejnym elementem, który znacząco usprawnił optymalizację linii produkcyjnej, był przetwornik położenia BTL6. Został w niego wyposażony siłownik pneumatyczny, którego zadaniem jest mierzenie półproduktów trafiających na podajnik wejściowy całego systemu - proces ten zachodzi przed ich dalszą obróbką.
Przetworniki położenia BTL firmy Balluff idealnie nadają się do tego typu zastosowań, ponieważ dokonują niezawodnych i precyzyjnych pomiarów położenia, a dodatkowo cechują się bezdotykową zasadą działania, co eliminuje konieczność ich konserwacji. Przystosowane są także do pracy w trudnych warunkach - dzięki hermetycznej obudowie wykazują wysoką odporność na działanie wstrząsów, wibracji i zanieczyszczeń.
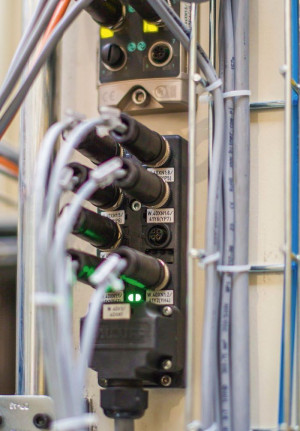
Fot. 4. Koncentrator pasywny
Oprócz powyższych rozwiązań, zastosowano również kilkadziesiąt czujników ciśnienia firmy Balluff. Ponadto do zbierania informacji z ponad stu czujników cyfrowych (indukcyjnych, optycznych oraz pola magnetycznego) wykorzystano koncentratory wejść cyfrowych BNI0032. Do sterowania rozdzielaczy służy koncentrator wejść/wyjść cyfrowych BNI0035, którego porty mogą być ustawione jako wyjścia.
Sam koncentrator zainstalowany jest na ramionach robotów i obsługuje podwójne szczęki z zespołem czujników. Aby osiągnąć najwyższą stabilność pomiarów i zwiększyć ich odporność na zakłócenia, wszystkie czujniki wielkości analogowych zostały wymienione na ich odpowiedniki z cyfrowym interfejsem komunikacyjnym IO-Link.
WYNIKI WDROŻENIA
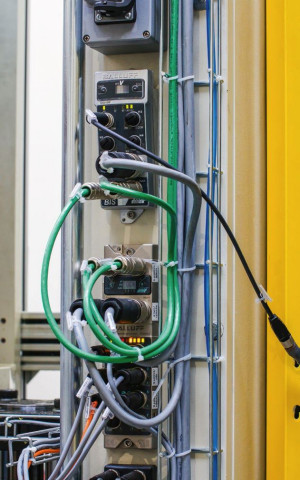
Fot. 5. Procesor RFID BIS V, Master IO-Link ProfiNet
W jaki sposób rozwiązania z zakresu automatyki przemysłowej przełożyły się na optymalizację linii produkcyjnej kształtowania cylindrów amortyzatorów?
Zastosowanie wszystkich rozwiązań firmy Balluff z zakresu automatyki przemysłowej, takich jak technologia RFID, przetworniki położenia, czujniki ciśnienia czy interfejs IO-Link, pozwoliło na efektywną optymalizację linii produkcyjnej kształtowania cylindrów amortyzatorów w wielu obszarach:
- Przede wszystkim zastosowanie rozwiązań z dziedziny automatyki przemysłowej generuje dużą oszczędność w zakresie planowania czasu pracy linii produkcyjnej, (dzięki technologii RFID nie musi być ona za każdym razem dostosowywana do konkretnego produktu), a także wpływa na zmniejszenie konieczności zatrudnienia kolejnych pracowników do jej obsługi. Interfejs IO-Link optymalizuje czas przesyłu danych, a dodatkowo zastosowane rozwiązania zwiększają elastyczność linii produkcyjnej w zakresie produkcji różnych komponentów.
- Wszystkie zastosowane rozwiązania redukują liczbę przewodów, potrzebnych do połączenia konkretnych urządzeń, co przekłada się na bardziej efektywne wykorzystanie miejsca w szafie sterowniczej oraz upraszcza obsługę całej linii produkcyjnej. Redukcja ilości przewodów połączeniowych możliwa jest dzięki wykorzystaniu interfejsu IO-Link, który realizuje przesył informacji w sposób cyfrowy. Do podłączenia dowolnego czujnika, niezależnie od tego czy jest to czujnik dwustanowy czy analogowy, wykorzystywany jest ten sam typ przewodu - 3-żyłowy, nieekranowany, którego długość może wynosić aż 20 metrów. Zastosowanie opisanych koncentratorów sygnałów pozwala na pogrupowanie sygnałów, skąd informacje przesyłane są do Mastera IO-Link wspomnianym jednym przewodem. Dodatkowo zyski widoczne są w przypadku dokumentacji, która przyjmuję formę prostych, jednokreskowych schematów, a instalacja sprowadza się do przykręcenia wtyczki (Plug&Play). IO-Link to także możliwość zdalnej parametryzacji i diagnostyki urządzeń wykonawczych z poziomu sterownika PLC oraz aplikacji mobilnej.
- Kolejną zaletą wdrożonego przez firmę Balluff rozwiązania jest łatwość modernizacji urządzeń oraz możliwość dodawania kolejnych komponentów do systemu. Takie rozwiązanie jednocześnie wpisuje się w pierwotne założenia klienta w zakresie optymalizacji linii produkcyjnej i jej późniejszej rozbudowy bądź modyfikacji pod kątem obrabianych elementów.
Krzysztof Lewandowski, L.K. Control s.c.
Karol Kowalczyk, Balluff