W artykule przedstawiamy wybrane problemy wraz z przykładowymi sposobami ich rozwiązywania, na wstępie krótko charakteryzując proces spawania laserem.
Techniki spawania laserowego
Techniki spawania laserowego dzieli się na dwie kategorie, spawanie kondukcyjne i spawanie z głębokim wtopieniem. W metodzie pierwszej powierzchnia złącza jest podgrzewana powyżej temperatury topnienia, ale nie w takim stopniu, by spawane materiały mogły odparować. To oznacza, że tylko pochłaniają promieniowanie lasera, ale nie są penetrowane przez jego wiązkę. Roztopione materiały przenikają się i zastygają, tworząc spoinę.
Wykonywane tą metodą spoiny przeważnie są gładkie i zaokrąglone. Zwykle nie wymagają obróbki wykończeniowej. Są też typowo szersze niż głębsze. Przewodność cieplna materiału ogranicza maksymalną głębokość spawu, która ze względu na konieczność używania laserów małych mocy (rzędu setek watów) nie przekracza zazwyczaj milimetra. W spawaniu kondukcyjnym korzysta się zarówno z laserów ciągłych, jak i impulsowych. W ten sposób łączy się głównie części cienkościenne i te, które wymagają estetycznej spoiny.
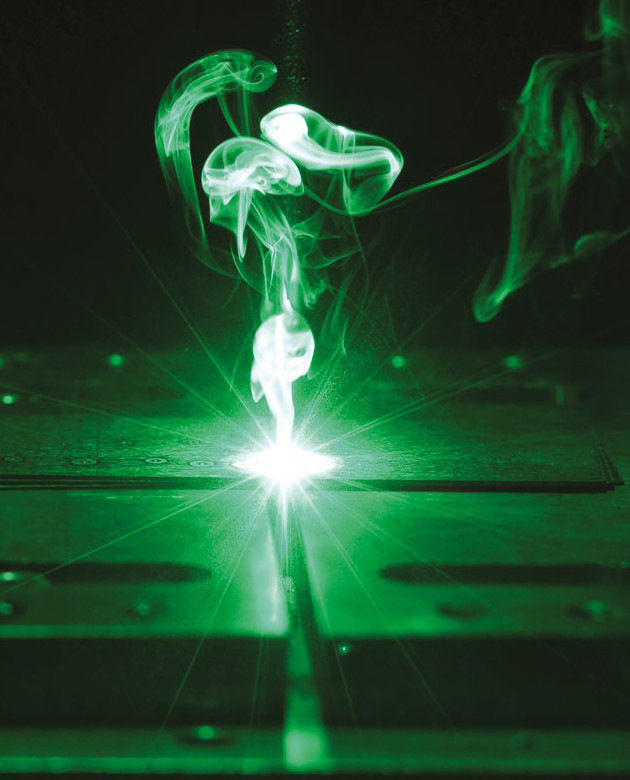
W spawaniu z głębokim wtopieniem wiązka lasera nie tylko topi materiały złącza, lecz powoduje także ich odparowanie. W efekcie na stopione materiały działa ciśnienie i częściowo je wypiera, powodując powstanie głębokiego i bardzo wąskiego otworu – kapilary. Jest ona wypełniona rozszerzającą się parą wodną, która zapobiega zapadaniu się ścianek tego otworu i otoczona stopionym materiałem. Przy przesuwaniu się kapilary podążającej za wiązką lasera zastyga on, tworząc spoinę. Warto też dodać, że na ściankach kapilary promień lasera ulega wielokrotnemu odbiciu, a stopiony materiał całkowicie absorbuje promień lasera. To zwiększa skuteczność spawania. Głębokość wykonanych tą technika spawów jest kilka razy większa niż szerokość i wynosi nawet kilkadziesiąt milimetrów. W spawaniu z głębokim wtopieniem używa się laserów o większej mocy niż w konwekcyjnym, zwykle rzędu kilowatów. Jest to metoda szybka.
Przegląd typów laserów spawalniczych
W spawaniu wykorzystywane są lasery różnych typów, od światłowodowych i diodowych, przez te na ciele stałym, jak lasery Nd:YAG, po gazowe CO2.
- Lasery światłowodowe, o długości fali około 1 μm, wyróżnia niezawodność i niski koszt. Poza tym zapewniają elastyczność w zakresie wymiarów spoin i duży stosunek głębokości penetracji do mocy, co pozwala uzyskać duże szybkości spawania.
- Lasery gazowe CO2 wykorzystywane są głównie w łączeniu materiałów grubszymi spoinami odpornymi na naprężenia, przykładowo w spawaniu blach na potrzeby przemysłu stoczniowego.
- Lasery Nd:YAG, o zbliżonej długości fali do laserów światłowodowych, zapewniają duże moce szczytowe przy niewielkich rozmiarach. Wyróżniającym je zastosowaniem jest mikrospawanie, proces wykorzystywany w produkcji implantów medycznych.
- Lasery diodowe cechuje duży rozmiar plamki i wyższa wydajność niż lasery światłowodowe. Są dostępne w szerokim zakresie długości fal, 780‒1060 nm, 1400=1500 nm, 450 nm. Ostatnia sprawdza się zwłaszcza w spawaniu miedzi ze względu na jej dużą absorpcję (65%) w tym materiale w porównaniu z promieniowaniem podczerwonym (tylko 5%). Lasery diodowe wykorzystywane są również w łączeniu tworzyw sztucznych.
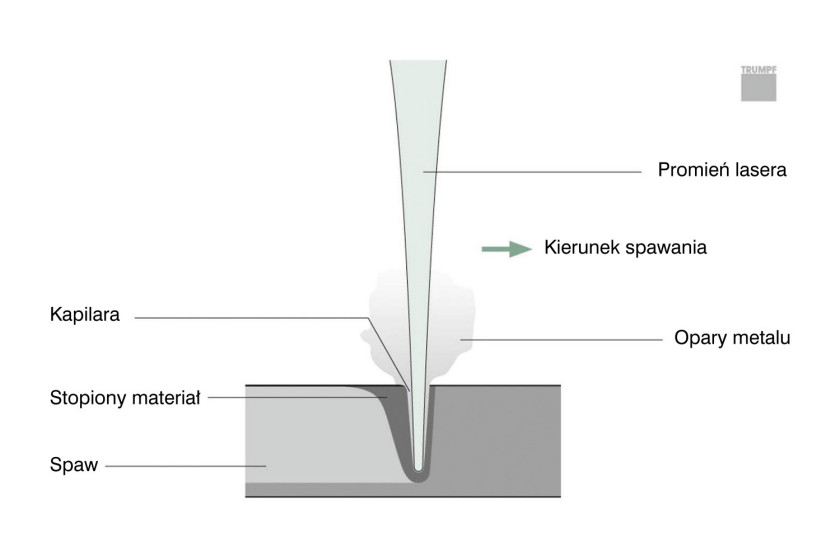
Zalety spawarek laserowych