CZĘŚĆ 1. GIĘCIE I CIĘCIE BLACH
Gięcie blachy to przykład metody kształtowania tego materiału, która zmienia jego kształt, bez wpływu na jego grubość (zazwyczaj) oraz objętość. Wyginanie ma na celu, poza uzyskaniem określonego kształtu detalu, również m.in. zaokrąglenie jego krawędzi oraz zwiększenie wytrzymałości i sztywności blachy. Dalej wyjaśniamy mechanizm tej metody obróbki. Przedstawiamy też popularne techniki gięcia.
GDZIE JEST OŚ NEUTRALNA?
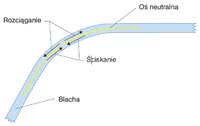
Rys. 1. Dookoła osi neutralnej na zginany materiał nie działa żadna siła
Podczas wyginania blachy jest ona równocześnie w miejscu zgięcia w jednym kierunku ściskana (do wnętrza zgięcia) i rozciągana (na zewnątrz zgięcia). W związku z tym, że są to oddziaływania przeciwstawne, musi istnieć obszar przejściowy, w którym na materiał nie będzie wywierana żadna siła. Takie miejsce znajduje się dookoła osi neutralnej (obojętnej) (rys. 1), której charakterystyczną cechą jest stała długość.
Położenie osi neutralnej zależy od sposobu zgięcia blachy oraz jej rodzaju. Zazwyczaj znajduje się ona jednak w odległości, która, mierzona od środka zgięcia, jest mniejsza (około 40%) od połowy grubości materiału. Im dalej od osi obojętnej, tym siła, z jaką blacha jest ściskana i rozciągana, jest większa.
JAK TRWALE WYGIĄĆ BLACHĘ?
Trwałość zgięcia blachy gwarantuje wyłącznie jej plastyczne odkształcenie. W przeciwieństwie do elastycznego nie ustępuje ono bowiem po ustaniu oddziaływania siły. Aby doszło do odkształcenia plastycznego, ta ostatnia musi przekroczyć wartość progową. Ponieważ dookoła osi obojętnej nie działa żadna siła, w obszarze tym materiał odkształca się elastycznie.
Kiedy na materiał nie jest już wywierany nacisk, to właśnie ta część blachy odzyskuje swój pierwotny kształt. Zachodzi wtedy efekt sprężynowania, czyli częściowego wyprostowania się arkusza. Zwykle na skutek tego zjawiska kąt zgięcia zwiększa się o kilka stopni. Stopień nasilenia sprężynowania zależy przede wszystkim od modułu sprężystości i granicy plastyczności materiału.
CZY MOŻNA ZAPOBIEC SPRĘŻYNOWANIU?
Istnieje kilka sposobów na uniknięcie efektu sprężynowania. Przykładowo najpierw wyznacza się kąt, o jaki blacha się rozprostuje. Potem wygina się ją silniej, niż jest to wymagane dla uzyskania ostatecznego kształtu. Ten ostatni osiąga się, gdy, po ustaniu nacisku, blacha prostuje się dokładnie tyle, o ile została nadmiernie wygięta.
Alternatywą jest wymuszenie plastycznego odkształcenia na linii zgięcia w elastycznym rdzeniu wokół osi neutralnej. Uzyskuje się to, przykładając w tym miejscu większą siłę po wstępnym ukształtowaniu blachy. Innym sposobem jest poddanie blachy równoczesnemu wyginaniu i rozciąganiu za oba jej końce. Zakres zastosowania tej ostatniej metody jest niestety ograniczony.
Roboty w zginaniu blach
W tym celu stanowisko gięcia blach uzupełniono o robota przemysłowego. Arkusze do obróbki są na miejsce przewożone wózkiem widłowym na palecie. Następnie za pomocą przyssawki robot podnosi jedną blachę i umieszcza ją w stacji kontrolnej, gdzie mierzona jest jej grubość. Ten etap ma na celu potwierdzenie, że jednocześnie podniesiony został tylko jeden arkusz. Sprawdzenie to jest koniecznie, ponieważ bardzo cienkie, oliwione blachy bardzo często sklejają się ze sobą. Dalej robot umieszcza arkusz w prasie, gdzie zostaje on wygięty. Następnie gotowe blachy są z powrotem układane na palecie. Zakładaną wydajność i opłacalność udało się uzyskać dzięki temu, że wybrano model robota, który można programować w trybie offline. W rezultacie w czasie, kiedy przygotowywany jest nowy program sterujący ramieniem maszyny, ona cały czas pracuje. Minimalizuje to przestoje w razie częstej zmiany parametrów gięcia lub materiałów blach. |
JAK UNIKNĄĆ ZŁAMANIA GIĘTEJ BLACHY?
Nie zaleca się korzystania z niej wtedy, kiedy chce się uzyskać skomplikowany wzór zgięć i te pod małym kątem. Ważne ponadto jest, żeby kontrolować siłę rozciągania boków blachy. Inaczej może ona popękać.
Stopień zgięcia blachy bez obaw o jej złamanie określa jej giętkość. Można ją wyznaczyć w prosty sposób, wyginając próbkę materiału do momentu, kiedy pojawią się pęknięcia na jego powierzchni. Promień zgięcia, przy którym do tego dochodzi, określa się często jako wielokrotność grubości blachy. Im jest on większy, tym mniejsza jest jej giętkość.
Na przykład promień zgięcia równy 0 oznacza, że końce blachy da się założyć na siebie. Giętkość zależy od typu materiału oraz jego grubości. Ma na nią wpływ również stan krawędzi arkusza. Pęknięcia, które tam występują, mogą się rozprzestrzenić na całą powierzchnię. Giętkość zmniejszają także zanieczyszczenia, zwłaszcza te ostro zakończone, i luki w materiale. Zwiększa ją natomiast podwyższona temperatura i ciśnienie.
PRZYKŁADY TECHNIK GIĘCIA
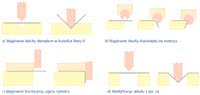
Rys. 2.
Na rysunku 2a przedstawiono jeden z popularniejszych sposobów wyginania blach za pomocą stempla w kształcie litery V. Tą metodą uzyskać można szeroki zakres kątów, zarówno rozwarte, ostre, jak i kąt prosty. W układzie z rysunku 2b arkusz jest dociskany do matrycy, a jego część wystająca poza nią jest zaginana przez stempel. Uzyskanie kąta innego niż prosty wymaga modyfikacji umożliwiającej przyłożenie siły w poziomie.
To ostatnie, ani dociskacz, nie są potrzebne w przypadku konfiguracji jak na rysunku 2c. Funkcję stempla pełni w niej obrotowy cylinder z wyciętym otworem o rozwarciu odpowiadającym kątowi wygięcia blachy. Na rysunku 2d przedstawiono z kolei modyfikację układu z rysunku 2a, w której arkusz w miejscu zgięcia nie jest bezpośrednio podparty na matrycy.
Dalej charakteryzujemy proces i wybrane techniki cięcia blach.
Jak wybrać maszynę współrzędnościową?
Wybierając maszynę współrzędnościową, zdecydować trzeba najpierw, jakiego typu urządzenie sprawdzi się najlepiej. Te, w których głowica zamontowana jest w osi pionowej, są dokładniejsze niż te z sondą w osi poziomej (o konstrukcji wysięgnikowej). Te drugie natomiast są zalecane do pomiarów większych elementów ze średnią dokładnością. Przenośne maszyny współrzędnościowe pozwalają natomiast na inspekcję na przykład wewnątrz obiektów. Jeśli badaniu będą poddawane detale o prostej geometrii albo krótkie serie produktów, można zakupić ręczną maszynę współrzędnościową. Jeżeli wymagana jest większa dokładność albo kontrolowane będą wymiary dużych partii jednakowych detali lepiej zainwestować w maszynę automatyczną. Ważne parametry to też: dokładność oraz powtarzalność pomiaru. Nie mniej istotne jest oprogramowanie. Dostępne są specjalizowane aplikacje. Ułatwiają one m.in.: zlokalizowanie i pomiary części z elementami charakterystycznymi, na przykład blach z zagiętymi krawędziami, spoinami i śrubami. |
CIĘCIE BLACH
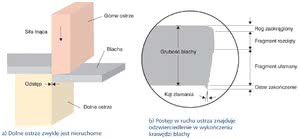
Rys. 3.
Oddzielenie części blachy następuje wówczas, gdy siła tnąca do niej przyłożona przekracza wartość graniczną. Oddziaływanie to jest wywierane przez dwa narzędzia, jedno nad, drugie pod arkuszem, na przykład górne oraz dolne ostrze. Zazwyczaj to drugie jest nieruchome (rys. 3a). Pomiędzy ich krawędziami zachowany jest odstęp, który ułatwia przecięcie materiału. Powinien on wynosić od 5 do 10% grubości arkusza.
Na rysunku 3b przedstawiono, jak postęp w ruchu ostrza znajduje odzwierciedlenie w wykończeniu krawędzi blachy. Kiedy uderza w powierzchnię arkusza, najpierw zachodzi plastyczna deformacja jej górnego rogu, w wyniku której końcówka ta zaokrągla się. Następnie ostrze na pewnym odcinku rozcina blachę. Kiedy nacisk na materiał jest już zbyt silny, arkusz pęka pod pewnym kątem. Dolny róg jest w rezultacie zwykle ostro zakończony.
WYKRAWANIE
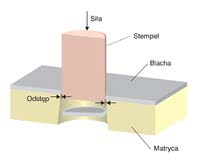
Rys. 4. Układ do wykrawania składa się ze stempla i matrycy
Uderzając w arkusz z odpowiednio dużą siłą, z blachy można wyciąć detal o w zasadzie dowolnym kształcie. Zwykle nie jest on jednak zbyt skomplikowany. Ostateczną formę elementowi nadaje się później, w kolejnych etapach obróbki. Ich celem jest także wygładzenie krawędzi detalu. Na rysunku 4 przedstawiono układ wykrawania, którego częścią jest matryca z wycięciem i stempel. Dwa ostatnie mają kształt taki jak ten, który uzyska detal. Stempel nie jest dokładnie dopasowany do wymiarów wycięcia. Podobnie jak w "zwykłym" cięciu zachowany jest odstęp o wartości od 10% do 20% grubości arkusza. W chwili, gdy stempel uderza w powierzchnię blachy, metal ugina się w tej przerwie i pęka. Następnie wycięty element wpada w wycięcie w matrycy.
Rysunek 5 przedstawia układ wykrawania, który uzupełniono o dociskacze oraz podparcie stempla. Dzięki nim wycinane detale są bardziej płaskie i mają gładsze krawędzie.
CIĘCIE BEZDOTYKOWE
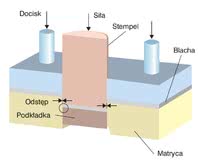
Rys. 5. Dzięki dociskaczom i podkładce wykrawane detale mają gładsze krawędzie i są bardziej płaskie
W cięciu blach zastosowanie znalazły także metody bezdotykowe, na przykład przy użyciu lasera. Jego promień jest kierowany i skupiany przez układ luster i soczewek na powierzchni arkusza. W miejscu, w którym pada taka wiązka o dużej energii, metal topi się i odparowuje. Jego pozostałości są zdmuchiwane z blachy przez strumień gazu, zwykle tlenu lub azotu. Do cięcia blach najczęściej używane są lasery gazowe CO2, o mocy do 2 kW. Głowica lasera jest ruchoma i przemieszcza się nad nieruchomym arkuszem lub pozostaje nieruchoma, podczas gdy cięty materiał znajduje się na obrotowym stole.
Lasery są używane do cięcia zarówno metali żelaznych, jak i nieżelaznych. Najłatwiej w ten sposób tnie się materiały o małej odblaskowości i małej przewodności cieplnej, na przykład stal węglową i stal nierdzewną. Te, które silnie odbijają światło i dobrze przewodzą ciepło, na przykład aluminium i stopy miedzi, wymagają użycia laserów o większej mocy.
Przykłady robotów spawalniczychRobotec AX-V6l |
![]() |
![]() |
ARC Mate 0i B
Zasięg: 1437 mm, liczba osi: 6, powtarzalność: ±0,08 mm, pozycja montażowa: podłogowa, sufitowa, pod kątem, zastosowanie: spawanie łukowe.
Cięcie laserem, w związku z tym, że nie wymaga fizycznego kontaktu z materiałem, ma liczne zalety - m.in. krawędzie są gładsze, dzięki czemu nie jest potrzebna dodatkowa obróbka. Małe jest odkształcenie blachy i w niewielkim stopniu oraz w wąskim obszarze jest ona nagrzewana. Zaletą wycinarek laserowych jest też duża precyzja.
To ostatnie odróżnia je od tych tnących plazmą. Ponadto krawędzie rozcięte przez wycinarki plazmowe są szorstkie, szczególnie w przypadku grubszych blach. Możliwość rozcinania tych ostatnich jest jednak ważna zaletą tej techniki, w porównaniu z wycinarkami laserowymi.
Blachy tnie się również przy użyciu strumienia wody pod dużym ciśnieniem, czystej lub zmieszanej ze ścierniwem. Uderzając w powierzchnię metalu, powoduje ona jej erozję. Jakość krawędzi rozcięć tak wykonanych jest zadowalająca. Ponadto cięty materiał nie jest podgrzewany.
Dalej przedstawiamy metody spawania, wskazówki odnośnie do jego realizacji oraz zagadnienie automatyzacji tego procesu.