MASZYNY KONTRA LUDZIE
Aby dorównać możliwościom człowieka, w systemach wizyjnych wykorzystuje się wysokiej klasy urządzenia, w tym kamery inteligentne oraz specjalistyczne oprogramowanie przetwarzające obraz. Mimo tego, pod pewnymi względami, przewaga człowieka nad automatycznymi systemami kontroli pozostaje ciągle duża.
Dotyczy to zwłaszcza elastyczności działania oraz zdolności do reakcji na zmienne i nieprzewidywalne sytuacje. Wadą automatycznych rozwiązań jest ścisłe realizowanie zaprogramowanego algorytmu. Odnosi się to również do systemów wizyjnych, a negatywne skutki mogą się ujawnić w przypadku błędnego lub nieścisłego algorytmu.
Z drugiej strony w środowisku przemysłowym wydajność człowieka jest jednak znacząco mniejsza. Wpływają na to takie czynniki jak nieuwaga, zmęczenie i znużenie. Automatyczne systemy inspekcji wizyjnej pozwalają uniknąć tych ograniczeń, zapewniając dużą szybkość pracy, większą dokładność i powtarzalność. Wiąże się z tym ograniczenie kosztów, zwiększenie wydajności produkcji oraz eliminacja poważnych usterek gotowych produktów wynikających z błędów na etapie montażu.
WSKAZóWKI PROJEKTOWE
W zależności od aplikacji system wizyjny powinien spełniać określone wymagania. Różne zadania wymagają implementacji konkretnych funkcji – przykładowo instalacja systemu inspekcji na taśmociągu z gotowymi wyrobami powinna umożliwiać szczegółową obserwację obiektu pod kątem występowania usterek.
Dane pochodzące z systemu wizyjnego decydują w takim wypadku o dalszym losie produktu. Na ich podstawie dany element powinien być zakwalifikowany jako dopuszczony do dalszej obróbki lub jako komponent obarczony defektem, uniemożliwiającym dalsze wykorzystanie.
W zastosowaniach związanym z montażem elementów wymagania są z kolei inne. Najczęściej obejmują możliwość skanowania powierzchni w celu zlokalizowania punktów referencyjnych. Znaczniki te są następnie wykorzystywane w określaniu pozycji i orientacji umieszczanego elementu.
Na podstawie tych przykładów wyraźnie widać, że system wizyjny zaprojektowany do konkretnych zadań niekoniecznie sprawdzi się w innym zastosowaniu. Ponadto należy rozważyć koszty związane z wdrożeniem systemu, integracją z istniejącą infrastrukturą, konserwacją, ewentualnymi modyfikacjami oraz uaktualnianiem oprogramowania.
ELEMENTY SKŁADOWE SYSTEMU WIZYJNEGO
Zasadnicze elementy systemu wizyjnego (rys. 1) obejmują kamerę, oświetlenie i elementy optyczne (obiektyw), urządzenia do akwizycji oraz przetwarzania obrazu, istotnym składnikiem jest też oprogramowanie. Często wraz z systemem stosowane są dodatkowe akcesoria – np. manipulatory pozwalające na obserwację elementu z różnych kierunków.
Niektóre systemy wykorzystują kamery analogowe. Wówczas niezbędne jest urządzenie pośredniczące pomiędzy kamerą i komputerem, czyli tzw. frame grabber. Obecnie coraz powszechniej używane są kamery cyfrowe komunikujące się bezpośrednio z komputerem. W niektórych aplikacjach stosuje się rozwiązanie jeszcze bardziej zaawansowane technicznie, którym są tzw. kamery inteligentne.Stanowią one samodzielny, zintegrowany system wizyjny.
Bez względu na stopień zaawansowania systemu, w każdym przypadku zasadniczą rolę odgrywa odpowiednie oświetlenie i wykorzystanie optyki dobranej stosownie do danej aplikacji. Jakość kontroli obiektów zależy bowiem w dużym stopniu od jakości uzyskanego obrazu. Dlatego poniżej skupiono się właśnie na opisie dwóch wymienionych elementów składowych systemów wizyjnych.
CZĘŚĆ I: OŚWIETLENIE
Istotne znaczenie dla jakości uzyskanego obrazu ma odpowiedni dobór układu oświetlenia elementu, które decyduje o tym, w jaki sposób obraz zarejestruje kamera. Przy doborze oświetlaczy powinny być brane pod uwagę m.in. geometria obiektu, struktura jego powierzchni oraz charakterystyczne cechy całego systemu.
Układ oświetlenia powinien zapewnić odpowiedni kontrast oraz minimalizować rejestrację artefaktów, które mogą prowadzić do błędnych wniosków w analizie obrazu. Stosowane są rozmaite modele oświetlaczy, m.in. układy w konfiguracji pierścienia (rys. 2) lub prostokątnej matrycy z diod LED.
W przypadku obiektów o wypukłym kształcie i błyszczącej powierzchni zalecane jest wykorzystanie oświetlaczy o kształcie kopuły (rys. 3).
Innym często stosowanym rozwiązaniem jest wykorzystanie efektu stroboskopowego. Oświetlenie poruszającego się obiektu światłem migającym pozwala uzyskać wrażenie jego zatrzymania. Trudności związane z realizacją takiego układu mogą być związane z koniecznością zsynchronizowania modulacji światła z ruchem obiektu.
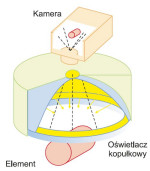
ŹRÓDŁA ŚWIATŁA
W systemach wizyjnych wykorzystywane są różne światła, przy czym najpopularniejszym obecnie rozwiązaniem jest użycie diod LED. Ich zaletą jest możliwość formowania układów w różnych konfiguracjach, zarówno w trybie pracy ciągłej, jak i w oświetleniu stroboskopowym.
Z drugiej strony problemem może być oświetlenie dużych powierzchni, ponieważ wymaga to matrycy złożonej z dużej liczby diod. Jednokolorowe oświetlenie zapewniane przez diody może być w niektórych aplikacjach zaletą. Z kolei w innych może utrudniać obserwację charakterystycznych cech obiektu.
Inne, równie popularne rozwiązania wykorzystują świetlówki oraz lampy halogenowe. W tym drugim przypadku do transmisji strumienia świetlnego stosuje się światłowody.
Zaletą takiego podejścia jest ograniczenie wpływu emisji ciepła, która jest charakterystyczna dla lamp tego typu. Wykorzystanie światłowodów pozwala budować układy w różnych konfiguracjach oraz ułatwia wymianę źródła światła w razie jego awarii.
Kolejnym często stosowanym źródłem światła są laserowe generatory linii, pomocne przy wymiarowaniu elementów. Oprócz różnorodnych źródeł światła w systemach inspekcji wizyjnej są wykorzystywane różne techniki oświetlania obiektów.
OŚWIETLACZE – KLASYFIKACJA
Ważnym terminem związanym z techniką oświetlania obiektów jest kąt bryłowy. Określa on powierzchnię na sferze, przez którą w omawianym przypadku przenika światło i w centrum której umieszczony jest obiekt.
Na tej podstawie dokonuje się podziału metod oświetleniowych stosowanych w systemach wizyjnych. W zależności od wartości kąta bryłowego oświetlenie dzieli się na punktowe (mały kąt bryłowy) i rozproszone (duży kąt bryłowy).
Oświetlenie punktowe (point-like lighting) jest proste w realizacji, ponieważ oświetlacze mają zazwyczaj niewielkie rozmiary i mogą być zainstalowane w niewielkiej odległości od obiektu. Oświetlaczem tego typu mogą być np. diody LED lub układy wykorzystujące światłowody.
Oświetlenie punktowe charakteryzuje się dużą intensywnością. Sprawdza się w tworzeniu obrazów o ostrych krawędziach i uwydatnianiu wszelkich charakterystycznych cech powierzchni obiektu.
Niewielki rozmiar sprawia, że oświetlacze tego typu są łatwiejsze w montażu niż oświetlenie rozproszone. Z drugiej strony, w przypadku silnie odblaskowych powierzchni punktowe oświetlenie sprzyja powstawania rozbłysków, które mogą oślepić kamerę i uniemożliwić uzyskanie obrazu całego obiektu.
Oświetlenie rozproszone (diffuse lighting) jest z definicji związane z dużym kątem bryłowym wokół obiektu. Przykładem oświetlaczy tego typu są świetlówki czy linijki diod LED.
Stosuje się też elementy rozpraszające przed punktowymi źródłami światła. Zaletą oświetlaczy ze światłem rozproszonym jest umożliwienie obserwacji odblaskowych powierzchni bez rozbłysków światła.
Problemem jest jednak często instalacja tego typu oświetlenia, ponieważ oświetlacz powinien otaczać obiekt. Jest to zazwyczaj związane ze złożoną konstrukcją całego systemu wizyjnego. Wadą oświetlaczy tego rodzaju jest też ryzyko uzyskania obrazów nieostrych.
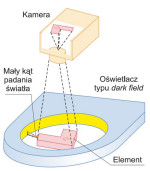
POLE JASNE, POLE CIEMNE
Jednym z pojęć związanych z techniką obserwacji jest tzw. oświetlenie w polu jasnym i polu ciemnym (rys. 4). W pierwszym przypadku światło pada pod pewnym kątem do powierzchni obiektu. Jest to metoda stosowana w większości systemów wizyjnych.
Odmianą tej techniki jest wykorzystanie oświetlenia współosiowego, które wymaga dodatkowo dzielnika wiązki (rys. 5). Promienie świetlne po odbiciu od dzielnika padają na obiekt pod kątem w przybliżeniu równym 90°.
Z kolei tzw. oświetlenie w polu ciemnym polega na bocznym oświetleniu obiektu. Wiązka światła padająca równolegle do powierzchni obiektu jest wykorzystywana np. do obserwacji wszelkich zanieczyszczeń, zarysowań i innych niedoskonałości elementu. Praktyczną realizacją oświetlenia tego typu jest ustawienie pierścienia diod LED pod bardzo małym kątem do powierzchni obiektu (rys. 6).
Trzecim sposobem jest podświetlanie obserwowanych obiektów (rys. 7). Jest wykorzystywane w dwóch przypadkach – do prześwietlania przeźroczystych i półprzeźroczystych obiektów oraz do kontroli konturów obiektów nieprzeźroczystych.
Przykładem zastosowania tej techniki jest produkcja szkła. Oświetlenie pozwala na obserwację zarówno uszkodzeń zewnętrznych, takich jak rysy i wyżłobienia, jak również defektów wewnątrz struktury, takich jak pęcherzyki powietrza i zanieczyszczenia.
Najczęściej jednak technika podświetlenia stosowana jest w obserwacji konturów nieprzeźroczystych obiektów. Obraz tego typu jest relatywnie prosty w przetwarzaniu, ponieważ jest zazwyczaj binarny i dwuwymiarowy. Innym zastosowaniem jest oświetlanie elementów w podajniku, mające na celu określenie ich orientacji przed podniesieniem przez ramię robota.
CZĘŚĆ II: OBIEKTYWY
Poprawna praca systemu wizyjnego zależy od działania części optycznej, gdyż obiektyw odwzorowuje podświetlone elementy obiektu. W wielu aplikacjach – np. w systemach kontroli poprawności ułożenia oraz w wymiarowaniu elementów, układ ten powinien odwzorowywać obiekt w stałej geometrii.
Jest to konieczne, aby można było precyzyjnie zmierzyć lub zlokalizować dany element. Układ oświetlenia oraz obiektyw powinny zatem współpracować tak, aby kns ten jest kluczowy przy planowaniu rozmieszczenia elementów systemu.
Wybierając obiektyw przeznaczony dla systemu wizyjnego, należy rozważyć kilka kwestii i pamiętać, że błędów w doborze obiektywu nie skoryguje nawet najbardziej złożone oprogramowanie. Parametry obiektywów (patrz rys. 8), w tym pole widzenia (field of view), rozdzielczość i głębia ostrości (depth of field) są warte przeanalizowania pod kątem wymagań danej aplikacji.
Należy rozważyć też właściwości elementów będących obiektem inspekcji oraz obszar obserwacji. Dyskusji wymaga też parametr zwany odległością roboczą (working distance), czyli odległość od obiektywu do obiektu. W systemach wizyjnych dystans ten jest kluczowy przy planowaniu rozmieszczenia elementów systemu.
NAJWAŻNIEJSZE PARAMETRY PRZY WYBORZE OBIEKTYWU
Projektując system wizyjny, inżynierowie często za najważniejszy parametr uważają uzyskiwane powiększenie. Należy jednak pamiętać, że powiększenie systemu zależy od różnych czynników, w tym od rozmiaru przetwornika obrazu oraz wyświetlacza. Na przykład powiększenie 50× może być uzyskane w systemie o polu widzenia 5,3mm z kamerą z przetwornikiem obrazu 1/2’’ i monitorem 13’’.
W systemie z polem widzenia 15,2mm, przetwornikiem 1’’ i monitorem 19’’ powiększenie będzie identyczne. Oba systemy w równym stopniu powiększają badany obiekt, różniąc się znacząco pod względem szczegółowych właściwości. Powiększenie w systemach wizyjnych nie jest więc najistotniejszym parametrem. O jakości uzyskiwanego obrazu oraz możliwości uwydatnienia istotnych cech obiektu decydują przede wszystkim takie parametry, jak pole widzenia i rozdzielczość.
Pole widzenia to obszar, który obiektyw powinien odwzorowywać na światłoczułym elemencie kamery. Zazwyczaj jest on opisywany w postaci długości przekątnej lub szerokości obszaru. Typowo stosunek szerokości pola widzenia do jego długości wynosi 4:3 i zależy m.in. od wymiarów pola obrazowego kamery. Dlatego rozmiar przetwornika obrazu w kamerze jest istotny przy wyborze obiektywu o wymaganej wartości ogniskowej. Znając wymaganą szerokość pola widzenia i odległość od obiektu, można dobrać obiektyw o odpowiedniej ogniskowej w zależności od wymiarów przetwornika.
ROZDZIELCZOŚĆ, ODLEGŁOŚĆ I GŁĘBIA OSTROŚCI
Rozdzielczość obiektywu związana jest ze zdolnością systemu rozróżniania szczegółów obiektu. Istnieją różne możliwości wyrażenia rozdzielczości w zależności od rodzaju obiektów, dla których parametr ten jest wyznaczany (punkty, linie). W wyznaczaniu rozdzielczości wyrażanej w parach linii na mm jest m.in. stosowany tzw. test USAF 1951 (rys. 9). Wykorzystywana jest w nim plansza, na której umieszczono paski odpowiadające różnej rozdzielczości. Linie zostały ułożone w grupy po sześć elementów, którymi są trzy poziome i trzy pionowe paski o takich samych wymiarach.
Odstęp pomiędzy paskami jest równy ich szerokości. Stosunek długości do szerokości dla każdej linii wynosi 5:1. Grupy mają numery: –6, –2, 0, 1, 2, 3, natomiast elementy są ponumerowane od 1 do 6. Rozdzielczość danego układu optycznego określa się, obserwując za jego pomocą test i odnotowując numer przypisany elementom, które dany układ pozwala jeszcze rozróżnić. Numer grupy i numer elementu umożliwiają odczytanie rozdzielczości w tablicach dołączonych do testu i opisać rozdzielczość obiektywu w konkretnej liczbie par linii na milimetr.
Odległość robocza jest to odległość od obiektywu do badanego obiektu i jest ona ograniczona dla każdego obiektywu minimalną odległością, dla której pozwala on uzyskać ostry obraz. Czasem fizyczne ograniczenia otoczenia systemu wizyjnego mogą stać się przyczyną trudności w doborze i skonfigurowaniu elementów optycznych.
Im dłuższa jest wymagana odległość robocza, tym trudniejsze staje się uzyskanie małego pola widzenia. Osiągnięcie pożądanego pola widzenia jest wówczas związane z większymi kosztami realizacji oraz zazwyczaj powoduje zmniejszenie rozdzielczości. W efekcie końcowym ograniczenia przestrzenne mogą wpłynąć na jakość uzyskiwanych obrazów.
Jeżeli obiektem inspekcji systemu wizyjnego mają być elementy trójwymiarowe, należy wziąć pod uwagę parametr zwany głębią ostrości. Określa on zdolność obiektywu do odwzorowania obiektu z wymaganą ostrością w przypadku przemieszczania obiektu w kierunku do i od obiektywu.
Duża głębia ostrości obiektywu może zniwelować ograniczenia przestrzenne otoczenia i uprościć instalację systemu. Należy przy tym pamiętać, że o ile obiektyw jest w stanie zachować wymaganą rozdzielczość w całym zakresie głębi ostrości, o tyle problemem może być zachowanie powiększenia. W systemach wizyjnych jest to szczególnie problematyczne. Rozwiązaniem może być stosowanie obiektywów telecentrycznych.
OBIEKTYWY TELECENTRYCZNE
Standardowe obiektywy odwzorowują obiekty z powiększeniem zależnym od odległości. Obiekty bliższe są powiększane w większym stopniu niż elementy oddalone od obiektywu. Efekt ten nie występuje w obiektywach telecentrycznych, które często znajdować mogą zastosowanie w systemach wizyjnych stosowanych np. w aplikacjach pomiarowych. Obiektyw telecentryczny można wyobrazić sobie jako obiektyw z nieskończenie długą ogniskową, a powiększenie uzyskiwane za jego pomocą pozostaje stałe, bez względu na odległość od obiektu.
Stałe powiększenie to szczególnie ważna właściwość wykorzystywana w wymiarowaniu obiektów trójwymiarowych. Różnica w obrazie uzyskanym w systemie ze zwykłym obiektywem i obiektywem telecentrycznym jest wyraźna (patrz przykłady w ramce). W systemach wizyjnych wdrażanych w kontroli wymiarów obraz obiektu jest porównywany z zadanymi parametrami, odpowiadającymi konkretnemu powiększeniu. Aplikacje tego typu bezwzględnie wymagają, aby powiększenie nie zmieniało się przy zmianie pozycji obiektu. W przeciwnym wypadku przy każdej zmianie pozycji obiektu wynik byłby inny.
Można wyodrębnić kilka przypadków, w których wykorzystanie obiektywu tego typu jest zalecane. Obiektyw telecentryczny powinien być użyty w sytuacji, gdy obiekt badany ma znaczną grubość. W przypadku, gdy planowane są pomiary obiektu w różnych płaszczyznach oraz gdy nie jest znana odległość obiektu od obiektywu, także warto zastosować obiektyw telecentryczny. Przykładem obiektów, do inspekcji których z pewnością lepiej wykorzystać ten rodzaj obiektywów, są wszelkiego rodzaju otwory. Obiektywy telecentryczne są także powszechnie stosowane w systemach kontroli wizyjnej w produkcji układów scalonych.
WPŁYW OTOCZENIA NA ELEMENTY OPTYKI
Projektując system wizyjny, należy rozważyć również wpływ czynników związanych ze środowiskiem jego pracy, takich jak refl eksyjność obiektu, oświetlenie, temperatura, wibracje i zanieczyszczenia. Wpływ zewnętrznego oświetlenia ograniczają specjalnie dobrane osłony obiektywów. Refl eksy powstające na odblaskowych obiektach niwelowane są przez dobór odpowiedniego oświetlenia, np. rozproszonego lub przy wykorzystaniu układów z filtrami polaryzacyjnymi (patrz ramka).
Temperatura oraz wibracje generowane przez maszyny mogą w dużym stopniu wpłynąć na jakość obrazu uzyskiwanego w systemie wizyjnym zainstalowanym w środowisku przemysłowym. Wysoka temperatura otoczenia wywołać może rozszerzanie się elementów optyki, poza tym nie wszystkie układy optyczne tolerują duże i szybkie zmiany temperatury otoczenia.
Do inspekcji obiektów o bardzo dużych temperaturach najlepiej jest więc korzystać z obiektywów o dużej ogniskowej, zapewniających dużą odległością roboczą. Natomiast wibracje układu optycznego w systemie wizyjnym można zredukować, instalując obiektyw bezpośrednio na izolującej platformie lub stole.
Innym zagrożeniem dla elementów optycznych są zanieczyszczenia występujące w danym środowisku. Do pracy w trudnych warunkach są przeznaczone elementy wytrzymujące długotrwałą pracę w otoczeniu szkodliwych substancji. Elementy optyczne tego typu są odporne na kontakt z płynami, ścieranie i korozję. Są zabezpieczone przed przenikaniem pyłów i charakteryzuje je wytrzymałość na uszkodzenia mechaniczne.
CZĘŚĆ III: KAMERY W SYSTEMACH WIZYJNYCH
Trzecią grupą elementów składowych systemów wizyjnych są kamery. W tego typu aplikacjach stosuje się podziały na kamery obrazowe (areascan) i linijkowe (linescan), urządzenia analogowe, cyfrowe i inteligentne (smart camera), a także kamery monochromatyczne i kolorowe. Ich dobór do aplikacji jest jedną z istotniejszych kwestii przy tworzeniu systemu wizyjnego. Decyzja o tym, jaką kamerę zastosować w konkretnej aplikacji wymaga przeanalizowania wad i zalet poszczególnych ich typów, co uczynione zostało w drugiej części artykułu, która opublikowana będzie w lutowym wydaniu APA.
Monika Jaworowska
Więcej informacjiKilkaset interesujących wdrożeń systemów wizyjnych znaleźć można m.in. na stronie firmy Cognex pod adresem www.cognex.com |