Bezpieczeństwo i higiena pracy są regulowane przepisami. Można w nich znaleźć wytyczne w zakresie organizacji, wyposażenia i użytkowania stanowisk pracy. Przykładem jest rozporządzenie ministra gospodarki z zalecaniami dla przemysłu papierniczego.
Uregulowano w nim ochronę przed wysokimi temperaturami, nakazując aby powierzchnie maszyn nagrzewające się powyżej +47°C, z którymi mogą mieć kontakt pracownicy były zasłonięte tak by zapobiec ich poparzeniu. W osłony należy także wyposażyć okorowarki, by chronić personel przed wiórami, urządzenia odprowadzające stop sodowy, by uniknąć poparzenia jego odpryskami i walce odwadniarek mas włóknistych, maszyn papierniczych i tekturniczych. Podczas czynności z użyciem wapna należy ograniczyć pylenie. Nie wolno korzystać ze sprężonego powietrza aby usuwać pyły. Zbiorniki trzeba wyposażyć w zabezpieczenia zapobiegające oblaniu personelu. Górne krawędzie tych otwartych, kadzi oraz mieszalników powinny być zabezpieczone barierką. Z kolei zbiorniki z ługami i kwasami muszą być zakryte pokrywami. Pomieszczenia, gdzie wydzielają się szkodliwe pary, dymy, cuchnące i drażniące wyziewy należy wentylować, a poziom ich stężeń powinien być monitorowany oraz sygnalizowany. Na wypadek przekroczenia tych dopuszczalnych sterowanie procesami w warzelniach, bielarniach i rębalniach powinno odbywać się z kabin klimatyzowanych i wyciszonych. Warzelnie, bielarnie i kotłownie sodowe muszą mieć co najmniej dwa dodatkowe wyjścia ewakuacyjne. Tam, gdzie może się rozlać masa włóknista, papiernicza, ciecze warzelne i inne podłogi powinny mieć spadek w kierunku kanałów ściekowych i być wykonane z materiału antypoślizgowego.
Bezpieczna obsługa obrabiarek do drewna
Kolejnym przykładem jest rozporządzenie w zakresie bezpieczeństwa i higieny pracy przy obsłudze obrabiarek do drewna. Zawiera m.in. wytyczne dotyczące ubioru ich operatorów. Powinni nosić nakrycia głowy zakrywające włosy oraz odzież roboczą bez odstających i luźno zwisających części. Niedozwolone jest wkładanie rękawic i owijanie dłoni bandażami, jeśli istnieje zagrożenie ich pochwycenia. Jeżeli możliwe jest zetknięcie się pracownika z wirującymi częściami maszyny, narzędziami tnącymi, przedmiotami obrabianymi, należy stosować urządzenia ochronne. Obrabiarki trzeba wyposażyć w zaciski i dociski zabezpieczające obiekt obróbki przed odrzutem lub wyrzutem.
Przedmiot i narzędzia tnące należy mocować w sposób uniemożliwiający ich wyrwanie albo zmianę położenia pod wpływem sił skrawania albo sił odśrodkowych. Pracownicy powinni się znajdować poza strefą zagrożoną odrzutem lub wyrzutem. Nie wolno trzymać obiektu obróbki w dłoni. Długie przedmioty wymagają podpórek albo innych rozwiązań, które zapewnią im stabilność.
Nie można otwierać ani zdejmować osłon pracujących obrabiarek, czyścić ich, sprawdzać precyzji obróbki ani usuwać wiórów. Przed rozpoczęciem konserwacji i naprawy maszyny trzeba wyłączać i zabezpieczać przed przypadkowym uruchomieniem. Jeżeli przy danej obrabiarce pracuje więcej niż jedna osoba, wszystkie powinny zostać uprzedzone o zamiarze jej ponownego uruchomienia.
Bezpieczne przetwórstwo tworzyw sztucznychWytyczne rozporządzenia w zakresie BHP obowiązującego w przetwórstwie tworzyw sztucznych dotyczą m.in. operacji ich rozdrabniania i mielenia. Zgodnie z nimi, jeśli maszyny używane w tych celach emitują hałas o natężeniu powyżej dopuszczalnego, powinny być instalowane w oddzielnym pomieszczeniu. Te pylące powinny być wyposażone w system odpylający. Ich otwory zasypowe muszą mieć zabezpieczenia chroniące przed wyrzutem materiału. Odseparować należy również mieszalniki typu otwartego, zwłaszcza do rozpuszczania polimerów syntetycznych, zaś w tych typu zamkniętego nie mogą się gromadzić szkodliwe gazy ani pary, które w wyniku ich odpowietrzenia powodowałyby przekroczenie dopuszczalnych stężeń szkodliwych substancji. Maszyny z walcami, bębnami i rolkami muszą być zabezpieczone przed przypadkowym dostępem personelu do strefy zagrożenia i wciągnięciem jego odzieży albo rąk. Zamykanie form prasowania przetłocznego, formowania wtryskowego, wytłaczania z rozdmuchiwaniem, termoformowania oraz formowania rotacyjnego powinno być w maksymalnym stopniu zautomatyzowane. Muszą też być zabezpieczone przed przypadkowym otwarciem – w razie nieplanowanego otwarcia formy proces powinien zostać wstrzymany. |
BHP na stanowiskach odlewu metali
Rozporządzeniem regulowane są także operacje obróbki metali, na przykład proces odlewu stopów żelaza i metali nieżelaznych. Zgodnie z nim nie można wykonywać żadnych prac bezpośrednio pod zawieszonymi urządzeniami albo przedmiotami wypełnionymi stopionym metalem ani w zasięgu jego rozprysku podczas ich przemieszczania. Jego spust powinien poprzedzać sygnał dźwiękowy. Kadzie napełnia się stopionym metalem do poziomu niegrożącego rozlaniem podczas transportu. Pojazdy do ich przewozu powinny być wyposażone w rozwiązania zapewniające ich stabilność oraz sygnalizację świetlną i dźwiękową. Drogi przenoszenia przez pracownika kadzi z ciekłym metalem przy ręcznym zalewaniu form nie mogą się krzyżować z innymi. W razie ręcznego wykonywania form w pozycji klęczącej, nie dłużej niż 4 godziny, pracownik musi nosić ochraniacze na kolana. Przed wejściem pracownika do pieca odlewniczego w celu jego konserwacji należy odłączyć media zasilające i wystudzić jego komorę do temperatury poniżej +50°C. Niedopuszczalne jest też ręczne czyszczenie odlewów, których temperatura powierzchni przekracza tę wartość.
Na wypadek ekspozycji pracownika na promieniowanie cieplne, rozpryski stopionego metalu czy płomienie podczas prac w bezpośredniej bliskości stopionego metalu, trzeba stosować odpowiednie środki ochrony indywidualnej. Pomieszczenia, w których personel może się poparzyć, a jego odzież zapalić, należy wyposażyć w wodne natryski ratunkowe, umywalki i podręczne środki ochronne do przemywania lub przepłukiwania oczu w razie dostania się do nich ciała obcego.
BHP w produkcji spożywczejKilka rozporządzeń dotyczy również różnych gałęzi przemysłu spożywczego. Przykładem jest to w sprawie BHP w zakładach przetwórstwa owoców i warzyw. Zgodnie z nim przenośniki mechaniczne stałe, bez wyłączników linkowych, wymagają wyłączników awaryjnych. Sprzęt do spłukiwania hydromechanicznego należy zabezpieczyć przed niekontrolowanym obrotem wokół własnej osi. Studzienki i kanały wymagają pokryw lub krat. Zbiorniki spławne na poziomie albo poniżej poziomu terenu należy zabezpieczyć na przykład murem (min. 1,1 m). Kosze zasypowe krajalnic wymagają rusztów ochronnych. Zbiorniki z miazgą połączone z prasą i napełniarkami produktów płynnych trzeba zabezpieczyć przed przelewaniem się. Stacje wyparne wymagają zaworów bezpieczeństwa. Kondensat należy odprowadzać przez odwadniacze. Kotły otwarte wywrotne wymagają mechanizmów stabilizacji położenia w każdej pozycji, a urządzenia do napełniania, zamykania i etykietowania opakowań szklanych osłon chroniących na wypadek rozprysku szkła. Przepisy BHP dla branży cukierniczej z kolei zalecają m.in. wyposażenie kotłów warzelnych przechylnych w mechanizm zapewniający równomierny, bezpieczny przechył i utrzymanie w stabilnej pozycji, a tych do zagęszczania roztworów w urządzenia wyciągowe usuwające opary na zewnątrz budynku. Instalacja gazowa prażaków musi mieć samoczynne urządzenie zamykające dopływ gazu do palników. Stoły chłodzone wodą trzeba zabezpieczyć przed niekontrolowanym przechyleniem się płyty. Przeciągarki wymagają wyłącznika krańcowego, a zawijarki wyrobów cukierniczych wyłączników przyciskowych przy stanowiskach obsługi. Górna część krajalnicy musi mieć osłonę uchylną z wyłącznikiem krańcowym, a dolna powinna być całkiem osłonięta. Formy do wypieku płatów waflowych wymagają mechanizmu blokady otwarcia ich pokrywy. Pojemniki i opakowania przewożone na wózkach trzeba zabezpieczać, żeby nie spadały ani się nie przemieszczały. |
Bezpieczeństwo galwanotechniki
W rozporządzeniu dotyczącym BHP w procesach galwanotechnicznych wiele uwagi poświęca się pomieszczeniom. Niedozwolone jest korzystanie z tych poniżej poziomu terenu. Jeżeli mieszczą się w budynku wielopiętrowym, musi być zapewniona szczelność stropów nad i pod nimi i spełnione następujące warunki: ściany, sufity oraz podłogi powinny być odporne na substancje z kąpieli galwanicznej, łatwo zmywalne, nienasiąkliwe i bez pęknięć, a ich złącza szczelne. Stosować w nich trzeba też rozwiązania zabezpieczające przed poślizgiem, wpadnięciem do wanny galwanicznej i rozlaniem kąpieli, umożliwiające bezpieczny odpływ w razie wycieku i zapobiegające mieszaniu się różnych kąpieli albo ścieków.
Ręczne zanurzanie i wyjmowanie przedmiotów z kąpieli jest dozwolone, o ile ich całkowita masa nie przekracza 10 kg na pracownika, a odległość między zewnętrzną krawędzią wanny a miejscem ich zawieszania nie przekracza 0,8 m. Dystans między górną krawędzią wanny a poziomem podestu powinien wynosić od 0,8 do 1,1 m. Przejście pomiędzy wannami musi mieć z kolei: 1 m, jeżeli nie jest wykorzystywane do ich obsługi, 1,2 m, jeśli są obsługiwane tylko z jednej strony, a 1,5 m, gdy z obu stron. Przedmioty należy zanurzać i wyjmować tak, aby nie rozlewać ani nie rozpryskiwać kąpieli. Te zanurzane w temperaturze powyżej +100°C muszą być suche.
By zmniejszyć emisję szkodliwych substancji, należy stosować środki ograniczające parowanie, a w czasie przerw w pracy przykrywać wanny pokrywami. Galwanizernie powinny być wentylowane. Wentylację należy projektować tak, by ograniczać ryzyko powstania atmosfery wybuchowej. Wanny z kąpielą wydzielającą substancje szkodliwe, na które pracownicy mogą być bezpośrednio narażeni, muszą być wentylowane miejscowo.
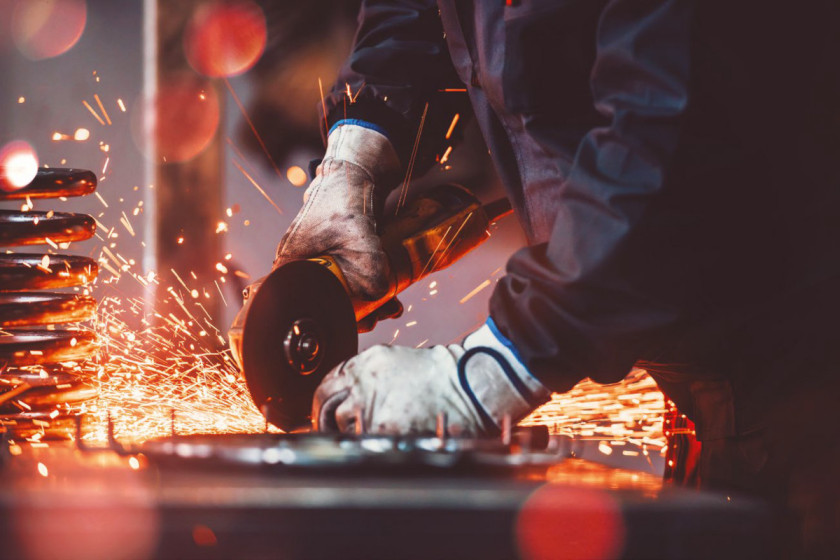
Wytyczne dla spawalni
W przypadku spawania organizacja pomieszczenia również ma kluczowe znaczenie. Zgodnie ze stosownym rozporządzeniem spawalnia powinna mieć co najmniej 3,75 m wysokości, a ściany kabiny spawalniczej najmniej 2 m z zachowaniem przy podłodze szczeliny wentylacyjnej. Ściany i strop spawalni oraz wnętrze kabiny spawalniczej należy malować farbami matowymi. Ścianki tej drugiej powinny być wykonane z materiału niepalnego albo trudno palnego. Musi też tłumić szkodliwe promieniowanie optyczne. Podłoga w spawalni i na stanowiskach także powinna być wykonana z materiału niepalnego.
Na każdego pracownika najliczniejszej ze zmian powinno przypadać przynajmniej 15 m³ wolnej objętości pomieszczenia, a na każde stanowisko najmniej 2 m² wolnej przestrzeni podłogi.
Spawalnia powinna być wyposażona w system wentylacji. Dodatkowo stanowiska muszą mieć lokalne wyciągi. Powinny być także wyposażone w stół i/albo odpowiednie oprzyrządowanie, które umożliwi bezpieczne wykonanie spawów. Przedmioty o dużych wymiarach albo o masie ponad 25 kg muszą być przemieszczane za pomocą urządzeń do transportu pionowego albo poziomego. Stanowiska, na których są używane ręczne palniki gazowe, powinny być wyposażone w osprzęt do ich bezpiecznego odkładania albo zawieszania i naczynie z wodę do ich schładzania. Spawanie łukowe elektrodami otulonymi wymaga pojemnika na resztki (ogarki) elektrod.
W spawalni ani na stanowisku spawania nie powinny być przechowywane materiały łatwopalne. Rozmieszczenie wyposażenia i obrabianych przedmiotów musi umożliwiać szybkie i bezpieczne opuszczenie stanowiska przez pracowników. W ramce przedstawiamy również wytyczne BHP na stanowiskach w produkcji spożywczej i przetwórstwie tworzyw sztucznych.
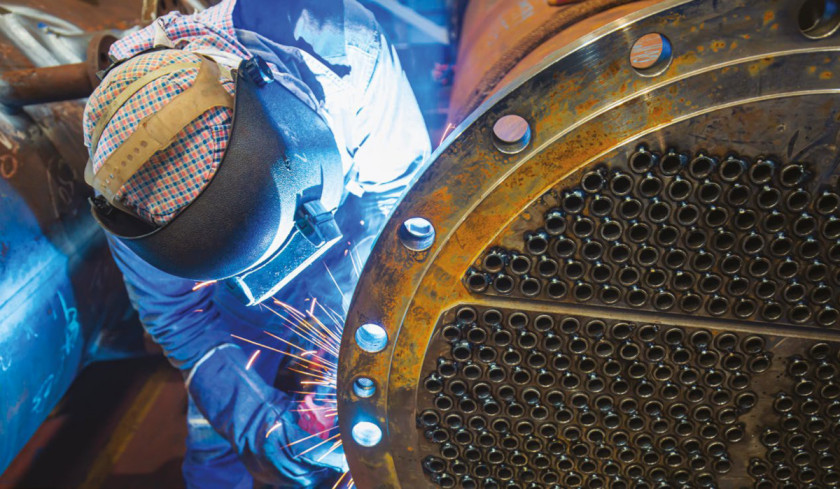