Systemy wizyjne składają się z dwóch części: sprzętowej, której zadaniem jest rejestrowanie i akwizycja obrazów, oraz oprogramowania, które odpowiada za analizę i uzyskanie oczekiwanych informacji. Z tych ostatnich korzystać mogą urządzenia, z którym współpracuje dany system. Przykładami są sterowane wizyjnie maszyny, które sortują produkty w ramach kontroli ich jakości, a także roboty przemysłowe, na przykład pracujące na liniach montażowych, liniach pakowania, malujące, spawające. Przewagę systemy wizyjne zawdzięczają szybkości - mogą wykonywać inspekcję od kilkuset do nawet kilku tysięcy detali w ciągu minuty, oraz dokładności - jeżeli są wyposażone w układ optyczny i kamerę o odpowiednio dużej rozdzielczości, są w stanie rozróżnić szczegóły o zbyt małych rozmiarach, aby mogło je dostrzec ludzkie oko oraz powtarzalności. Ponieważ, jak już wspomniano, nie męczą się i nie rozpraszają, łącznie cechy systemów wizyjnych przyczyniają się do poprawy jakości i wydajności produkcji.
Rozwiązywanie problemów, cz. 1
Jeżeli jakość obrazu uległa znaczącemu pogorszeniu, kolejnym krokiem powinno być ustalenie, czy przyczyną jest kamera, czy obiektyw. Problemy z kamerą albo z samym czujnikiem obrazu mają z reguły wpływ na cały obraz. Najczęstszymi ich objawami są m.in.: zmiany w jasności i kontraście, o ile wykluczy się to, że ich powodem są zmiany oświetlenia, obecność szumów oraz przesunięcia w balansie bieli kolorowych zdjęć. Problemy z powodu obiektywów są z kolei zwykle widoczne miejscowo, na przykład objawiają się jako zmiany ostrości na obrazie albo zaciemnienia na jego rogach. Prawdopodobnymi powodami są: rozregulowanie obiektywu, albo jeżeli podejrzewamy problem z soczewkami, ich uszkodzenia, na przykład zarysowania. |
ZALETY SYSTEMÓW WIZYJNYCH
Ponadto wiele korzyści przynosi wyeliminowanie bezpośredniego kontaktu między obiektem inspekcji a komponentami systemu kontroli jakości. Przede wszystkim unika się dzięki temu przypadkowego zniszczenia tego pierwszego i zużycia w miarę użytkowania elementów tego drugiego.
Z kilku powodów warto ograniczyć udział ludzi w procesie produkcyjnym. Na przykład zapewnia to oszczędność miejsca zajmowanego przez ich stanowiska, a gdy jeden system wizyjny zastępuje jednocześnie wielu ludzi, znacząco zmniejszają się koszty pracy.
W przypadku linii produkcyjnych niektórych produktów, na przykład w branży farmaceutycznej i spożywczej, wizyjna kontrola jakości bez udziału ludzi jest koniecznością ze względu na wysokie wymagania w zakresie higieny. W innych z kolei dzięki niej można ochronić pracowników przed kontaktem z niebezpiecznymi czynnikami, m.in. warunkami otoczenia, substancjami, maszynami. Sterowanie wizyjne robotów również poprawia jakość produkcji oraz jej elastyczność, dzięki temu, że łatwiej mogą się dostosować do zmienności cech detali, którymi operują.
Zastosowania systemów wizyjnych dzieli się na cztery kategorie zadań. Do pierwszej zaliczane jest nakierowywanie innych urządzeń na obiekt ich działań.
|
KLASYFIKACJA ZADAŃ
W tym celu system wizyjny ustala jego położenie i orientację w przestrzeni 2D lub 3D w zależności od potrzeb. Informacje te są porównywane z wartościami oczekiwanymi. Jeżeli różnice pomiędzy nimi nie przekraczają wartości dopuszczalnych, wiadomo, że obiekt znajduje się we właściwym miejscu.
W przeciwnym wypadku do kontrolera robota lub innej maszyny, która jest sterowana wizyjnie, wysyłana jest informacja o odchyłce. Przykładowe zadania, które dzięki systemom wizyjnym są wykonywane znacznie szybciej i dokładniej niż ręczne pozycjonowanie, to: rozładowywanie oraz załadowywanie palet, podnoszenie części z przenośnika, wyjmowanie ich z kosza i wyrównywanie ich względem innych.
Kolejnym zadaniem systemów wizyjnych jest rozpoznawanie obiektów na podstawie oznakowania. Rozróżnia się różne typy symboli, na przykład kody kreskowe jednowymiarowe i dwuwymiarowe, oznaczenia wykonane bezpośrednio na produkcie na przykład przez wypalanie laserem, żłobienie, wytrawianie albo malowanie i nadruki na opakowaniach i etykietach na nie naklejanych. Poza tym systemy wizyjne identyfikują obiekty na podstawie unikalnych cech (kształtu, rozmiaru, koloru).
Następnym ich zadaniem są pomiary. Dokonują ich, mierząc odległości między dwoma lub większą liczbą punktów odniesienia zlokalizowanych na obiekcie. W oparciu o nie przeprowadza się także kontrolę jakości. Systemy wizyjne wykrywają różne wady obiektów inspekcji, takie jak m.in. ich uszkodzenia, zanieczyszczenia, niekompletność i problemy w działaniu. W ramce przedstawiamy przykłady zastosowania systemów wizyjnych w wymienionych kategoriach zadań.
Kamera sprawdza rozmiary otworówPewna chińska firma, która produkuje podzespoły do urządzeń elektroniki użytkowej na zlecenie kilku czołowych przedsiębiorstw z tej branży, poszukiwała sposobu zautomatyzowania kontroli jakości obudów aparatów fotograficznych. Sprawdzenia poprawności wykonania wymagają rozmiary wyciętych w nich otworów, w które wkładane są przyciski i wizjer. Inspekcja jest konieczna, jeżeli bowiem otwory są za małe albo za duże występują problemy na etapie montażu i później podczas korzystaniu z tego sprzętu. Niezadowolenie użytkowników odbija się na reputacji producenta, ten natomiast obwinia o to podwykonawcę. Ze względu na rangę klientów i intratność zamówień na obudowy aparatów produkowanych na masową skalę ten ostatni do kontroli jakości przywiązuje dużą wagę. Dlatego pracowników trzeba dobrze do niej przygotować. W tym celu szkolą się nawet kilka miesięcy, a nim rozpoczną pracę na stanowisku inspekcji, muszą uzyskać specjalny certyfikat. Produkcja na masową skalę wymaga zaangażowania do kontroli jakości wielu pracowników. Łącznie ze złożonym procesem ich szkolenia przekłada się to na duże koszty. Ponadto nawet najlepsze przeszkolenie nie zapobiegnie zmęczeniu pracowników, co odbija się negatywnie na dokładności inspekcji. Presja kosztów i jakości skłoniła firmę do zainwestowania w system wizyjny. Wybrano taki, który współpracuje z komputerem (PC-based), z kamerą o rozdzielczości 5 Mpix oraz interfejsem GigE. Zamocowano ją na ruchomej platformie, która przemieszcza się nad przenośnikiem we wszystkich kierunkach zgodnie z zaprogramowaną sekwencją ruchów, które naprowadzają kamerę kolejno nad wszystkie otwory. Obiekty inspekcji podświetlane są lampami LED. Sygnał wyzwalający kamerę dociera do niej ze sterownika PLC, który potem odbiera sygnał zakończenia inspekcji. System wizyjny zorganizowany w ten sposób rozpoznaje ponad 10 typów otworów, kwadratowych i okrągłych, różniących się rozmiarami, w obudowach kilkunastu różnych modeli aparatów. Mierzy on średnicę każdego wycięcia z dokładnością rzędu setnych części milimetra. Sprawdzana jest też jego kolistość. |
KOMPONENTY LINII WIZYJNEJ INSPEKCJI I STEROWANIA
System wizyjny to tylko jeden z kilku komponentów kompletnej linii, czy to sterowania robotem przemysłowym, czy kontroli jakości. Poza sekcją złożoną z kamery, obiektywu, oświetlenia oraz oprogramowania do przetwarzania obrazów, która odpowiada za: rejestrację obrazu obiektu inspekcji, jego obróbkę w celu uzyskania potrzebnych danych oraz opracowanie informacji zwrotnej, która na przykład w przypadku systemu kontroli jakości stwierdza, czy obiekt spełnia stawiane mu wymagania, wyróżnia się jeszcze trzy sekcje. Ich zadaniem jest współpraca z system wizyjnym w celu automatyzacji zadania inspekcji.
Jedną z nich jest system transportu, dzięki któremu obiekty poddawane kontroli znajdują się w polu widzenia kamery. Realizuje się to, wykorzystując do ich przenoszenia przenośniki albo mechanizm, który przemieszcza kamerę nad nimi.
Częściami zautomatyzowanej linii kontroli jakości są też: czujniki, których zadaniem jest określenie położenia obiektu inspekcji oraz mechanizm do usuwania wybrakowanych egzemplarzy. Ten drugi jest sterowany w zależności od informacji zwrotnej z systemu wizyjnego. Dalej szerzej opisujemy najważniejsze komponenty tego ostatniego.
Algorytmy przetwarzania obrazówDopasowanie wzorca
W pierwszym etapie, tzw. fazie uczenia się, przetwarzany jest wzorzec, na przykład wyznaczane są jego krawędzie, co ma na celu określenie jego cech, które wykorzystane zostaną podczas drugiego etapu, czyli porównywania z obrazami obiektów badanych. Faza uczenia jest dość skomplikowana, a obliczenia zająć mogą kilka sekund przy dużych lub złożonych obiektach. Przeprowadza się ją jednorazowo dla każdego wzorca, a dane zapisuje i wykorzystuje wielokrotnie. Wybór odpowiedniego wzorca ma bardzo duży wpływ na prędkość oraz dokładność analizy i warto tutaj kierować się kilkoma zasadami. Wzorzec powinien być asymetryczny, żeby możliwe było zidentyfikowanie go w określonym położeniu. Przykładowo okrągły otwór nie będzie ze sobą niósł informacji o tym, czy obiekt nie został obrócony. Istotny jest również sam charakter wzorca. Jeżeli jako wzorzec zostanie wybrany skomplikowany element, jego odnalezienie w obrazie obiektu zajmie więcej czasu. Jeżeli natomiast wzorzec będzie zbyt prosty - w efekcie może dojść do zafałszowania wyników porównywania. Jeżeli za wzorzec przyjęto prosty element, należy pamiętać, że powinien on mieć odpowiednio duży rozmiar. Jeżeli jest to zwykły otwór, to jako wzorzec warto wybrać fragment obrazu obejmujący wystarczająco duży fragment otoczenia otworu. Informacje o otoczeniu pozwolą odróżnić konkretny obiekt od podobnych elementów. Detekcja krawędzi
W związku z tym istnieje ogromna liczba stosowanych wartości progowych wykorzystywanych filtrów, które odpowiadają rozmaitym typom krawędzi. Wybór algorytmu detekcji krawędzi zależy w dużym stopniu od samej aplikacji. Można przykładowo zdefiniować go dla momentu pierwszego przekroczenia wartości progowej lub przy kolejnej zmianie jasności obrazu. Dotyczy to też sposobów detekcji orientacji krawędzi. Filtry optymalizowane są pod kątem wyszukiwania krawędzi w poziomie, pionie i po przekątnej. |
PRZEGLĄD TECHNIK OŚWIETLENIA
Sposób oświetlenia obiektu inspekcji ma duży wpływ na jakość obrazów rejestrowanych przez kamerę. Dobierając je, należy w związku z tym uwzględnić szereg czynników, przede wszystkim właściwości obiektu, takie jak jego geometria i struktura powierzchni, oraz specyficzne cechy całego systemu. Oświetlenie musi zapewnić odpowiedni kontrast i nie powinno powodować efektów, takich jak na przykład odbicia, które utrudniają analizę obrazu.
Stosowane są różne modele oświetlaczy, na przykład w formie pierścienia lub prostokątnej matrycy z diod LED. Obiekty wypukłe i błyszczące najlepiej oświetlać pod kopułą. Wykorzystuje się też efekt stroboskopowy. Oświetlając w ten sposób obiekt w ruchu, uzyskuje się wrażenie jego zatrzymania.
Oświetlenie w systemach wizyjnych można również podzielić na punktowe i rozproszone. Pierwsze ma zwykle niewielkie rozmiary, można je zainstalować blisko obiektu, charakteryzuje je duża intensywność, a obrazy obiektów przez nie oświetlanych mają ostre krawędzie i uwydatniają wszelkie charakterystyczne cechy ich powierzchni. Niestety, w przypadku silnie odblaskowych powierzchni punktowe oświetlenie sprzyja powstawaniu rozbłysków, które mogą oślepić kamerę.
Oświetlacze rozproszone z kolei pozwalają na obserwację odblaskowych powierzchni bez rozbłysków światła. Niestety, czasem mogą powodować powstawanie obrazów nieostrych.
Jeżeli światło pada pod pewnym kątem do powierzchni obiektu, mamy oświetlenie z tzw. polem jasnym. W przypadku oświetlenia współosiowego z kolei promienie świetlne po odbiciu od dzielnika padają na obiekt pod kątem w przybliżeniu równym 90°. Oświetlenie w polu ciemnym polega na bocznym oświetleniu obiektu. Do prześwietlania przezroczystych i półprzezroczystych obiektów oraz do kontroli konturów obiektów nieprzezroczystych wykorzystuje się natomiast podświetlanie.
Rozwiązywanie problemów, cz. 2
Przyczyną może być problem sprzętowy. Jeżeli natomiast chodzi o oprogramowanie, to przeważnie nie przestaje ono raptownie działać prawidłowo, chyba że zostały w nim wprowadzone jakieś zmiany. Jeśli zatem w ostatnim czasie zostało ono zaktualizowane lub zmodyfikowano jego wcześniejsze ustawienia, by sprawdzić, czy to jest powodem dysfunkcji, warto na próbę przywrócić wcześniejszą wersję oprogramowania. Jeśli to nie pomoże, zyskujemy pewność, że problem ma charakter sprzętowy, chyba że zostały zmienione kryteria, przy których system wizyjny uznaje wyrób za pełnowartościowy. Jeżeli na przykład tolerancję wykonania jakiegoś jego wymiaru zwiększono o kilka procent, można oczekiwać, że liczba wyrobów uznanych za prawidłowe może znacznie wzrosnąć. |
NAJWAŻNIEJSZE PARAMETRY OBIEKTYWÓW
Najważniejsze parametry obiektywów to pole widzenia, rozdzielczość, głębia ostrości i odległość robocza. Pierwszy to obszar, który obiektyw powinien odwzorowywać na światłoczułym elemencie kamery. Zwykle opisuje go długość przekątnej lub szerokość obszaru. Typowo stosunek szerokości pola widzenia do jego długości wynosi 4:3 i zależy od wymiarów pola obrazowego kamery.
Dlatego rozmiar przetwornika obrazu w kamerze jest istotny przy wyborze obiektywu o wymaganej wartości ogniskowej. Znając wymaganą szerokość pola widzenia oraz odległość od obiektu, można dobrać obiektyw o odpowiedniej ogniskowej w zależności od wymiarów przetwornika.
Rozdzielczość obiektywu charakteryzuje zdolność systemu do rozróżniania szczegółów obiektu. Odległość robocza jest to odległość dzieląca obiektyw od badanego obiektu. Jest ona dla każdego obiektywu ograniczona minimalną odległością, dla której można uzyskać ostry obraz. Im dłuższa jest wymagana odległość robocza, tym trudniej uzyskać małe pole widzenia. Osiągnięcie tego pożądanego jest wówczas związane z większymi kosztami realizacji i zazwyczaj powoduje zmniejszenie rozdzielczości.
Głębia ostrości jest ważna w przypadku obiektów trójwymiarowych. Określa ona zdolność obiektywu do odwzorowania obiektu z wymaganą ostrością w przypadku jego przemieszczania się w kierunku do i od obiektywu. Duża głębia ostrości obiektywu upraszcza instalację systemu.
O ile obiektyw jest w stanie zachować wymaganą rozdzielczość w całym zakresie głębi ostrości, o tyle problemem może być zachowanie powiększenia. Rozwiązaniem są obiektywy telecentryczne odwzorowujące obiekty z powiększeniem niezależnym od odległości. Na koniec warto dodać, że błędów w doborze obiektywu nie skoryguje nawet najbardziej złożone oprogramowanie systemu wizyjnego.
Kamera zastępuje mikrometr
Tradycyjnie pomiary wykonuje się przy użyciu kontaktowych, ręcznych przyrządów pomiarowych. Przykładem jest mikrometr. Pracownik, który go używa, na podstawie wyników pomiaru podejmuje decyzję o tym, czy zwymiarowany wyrób spełnia wymagania, czy nie. Wraz ze wzrostem oczekiwań odbiorców w kwestii jakości wykonania, wymiarów i wykończenia powierzchni, a równocześnie dlatego, że dla utrzymania rentowności producenci muszą zwiększać wydajność produkcji, pomiary manualne przestają się opłacać. W opisywanym zakładzie obecnie dziennie produkowanych jest 300 tys. sztuk wyrobów. Łatwo sobie wyobrazić, jak wielu ludzi, którzy na dodatek musieliby pracować na zmiany całą dobę, jest potrzebnych do skontrolowania jakości w tempie zgodnym z taką wydajnością produkcji. Ponadto wiele czynników wpływa na wiarygodność ich oceny (zmęczenie, brak uwagi). Dlatego opisywana firma zdecydowała się zastąpić inspekcję manualną systemem wizyjnym z kamerą linijkową, którą zamontowano nad przenośnikiem transportującym wytłoczone elementy, dodatkowo zintegrowanym z robotem przemysłowym. Zadaniem tego pierwszego jest pomiar kluczowych wymiarów wyrobu. Jeżeli wymiary któregoś z nich nie spełniają założonych kryteriów, informacja o tym jest przesyłana do sterownika robota, który zdejmuje wadliwy wyrób z przenośnika. W ciągu godziny przetwarzanych jest ponad 2 tysiące obrazów. Automatyczna inspekcja zapewnia nie tylko większą dokładność i powtarzalność, ale jednocześnie nie jest przyczyną przestojów w produkcji. |
KAMERY, KOMUNIKACJA, OPROGRAMOWANIE
Kamera zawiera przetwornik, na którym obiektyw odwzorowuje obraz obiektu. Rejestruje ona tę informację i przesyła dalej. Kamery klasyfikuje się ze względu na rodzaj przetwornika obrazu (CCD, CMOS) oraz dzieli na monochromatyczne i kolorowe, jak również na matrycowe oraz linijkowe.
Przedostatnie rejestrują sekwencję obrazów odwzorowujących poruszający się obiekt. Obraz w kamerze linijkowej jest tworzony krokowo, linia po linii. Dzięki temu wykorzystuje się je m.in. w pomiarach obiektów obracających się i materiałów w postaci arkuszy, jak: papier, szkło, blachy stalowe i materiały włókiennicze. Jeżeli z kolei chodzi o interfejsy komunikacyjne, w które wyposaża się kamery, to są to m.in.: IEEE 1392 (FireWire), USB oraz GigE Vision.
Systemy wizyjne generalnie można podzielić na kilka grup. Jedną z nich są te współpracujące z komputerem (PC-based). Kamera jest do niego podłączona bezpośrednio lub za pośrednictwem modułu akwizycji obrazu. Choć ich zaletą jest elastyczność w zakresie konfiguracji systemu i dostępność narzędzi programowych, zazwyczaj wymagają od programistów dużej wiedzy i najlepiej sprawdzają się w większych systemach.
Oddzielną kategorię stanowią kamery inteligentne. Ich podstawowymi elementami są: przetwornik obrazu, obiektyw, układ mikroprocesorowy i komunikacyjny, a czasem także oświetlacze i układy sterowania oświetleniem. Integrują one więc większość komponentów systemów wizyjnych, a zarazem są często prostsze w konfiguracji i obsłudze niż inne ich typy.
Kompletny system wizyjny w jednej obudowie zrealizowany z wykorzystaniem kamery inteligentnej to w wielu przypadkach lepsze rozwiązanie niż użycie kamery połączonej z oddzielnym komputerem, na przykład w ograniczonej przestrzeni albo warunkach sterylnych.
Dopełnieniem systemów wizyjnych jest oprogramowanie do przetwarzania i analizy obrazów. Implementuje się w nim różne algorytmy umożliwiające tworzenie różnych aplikacji kontrolno-pomiarowych. Przykładami są: algorytmy dopasowywania wzorca, detekcji krawędzi i optycznego rozpoznawania znaków (Optical Characeter Recognition, OCR). Dwa pierwsze przedstawiamy w ramce.
Rozwiązywanie problemów, cz. 3
Podobnie, jeżeli w międzyczasie wprowadzono zmiany w obrębie linii produkcyjnej, mogło dojść do niezamierzonej modyfikacji takich parametrów jak odległość robocza lub pole widzenia kamery, przez co obiekt na zdjęciach będzie mniejszy lub większy niż wcześniej. Mogło to też spowodować powstanie odblasków tam, gdzie ich wcześniej nie obserwowano. Jeżeli nie można przywrócić pierwotnych ustawień, w takim wypadku powinno się zastosować filtry albo polaryzatory. Czasami zmieniają się również zewnętrzne warunki w otoczeniu linii inspekcji. Przykładem jest sytuacja w pewnym zakładzie, w którym system wizyjny po uruchomieniu przez kilka miesięcy działał bez problemu. Po tym czasie jednak nagle zaczął wzrastać wskaźnik jego błędów, ale co ciekawe, miało to miejsce tylko popołudniami. Od razu domyślono się zatem, że źródłem tego problemu prawdopodobnie jest zmienność oświetlenia zewnętrznego. Jak wykazała dalsza analiza, wcześniej nie przysparzało ono takiego kłopotu, ponieważ system wizyjny został zaprojektowany i zainstalowany w porze letniej, kiedy ze względu na wyższe położenie słońca na niebie po południu jego promienie nie wpływały na oświetlenie w hali produkcyjnej. Kiedy jednak nadeszła zima i zmniejszyła się wysokość słońca na niebie, w rezultacie więcej promieni słonecznych zaczęło docierać do pomieszczeń zakładu. W tych, w których zainstalowano system wizyjny, okazało się szczególnie dokuczliwe. |
ORGANIZACJA SYSTEMU WIZYJNEGO
Organizując stanowiska z systemem wizyjnym, trzeba pamiętać o kilku ważnych kwestiach, dzięki którym będzie on działał prawidłowo. Na przykład pole widzenia kamery musi być na tyle duże, aby obejmowało cały obiekt albo tę jego część, której obraz powinien być rejestrowany.
Jednocześnie pole widzenia kamery nie może pokrywać zbyt dużego obszaru, bowiem wtedy obraz nie będzie miał wystarczająco dużej rozdzielczości. Jak pokazuje praktyka, rozdzielczość systemu wizyjnego, czyli odległość między dwoma szczegółami, które rozróżnia, powinna być co najmniej od pięciu do dziesięciu razy większa niż najmniejszy spodziewany defekt. Rozdzielczość systemu wizyjnego ma też wpływ na dokładność pomiarów przez niego wykonywanych.
Jakość zarejestrowanego obrazu jest kluczowa dla prawidłowego, zgodnego z oczekiwaniami, działania systemu wizyjnego. Aby wyniki na przykład kontroli jakości były spójne i wiarygodne, kontury obiektu powinny wyraźnie kontrastować z tłem. Ułatwia to ustalenie jego względnego położenia oraz wyznaczenie rozmiarów. Kluczem do uzyskania odpowiedniego kontrastu jest zapewnienie odpowiedniego oświetlenia.
Równie ważne jest to, żeby jasność i kontrast rozkładały się jednolicie na całym obrazie. Pozwala to na rozróżnienie na nim konturów obiektu. Równomierność rozkładu jasności i kontrastu zależą zarówno od oświetlenia, jak i ustawień obiektywu.
Kolejną ważną kwestią jest dostosowanie szybkości, z jaką przemieszczają się obiekty poddawane inspekcji do szybkości przetwarzania obrazów. Najlepiej, jeżeli jest ona tak dobrana, aby między zapisem kolejnych zdjęć był zachowany odpowiedni odstęp czasowy. Margines bezpieczeństwa będzie rekompensował opóźnienia powodowane przykładowo zmianami: szybkości przenośnika albo odległości między kolejnymi obiektami.
Jeżeli komponenty systemu wizyjnego będą wystawione na działanie takich czynników, jak: brud, substancje oleiste, wilgoć i pyły, dobrym rozwiązaniem jest umieszczenie kamery w osłonie. Łatwiej jest ją wyczyścić niż zabrudzony obiektyw. W przypadku, gdy podejmie się tego osoba niedoświadczona, może niechcący go zniszczyć albo zmienić jego ustawienia.
Trzeba również podjąć odpowiednie kroki, aby ochronić komponenty systemu wizyjnego przed gorącem, wibracjami i uderzeniami, na przykład przez zamocowanie kamery, oraz zaburzeniami elektromagnetycznymi. Dobrze, jeżeli kamery są zasilane z niezależnego stabilnego zasilacza, zaś kable komunikacyjne trzeba odizolować od kabli innych maszyn, które mogą emitować zaburzenia.
Czytniki kodów 2D nadzorują montaż
W pierwszym kroku element bazowy miał być znakowany kodem 2D, poddawanym weryfikacji na następnym stanowisku, na którym pracował robot spawalniczy. Jeśli sprawdzenie dało pozytywny wynik, do elementu przymocowywano inne. Kolejnym etapem była wizyjna kontrola jakości spawów. Informacja o tych, które wymagały poprawki, była przesyłana na kolejne stanowisko. Niewłaściwie zespawane elementy były na nim rozpoznawane na podstawie kodu 2D i dokonywano niezbędnych poprawek. Następnie zespawane części trafiały na stanowisko malowania. Z tym krokiem wiązało się jedno z większych wyzwań w realizacji tego systemu. Obawiano się bowiem, że jeżeli oznaczenia będą zbyt płytko wykonane, pokrycie ich powłoką farby pogorszy kontrast między symbolami a tłem. Utrudniłoby to ich rozpoznawanie. Aby tego problemu uniknąć, zdecydowano się na znakowanie metodą mikroudarową (dot peen). Do nanoszenia symboli używane się w niej igły z diamentową albo karbidową końcówką. Uderzając w detal, wybija ona na jego powierzchni mikrootworki rozmieszczone gęsto obok siebie. Łącząc się ze sobą, tworzą one linie symboli. Napis jest widoczny dzięki różnicy w sposobie odbijania światła przez otworki i gładkie tło. Do rozpoznawania oznaczeń zdecydowano się wykorzystać czytniki kodów kreskowych. Podczas testów przeprowadzonych w zakładzie ustalono optymalne odległości, które powinna dzielić czytnik i obiekt w zależności od rozmiarów jego oznaczeń oraz tego, czy został już pokryty powłoką malarską, czy nie i odpowiedni kąt odczytu. |
JAK EFEKTYWNIE TESTOWAĆ SYSTEM WIZYJNY?
Na etapie organizacji systemu wizyjnego, przed oddaniem go do użytku, poddaje się go testom. Podczas takiego sprawdzenia ważne jest, aby przetestować go na przykładowych obiektach różnego typu, tzn. w przypadku systemu kontroli jakości, zarówno na tych, które powinny być rozpoznane jako pełnowartościowe, jak i tych wybrakowanych.
Próbki powinny być jak najbardziej podobne do obiektów, które będą poddawane inspekcji. Nawet ich cechy, które mogą się wydawać nieistotne ze względu na to, że zadaniem systemu wizyjnego będzie analiza innych ich właściwości, mogą mieć znaczenie. Na przykład, choć system wizyjny będzie miał za zadanie wykrywać śruby zbyt krótkie lub źle nagwintowane, inaczej może się wywiązywać z tego zadania w przypadku elementów, które wykonano ze stali, a inaczej w przypadku tych z mosiądzu, nawet jeżeli będą miały taki sam kształt. Wynika to stąd, że oba metale w nieco inny sposób odbijają światło.
Systemy wizyjne testuje się, wykonując setki próbnych badań na danym zestawie obiektów, aby uzyskać pewność, że wyniki jego inspekcji są statystycznie spójne i wiarygodne. Pozwala to też dostosować do potrzeb tolerancję, z jaką wykrywa braki. Celem jest uzyskanie równowagi między liczbą błędów, czyli liczbą pełnowartościowych egzemplarzy uznanych błędnie za uszkodzone, a liczbą tych wybrakowanych, dla których wynik inspekcji był pozytywny.
Na etapie testów wykrywa się również różne błędy spowodowane niewłaściwą instalacją komponentów systemu wizyjnego. Przykładem są cienie rzucane przez osłony i odbicia od urządzeń i elementów konstrukcyjnych w otoczeniu, w którym wpływają na jakość rejestrowanych obrazów.
Rozwiązywanie problemów, cz. 4Jeżeli w trakcie działania system wizyjny przestaje dostarczać wiarygodnych wyników może się okazać, że przyjęto nadmiernie zaniżone założenia projektowe. Prawidłowo zaprojektowany oraz zainstalowany system kontroli wizyjnej maszyny powinien bowiem (z wyjątkiem sytuacji, kiedy zmodyfikowano linię produkcyjną, zmieniły się warunki otoczenia albo wymagania w zakresie inspekcji), działać długo i bezawaryjnie. |
SYSTEMY WIZYJNE - ROZWIĄZYWANIE PROBLEMÓW
Właściwie zaprojektowany i zainstalowany system wizyjny powinien działać prawidłowo. Jeżeli po jakimś czasie od uruchomienia przestaje wykrywać defekty i sygnalizuje je dla pełnowartościowych wyrobów, traci na wiarygodności. By ograniczyć straty przez to powodowane, trzeba szybko odkryć powód problemu i go usunąć. Bywa to proste, jeżeli przyczyna jest oczywista, ale zdarza się też, że trudno ją odkryć.
Generalnie przyczyny, dla których system wizyjny nie działa zgodnie z oczekiwaniami, można podzielić na trzy kategorie ze względu na ich charakter. Są to problemy natury: mechanicznej, elektrycznej lub optycznej. Warto od razu zaznaczyć, że lepiej powstrzymać się od wprowadzania zmian w ustawieniach oprogramowania, dopóki nie wykluczymy, że powód dysfunkcji nie należy do żadnej z tych grup. Ważną wskazówką co do rodzaju awarii jest to, czy pogorszenie działania systemu wizyjnego nastąpiło nagle, czy pogłębiało się stopniowo.
Postępujące pogarszanie się jakości i ostrości obrazu może zasygnalizować oprogramowanie systemu wizyjnego. W takim przypadku z dużym prawdopodobieństwem źródłem problemu jest zmniejszanie się ilości światła, które dociera do kamery.
Możliwe tego przyczyny to m.in. gromadzenie się zanieczyszczeń na soczewkach albo starzenie się źródła światła. To ostatnie wraz z upowszechnianiem się lamp LED występuje coraz rzadziej.
Częściej jednak zauważalne jest nagłe pogorszenie się. Wtedy w pierwszej kolejności trzeba przeanalizować co się zmieniło od czasu, gdy system wizyjny działał poprawnie. Przyczyna raptownej zmiany ma zwykle charakter mechaniczny. Przykładowo na skutek wibracji albo uderzenia przesunięciu mógł ulec któryś z komponentów systemu, przeważnie kamera albo oświetlenie. Łatwo to naprawić i zapobiec powtarzaniu się tego problemu w przyszłości przez mocniejsze zamocowanie obluzowanego elementu.
|
PROBLEMY ELEKTRYCZNE I KOMUNIKACYJNE
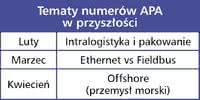
Tematy numerów APA w przyszłości
Nagłe pogorszenie się działania systemu wizyjnego może być także spowodowane problemem natury elektrycznej. Najprościej jest zdiagnozować rozłączenie się kabli, gdyż najważniejsze komponenty systemu wizyjnego, jak kamera czy oświetlacze, wyposażone są we wskaźniki świetlne, które sygnalizują problem z zasilaniem. Do tej grupy zalicza się także problemy z komunikacją między komponentami systemu.
W takim przypadku najlepiej sprawdzić wszystkie połączenia, a przynajmniej te, które gdy zostaną przerwane, to dana funkcja systemu nie będzie działać. Na przykład jeśli zdjęcia wyrobów w ogóle nie są wykonywane, to prawdopodobnie do kamery nie dociera sygnał wyzwalający, na przykład z powodu przerwania jej połączenia z czujnikiem, który wykrywa obecność obiektu inspekcji na stanowisku kontroli wizyjnej.
Jeżeli z kolei mimo informacji z systemu wizyjnego o wykryciu wybrakowanego wyrobu zostaje on przetransportowany na kolejne stanowisko, prawdopodobnie nie zadziałał mechanizm odrzucania takich produktów. Może to oznaczać przerwanie połączenia pomiędzy jego sterownikiem, a na przykład komputerem, na którym zainstalowano oprogramowanie do przetwarzania obrazu.
W ramkach przedstawiamy więcej informacji na temat rozwiązywania problemów w działaniu systemów wizyjnych.
Monika Jaworowska