Część 3: Komponenty heavy duty
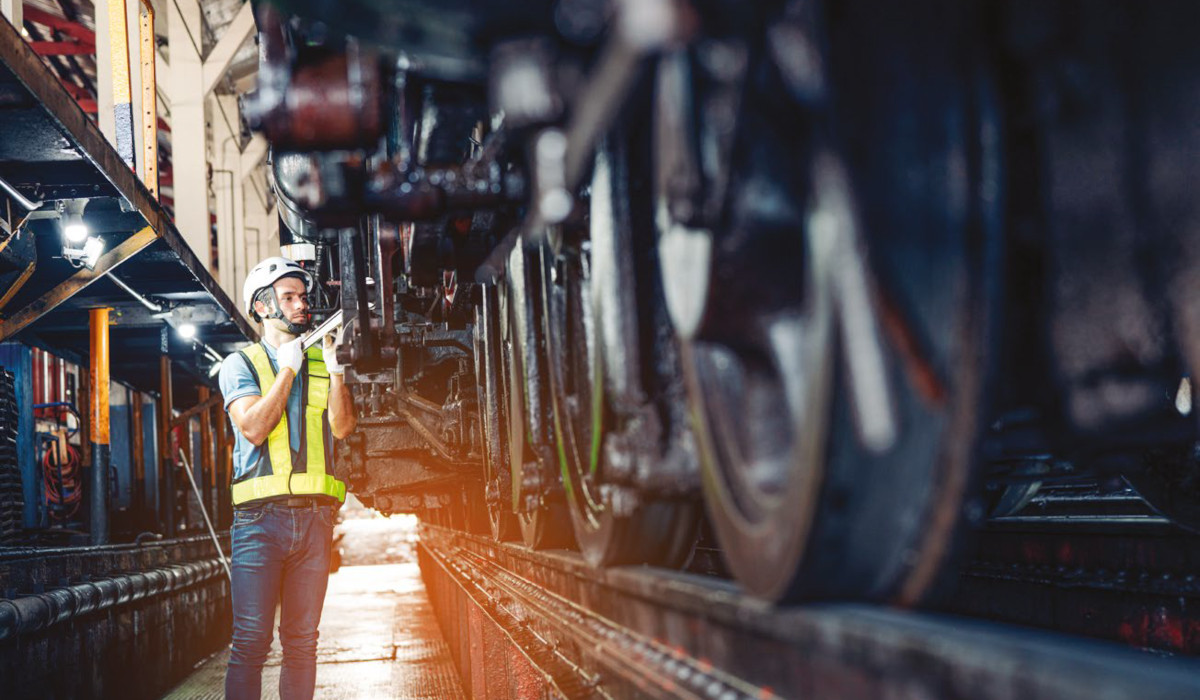
Wyposażenie pociągów i infrastruktury kolejowej musi spełniać specjalne wymagania w zakresie wytrzymałości fizycznej oraz projektu nakierowanego na eliminowanie błędów ludzkich, co jest gwarancją niezawodnej oraz bezpiecznej pracy taboru. Dotyczy to m.in. komponentów układów zasilania i paneli operatorskich – wytyczne dla tych grup produktów przedstawiamy w ramkach. Elementem krytycznym systemów sterowania pociągami są również złącza, które doprowadzają zasilanie oraz zapewniają łączność w urządzeniach przytorowych i pokładowych. Wymagania im stawiane różnią się w zależności od miejsca ich montażu.
Generalnie można podzielić je na dwie grupy. Do pierwszej zaliczane są złącza, z których korzysta się na zewnątrz pojazdów szynowych, tzn. montowane na przykład między wagonami, pod nimi lub na dachu i przytorowo. Wymaga się od nich przede wszystkim wysokiej odporności na uciążliwe warunki pracy. Wśród najbardziej niekorzystnych czynników, na które są narażone, wymienia się: silne wibracje, uderzenia na przykład drobin piasku i kamieni, opady atmosferyczne (deszcz, śnieg), oblodzenie oraz nasłonecznienie, a zatem skrajnie niskie oraz ekstremalnie wysokie temperatury.
Jeżeli natomiast chodzi o złącza oraz przewody, które są montowane wewnątrz lokomotywy oraz w wagonach, w tym w przedziałach pasażerskich, wymaga się m.in., by były wykonane z materiałów niepalnych, nierozprzestrzeniających ognia oraz niewydzielających w czasie spalania szkodliwych substancji. Podwyższa to poziom bezpieczeństwa, ogień oraz dym w zamkniętych pomieszczeniach stanowią bowiem śmiertelne zagrożenie dla osób w nich przebywających. Ponadto, ze względu na ograniczenia przestrzenne wewnątrz pociągów, instaluje się tam głównie złącza o jak najmniejszych rozmiarach, jak najlżejsze i o jak największej gęstości upakowania przewodów. Ważna jest również łatwość odłączania i podłączania złączy, najlepiej bez używania narzędzi. Na przykład w kabinie maszynisty wszelkie opóźnienia w tym zakresie mogą mieć bardzo poważne skutki.
Materiały obudów
Przed destrukcyjnym wpływem czynników zewnętrznych złącza chronią obudowy. Kluczowy jest materiał, z którego są wykonane. Obudowy metalowe sprawdzają się w przypadku narażenia złączy na duże siły ciągnące i ekstremalne temperatury. Popularnym materiałem jest aluminium. Obudowy z niego są zwykle wykonywane w formie odlewów ciśnieniowych. Popularność aluminium wynika z jego właściwości. Jest to materiał o gęstości i sztywności równej jednej trzeciej tych parametrów stali, plastyczny i łatwy w obróbce. Czyste aluminium charakteryzuje duża odporność na korozję. Wynika to stąd, że jego powierzchnia samoczynnie pokrywa się bardzo cienką, o grubości zaledwie kilku nanometrów, lecz równocześnie szczelną, ściśle przylegającą do podłoża, warstwą ochronną tlenku. Powłoka ta przeciwdziała postępowi utleniania, a w przypadku uszkodzenia następuje jej szybka odbudowa.
W agresywniejszych środowiskach nie stanowi ona jednak wystarczającego zabezpieczenia przed rozwojem korozji. Dlatego obudowy aluminiowe poddaje się dodatkowej obróbce. Przykładem jest anodowanie. Ta metoda obróbki polega na wytworzeniu powłoki tlenkowej w procesie elektrolizy. Anodą jest w tym przypadku powierzchnia aluminiowa, natomiast katodę stanowi metal, który jest odporny na działanie elektrolitu. Na właściwości powstałej powłoki wpływa skład elektrolitu – na przykład porowate antykorozyjne warstwy tlenku glinu tworzą się w roztworach kwasu siarkowego, chromowego albo szczawiowego.
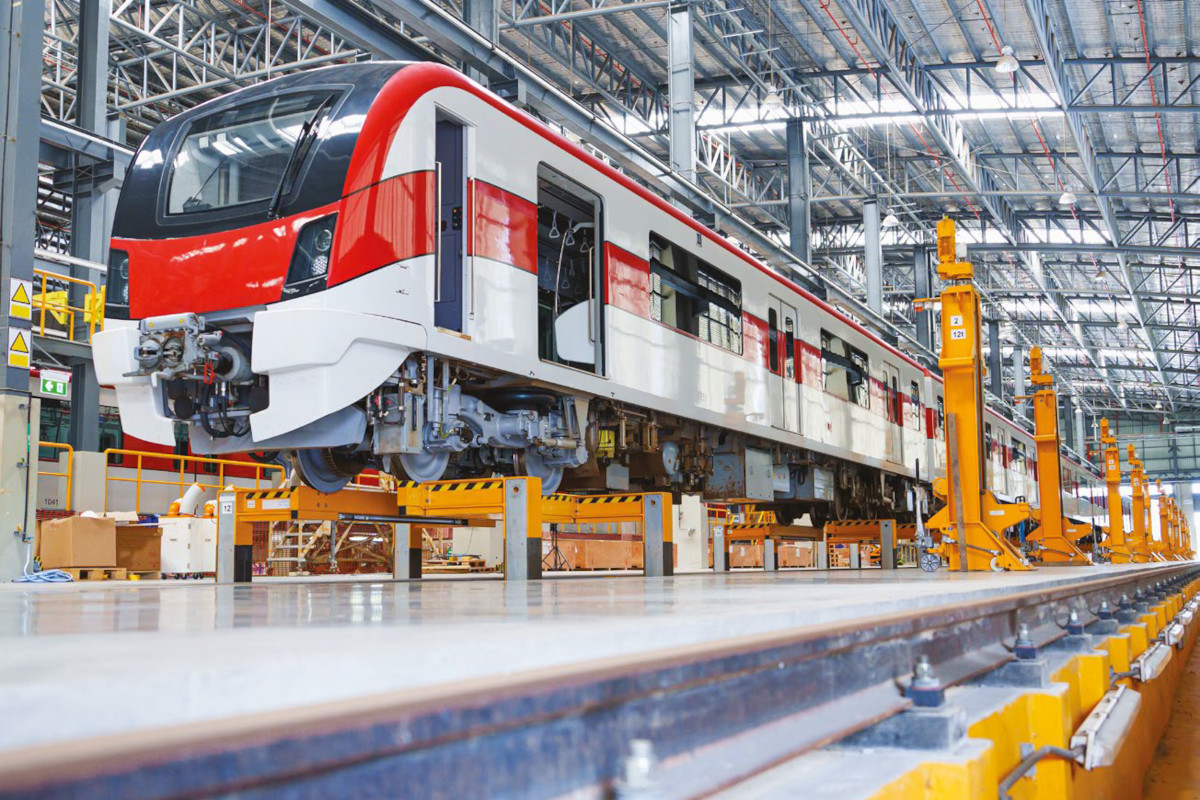
Malowanie proszkowe i powlekanie
Alternatywa dla anodowania to malowanie proszkowe, czyli aplikacja sproszkowanej farby metodą natrysku elektrostatycznego. W tym celu uziemiona powierzchnia jest spryskiwana przy użyciu specjalnego pistoletu naelektryzowanymi w nim cząstkami farby, które dzięki temu się na niej osadzają. Następnie malowany przedmiot jest umieszczany w piecu nagrzewanym do wysokiej temperatury, rzędu kilkuset °C. W nim proszek ulega stopieniu, polimeryzuje się oraz utwardza, tworząc powłokę malarską. Ważną zaletą tej techniki jest możliwość ponownego użycia proszku, który nie osiadł na malowanym przedmiocie. Nie są również potrzebne rozpuszczalniki. Powłoka powstała w ten sposób jest odporna na korozję, chemikalia, wysoką temperaturę (około +100°C) i uszkodzenia mechaniczne, wilgoć i promieniowanie UV.
Aluminium jest także pokrywane powłokami, na przykład kadmową, niklową, niklowo-teflonową, cynkowo-niklową albo cynkowo-kobaltową. Trzy ostatnie charakteryzuje większa odporność na zarysowania w porównaniu do kadmu. Obudowy aluminiowe pokrywa się oprócz tego powłokami tytanowymi. Przykładowym rozwiązaniem jest powlekanie osłon tlenkiem tytanu metodą natrysku plazmowego, która polega na stopieniu materiału powłoki w plazmie łuku elektrycznego w atmosferze gazu obojętnego. Technikę tę wyróżnia wszechstronność pod względem materiałów powłok i podłoży. Powłoki z tytanu natryskiwane plazmowo charakteryzuje duża wytrzymałość na oddziaływania mechaniczne, na przykład na uderzenia kamieniami.
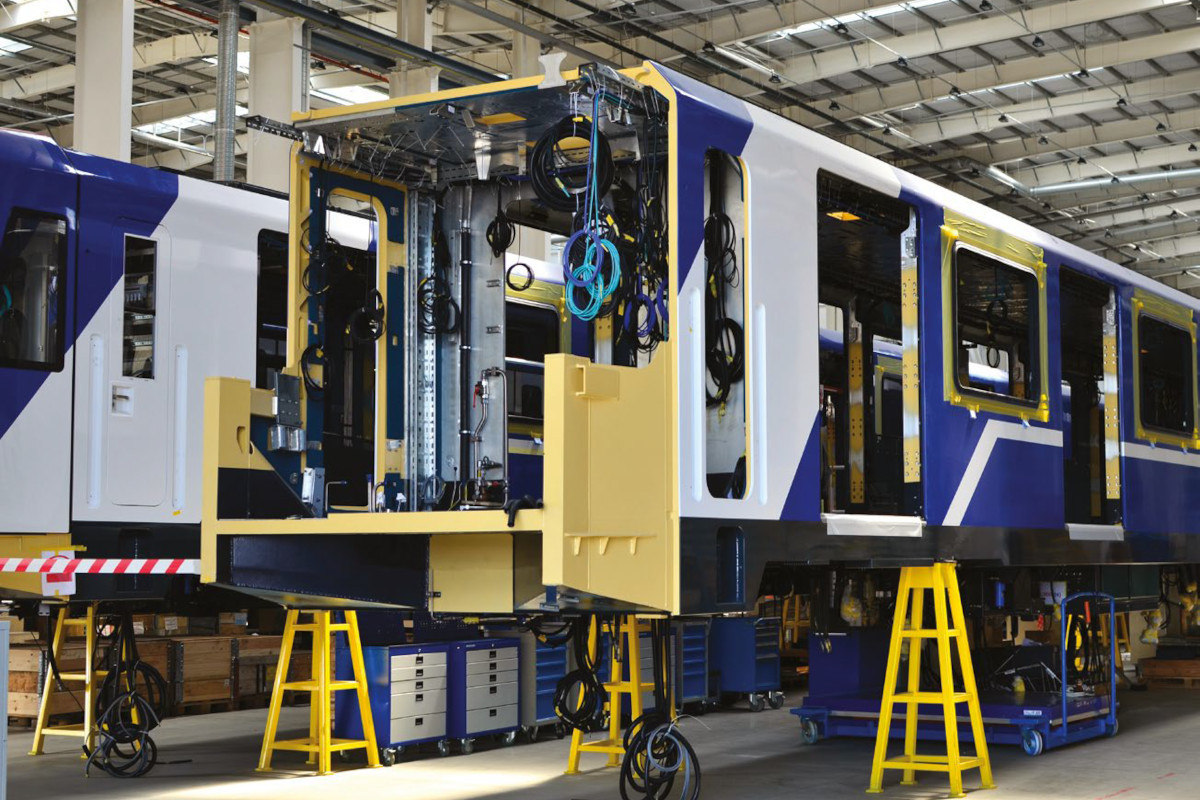
Ochrona przed wibracjami, wodą i pyłem
Jeżeli chodzi o ochronę złączy przed drganiami, dostępnych jest kilka mechanizmów blokujących, w zależności od wymagań. Standardowy pojedynczy system blokujący ma dźwignię (rygiel) z przodu albo z boku obudowy. Ruch dźwigni powoduje zamknięcie obudowy i osłony. Podwójne systemy blokowania mają dwie dźwignie.
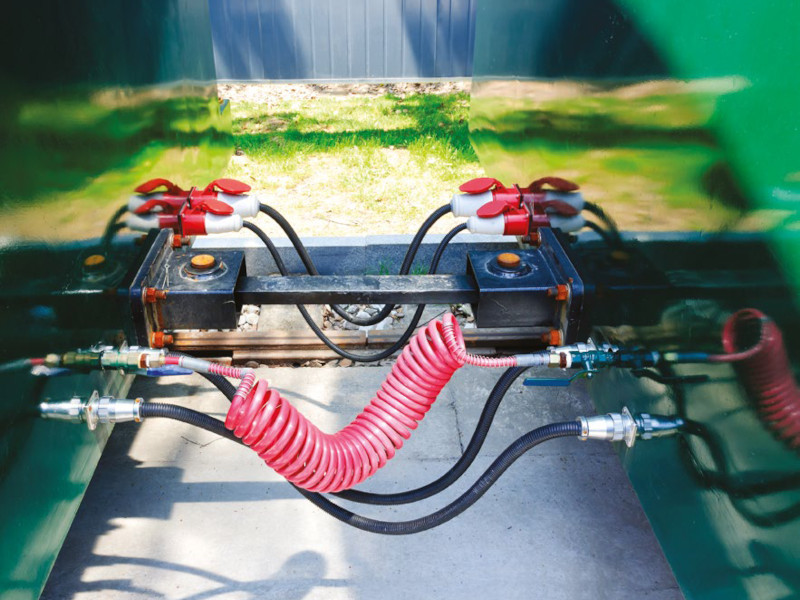
Wodoodporność i pyłoszczelność zapewniają uszczelnienia z tworzyw sztucznych. Ich skuteczność charakteryzuje dwucyfrowy stopień ochrony IP. Pierwsza cyfra w jego zapisie, z przedziału 0–6, opisuje pyłoszczelność, zaś druga, z zakresu 0–9, charakteryzuje wodoszczelność przy różnym nasileniu oddziaływania wody, od opadów pojedynczych kropel, przez polewanie strugą, aż po zanurzenie. Przykładowo stopień ochrony IP67 w porównaniu z IP68 oznacza, że chociaż oba złącza są pyłoszczelne, pierwsze jest odporne na krótkotrwałe zanurzenie w wodzie, a drugie pozostanie szczelnie nawet przy ciągłym zanurzeniu.
Kompatybilność elektromagnetyczna złączy zależy od właściwości ekranujących obudowy wtyczki, obudowy gniazda i dławnicy kablowej. Wpływ na właściwości ekranujące mają przede wszystkim: przewodność elektryczna materiału i grubość ekranu. Ważna jest także ciągłość połączeń pomiędzy wymienionymi elementami złączy. Dlatego by zwiększyć powierzchnię kontaktową na styku gniazda z wtykiem, m.in. wykonuje się je w taki sposób, żeby nachodziły na siebie. Korzysta się również z przewodzących uszczelnień. By ekranowanie było skuteczne, trzeba się upewnić, że wszystkie komponenty złącza zapewniają zbliżony poziom tłumienia zaburzeń elektromagnetycznych.
Monika Jaworowska