Korozja
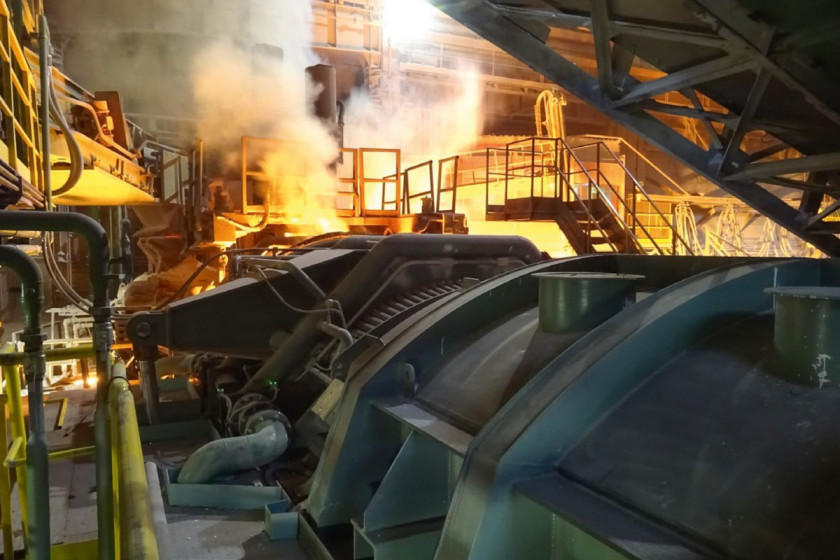
Niekorzystny jest też kontakt wody z zewnętrznymi powierzchniami obudów, powodujący korozję, czyli postępujące niszczenie materiałów, zwłaszcza metali, w następstwie ich reakcji z otoczeniem. Rozwija się w obecności cieczy albo gazów, na ogół szybciej w wyższej temperaturze. Jej postępowi sprzyja obecność zanieczyszczeń.
Wyróżnia się kilka typów korozji. Pojawia się równomiernie lub miejscowo (wżerowa, szczelinowa). Galwaniczna występuje, jeżeli różne metale stykają się w obecności elektrolitu. Mikrokrystaliczna rozwija się na granicach ziaren metalu w wyniku niewłaściwej obróbki cieplnej, na przykład spawania, a wysokotemperaturowa na skutek reakcji z otoczeniem w podwyższonej temperaturze. Najpowszechniejsza jest korozja atmosferyczna. Przykład to rdza na żelazie. Może mieć charakter chemiczny albo elektrochemiczny.
Korozja to problem w branży morskiej, na statkach i farmach wiatrowych. Elementy ich konstrukcji i wyposażenia mają kontakt z wilgotnym i zasolonym powietrzem, na co narażona jest część statku niezanurzona w morzu i jego wnętrze (maszynownia, ładownia, kabiny), a w przypadku elektrowni – turbina, i ze słoną wodą morską. Z tą stykają się podwodna część kadłuba statków i wieże wiatraków. Korodują też części maszyn budowlanych, do prac leśnych, sprzętu górniczego. Choć korozji nie można całkiem wyeliminować, można ją ograniczyć. Jeśli mimo wszystko się rozwija, oznacza to, że zastosowane środki nie są wystarczające lub dany sprzęt nie nadaje się do użytku w tych konkretnych warunkach.
Projektowanie obudów wodoszczelnychKluczowe znaczenie ma materiał obudowy. Wybierać można z metali i tworzyw sztucznych. Poza ich ogólnymi właściwościami warto zwrócić uwagę na kwestie nieoczywiste. Na przykład wybierając mieszankę poliwęglanu PC z ABS łączącą zalety obu materiałów (łatwość obróbki ABS, dobre właściwości mechaniczne i termiczne poliwęglanu), trzeba pamiętać, że pod wpływem olejów i rozpuszczalników ulega uszkodzeniu. Dlatego śruby używane do łączenia części obudów z PC/ABS nie mogą być pokryte smarami, które z czasem wnikałyby do tego tworzywa, osłabiając konstrukcję. Ważny jest kształt obudowy. Unikać należy ostrych narożników. Trudno je uszczelnić i są podatne na uszkodzenia. Alternatywą są narożniki zaokrąglone. W ich przypadku łatwiej zapewnić ciągłość uszczelnienia i są trwalsze. Uszczelnienie zapewniają uniwersalne uszczelki oring. Wymagają one precyzyjnego montażu – w razie niedopasowania części obudowy, mimo obecności uszczelki woda wniknie do środka. Dlatego nie sprawdzają się przy wyższych stopniach ochrony IP. Alternatywą są uszczelki niestandardowe wykonywane na wymiar. Prawdopodobieństwo ich niewłaściwego założenia jest mniejsze, ale by były dopasowane, muszą być zwykle grubsze niż standardowe. To wpływa na estetykę obudowy. Najlepsze rozwiązanie to uszczelki wylewane formowane bezpośrednio na obudowie. Integracja uszczelnienia przyspiesza montaż, a na szczelność nie wpływają zdolności manualne osób, które składają obudowę. Ważny jest docisk uszczelki, bo nie tylko zapobiega wnikaniu wody do środka, ale i pozwala uniknąć konsekwencji zmian ciśnienia w obudowie na skutek wahań temperatury. Gdy bowiem osłona się nagrzewa ciśnienie wewnątrz niej rośnie przez co powietrze nieszczelnościami wypływa na zewnątrz. Gdy z kolei zaczyna się ochładzać, odwrócony gradient ciśnienia powoduje zasysanie powietrza z otoczenia. By do tego nie dopuścić należy zapobiec wybrzuszaniu się obudowy przez gęstsze rozmieszczenie śrub montażowych. |
Jak zapobiegać korozji?
Kluczowy jest dobór materiałów. Odporna na korozję jest stal nierdzewna, dzięki zawartości chromu (min. 10%), który tworzy na powierzchni samonaprawiającą się warstwę tlenku. Występuje w różnych odmianach.
Stal nierdzewną 316 wyróżnia wyjątkowa odporność na korozję ze względu na większą zawartość niklu i dodatek molibdenu. Dzięki temu jest to popularny materiał obudów urządzeń elektrycznych do pracy w środowisku morskim. Ten typ stali sprawdza się szczególnie w ich korpusach, natomiast nie jest polecany jako materiał wykonania elementów, takich jak nakrętki, śruby, złącza. W zamian lepiej jest wykorzystać stal nierdzewną 304, o większej wytrzymałości i odporności na zużycie (częściowo dzięki nieco większej zawartości chromu) i tańszą.
Kolejne materiały to stopy miedzi. Wyróżnia je dobre przewodnictwo cieplne i elektryczne, dobre właściwości mechaniczne, łatwość obróbki. Choć reagują z niektórymi kwasami, generalnie w powietrzu, wodzie, słonej wodzie, w obecności wielu organicznych i nieorganicznych chemikaliów charakteryzuje je duża odporność na korozję. Nikiel i jego stopy są z kolei odporne na roztwory żrące. Inny przykład to aluminium i jego stopy, m.in. 5052, który poza odpornością na korozję wyróżnia wytrzymałość zmęczeniowa i łatwość spawania.
Ważna kwestia to kompatybilność metali. Trzeba unikać zestawień, w których może wystąpić korozja galwaniczna, na przykład połączenia miedzi i stali nierdzewnej. Metale zabezpiecza się też powłokami ochronnymi wytwarzanymi m.in. w procesie cynkowania i miedziowania. Przed korozją zabezpiecza ponadto malowanie proszkowe i powłoki ceramiczne.
Korozja zbiorników na wodę w pojazdach strażackichCase study ![]() Na wykonanych ze stali nierdzewnej typu 1,4301 zbiornikach na wodę (surową, nieoczyszczoną) w pojazdach strażackich wykryto korozję powodującą wycieki. Uszkodzeniu uległy głównie spawy. Wykryto tam miejscowe wżery. Spawy miały prawidłową strukturę i zostały dokładnie oczyszczone po spawaniu (przebarwienia cieplne usunięto chemicznie). Badania próbek wody wykazały, że jej parametry chemiczne są akceptowalne przy odporności korozyjnej użytej stali. Natomiast badania mikrobiologiczne osadów ze stali i wody wykazały obecność tlenowych bakterii heterotroficznych w procesie metabolizmu wytwarzających kwas organiczny. Obecne były także bakterie utleniające żelazo i mangan. Wszystkie te mikroorganizmy, poprzez różne mechanizmy, powodowały korozję. Sprzyjało temu też to, że woda w zbiornikach stała. To ułatwiało nagromadzanie się bakterii w spawach i innych szczelinach. By w przyszłości uniknąć takich problemów, należy używać wody uzdatnionej lub stosować środki dezynfekujące odpowiednie dla stali, z której wykonano zbiorniki. |
Korozja szczelinowa płytowych wymienników ciepłaCase study ![]() Po kilku miesiącach użytkowania na płytowych wymiennikach ciepła wykonanych z austenitycznej stali nierdzewnej typu 1,4404 zainstalowanych w hydroelektrowni wykryto perforację wywołaną korozją. Na skutek ich uszkodzenia okresowo dochodziło do przekraczania przez temperaturę oleju smarowego generatorów wartości dopuszczalnej, co skutkowało przestojami w produkcji energii. W instalacji używano surowej wody o małym stężeniu chlorków. Gdy jednak była nieczynna, ze względu na konstrukcję wlotów wody i fakt, że była zlokalizowana na rzece w pobliżu wybrzeża morskiego, silnie zasolona woda morska wpływała do systemu. Skutkiem były miejscowe uszkodzenia korozyjne, zwłaszcza w szczelinach między płytami. Ponieważ wykorzystywany typ stali nierdzewnej okazał się nieodporny na kontakt z wodą o tak dużej zawartości chlorów, konieczna okazała się wymiana używanych wymienników na takie z płytami tytanowymi. |
Korozja szczelinowa wymiennika ciepła na statkuCase study Nowe wymienniki ciepła, które zamontowano w maszynowni statku, wykonano z stali nierdzewnej austenitycznej typu 1,4404. Po kilku tygodniach, podczas których były wystawione na działanie atmosfery morskiej, na rurach odkryto ślady korozji. Uszkodzenia zlokalizowane były w obszarze styku rur – wzdłużna spoina była prawie całkowicie skorodowana. Charakter uszkodzeń wskazywał na nieodpowiednie rozwiązanie konstrukcyjne, w taki sposób wykonanym złączu występowała bowiem szczelina, w której łatwo gromadziły się ciała obce i osadzały się chemicznie agresywne produkty kondensacji morskiego powietrza. Jednocześnie obszar szczeliny był zubożony w tlen, co zmniejszało zdolność warstwy pasywnej do regeneracji (repasywacji), która zapewnia odporność na korozję. Konieczna zatem okazała się wymiana wymienników na inny model. |
Korozja wżerowa w instalacji odsalaniaCase study ![]() Po kilku miesiącach eksploatacji na elementach instalacji odsalania wody wykonanych ze stali nierdzewnej w rejonie złączy spawanych wykryto korozję powodującą nieszczelność. Badanie składu chemicznego metodą fluorescencyjnej spektrometrii rentgenowskiej wykazało, że rury wykonano z dwóch rodzajów austenitycznych stali nierdzewnych – odcinek z pierścieniem uszczelniającym ze stali typu 1,4372, a pozostałą część ze stali 1,4404. Wżery korozyjne pojawiły się na złączach spawanych na obu materiałach, ale badania rentgenowskie i makroskopowe wykazały, że części wykonane z pierwszego typu stali uległy większym uszkodzeniom. Jest to konsekwencją niższej zawartości pierwiastków stopowych i braku Mo w porównaniu ze stalą typu 1,4404. Oba materiały mają jednak niewystarczającą odporność na wodę o zawartości chlorków, jak w tej instalacji (zasolenie do 3500 mg/l). Ponadto rozwój korozji w obszarze złącza przyspieszyło to, że przebarwienia powstałe w wyniku ogrzania podczas spawania nie zostały dokładnie usunięte. By uniknąć uszkodzeń, należało wykonać instalację z rur ze stali nierdzewnej superaustenitycznej albo duplex, przykładając większą wagę do jakości wykończenia zespawanych powierzchni albo wykorzystać rury z tworzywa sztucznego. Na te ostatnie ostatecznie wymieniono te skorodowane. |
Przeciekająca obudowaCase study Użytkownicy nowo wprowadzonych na rynek przenośnych urządzeń pomiarowych zaczęli masowo zgłaszać ich producentowi, że mimo deklarowanej wodoodporności (IPX7), przeciekają. Przeprowadzone podciśnieniowe testy szczelności potwierdziły usterkę, więc obudowę postanowiono przeprojektować. ![]() Rozpoczęto od analizy wykonania uszczelki między przednią i tylną częścią obudowy. W istniejącej konstrukcji została wykorzystana uszczelka o przekroju okrągłym o średnicy 1,2 mm. Umieszczono ją w rowku o głębokości 0,9 mm. Oznaczało to, że będzie ściskana osiowo o 0,3 mm. Z kolei szerokość rowka wynosiła 1,4 mm. Pozostawało zatem jedynie 0,1 mm luzu promieniowego po każdej stronie uszczelki. Przy takich wymiarach współczynnik wypełnienia rowka uszczelką wynosił 90%. Jeżeli jednak uwzględnić tolerancję wykonania, na przykład na poziomie ±0.05mm, współczynnik wypełnienia wzrastał do 115%. Uszczelka o 15% większa niż rowek uniemożliwiała domknięcie obudowy. W efekcie warunek szczelności IPX7 był niemożliwy do spełnienia. Współczynnik wypełnienia należało więc zmniejszyć, zmniejszając średnicę uszczelki lub zwiększając głębokość bądź szerokość rowka. Ze względu na ograniczone możliwości ingerencji w rozmiary urządzenia rowka nie można było wystarczająco poszerzyć. Z kolei zmniejszenie średnicy uszczelki lub zwiększenie głębokości rowka przy mniejszych tolerancjach wykonania też skutkowałoby rozszczelnieniem. Oczywiste stało się, że należało zrezygnować z okrągłej uszczelki na rzecz konstrukcji zapewniającej większy margines w kierunku osiowym bez zajmowania większej ilości miejsca promieniowo. Rozwiązaniem okazała się uszczelka w kształcie jak na rys. 1, o szerokości 1,5 mm, a zatem trochę szersza niż ta wcześniejsza i zarazem prawie 4-krotnie wyższa (4,35 mm). Dzięki kątowi styku 50º między uszczelką a tylną obudową ściskanie jest zapewniane częściowo przez zaciśnięcie śrub obudowy (osiowo), a częściowo przez sztywność zmontowanych części obudowy (promieniowo). W celu przetestowania projektu wykonany został model obudowy i uszczelki na drukarce 3D. Przeszedł on pomyślnie podciśnieniowe testy szczelności. To zdecydowało o przekazaniu projektu obudowy do realizacji. Także gotowe urządzenia spełniły wymóg stopnia ochrony IPX7. |