- Podczas niedawnych targów Automation Fair 2015 wiele uwagi poświęcono tematyce zintegrowanego przedsiębiorstwa, Internetowi Rzeczy oraz Przemysłowi 4.0. Zagadnienia te, szczególnie Industry 4.0, są tradycyjnie kojarzone z firmami niemieckimi. Jaka jest w tym zakresie oferta firmy Rockwell Automation i czym możecie wyróżnić się spośród innych dostawców branżowych?
Keith Nosbusch: W porównaniu do dużych konkurentów rynkowych, Rockwell Automation jest jedyną firmą, która jest w pełni skupiona na automatyce przemysłowej. Obejmujemy wszystkie jej dziedziny jedną, zintegrowaną platformą sterowania i kontroli, bazujemy na wspólnej sieci komunikacyjnej opartej na standardowym, niemodyfikowanym Ethernecie oraz wspólnym środowisku programistycznym.
Dostarczamy również wiele "inteligentnych" produktów - np. napędów czy sterowników z funkcjami analizy danych, a także mamy ekspertyzę w szeregu kluczowych obszarów branżowych. Wszystkie te cechy sprawiają, że możemy wyróżniać się na rynkach - nawet tych najbardziej konkurencyjnych, jak przykładowo niemieckim.
Współpracujemy również z licznymi partnerami z branży IT oraz infrastrukturalnej, co daje nam możliwość oferowania produktów zapewniających naszym klientom bezpieczeństwo inwestycji w automatykę oraz jej kompatybilność z dzisiejszymi oraz przyszłymi rozwiązaniami technicznymi.
Thomas Donato: Wysiłki podejmowane w celu stworzenia produkcji bardziej wydajną, a maszyn bardziej inteligentnymi podejmowane są dzisiaj na całym świecie. Zależnie od regionu mają one inne nazwy - może być to Przemysł 4.0, Industrial Internet of Things, Made in China 2025, Usine du Futur czy, w przypadku Stanów Zjednoczonych, SMLC.
Właściwie w każdym z krajów rozwiniętych mamy dzisiaj do czynienia z jedną lub kilkoma tego typu inicjatywami, przy czym Industrie 4.0 jest chyba najbardziej znane. Spopularyzowało się ono jako pierwsze, dodatkowo powstało w Niemczech, które są największym na świecie producentem maszyn.
Wszystkie inicjatywy mają część wspólną - ich celem jest stworzenie produkcji bardziej efektywnej oraz pozwalającej na indywidualizację produktów przy zachowaniu niskich kosztów. Wymaga to wymiany informacji pomiędzy maszynami oraz systemami zarządzania produkcją, ale też zmian w zakresie stosowanych standardów i kultury organizacyjnej. Wielu naszych klientów to firmy produkcyjne działające globalnie - my również tak działamy i możemy w każdym zakątku świata zapewniać naszym odbiorcom wsparcie inżynieryjne i biznesowe.
Bardzo podobnie jest w przypadku producentów maszyn, których grupa jest szczególnie istotna w przypadku rynku europejskiego. Firmy te szukają możliwości technologicznych i skalowanych rozwiązań, oczekują też od dostawcy ekspertyzy i sprawnie działającego łańcucha dostaw. Co roku prezentujemy coraz bardziej inteligentne produkty, rozbudowujemy też cały ekosystem rozwiązań, co moim zdaniem pozwala na tworzenie wydajnych maszyn, które dodatkowo można łatwo integrować z systemami IT przedsiębiorstw.
- Trend łączenia ze sobą urządzeń i instalacji produkcyjnych nie jest nowy - jak dużo systemów przemysłowych jest dzisiaj podłączonych do sieci i wymienia ze sobą dane?
KN: Wbrew pozorom jest ich ciągle bardzo niewiele. Nasze najnowsze badania wskazują, że jedynie 14% wszystkich maszyn produkcyjnych jest podłączonych do sieci firmowych i wymienia w sposób ciągły dane z systemami IT! Oczywiście występują różnice pomiędzy regionami i branżami, ale są one relatywnie niewielkie. Pomimo zatem zachodzących od kilku lat zmian i zwiększania stopnia integracji pomiędzy poziomami produkcyjnym i zarządzania przedsiębiorstwem, stopień informatyzacji przemysłu jest nadal niski.
Powyższy fakt traktujemy jako szansę biznesową - stwarza ona perspektywę wzrostów dla firm takich jak Rockwell Automation, jak też przekłada się na nowe możliwości dla naszych klientów. Ich produktywność może rosnąć nie tylko na skutek dalszej automatyzacji, ale też integracji systemów produkcyjnych z IT.
To ostatnie zresztą powinno być, naszym zdaniem, głównym powodem kolejnego, skokowego wzrostu produktywności. Tak może być szczególnie w przypadku rynków rozwiniętych, gdzie większość zakładów jest już zautomatyzowanych. Dopiero jednak zintegrowane sterowanie, komunikacja i integracja z IT przełożą się na podejmowanie lepszych i szybszych decyzji, a w efekcie na rozwój tych biznesów.
- Czy może w tym pomóc rozwój technologii Internetu Rzeczy?
KN: Zdecydowanie tak. IoT oraz wszechobecne użycie sieci ethernetowych pozwala na łączenie bardzo dużych oraz rozproszonych systemów. Wprawdzie po części było to już możliwe w przeszłości, ale teraz stało się znacznie tańsze i bardziej dostępne dla klientów. Weźmy pod uwagę producenta maszyn, który w swoich produktach wdrożył zdalne monitorowanie silników elektrycznych. Poprzez analizę danych pochodzących od setek klientów tworzą się zupełnie nowe możliwości w zakresie predykcyjnego utrzymania ruchu i zapewniania niezawodności pracy urządzeń!
Innym przykładem wykorzystania wielu źródeł danych i integracji systemów jest optymalizacja wykorzystania energii. Dotyczy to zarówno sieci smart grid, jak też inteligentnego korzystania ze źródeł energii. Przykładowo urządzenie czy cały system może na bazie informacji o kosztach surowców czy choćby bieżącej ceny energii korzystać z różnych źródeł zasilania.
W przyszłości coraz częściej będziemy chcieli liczyć zużycie energii i koszt na każdy pojedynczy produkt. Wymaga to nie tylko monitorowania urządzeń, ale też pełnego śledzenia produkcji. To ostatnie wpisuje się w szerszy trend, którym jest tzw. mass serialization - wytwarzanie personalizowanych produktów, ale ciągle w sposób masowy i przy zachowaniu niskich kosztów. Takie coś zdecydowanie wymaga integracji systemów produkcyjnych z warstwą zarządzania przedsiębiorstwem.
- Czy tego typu rozwiązania wdrożyliście w swoim zakładzie produkcyjnym w Twinsburgu?
KN: Tak - jest to doskonały przykład implementacji idei "smart manufacturing" i jednocześnie nasza jednostka referencyjna. W zakładzie wykorzystujemy połączone w sieci maszyny, których praca jest harmonogramowana z wykorzystaniem systemu MES. Zapewnia to możliwość wytwarzania krótkich serii oraz optymalizację produkcji, która bazuje bezpośrednio na zamówieniach od klientów.
Dzięki temu skróciliśmy czasy dostaw, udało się też zmniejszyć wielkość magazynu o jedną trzecią, zaś jakość wzrosła aż o 50% w stosunku do poprzedniego stanu. Omawiane rozwiązania wdrożyliśmy zresztą nie tylko w Twinsburgu - z inteligentnej produkcji korzystamy również w innych jednostkach produkcyjnych, w tym w Europie.
- Czy omawiana integracja dotyczy tylko pojedynczych zakładów, czy wykracza również poza ich obszar?
KN: Informatyzacja i integracja produkcji zdecydowanie wykracza dzisiaj poza teren hal fabrycznych. Przykładem jest tutaj wdrożenie w firmie Ford, gdzie wykorzystując oprogramowanie FactoryTalk ProductionCentre, połączono systemy zakładów w różnych częściach świata. W tym i podobnych przypadkach integrujemy produkcję oraz jej harmonogramowanie z łańcuchem zaopatrzeniowym. Pozwala to na uruchamianie i wykonywanie zleceń, bazując na aktualnych zamówieniach od klientów, również zakupy są realizowane na bieżąco, z uwzględnieniem zapotrzebowania działu produkcyjnego.
Sądzę, że takie systemy będą coraz częściej powstawały w przyszłości. Pozwalają one na produkcję zgodnie z zapotrzebowaniem, a nie prognozami, co istotnie zmienia kwestie magazynowania i logistyczne. Oczywiście integracja systemów produkcyjnych, łańcucha zaopatrzeniowego i zarządzania przedsiębiorstwem wiąże się również z licznymi wyzwaniami. Dotyczą one m.in. bezpieczeństwa systemów IT i produkcyjnych, a także rozwoju komunikacji i wspomnianej wcześniej potrzeby zmian organizacyjnych.
- Nasza poprzednia rozmowa miała miejsce ponad dwa lata temu - co zmieniło się od tego czasu w Waszej ofercie?
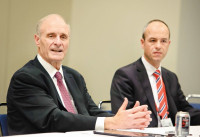
Keith Nosbusch (po lewej) oraz Thomas Donato
KN: Dwa lata temu podczas Automation Fair mówiliśmy o pewnej wizji w zakresie integracji obszarów IT oraz OT (Operational Technology) - dzisiaj zyskała ona konkretny wymiar fizyczny. Oferujemy gamę nowych produktów, które są lepiej dopasowane do zintegrowanych przedsiębiorstw, zmieniliśmy się również organizacyjnie. W tym czasie rozwinęliśmy też współpracę z Cisco, co również zaowocowało powstaniem kolejnych urządzeń łączących świat automatyki oraz IT.
TD: W centrum naszej oferty znajduje się jak dawniej platforma Logix wraz z oprogramowaniem Studio 5000, natomiast ostatnio rozwinęliśmy ją o wiele "inteligentnych" produktów. Takimi są sterowniki logiczne z wbudowanym oprogramowaniem PlantPAx Model Predictive Control służącym do sterowania predykcyjnego. Innym przykładem są nowe serwonapędy Kinetix 5700 z autotuningiem znacznie skracającym czas uruchamiania systemów wieloosiowych.
Rozwój dotyczy też oprogramowania - m.in. służącego do analizy dużych zbiorów danych (Big Data). Sądzimy, że przyszłością w przemyśle jest nie tylko przetwarzanie w chmurze, ale też analiza dokonywana bezpośrednio w systemie sterowania, czyli tzw. edge computing. Korzysta z niej wiele firm w branży oil & gas, gdzie wdrażamy zdalne monitorowanie pracy szybów naftowych oraz lokalną analizę wykonywaną w czasie bieżącym.
- Jak z Waszej perspektywy wyglądała sytuacja na rynku globalnym?
KN: Generalnie rozwój zwolnił zarówno w USA, jak też w Azji. Podczas gdy region EMEA cały czas się rozwijał, w Chinach - już przed końcem 2015 roku - obserwować można było słabnącą dynamikę rynku. Tamtejsze firmy miały niewykorzystane nadwyżki mocy produkcyjnej, a wiele małych i średniej wielkości przedsiębiorstw odczuwało problemy z pozyskiwaniem kapitału. Jeżeli chodzi o USA, to tutaj z kolei duży wpływ na rynek miały niskie ceny ropy naftowej i zwolnienie w sektorze oil & gas.
Na tle powyższego region Europy - szczególnie Środkowo-Wschodniej, radził sobie bardzo dobrze. Strefa euro na pewno skorzystała na słabszej walucie, zaś w przypadku Rockwella w regionie EMEA w ostatnim roku fiskalnym uzyskaliśmy w porównaniu do poprzedniego wzrost wynoszący 2,6%.
- Jak istotny jest obszar EMEA dla biznesu firmy Rockwell Automation? Jak wyglądał w ostatnich kilkunastu miesiącach rozwój poszczególnych jego rynków?
TD: Na to pytanie najlepiej odpowiedzieć, podając dane liczbowe. Region EMEA, czyli Europa, Bliski Wschód, Afryka, to w naszym przypadku oddziały lokalne w 28 krajach i prawie 5 tys. pracowników. Wśród nich jest około 850 osób zajmujących się usługami, pracuje tutaj również ponad tysiąc inżynierów tworzących rozwiązania dla klientów.
W regionie mamy trzy zakłady produkcyjne, w tym największy znajdujący się w Polsce. W Katowicach zatrudnionych jest obecnie 1200 pracowników, w tym w produkcji oraz w centrum usług wspólnych - m.in. finansowych oraz rozwoju oprogramowania. W obszarze EMEA osiągamy wartościowo około 20% całkowitych obrotów, co w zeszłym roku wyniosło 1,4 mld dolarów.
KN: EMEA to duży terytorialnie obszar, którego dynamika różni się w zależnie od regionu i branży. W ostatnim okresie odnotowaliśmy wzrosty m.in. we Włoszech i w Niemczech, a więc krajach silnych w zakresie produkcji maszyn, a także w Hiszpanii. Ciekawym dla nas rynkiem, tym razem związanym praktycznie tylko z klientami końcowymi, jest Afryka Południowa.
Jest to dzisiaj hub przemysłowy dla wielu krajów afrykańskich i jednocześnie obszar dla nas wiodący pod względem marżowości sprzedaży. Interesuje nas też Turcja, która jest bardzo zdywersyfikowanym rynkiem - znajduje się tam zarówno wielu producentów maszyn o różnym poziomie zaawansowania, jak też klientów końcowych będących firmami międzynarodowymi. Z kolei ostrożni jesteśmy w stosunku do Rosji, co wynika głównie z przyczyn politycznych. Długofalowo jednak traktujemy ten rynek jako perspektywiczny, szczególnie z uwagi na branżę energetyczną i sektor wydobywczy.
Bardzo dobrze po raz kolejny prezentował się na tle globalnym region Europy Środkowo-Wschodniej. W Polsce, w Czechach czy na Słowacji działa wiele firm produkcyjnych, są tu również wytwórcy maszyn. W regionie odnotowaliśmy wzrosty, które były, zależnie od krajów i grup produktów, jedno- lub dwucyfrowe. Sądzę, że w przypadku omawianych rynków szczególnie korzystne było wprowadzenie przez nas nowych produktów - szczególnie z zakresu midrange.
- Dywersyfikacja przemysłu w regionie jest z pewnością wyzwaniem dla działających tutaj globalnych dostawców automatyki. Jaka jest Wasza strategia i plany dotyczącego tego obszaru?
TD: Europy i, szerzej, całego regionu EMEA nie traktujemy jako monolitu. W każdym z krajów wyróżniamy kluczowe obszary rynku oraz typy aplikacji - i to odpowiednio do nich rozwijamy oddziały lokalne i zasoby ludzkie. Specjalizujemy się w rynkach wertykalnych - takimi są dla nas m.in. oil & gas, motoryzacyjny, wodociągowo-kanalizacyjny oraz produkcji towarów konsumenckich i spożywczy.
Innymi słowy, identyfikujemy branże oraz aplikacje, gdzie możemy klientom zapewnić ofertę produktów i rozwiązań, a także wartość dodaną w postaci naszego know-how. W każdym z państw skupiamy się na określonych domenach, dopasowując się do potrzeb lokalnych klientów i aktualnego stanu rozwoju technologicznego rynku.
Dzięki strategii specjalizacji mogliśmy stworzyć też bazę referencji w różnych krajach, dzięki czemu możemy przekonywać potencjalnych klientów, pokazując im nie tylko ofertę produktów, ale przede wszystkim demonstrując nasze rozwiązania i know-how. Jest to szczególnie ważne w przypadku oferty z obszaru The Connected Enterprise, bowiem w jej przypadku wartością są nie tylko pojedyncze produkty, ale przede wszystkim kompletne, innowacyjne rozwiązania. Z tego również powodu adresujemy nasz przekaz nie tylko do inżynierów i służb utrzymania ruchu, ale też coraz częściej do menedżerów i osób odpowiadających w firmach przemysłowych za rozwój biznesu.
- Dziękujemy za rozmowę.