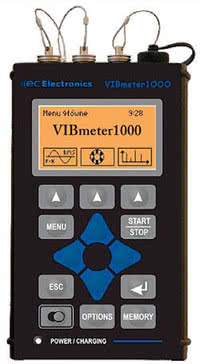
Fot. 1. VIBmeter1000 firmy EC Electronics
Wibracje, tzn. cykliczne odchylenia maszyny lub jej części od pozycji ustalonej, są skutkiem sił powstających wewnątrz urządzenia - na przykład w wyniku niewyważenia jego wirujących elementów lub nierównomiernego rozkładu pola magnetycznego w silniku. W urządzeniach takich jak wentylatory, dmuchawy i pompy drgania są też wywoływane przez turbulencje w przepływie medium, z kolei w turbinach gazowych oraz kotłach mogą zachodzić turbulencje w procesie spalania.
Wibracje występują też na skutek tarcia, niewspółosiowości, obluzowania komponentów maszyn - na przykład pasów napędowych, osłabienia mocowania urządzenia z podstawą lub jej pęknięcia (rys. 1). Drgania wewnętrznych podzespołów przenoszą się też na obudowę, co może wzbudzać inne komponenty lub sąsiadujące maszyny do drgań. Nadmierne wibracje są więc przeważnie oznaką jakiegoś problemu w funkcjonowaniu maszyny, a zbagatelizowane prowadzić mogą m.in. do skrócenia czasu jej użytkowania lub jego części.
Na przykład dodatkowe dynamiczne obciążenie źle wpływa na pracę łożysk, komponentów i bez tego będących jedną z częstszych przyczyn awarii maszyn. Ponadto w przypadku precyzyjnych maszyn do obróbki drgania negatywnie wpływają na stan produktu, w tym na przykład na dokładność jego wymiarów lub jakość wykończenia powierzchni.
Case study: Wibrodiagnostyka demaskuje nieprawidłowe mocowanie silnikaW pewnym zakładzie tuż po uruchomieniu nowego zespołu pompa odśrodkowa-silnik, wystąpiły duże wibracje. Ich przyczyny bezskutecznie szukano przez kilka dni, m.in. rozmontowując pompę, sprawdzając pod tym kątem łożyska, a także konsultując się z producentami tych komponentów. Ostatecznie zdecydowano się poprosić o pomoc specjalistów z zakresu wibrodiagnostyki. Przeprowadzone przez nich pomiary ujawniły, że prawdopodobną przyczyną jest rezonans podstawy, na której zamontowano urządzenia. Zaczęto wówczas podejrzewać, że wibracje te mają związek z konstrukcją mocującą silnik, którą stanowiły dwie równoległe belki. Na każdej z nich opierała się jedna noga silnika. Ponieważ nie zastosowano żadnego połączenia między belkami, pod silnikiem pozostała wolna przestrzeń. Inżynierowie zdecydowali się w związku z tym na odłączenie zespołu silnika i pompy, a następnie przeprowadzenie testów polegających na uderzaniu młotem w podstawę, na której zamocowano czujnik wibracji. Okazało się, że częstotliwość rezonansowa podstawy wynosi 3600 cykli/min. Odnosząc ten wynik do prędkości obrotowej silnika przy pełnym obciążeniu, która wynosiła 3585 obr./min., uznano zagadkę źródła nadmiernych wibracji za rozwiązaną. Następnie, aby zapobiec drganiom, konstrukcję mocującą silnik wzmocniono, a pomiary wibracji po uruchomieniu zespołu silnika i pompy powtórzono. Okazało się, że poziom drgań zmniejszył się do wartości dopuszczalnej. |
POMIARY WIBRODIAGNOSTYCZNE
Obsługując dane urządzenie, często łatwo można zorientować się od razu, gdy coś odbiega od normy - na przykład maszyna jest za gorąca lub zaczyna wibrować podczas pracy. Nie jest to jednak miarodajny sposób oceny stanu urządzenia, ponieważ wymaga sporego doświadczenia w jego obsłudze, a ponadto każdy człowiek może inaczej interpretować odbierane wrażenia zmysłowe. Ponadto niektórych usterek w ich wczesnej fazie, np. awarii łożysk lub przekładni, w ten sposób w ogóle nie można wykryć.
Z powyższych powodów w praktyce wykorzystuje się analizatory wibracji, które mierzą drgania, dostarczając wyniki pomiarów w postaci umożliwiającej ich porównanie z wartościami zamieszczonymi na przykład w normie lub w charakterystyce urządzenia. Przyrządy te, oprócz różnych dodatkowych funkcji, przeważnie mierzą cztery najważniejsze parametry drgań, tzn. ich częstotliwość, przemieszczenie, prędkość i przyspieszenie. Na podstawie każdego z nich lub kilku łącznie można wyciągnąć wnioski o aktualnym stanie urządzenia.
|
CZĘSTOTLIWOŚĆ DRGAŃ
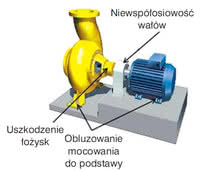
Rys. 1. Tarcie, niewspółosiowość, obluzowanie komponentów maszyn, osłabienie mocowania urządzenia z podstawą lub jej pęknięcie - to częste przyczyny nadmiernych wibracji
Szukanie źródła awarii objawiającej się nadmiernymi wibracjami to w praktyce proces eliminacji, w którym cennym źródłem informacji może być widmo częstotliwościowe drgań. Analizując je, można powiązać częstotliwość wibracji z prędkością obrotową konkretnego elementu maszyny. Jeżeli częścią urządzenia jest na przykład wentylator z silnikiem o prędkości 2000 obr./min oraz pas napędzany przez silnik o prędkości 3400 obr./min, a zarejestrowane wibracje występują z częstotliwością 2000 cykli/min, jest bardzo prawdopodobne, że źródłem anomalii jest wentylator.
Wówczas z dalszej analizy można od razu wykluczyć pas napędowy i różne problemy w jego funkcjonowaniu, jak również napędzający go silnik, w tym np. problemy w zasilającej go instalacji elektrycznej. Niestety nie zawsze tak łatwo skojarzyć można objawy z ich przyczyną. Niektóre problemy, jak na przykład obluzowanie jakiegoś komponentu lub niewspółosiowość współpracujących elementów, są źródłem wibracji o częstotliwości odpowiadającej wielokrotności prędkości obrotowej komponentu.
Tak jest m.in. w przekładniach, w przypadku których problemy objawiają się wibracjami o częstotliwości równej na przykład iloczynowi liczby zębów i prędkości obrotów. Podobnie aerodynamiczne problemy w pracy wentylatorów skutkować mogą wibracjami o częstotliwości, która jest iloczynem prędkości obrotowej i liczby łopatek wirnika.
Często też nie sposób w ogóle powiązać częstotliwości drgań z prędkością obrotową jakiegokolwiek komponentu maszyny, na przykład gdy wibracje są generowane na skutek defektów łożysk lub gdy ich przyczyna ma charakter bardziej złożony, a drgania o różnych częstotliwościach nakładają się na siebie.
PRĘDKOŚĆ, PRZEMIESZCZENIE, PRZYSPIESZENIE
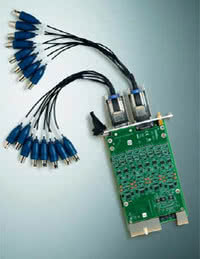
Fot. 2. Moduł akwizycji sygnałów analogowych w standardzie PXI firmy National Instruments
W przypadkach jak wymienione pomocna jest analiza pozostałych parametrów drgań - na przykład ich prędkości. Parametr ten określa, jak szybko obiekt przemieszcza się między dwoma skrajnymi wychyleniami od pozycji ustalonej. Od tej wartości zależy jak szybko dana część ulegnie awarii na skutek zmęczenia materiału. Z kolei drgania wywołujące nadmierne naprężenia materiału oraz odchylenia poza dopuszczalnym zakresem mogą powodować na przykład złamanie śrub mocujących maszynę do podstawy, pęknięcia spoin oraz betonowych podstaw urządzenia.
Dlatego ważny jest też trzeci parametr wibracji - przemieszczenie. Był to zresztą pierwszy parametr, którego pomiar zaimplementowano w miernikach wibracji. Pierwsze urządzenia tego typu - wibrometry wskazówkowe - były bowiem miernikami mechanicznymi i umożliwiały jedynie pomiar odległości między dwoma skrajnymi położeniami drgającego komponentu.
Ostatnim parametrem jest przyspieszenie, które charakteryzuje siłę oddziałującą na odchylany obiekt. Jeżeli jest ona duża to nawet jeżeli jednocześnie przemieszczenie jest nieznaczne, obiekt może ulec deformacji. Problem ten może dotyczyć na przykład zębów przekładni oraz łożysk. Wystąpić może też duże tarcie skutkujące nadmiernym wydzielaniem ciepła.
Case study: Pęknięta podstawa destabilizuje pracę turbiny i generatoraW pewnym zakładzie zarejestrowano nagły wzrost wibracji zespołu turbina gazowa-generator, który wykorzystywany był w instalacji zasilania tego kompleksu przemysłowego. Poziom drgań był na tyle wysoki, że konieczne było wstrzymanie pracy generatora. W efekcie spowodowało to konieczność zakupu energii elektrycznej z sieci publicznej. Ponieważ wiązało się to ze znacznym wzrostem kosztów, rozpoczęto przyspieszone poszukiwania przyczyny anomalii, sprawdzając m.in. generator i zasilającą go instalację elektryczną. Niestety, w ten sposób ustalono jedynie, że problem ma swoje źródło praw dopodobnie w skrzyni przekładniowej. Jednocześnie zauważono, że poziom wibracji wzrasta przy większym obciążeniu skrzyni. Skłoniło to przedstawicieli służb utrzymania ruchu ku tezie, że przyczyną może być pęknięcie obudowy i pod tym kątem przeprowadzono dokładne oględziny skrzyni. Okazało się, że wniosek był słuszny, bo na podstawie rzeczywiście odkryto powiększającą się rysę. Po zabezpieczeniu pęknięcia ponownie uruchomiono zespół turbina-generator. Wtedy już poziom drgań zmniejszył się do wcześniejszego, dopuszczalnego. |
CO KIEDY MIERZYĆ
Przyjmuje się, że w określonych zakresach częstotliwości należy zwrócić szczególną uwagę na konkretne parametry. Na przykład w wypadku wibracji o małych częstotliwościach uszkodzenia są powodowane zazwyczaj przez zbyt duże wychylenie, dlatego dla drgań o częstotliwości poniżej 10Hz dominujące znaczenie ma wartość przemieszczenia.
Z kolei w zakresie częstotliwości od 10Hz do 2 kHz, nawet przy małej wartości przemieszczenia, uszkodzenie może być spowodowane zmęczeniem materiału. Wówczas na znaczeniu zyskuje prędkość, z jaką obiekt drga. Przy częstotliwościach powyżej 2 kHz zaleca się z kolei, by mierzyć przyspieszenie.
|
CZUJNIKI I WARUNKI POMIARU
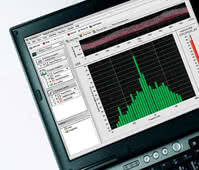
Fot. 3. Obróbkę danych z czujników wibracji ułatwia pakiet oprogramowania NI Sound and Vibration Measurement Suite
O tym, czy zarejestrowane wyniki okażą się użyteczne, decyduje przede wszystkim wybór typu czujnika oraz sposób przeprowadzania pomiaru, głównie zamocowania sensora. Bez należytej staranności w zakresie tych dwóch kwestii dane z systemu pomiarowego mogą wprowadzić personel w błąd, na przykład bezpodstawnie wskazując na awarię. Podstawowe parametry wibracji można mierzyć różnymi czujnikami - co więcej, dzięki łączącym je zależnościom matematycznym na podstawie jednego parametru można wyznaczyć też pozostałe.
Często wykorzystuje się bezkontaktowe sensory zbliżeniowe - na przykład sondy wiroprądowe. W przypadku gdy występuje problem z zamontowaniem sond bezkontaktowych, wykorzystać można np. piezoelektryczne akcelerometry. W zakresie sposobu montażu czujnika powinno obowiązywać kilka zasad. Przede wszystkim punkty pomiarowe powinny być dokładnie określone i wyraźnie oznaczone.
Powierzchnia, do której czujnik zostanie przymocowany - na przykład magnesem, powinna być płaska, czysta i niezatłuszczona (powinno się usunąć smary). Należy też zwrócić uwagę, aby przed zamocowaniem czujnika usunąć z powierzchni złuszczoną farbę oraz oczyścić powierzchnie zardzewiałe.
Czujnik powinien być też odpowiednio zabezpieczony, tak by w czasie pomiaru się nie przemieszczał. Dotyczy to również okablowania łączącego sensor z systemem pomiarowym. W przypadku pomiarów powtarzanych kilkukrotnie w celu porównania wyników należy też zadbać o to, aby warunki pracy, na przykład obciążenie, w czasie każdego testu były porównywalne.
|
SYSTEMY POMIAROWE
W przemyśle popularne są wielofunkcyjne mierniki podręczne. Przykładem jest VIBmeter1000 oferowany przez firmę EC Electronics (fot. 1), który oprócz pomiaru standardowych parametrów wibracji (przyspieszenia w zakresie do 500 m/s², prędkości w zakresie do 500 mm/s i przemieszczenia do 5000μm) umożliwia przeprowadzanie analizy widmowej drgań, pomiar prędkości obrotowej (w zakresie od 60 do 20 tys. obrotów/min) i fazy wibracji. Może też pełnić funkcję wyważarki.
Do rejestracji danych z pojedynczych czujników wibracji można wykorzystać moduły akwizycji danych przetwarzające sygnały analogowe z sensorów do postaci cyfrowej. Urządzenia takie znaleźć można na przykład w asortymencie firmy National Instruments, która oferuje m.in. moduły akwizycji danych bazujących na standardzie PXI (fot. 2). Sygnał cyfrowy można dalej przetwarzać i analizować w komputerze, wykorzystując specjalne oprogramowanie rozbudowane o dodatkowe funkcje ułatwiające obróbkę tych danych.
Przykładem jest Sound and Vibration Measurement Suite (fot. 3), pakiet narzędzi do obróbki i analizy sygnałów z czujników dźwięku i wibracji również z oferty National Instruments. Okresowa diagnostyka nie jest rozwiązaniem optymalnym w przypadku, gdy chcemy badaniem objąć większą grupę urządzeń lub pomiary zamierzamy wykonywać w krótkich odstępach czasu. W drugim przypadku trudno na przykład o zapewnienie powtarzalności w zakresie rozmieszczenia czujników.
Rozwiązaniem jest stworzenie automatycznego systemu kontroli drgań, co można zrealizować, integrując system wibrodiagnostyki z systemem automatyki już pracującym w zakładzie. Zarejestrowane przebiegi można wówczas wizualizować na przykład w oprogramowaniu SCADA. Można też tak skonfigurować system, aby sygnalizował przypadki przekroczenia limitów drgań ustalonych dla poszczególnych maszyn.
Monika Jaworowska