ETHERNET POWERLINK
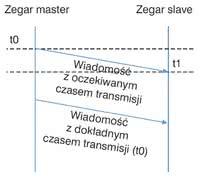
Rys. 4. Proces synchronizacji według wytycznych standardu IEEE 1588 rozpoczyna się od wyznaczenia różnicy czasów zegarów master i slave
Protokół ten został opracowany w 2001 roku przez firmę B&R, a obecnie jego rozwojem zajmuje się organizacja Ethernet Powerlink Standardization Group (EPSG). W zakresie kontroli dostępu do łącza jest w nim wykorzystywany mechanizm szczelin czasowych (timeslots), które są przyporządkowywane poszczególnym stacjom oraz procedura odpytywania (polling).
W sieci funkcję nadrzędną pełni węzeł typu MN (Managing Node), którego zadaniem jest koordynacja transmisji danych. Przydziela on uprawnienia do nadawania węzłom podrzędnym typu CN (Controlled Node) oraz synchronizuje je. W każdym cyklu transmisji wyróżnić można trzy przedziały (rys. 2). W pierwszym MN wysyła do wszystkich CN ramkę SoC (Start of Cycle), która synchronizuje te węzły.
Następnie zachodzi wymiana danych izochronicznych. MN wysyła kolejno w stałym porządku do poszczególnych CN zapytanie (Poll Request). Każdy z węzłów podrzędnych natychmiast na nie odpowiada, dzięki czemu unika się kolizji. Ramka odpowiedzi (Poll Response) jest dostępna także dla pozostałych CN (broadcast).
W trzeciej fazie cyklu przesyłane są dane asynchroniczne. Mogą to być duże pakiety danych o niekrytycznym znaczeniu, które są dzielone na części i transmitowane oddzielnie, w kilku cyklach. W ten sposób przesyła się na przykład dane konfiguracyjne lub ramki TCP/IP.
By dany węzeł mógł rozpocząć transmisję takich informacji, musi o tym poinformować wcześniej w odpowiedzi na zapytanie MN. Na tej podstawie węzeł nadrzędny tworzy listę oczekujących CN, według której dane asynchroniczne są później nadawane.
Ethernet Powerlink w sterowaniu maszyną do etykietowania
Dane te wykorzystywane są później w sterownikach głowic. Wymiana informacji między tymi podsystemami musi być realizowana w czasie rzeczywistym - wymagana jest bowiem duża szybkość nanoszenia etykiet oraz zdolność do szybkiej adaptacji maszyny do często zmieniających się typów znakowanych produktów. W pierwotnej wersji system sterowania maszyną z dwoma głowicami składał się łącznie z aż siedmiu kontrolerów ruchu. Producent zdecydował się jednak zmodyfikować projekt urządzenia, zastępując dotychczas używane sterowniki trzema kontrolerami serii NextMove e100 firmy Baldor (obecnie firma należy do ABB) wyposażonymi w interfejs Ethernet Powerlink. Wprowadzenie sieci ethernetowej umożliwiło szeregowe połączenie wszystkich serwomotorów oraz pozostałych urządzeń I/O maszyny. Dzięki temu uzyskano oszczędność miejsca oraz ograniczono wydatki na okablowanie. Łatwiejsza stała się też rozbudowa maszyny. |
ETHERCAT
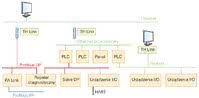
Rys. 5. TH-Link służą do podłączenia komputera z aplikacją diagnostyczną do sieci Profinet
EtherCAT (Ethernet for Control Automation Technology) został opracowany przez firmę Beckhoff Automation, a obecnie w jego rozwój i popularyzację jest też zaangażowana organizacja ETG (EtherCAT Technology Group). Komunikacja w sieci zorganizowana jest według modelu master-slave z dodatkowym mechanizmem przetwarzania ramki w locie - węzeł nadrzędny wysyła jedną ramkę ethernetową, w której umieszczane są wiadomości przeznaczone dla wszystkich węzłów podrzędnych, a nie tylko dla jednego odbiorcy.
Ramka taka dociera po kolei do wszystkich stacji w sieci (rys. 3). Każda z nich najpierw sprawdza, czy w ramce znajdują się dane, których jest odbiorcą. Jeżeli tak, to odczytuje odpowiedni fragment, a następnie dodaje swoją odpowiedź - na przykład potwierdzającą odbiór wiadomości. Ramka jest wówczas przesyłana dalej, a kiedy dotrze do ostatniego węzła, zostaje zawrócona.
Sieci EtherCAT pracują zatem w topologii logicznego pierścienia. Dzięki temu, że w ramce przenoszone są dane do i od wielu węzłów sieci jednocześnie, zostaje rozwiązany problem nieprzystosowania Ethernetu do transmisji małych pakietów danych. W standardowej ramce ethernetowej dane kontrolne mogą bowiem zajmować więcej miejsca niż zasadnicza informacja.
Najkrótsza ramka ethernetowa ma rozmiar 84 bajtów. Jeżeli przykładowo urządzenie okresowo przesyła 4 bajty informacji, to wykorzystuje ją w niespełna 5%, podczas gdy dla EtherCAT jest to nawet w ponad 90%. W sieciach przemysłowych ma to ogromne znaczenie, ponieważ za ich pośrednictwem najczęściej przesyłane są właśnie małe ilości informacji - na przykład wyniki pomiarów oraz instrukcje sterujące.
ETHERNET/IP
Protokół Ethernet/IP (Ethernet Industrial Protocol, EIP) został opracowany w 2000 roku przez firmę Rockwell Automation, natomiast jego rozwojem obecnie zajmuje się m.in. organizacja ODVA (Open DeviceNet Vendors Association). EIP opiera się na protokole CIP (Common Industrial Protocol). Definiuje on profile różnych urządzeń przemysłowych, w których scharakteryzowane są ich właściwości i metody komunikowania się.
W Ethernet/IP wyróżniono też dwa rodzaje wiadomości. Do pierwszej grupy zaliczane są dane o znaczeniu niekrytycznym, na przykład diagnostyczne lub konfiguracyjne (Explicit Messages). Do ich transmisji wykorzystywany jest protokół TCP. Dane, które muszą być transmitowane w czasie rzeczywistym (Implicit Messages), są z kolei przesyłane za pośrednictwem protokołu UDP.
Zastosowanie priorytetyzacji Quality of Service gwarantuje, że pakiety drugiego typu będą miały wyższy priorytet. Ethernet/ IP korzysta również z protokołu CIPsync, który zapewnia synchronizację zegarów czasu rzeczywistego w rozproszonych systemach. Taka możliwość jest wymagana w systemach koordynujących działanie kilku podsystemów - na przykład w wieloosiowych
Rys. 6. Bramy sieciowe firmy HMS z oferty Elmark Automatyka