Maszyny, które są sprzedawane na rynku europejskim, powinny spełniać wymagania Nowej Dyrektywy Maszynowej, czyli 2006/42/WE. Przyjmuje się, że zgodność taka w określonym zakresie jest zapewniona, jeżeli urządzenie zostało zaprojektowane i wykonane według zasad podanych w odpowiednich normach zharmonizowanych z tą dyrektywą.
Standardy zharmonizowane podzielone są na trzy grupy: A, B i C. Normy typu A zawierają ogólne wymagania, wskazówki projektowe oraz podstawowe pojęcia z zakresu bezpieczeństwa maszyn. Przykładem jest PN-EN ISO 12100, w której określono m.in. zasady oceny oraz zmniejszania ryzyka technicznego maszyn.
NORMY GRUP WYROBÓW
Z kolei w standardach typu B podane są wymogi bezpieczeństwa wspólne dla wszystkich maszyn. Te tzw. normy grup wyrobów również dzieli się na typy. Do standardów B1 zaliczane są te, w których zdefiniowano wybrane aspekty bezpieczeństwa maszyn (przykładowo ergonomię, bezpieczne odległości, wymagania elektryczne).
Normy typu B2 dotyczą natomiast konkretnych urządzeń zabezpieczających (na przykład mat i przycisków bezpieczeństwa, osłon, systemów detekcji ruchu).
Przykładami standardów typu B są:
- PN-EN 62061 "Bezpieczeństwo maszyn - Bezpieczeństwo funkcjonalne elektrycznych, elektronicznych i elektronicznych programowalnych systemów sterowania związanych z bezpieczeństwem",
- PN-EN ISO 13849-1 "Bezpieczeństwo maszyn - Elementy systemów sterowania związane z bezpieczeństwem - Część 1: Ogólne zasady projektowania",
- PN-EN 1088, w której opisano zasady projektowania oraz doboru urządzeń blokujących sprzężonych z osłonami
- PN-EN I SO 13850, określająca warunki użytkowania i zasady projektowania funkcji zatrzymania awaryjnego maszyn.
OD OGÓŁU DO SZCZEGÓŁU
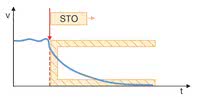
Rys. 1. Funkcja bezpieczeństwa STO polega na odłączeniu zasilania od silnika - nie wytwarza on wówczas momentu obrotowego (siły)
W normach typu C przedstawiane są wymogi bezpieczeństwa dla konkretnych urządzeń, które uzupełniają lub, jeżeli dotyczą tej samej kwestii, zastępują te zawarte w normach typu A i B.
Przykładem jest norma produktowa PN-EN 61800-5-2. Dotyczy ona elektrycznych układów napędowych o regulowanej prędkości, w których można zrealizować różne funkcje bezpieczeństwa (Power Drive System with Safety-Related Functions), czyli PDS(SR).
Te ostatnie to m.in.:
- bezpieczne wyłączenie momentu (Safe Torque Off , STO),
- bezpieczny stop 1 oraz 2 (Safe Stop 1, Safe Stop 2, SS1, SS2),
- bezpieczne zatrzymanie pracy (Safe Operating Stop, SOS),
- bezpiecznie ograniczona prędkość (Safely Limited Speed, SLS),
- bezpieczny zakres prędkości (Safe Speed Range, SSR),
- bezpieczny kierunek ruchu (Safe Direction, SDI),
- bezpiecznie ograniczona długość kroku (Safe Limited Increment, SLI),
- bezpieczne wysterowanie hamulców (Safe Brake Control, SBC)
- bezpieczny test hamulców (Safe Brake Test, SBT).
NORMY POWIĄZANE
Do scharakteryzowania funkcji bezpieczeństwa w PN-EN 61800-5-2 wykorzystywane są trzy kategorie zatrzymania zdefiniowane w normie PN-EN 60204-1 "Bezpieczeństwo maszyn - Wyposażenie elektryczne maszyn - Część 1: Wymagania ogólne". Zatrzymanie niekontrolowane kategorii 0 polega na natychmiastowym odłączeniu zasilania od napędu maszyny.
W przypadku zatrzymania kontrolowanego kategorii 1 napęd maszyny jest podłączony do źródła napięcia do momentu jej całkowitego zatrzymania - dopiero wówczas zasilanie jest odcinane. Z kolei w wypadku zatrzymania kontrolowanego kategorii 2 zasilanie po unieruchomieniu maszyny w ogóle nie jest odłączane.
Według PN-EN 60204-1 funkcja zatrzymania awaryjnego powinna być zrealizowana jako zatrzymanie niekontrolowane kategorii 0 lub kontrolowane kategorii 1. Producenci urządzeń PDS(SR) są ponadto zobowiązani do określenia w ich specyfikacji poziomu nienaruszalności (zapewnienia) bezpieczeństwa.
Parametr ten może być wyrażony jako jeden z trzech poziomów nienaruszalności bezpieczeństwa SIL (Safety Integrity Level) lub jeden z pięciu poziomów bezpieczeństwa PL (Performace Level). Poszczególnym poziomom przyporządkowane są przedziały prawdopodobieństwa wystąpienia błędu skutkującego niezadziałaniem funkcji ochronnej. Im wyższy jest ten stopień, tym mniej prawdopodobne jest, że zabezpieczenie nie zadziała.
Klasyfikacja wskaźników SIL przedstawiona jest w normie PN-EN 62061, a PL w PN-EN ISO 13849-1. Ta pierwsza bazuje na normie PN-EN 61508, a jej wymagania mogą być stosowane wyłącznie do systemów elektronicznych.
Z kolei PN-EN 13849- 1 (wraz z innymi normami) zastąpiła wcześniej stosowaną PN-EN 954-1, rozszerzając zastosowania pod względem zakresu urządzeń (np. systemów pneumatycznych oraz hydraulicznych) oraz wprowadzając probabilistyczną ocenę ryzyka. Porównanie wskaźników SIL oraz PL przedstawiono w tabeli 1. Poniżej zaś przedstawiamy charakterystykę wybranych funkcji oraz ich przykładowe zastosowania.
STO
Funkcja bezpieczeństwa STO (rys. 1) polega na odłączeniu zasilania od silnika, w efekcie czego nie wytwarza on momentu obrotowego lub siły (w wypadku silników liniowych). Odpowiada to niekontrolowanemu zatrzymaniu kategorii 0 według klasyfikacji przedstawionej w normie PN-EN 60204-1.
STO jest podstawową metodą zapobiegania nagłemu i nieoczekiwanemu rozruchowi silnika powodującemu niekontrolowane przemieszczenie się ruchomych części maszyny. Najlepiej sprawdza się w przypadku, gdy nie jest wymagane natychmiastowe zatrzymanie całego układu napędowego. Tarcie oraz inercja silnika i jego mechanicznego obciążenia wpływają bowiem na szybkość hamowania.
Dlatego ważne jest, by ta ostatnia zapewniała w danym przypadku odpowiedni poziom bezpieczeństwa. W pewnych zastosowaniach STO konieczne jest też użycie dodatkowych mechanizmów (na przykład hamulców w połączeniu z funkcją SBC), które zapobiegną samoistnemu przemieszczaniu się mechanicznych obciążeń układu napędowego pod wpływem sił zewnętrznych (na przykład grawitacji).
To ostatnie stanowi duże zagrożenie dla pracowników, którzy przekonani o zadziałaniu funkcji zatrzymania znaleźliby się w strefie zabronionej.
SS1
Bezpieczny stop SS1 to dwuetapowa funkcja bezpieczeństwa (rys. 2). W pierwszej fazie następuje stopniowe zmniejszanie prędkości silnika aż do jego zatrzymania. Następnie aktywowana jest funkcja STO (oraz SBC, jeżeli jest dostępna). W normie PN-EN 61800-5-2 założono pewną dowolność w zakresie realizacji funkcji SS1, dopuszczając dwie możliwości.
W pierwszym przypadku prędkość silnika jest monitorowana i dopiero, gdy jest mniejsza niż wartość graniczna, aktywowana zostaje funkcja bezpiecznego wyłączenie momentu. W wypadku, gdy zmiana prędkości silnika w czasie jego hamowania nie jest kontrolowana, funkcja STO zostaje załączona po pewnym czasie, z góry określonym i dostosowanym do potrzeb danej aplikacji.
Bezpieczny stop typu pierwszego odpowiada kontrolowanemu zatrzymaniu kategorii 1 według normy PN-EN 60204-1 (a po wyłączeniu silnika - zatrzymaniu kategorii 0). Funkcja SS1 jest zalecana, gdy wymagane jest jak najszybsze zatrzymanie maszyny, zwłaszcza ciężkich, wirujących obciążeń mechanicznych lub silnika pracującego z dużą prędkością. Typowe zastosowania bezpiecznego stopu 1 to m.in. hamowanie napędów pił, wrzecion szlifierek, wirówek oraz pras.
Integracja funkcji bezpieczeństwa to najnowszy trend w zakresie konstrukcji napędów elektrycznych. Urządzenia takie w swojej ofercie ma większość producentów, m.in. Mitsubishi Electric, Siemens, Lenze, Rockwell Automation i B&R. Poniżej prezentujemy przykładowe produkty:
Wybrane funkcje i cechy: bezczujnikowe sterowanie wektorowe, autotuning (identyfikacja parametrów silnika), przeciążalność 200% przez 3 s (150% przez 60 s), ograniczanie momentu / prądu w czasie rozruchu i hamowania, możliwość podłączenia zewnętrznego hamulca załączanego przez przetwornicę, kontrolowane hamowanie po chwilowym braku zasilania, automatyczny restart po awarii zasilania, zintegrowana funkcja STO według PN-EN 61800-5-2, rozwiązania konstrukcyjne wydłużające żywotność; zakres mocy 0,1÷2,2 kW (FR-E720S), 0,4÷15 kW (FR-E740), stopień ochrony IP20. www.mitsubishi-automation.plWybrane funkcje i cechy: konstrukcja modułowa (jednostka sterująca + moduł mocy), sterowanie wektorowe, skalarne i FCC (Flux Current Control), zintegrowane funkcje bezpieczeństwa (kategorii 3 według PN-EN 954-1, SIL 2 według PN-EN 61508, PL d według PN-EN 13849-1), bez enkodera: bezpieczne wyłączenie momentu, bezpieczny stop 1, bezpiecznie ograniczona prędkość, bezpieczny kierunek ruchu, interfejsy komunikacyjne: Profinet, Profibus, Profisafe, Modbus RTU, CANopen, BacNet, MS / TP, port USB, zintegrowane funkcje PLC, zakres mocy 0,37 kW - 250 kW. www.automatyka.siemens.pl
Wybrane funkcje i cechy: zakres mocy 0,75÷250 kW (PowerFlex 753), 0,75÷900 kW, 200÷1000 kW ( PowerFlex 755), karty rozszerzeń dla sieci Ethernet/IP, ControlNet, DeviceNet i różnych sieci przemysłowych, wbudowany port Ethernet (funkcje zależne od modelu); typy silników: indukcyjne (Power Flex 753), indukcyjne i z magnesem trwałym (PowerFlex 755), wbudowany sterownik PLC DeviceLogix, zintegrowane funkcje bezpieczeństwa (SIL 3, PL e, kategoria 3 lub 4): bezpieczne wyłączenie momentu, bezpieczne zatrzymanie, ograniczona prędkość bezpieczna, maksymalna prędkość bezpieczna, maksymalne przyspieszenie bezpieczne, kierunek bezpieczny, monitorowanie prędkości zerowej, sterowanie i monitorowanie drzwi. www.rockwellautomation.pl |
SS2 Z SOS
Funkcja bezpiecznego stopu 2, podobnie jak SS1, jest dwuetapowa (rys. 3). Po jej aktywowaniu silnik zostaje w określonym czasie wyhamowany, a następnie inicjowana jest funkcja SOS. W jej wypadku, w przeciwieństwie do STO, zasilanie napędu silnika nie jest wyłączane. Dzięki temu podtrzymywany jest moment obrotowy - w rezultacie silnik zostaje unieruchomiony w określonej pozycji.
Przez cały czas działania tego zabezpieczenia położenie jest monitorowane oraz odpowiednio utrzymywane przez sterownik napędu. Funkcja SS2 odpowiada kontrolowanemu zatrzymaniu kategorii 2 według PN-EN 60204-1. Bezpieczny stop 2, podobnie jak SS1, gwarantuje szybkie zatrzymanie silnika. Równocześnie dzięki temu że zasilanie nie jest odłączane, restart silnika jest szybszy.
Dlatego funkcja SS2 jest zwykle wykorzystywana, gdy maszyna lub jej część powinna przez krótki czas pozostać unieruchomiona przy włączonym zasilaniu. Wymagać tego może specyfika procesu produkcyjnego lub konieczność wykonania okresowych, krótkotrwałych prac konserwacyjnych. Przykładem jest czyszczenie lub regulacja komponentów systemu wizyjnego zainstalowanego w obrębie danej linii produkcyjnej lub usunięcie z niej resztek materiałów.
SLS, SSR, SDI, SBC
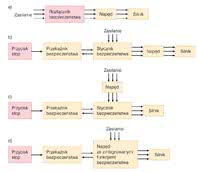
Rys. 6. Zatrzymanie silnika można zrealizować z wykorzystaniem rozłącznika bezpieczeństwa (a), przekaźnika oraz stycznika umieszczonego przed (b) lub za napędem (c); alternatywą są napędy ze zintegrowanymi funkcjami bezpieczeństwa (d)
Działanie funkcji SLS polega na monitorowaniu prędkości silnika (rys. 4). W razie przekroczenia ustalonej wartości granicznej podejmowane jest odpowiednie działanie określone na etapie konfiguracji. Zwykle aktywowane jest wówczas bezpieczne wyłączenie momentu i silnik jest zatrzymywany.
Funkcja bezpiecznego ograniczenia prędkości jest użyteczna wtedy, gdy operator musi wykonać pewne czynności (konserwacyjne, konfiguracyjne, itp.) w pracującym urządzeniu, a niemożliwe lub nieefektywne jest jego całkowite zatrzymanie. Przykładem są maszyny, których podajniki trzeba co jakiś czas ręcznie uzupełnić. Dzięki SLS po zakończeniu tej czynności można płynnie przełączyć maszynę w tryb pracy na pełnych obrotach.
Bezpieczne zmniejszenie prędkości ułatwia również konserwację m.in. przenośników. Oprócz ochrony ludzi funkcja ta jest wykorzystywana także do zabezpieczania maszyn przed uszkodzeniem w wyniku przekroczenia ich granicznych parametrów pracy. Innym przykładem jest dostosowanie prędkości obrotowej do rodzaju narzędzia używanego w danym momencie.
Rozszerzeniem SLS jest funkcja bezpiecznego zakresu prędkości. W jej wypadku wykrywany jest również spadek szybkości silnika poniżej minimalnej wartości granicznej. Z kolei funkcja SDI monitoruje kierunek obrotów wału silnika i jest przydatna wtedy, gdy wymagany jest ruch tylko w jedną stronę.
Podobnie jak SLS umożliwia ona operatorom bezpieczny dostęp do strefy zabronionej w czasie pracy maszyny. Przykładowe jej zastosowanie to blokada drzwi osłonowych maszyny w czasie, gdy kierunek obrotów ma zwrot w stronę obsługi. Funkcja SBC umożliwia z kolei sterowanie zewnętrznym hamulcem. Zwykle jest aktywowana razem z funkcją STO (rys. 5).
BEZPIECZEŃSTWO W NAPĘDACH ELEKTRYCZNYCH W PRAKTYCE
Komponentem układów napędowych PDS(SR) jest przemiennik częstotliwości SR (Safety-Related). Urządzenie to pozwala realizować jedną lub więcej funkcji bezpieczeństwa. Można go przykładowo wykorzystać w połączeniu z modułem bezpieczeństwa i innymi, dodatkowymi komponentami (czujnikami, przekaźnikami, stycznikami, obwodami blokad, itp.).
Obecnie jednak coraz częściej funkcje zdefiniowane w PN-EN 61800-5-2 są integrowane bezpośrednio w falowniku. Takie rozwiązanie ma z pewnością wiele zalet. Im więcej elementów wchodzi w skład systemu bezpieczeństwa maszyny, tym większy jest stopień jego komplikacji i zawodności oraz koszty.
Na te ostatnie składają się wydatki na sam sprzęt oraz na okablowanie, którym przesyłane będą sygnały z czujników oraz te sterujące elementami wykonawczymi. Połączenie i skonfigurowanie wielu urządzeń, tak by ze sobą współpracowały, może zająć sporo czasu na etapie budowy, jak i później podczas napraw, konserwacji lub rozbudowy systemu.
Integracja funkcji bezpieczeństwa w jednym urządzeniu zapewnia ponadto oszczędność miejsca, co ma wpływ na rozmiary całej maszyny. Poniżej przedstawiono przykład realizacji bezpiecznego wyłączenia momentu silnika z wykorzystaniem komponentów elektromechanicznych oraz w sposób zintegrowany. STO jest funkcją elementarną i najczęściej wbudowywaną w przemienniki częstotliwości.
PRZYKŁAD - STO
Do realizacji funkcji bezpiecznego wyłączenia momentu silnika można użyć rozłącznika bezpieczeństwa, który odłączy napęd od źródła napięcia (rys. 6a) lub przekaźnika, który steruje stycznikiem odcinającym zasilanie od napędu lub bezpośrednio od silnika. Stycznik można bowiem zainstalować na wejściu (rys. 6b) lub na wyjściu (rys. 6c) przemiennika częstotliwości.
Każda z tych konfiguracji ma zalety oraz wady wynikające ze specyfiki konstrukcji zarówno styczników, jak i samych falowników. Jeżeli to ostatnie nie zostanie uwzględnione, nie można mieć pewności, że zabezpieczenie będzie niezawodne. Umieszczając stycznik na wyjściu przemiennika, należy pamiętać, że z reguły styczniki te są przystosowane do odcinania prądu o częstotliwości 50 lub 60 Hz.
Tymczasem częstotliwość prądu wyjściowego przemiennika w zależności od aktualnej prędkości silnika może się zmieniać w bardzo szerokim zakresie. Jeżeli w momencie otwarcia stycznika będzie ona zbyt mała, na stykach może wystąpić zjawisko łuku elektrycznego. To z kolei może wywołać pożar lub spowodować stopienie, a w efekcie trwałe złączenie się styków. Z tego powodu łącznik ten nie będzie dłużej spełniał swojej funkcji.
ŚRODKI ZARADCZE
Dlatego zanim stycznik zostanie przełączony, przez wyjście falownika nie powinien już płynąć prąd. Można to uzyskać, korzystając z przemienników wyposażonych w wejście sterujące, które blokuje przepływ prądu przez to urządzenie. Instalując stycznik na wejściu przemiennika można uniknąć zjawiska łuku elektrycznego.
Wówczas jednak należy się liczyć z wolniejszym restartem silnika, na którego wydłużenie wpływ ma obecność obwodu DC na wejściu tego urządzenia. Realizując funkcję STO z użyciem komponentów elektromechanicznych, trzeba również uwzględnić możliwość ich niezadziałania, na przykład w wyniku zużycia się styków (mechanicznego lub elektrycznego).
Aby zapobiec takiej sytuacji, zwykle w obwodzie bezpieczeństwa montowane są nadmiarowe komponenty, na przykład dwa szeregowo połączone styczniki jak na rysunku 7. Stan obu tych urządzeń powinien być monitorowany przez przekaźnik, tak by w razie awarii jednego ze styczników drugi na czas odłączył silnik od zasilania.
|
STO ZINTEGROWANE
Na rysunku 8 przedstawiono uproszczony schemat przemiennika częstotliwości. Stopień wyjściowy tego urządzenia stanowią trzy pary tranzystorów IGBT wykorzystywane do wytworzenia trójfazowego napięcia przemiennego zasilającego silnik. Częścią falownika jest również układ sterowania przełączaniem tranzystorów.
W najprostszym przypadku powinien on zapewnić stały stosunek wartości i częstotliwości napięcia wyjściowego, a w rezultacie niezmienny moment obrotowy silnika. Aby zrealizować funkcję bezpiecznego wyłączenia momentu, należy zablokować dopływ impulsów sterujących tranzystorami. Uproszczony schemat takiego zabezpieczenia zamieszczono na rysunku 9.
W tym przypadku po aktywowaniu funkcji STO odłączane jest zasilanie modułu sterownika oraz optoizolatora, za pośrednictwem którego przesyłane są sygnały sterujące z kontrolera do tranzystorów falownika.
Należy pamiętać, że bezpieczne wyłączanie momentu zintegrowane w falowniku tylko w oparciu o komponenty półprzewodnikowe nie zapewnia ochrony przed porażeniem elektrycznym. Czynności naprawcze lub konserwacyjne w silniku lub napędzie można zatem rozpocząć dopiero po odłączeniu napędu od zasilania.
Monika Jaworowska