Przykład rozproszonego systemu sterowania (Distributed Control System) przedstawiono na rysunku 1. Z głównego serwera magistralą systemową do stacji operatorskich oraz rozproszonych stacji procesowych przesyłane są w nim informacje niezbędne do realizacji funkcji nadzoru i sterowania. Poszczególne kontrolery sterują elementami wykonawczymi i przetwarzają wyniki pomiarów z czujników i innych elementów.
System obejmuje przy tym stacje procesowe różnych typów. Wśród nich znajduje się przykładowo: sterownik PLC, procesowy, sterownik maszyny oraz regulator z pojedynczą pętlą. Ten ostatni komunikuje się z sensorami oraz z elementami wykonawczymi przez połączenie punkt-punkt, natomiast pozostałe korzystają w tym celu z sieci polowych (fieldbus), takich ja na przykład Profibus.
DECYDUJE SPECYFIKA PRODUKCJI
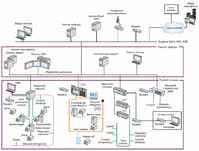
Rys. 1. Przykład rozproszonego systemu sterowania
Konkurencją dla DCS-ów są przede wszystkim systemy sterowania zbudowane w oparciu na połączeniach PLC/SCADA. Jedne i drugie mogą na przykład: przetwarzać sygnały w czasie rzeczywistym, gromadzić dane historyczne, zapewnia redundancję układów I/O. Obydwa rodzaje systemów są też zwykle skalowalne, mają zaimplementowane funkcje autodiagnostyki oraz są kompatybilne z różnymi standardami sieciowymi. Zatem jaki system sterowania lepiej wybrać - DCS czy PLC/SCADA?
Odpowiedzi na te pytania przybliża publikacja "DCS or PLC? Seven questions to help you select the best solution", którą opublikowała firma Siemens. Zebrano tam kilka pytań, na które należy odpowiedzieć przed podjęciem ostatecznej decyzji. Podstawowe z nich dotyczy rodzaju produkcji. Przyjmuje się, że systemy sterowania PLC/SCADA, które w latach 60. ubiegłego wieku zastąpiły przekaźniki elektromechaniczne, są przeznaczone dla tej dyskretnej, natomiast DCS-y, projektowane od lat 70. pod kątem wymagań regulacji ciągłej, dla produkcji procesowej.
Produktem tej pierwszej są "rzeczy", z których da się wyodrębnić części składowe wytwarzane w ciągu operacji, które wymagają szybkiego sterowania cyfrowego. Produkcja procesowa polega z kolei na przetwarzaniu surowców, w wyniku reakcji chemicznych albo oddziaływania fizycznego, w "wyroby", których składników nie można później odtworzyć. Procesy te zachodzą zwykle wolno i wymagają regulacji analogowej. Taki podział aplikacji nie jest oczywiście sztywny. Na przykład procesami wsadowymi o prostych oraz rzadko zmienianych recepturach da się równie efektywnie sterować za pomocą każdego z systemów.
DCS A PLC/SCADA
DCS to zwykle system specjalizowany pod kątem konkretnego obiektu sterowania, przez co jest droższy niż ten bazujący na sterownikach PLC. Jednocześnie w ten pierwszy inwestuje się w tych gałęziach przemysłu, w których koszty spowodowane przestojami, stratami surowców oraz uszkodzeniami maszyn są duże. Takimi są przykładowo branża chemiczna i petrochemiczna, farmaceutyczna, naftowa oraz spożywcza i energetyczna.
Z drugiej strony modyfikowanie rozproszonego systemu sterowania jest trudne, w przeciwieństwie do instalacji bazującej na klasycznych sterownikach PLC, kontrolerach PAC i pracującej pod kontrolą oprogramowania SCADA, które jest bardziej elastyczne i uniwersalne. Dzięki temu łatwo można to drugie dostosować do potrzeb różnych zadań sterowania. Warto się na nie zdecydować również wówczas, gdy redundancja nie jest opłacalna.
Oba rozwiązania różnią się ponadto w zakresie roli operatora. Po zaprogramowaniu PLC zadaniem tego ostatniego jest przede wszystkim nadzór i reagowanie na zdarzenia nieprzewidziane. Od obsługi rozproszonego systemu sterowania oczekuje się natomiast większego zaangażowania w zadanie sterowania. Konieczna jest m.in. dobra znajomość charakterystyki kontrolowanego procesu, która pozwoli na konfigurowanie DCS-a w trybie online.
Zdarza się, że dany obiekt sterowania wymaga hybrydowego systemu sterowania, wówczas warto rozważyć zakup wspomnianego kontrolera PAC (patrz ramka). Wybierając konkretny DCS, jego możliwości trzeba przeanalizować pod kątem wymagań obiektu sterowania. Na przykład do rozległości tego ostatniego i stopnia skomplikowania kontrolowanych procesów należy dostosować liczbę modułów I/O, sterowników, stacji operatorskich oraz stacji inżynierskich.
Rynek w liczbach
Dzięki postępującej industrializacji rozwijających się regionów Azji i Pacyfiku rynek nowo instalowanych DCS-ów właśnie tam będzie się rozwijał najdynamiczniej. Z kolei w Europie oraz w Ameryce Północnej, gdzie większość rozproszonych systemów sterowania została zainstalowana w latach 80. i 90. ubiegłego wieku, częściej będą przeprowadzane ich migracje. |
WYBÓR SYSTEMU - NA CO ZWRÓCIĆ UWAGĘ?
W wypadku tych pierwszych, za pośrednictwem których dane z czujników są przesyłane do kontrolerów, warto zwrócić uwagę na cechy ułatwiające ich instalację i użytkowanie. Są to m.in.: modułowość, możliwość podłączania oraz odłączania hot-swap, opcja zdalnej konfiguracji programowej, w tym konfiguracji online, funkcjonalność w zakresie diagnostyki i sygnalizacji awarii oraz różnorodność typów wejść i wyjść (cyfrowe, analogowe, rezystancyjne, termoparowe, itp.).
Istotny jest także sposób instalacji modułów I/O. Stosuje się w tym zakresie dwa podejścia: zdalne (remote, distributed) i lokalne. W tym pierwszym moduły I/O są instalowane w pobliżu urządzeń polowych, natomiast ze sterownikiem komunikują się za pośrednictwem kabla, przeważnie światłowodowego, o znacznej długości (liczonej nawet w kilometrach). Dzięki temu kable łączące układy I/O z elementami wykonawczymi i czujnikami są krótsze.
Im większa jest liczba urządzeń polowych, tym większe dzięki temu uzyskuje się oszczędności miejsca oraz w wydatkach na okablowanie. Mniejsze jest też prawdopodobieństwo awarii w wyniku uszkodzenia tego ostatniego. Lokalne moduły I/O sprawdzają się natomiast w mniejszych instalacjach. Moduły wejść i wyjść, które będą pracować w niekorzystnych warunkach otoczenia, powinny być ponadto odporne na wstrząsy, skrajne temperatury, czynniki korozyjne oraz te powodujące zapłon albo wybuch.
Ważne cechy kontrolerów to z kolei m.in.: modułowość, skalowalność, moc obliczeniowa, szybkość przetwarzania (czas cyklu), możliwości komunikacji, zaimplementowane algorytmy sterowania - oprócz podstawowych, jak PID, także te zaawansowane, na przykład sterowanie rozmyte (fuzzy logic), oraz opcja pracy równoległej i współpracy z modułami I/O lokalnymi, jak i tymi rozproszonymi.
PAC - opcja pośrednia
PAC bowiem równie dobrze sprawdzają się w sterowaniu dyskretnym, ciągłym, ruchem, jak i napędami, korzystają z jednej, wspólnej bazy tagów, charakteryzuje je otwarta i modułowa architektura oraz moc obliczeniowa PC. Można je ponadto programować w językach zdefiniowanych w standardzie IEC 61131-3. Więcej informacji o programowalnych sterownikach automatyki można znaleźć w numerze APA z września w 2012 roku w artykule "PAC rewolucjonizują systemy sterowania". |
STACJE OPERATORSKIE I INŻYNIERSKIE
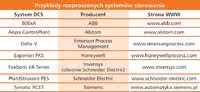
Przykłady rozproszonych systemów sterowania
Jeżeli chodzi o stacje operatorskie, za pośrednictwem których personel śledzi, kontroluje i wprowadza nastawy dla procesu, liczą się przede wszystkim: modułowość oraz skalowalność, opcja pracy jednostanowiskowej (tzn. połączenia stacji wprost z magistralą systemową) i wielostanowiskowej (czyli w konfiguracji typu klient-serwer), ergonomia i czytelność danych oraz możliwość przełączania między różnymi wersjami językowymi. Na efektywność nadzoru nad procesem ma również wpływ sposób zarządzania alarmami.
Ważne jest, żeby w sytuacjach krytycznych, jak i tych prawidłowych, ale wymagających większej uwagi, jak na przykład serwisowanie instalacji, operatora nie przytłaczał nadmiar informacji. Aby tego uniknąć, alarmy klasyfikuje się według ważności, która determinuje kolejność ich prezentowania, i decyduje o tym, czy będą otwarcie prezentowane od razu, czy po pewnym czasie, czy też zostaną zapisane w archiwum w ogóle bez wyświetlania.
W wypadku stacji inżynierskich, za pośrednictwem których DCS jest zarządzany, kluczowe jest oprogramowanie. Niezbędne są narzędzia m.in. do: konfiguracji i diagnostyki sprzętowej oraz sieciowej, implementacji algorytmów sterowania i doboru nastaw regulatorów, przygotowywania wizualizacji, zarządzania projektami i dokumentacją.
Do zakupu rozproszonego systemu sterowania konkretnego dostawcy zachęcać może także obecność w jego ofercie rozwiązań uzupełniających podstawową funkcjonalność DCS-a (m.in. pakietów do sterowania procesami wsadowymi, transportem, pakowaniem lub innymi zadaniami specyficznymi dla danej branży, ułatwienia w zakresie serwisu i nadzoru nad utrzymaniem ruchu) oraz urządzeń polowych (czujników, regulatorów, itp.) "kompatybilnych" z konkretnym DCS-em. Ważną kwestią jest również redundancja komponentów rozproszonego systemu sterowania.