CZĘŚĆ 2. AUTOMATYZACJA MALOWANIA
W porównaniu z malowaniem ręcznym, w którym operator obsługuje pistolet do natrysku, malując automatycznie, uzyskuje się wiele korzyści. Najważniejsze z nich to: większa wydajność i powtarzalność. Ta ostatnia odnosi się m.in. do grubości powłoki i liczby warstw, z jakiej się ona składa.
To przekłada się na lepszą jakość pokrycia, jej porównywalność między kolejnymi egzemplarzami i na efektywniejsze wykorzystanie farb. Ponadto stanowiska zautomatyzowane można odizolować od otoczenia. To poprawia bezpieczeństwo personelu. Łatwiejsze jest też wtedy kontrolowanie wpływu tego procesu na środowisko i otoczenia na jego przebieg. Sprawniej się je czyści i przestraja, na przykład zmieniając kolor, wzór lub dostosowując parametry natrysku do gabarytów obiektu.
Wybierając rodzaj farby, grubość powłoki i sposób przygotowania powierzchni do pomalowania, należy przeanalizować warunki jej użytkowania, które mogą sprzyjać korozji bądź przyspieszać jej rozwój. Istotne są: wilgotność i temperatura otoczenia, nasłonecznienie, środki chemiczne oraz możliwe oddziaływania mechaniczne (ścieranie, uderzenia, itp.). W wypadku obiektów, które zostaną zakopane, liczy się m.in. stopień zawilgocenia i pH gleby, a tych zanurzonych - skład chemiczny wody. Poniższe przykłady pokazują, że nie wszystko jednak da się przewidzieć. Case study: Kolor ma znaczenie
Okazało się, że odwarstwienie farby najsilniejsze było na dachu zbiorników. Ściany, z których także się ona złuszczała (choć w mniejszym stopniu), były skierowane na południe. Ponadto części dachu całkowicie zacienione zachowały powłokę praktycznie w nienaruszonym stanie, a te przysłaniane czasowo uległy tylko lekkiemu naruszeniu. Oprócz tego zauważono, że farba złuszczała się tylko z tych zbiorników, które zostały pomalowane na ciemnoniebieski kolor. Pozostałe, do pomalowania których użyto jasnoszarej farby, zachowały dobry stan pokrycia. Ostatecznie stwierdzono, że złuszczanie się powłok malarskich było efektem ich słabej odporności na silne nasłonecznienie, jakie występuje w rejonie, gdzie mieści się zakład. Nierównomierność z kolei była spowodowana tym, że promieniowanie UV w większym stopniu jest pochłaniane przez powłokę o ciemniejszym kolorze oraz obszary niezacienione. Konieczne okazało się zatem ponowne przemalowanie kontenerów, tym razem farbą o odpowiednich właściwościach i kolorze. Case study: Kłopotliwe sąsiedztwo
Ekipa specjalistów zatrudniona w celu wykrycia przyczyny niszczenia powłoki przeprowadziła jej kompleksowe badania. Najpierw zmierzono grubość farby i wykonano dokumentację fotograficzną. Następnie pobrano próbki złuszczeń powłoki. Kolejnym krokiem było wykonanie ich spektroskopii. Dzięki niej ustalono skład chemiczny powłoki. Wykryto także cząstki siarki i chloru, które nie były składnikiem ani żywicy, ani pigmentów, ani wypełniaczy farby oraz resztki sadzy. Dla formalności próbki przebadano jeszcze pod mikroskopem, ale nie wykryto w nich żadnych defektów, takich jak pęcherze. Na podstawie analizy zgromadzonych wyników badań eksperci orzekli, że farby, których użyto do pomalowania zbiornika i rur, okazały się nieodporne na połączenie wilgoci silnie obecnej lokalnie z zanieczyszczeniami emitowanymi - jak zresztą sprawdzono całkowicie zgodnie z obowiązującymi normami emisji - przez sąsiednią elektrownię. W rezultacie siarka i chlor przenikały przez powłokę i korodowały metalowe podłoże, co z kolei prowadziło do odwarstwiania się farby. Jako środek zaradczy eksperci zalecili inne, odporniejsze farby do pokrycia zbiornika i rurociągów. Konieczne było też ich dokładne oczyszczenie z rdzy i resztek wadliwej powłoki. |
JAK JEST ZBUDOWANY AUTOMAT DO MALOWANIA?
Częścią wyposażenia zautomatyzowanego stanowiska malarskiego są sprzęty do nakładania farby. Na przykład w automatach do malowania proszkowego są to: zbiornik z proszkiem, pompa do jego transportu, pistolet natryskowy wyposażony w mechanizm elektryzowania cząstek farby oraz piec do utwardzania powłok. Urządzenia do aplikacji (oprócz pieca) znajdują się kabinie do napylania. To pomieszczenie jest zwykle wykonane z przezroczystego tworzywa sztucznego.
Materiał ten jest preferowany ze względu na łatwość jego czyszczenia z resztek proszków. Obiekt malowania wprowadza się do kabiny na przenośniku. Częścią stanowiska jest również zsyp, który łączy się z systemem do odzyskiwania proszku farby niewykorzystanej w danym cyklu malowania. Bardziej zaawansowane, a przez to droższe, automaty do napylania są wyposażane w instalacje do automatycznego czyszczenia.
CZYSZCZENIE ZAUTOMATYZOWANE PO ZMIANIE KOLORU
Mycie automatu malarskiego powinno być szybkie oraz dokładne. Ta pierwsza cecha wpływa na wydajność procesu i możliwość integracji stanowiska z linią produkcyjną, z którą musi być ono zsynchronizowane. Dokładność czyszczenia kabiny z pozostałości farb jest z kolei bardzo ważna przy zmianie koloru. Zyskując pewność, że w zakamarkach nie ma już jej resztek, od pierwszego egzemplarza wprowadzonego do boksu po zmianie koloru można zacząć malowanie "na czysto", zamiast tego z przeznaczeniem "na straty".
Mycie zautomatyzowane przebiega etapowo. Najpierw sprzęt do aplikacji zostaje przedmuchany, po czym wyprowadza się go z kabiny. Wówczas do jej wnętrza wjeżdża aparat czyszczący. Jest to zwykle rama z dyszami powietrznymi i myjkami. Te pierwsze przesuwają się wzdłuż ścian boksu, zdmuchując z nich pozostałości proszku, które spadają do zsypu. Boki kabiny przeciera się wtedy zwilżonymi myjkami. Równocześnie czyszczona jest instalacja odzysku drobin farby.
ROBOTY MALARSKIE
Alternatywą dla automatów malarskich są stanowiska zrobotyzowane.
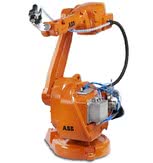
Robot malarski IRB 52. Najważniejsze cechy: zasięg: 1,2 m, udźwig: 7 kg, liczba osi: 6, stopień ochrony: IP 67. Dostępny w dwóch wersjach: IRB 52 / 1.2 (dolne ramię 1,2 m) oraz IRB 52 / 1.45 (dolne ramię 1,45 m).
Na przykład jednym z częstszych defektów są krople farby zastygłe na powierzchni przedmiotu, w wyniku niedokładnej atomizacji farby. Ta z kolei jest skutkiem m.in. zabrudzenia dyszy pistoletu do natrysku, częściowego przytkania się przewodu, którym doprowadzana jest farba albo zbyt niskiego ciśnienia powietrza rozpylającego.
Zacieki są natomiast przeważnie wynikiem nałożenia zbyt dużej ilości farby. Przyczyn tego może być wiele. Sprawdzić należy, czy szybkość aplikacji, rozmiar dyszy, jej odległość od obiektu, kąt aplikacji i orientacja przedmiotu są odpowiednie.
Pęknięcia
Główną przyczyną niejednolitej koloryzacji powierzchni, pojawienia się na niej niepożądanego wzoru i różnic w kolorach różnych obiektów malowanych w jednej serii jest nierównomierne zakrycie podłoża. Przykładem niedoskonałości są też pęknięcia.
Pojawiają się one wówczas, gdy dwa materiały połączone ze sobą rozszerzają się albo kurczą z różną prędkością, a siły temu towarzyszące są większe niż te, które je scalają. Pęknięcia mogą występować pomiędzy podłożem a podkładem lub podkładem a warstwą farby albo pomiędzy farbą a lakierem. Przyczyną kurczenia się i rozszerzania materiałów są wahania temperatury. Inne częste problemy to: pęcherze, złuszczanie oraz tzw. pomarańczowa skórka.
Unikaj zabrudzeń!
Pierwsze powstają, kiedy obce materiały, które dostaną się pod farbę, odparowują podczas dalszej obróbki powierzchni. Pękając, tworzą one mikrokratery. Z kolei gdy farba nie przylega do podłoża z powodu jego nieprawidłowego przygotowania, złuszcza się.
Skórka pomarańczowa jest skutkiem niedostatecznego rozpłynięcia się farby z powodu niedopasowania właściwości jej i podłoża albo niewłaściwego ułożenia przedmiotu podczas aplikacji. Pamiętać także trzeba, że wiele skaz jest wynikiem zanieczyszczenia malowanej powierzchni albo farby. Zabrudzenia mogą oprócz tego powstawać podczas nakładania powłoki. Na szczęście brud jest widoczny.
Kontrola klimatu malowania
Dokładna inspekcja pozwala zatem zazwyczaj wykryć, na jakim etapie się on pojawia. Wówczas można podjąć odpowiednie kroki, by go wyeliminować. Oprócz brudu na powierzchni skrapla się wilgoć z otoczenia.
To zjawisko zachodzi wtedy, kiedy wilgotność względna otoczenia jest bardzo wysoka lub kiedy temperatura powierzchni jest niższa od temperatury punktu rosy. Na jakość aplikacji ma wpływ także temperatura. W niskiej lepkość farby rośnie, przez co trzeba ją bardziej rozcieńczyć. Zbyt wysoka sprzyja natomiast powstawaniu skórki pomarańczowej, kiedy powłoka wysycha zbyt szybko, blokując odparowanie rozpuszczalnika.
BEZKONTAKTOWY POMIAR GRUBOŚCI POWŁOKI
Czujnik prądów wirowych jest tak zbudowany, aby umieszczony nad nim sensor laserowy również miał dostęp do powierzchni mierzonej. Przedstawiono to na rysunku 1. Grubość powłoki malarskiej jest obliczana jako różnica pomiędzy odległością do podłoża mierzoną przez czujnik prądów wirowych a odległością od pomalowanej powierzchni, którą wyznacza sensor laserowy.
Połączenie obu typów czujników ma wiele zalet. Korzystając z nich, można monitorować grubość powłoki na bieżąco, jeszcze w trakcie jej nakładania. Nie jest to wykonalne przy użyciu wyłącznie samego sensora prądów wirowych. Przede wszystkim należałoby wtedy czekać, aż farba wyschnie. Nie jest to efektywne, bowiem wiąże się z koniecznością wstrzymania malowania kolejnych egzemplarzy, gdy jeden wymaga poprawki. Ponadto wówczas należałoby czujnik umieścić bezpośrednio na obiekcie. Ten z kolei mógłby uszkodzić świeżo naniesioną powłokę.
Na zakończenie na przykładzie wyjaśniamy, jak można sobie poradzić z ubocznymi i równocześnie uciążliwymi produktami malowania.
JAK SIĘ POZBYĆ ROZPUSZCZALNIKÓW?
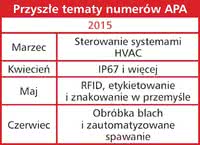
Przyszłe tematy numerów APA
W metodach poza malowaniem proszkowym poważnym problemem są rozpuszczalniki zawarte w farbach w płynie. Są to bowiem substancje groźne dla ludzi i dla środowiska. Ich bezpieczne, a zarazem tanie usunięcie powinno być, w związku z koniecznością spełnienia norm środowiskowych i redukcji kosztów operacyjnych, uwzględnione w projekcie automatu malarskiego albo stanowiska zrobotyzowanego.
Przykładowym rozwiązaniem jest oczyszczanie powietrza w obiegu zamkniętym. Najpierw należy doprowadzić do stanu jego nasycenia oparami rozpuszczalników. Realizuje się to, dodając niewielką ilość czystego powietrza albo usuwając ją z kabiny, w zależności od stale monitorowanego stężenia par tych szkodliwych substancji. Następnie taką mieszankę przepompowuje się do komory, w której podgrzewa się ją do odpowiednio wysokiej temperatury (typowo kilkuset °C). Powietrze nasycone rozpuszczalnikiem jest dalej pompowane do komory, w której ulega on samospaleniu. Oczyszczone powietrze, nim trafi z powrotem do kabiny malarskiej, jest schładzane.
Monika Jaworowska
W artykule wykorzystano materiały firm: Tikkurila, Tensor Consulting i Kuka.