CZĘŚĆ 1 - PRODUKCJA SZKŁA
Szkło to materiał bezpostaciowy. Pod względem właściwości, z powodu braku uporządkowania struktury przestrzennej, przypomina ono ciecz, z kolei sztywność oraz kruchość upodabniają je do ciał stałych. Szkło powstaje w wyniku przechłodzenia stopionych surowców, bez ich krystalizacji.
GDZIE I JAK WYTAPIA SIĘ SZKŁO?
Pierwszy etap produkcji wyrobów ze szkła to stopienie zestawu szklarskiego w piecu, w produkcji ciągłej w wannowo-zmianowym (wannie szklarskiej, wannie topliwej), zaś w produkcji okresowej - w donicowym. Centralne miejsce pieców pierwszego rodzaju to wanna. Na jednym z jej końców znajduje się kieszeń zasypowa, przez którą podawany jest zestaw szklarski. W miarę jego przerabiania ubytki uzupełnia się nowymi porcjami surowców.
Po ogrzaniu płomieniami z palników te ostatnie ulegają stopieniu. Powstała w ten sposób masa szklana stopniowo wypełnia całą wannę. Przepływając w przeciwległy koniec wanny, szkło jest klarowane.
Pod wpływem wysokiej temperatury oraz ruchów konwekcyjnych masa zostaje wymieszana. Usuwane są z niej również pęcherzyki gazów, efekt reakcji chemicznych zachodzących podczas topienia się składników zestawu szklarskiego. Potem szkło jest schładzane.
Temperatura w wannie jest zmieniana stosownie do potrzeb, od najwyższej w sekcji klarowania, do coraz niższej, tuż przed formowaniem gotowych wyrobów. Piece wannowe opala się gazem ziemnym, olejem opałowym albo gazem generatorowym.
Powietrze mieszane z paliwem zastępuje się coraz częściej czystym tlenem. Poprawia to efektywność energetyczną pieca i zmniejsza ilość szkodliwych związków emitowanych do atmosfery. Tę pierwszą polepsza również system odzysku ciepła ze spalin.
Z czego produkuje się szkło?
Połączenie tych związków jest rozpuszczalne w wodzie. Żeby to zmienić, dodaje się stabilizator - tę funkcję spełnia z kolei węglan wapnia. Do mieszanki, tzw. zestawu szklarskiego, dodaje się również substancje, które usuwają z masy szklanej pęcherzyki powietrza (środki klarujące). Przykładami substancji o takich właściwościach są: siarczan sodu, arszenik i saletra. Kolejny składnik zestawu szklarskiego to stłuczka szklana pozyskiwana z wyrobów szklanych poddanych recyklingowi. Dzięki niej zmniejsza się ilość emitowanych zanieczyszczeń i koszty produkcji. Na to ostatnie wpływa ograniczenie ilości zużywanej energii (do stopienia stłuczki potrzeba mniej ciepła) i pozostałych surowców. Do zestawu szklarskiego dodaje się poza tym substancje nadające szkłu specjalne właściwości. Na przykład tlenek glinu poprawia jego odporność chemiczną, tlenki ołowiu zwiększają współczynnik załamania światła, zaś tlenek boru zmniejsza współczynnik rozszerzalności. Aby wyprodukować szkło matowe (mleczne), używa się związków fluoru. Z kolei dodatek miedzi zabarwi je na kolor jasnoniebieski, chromu - zielony albo żółty, manganu - fioletowy, kobaltu - niebieski lub zielony, a selenu na różowy. |
JAK POWSTAJĄ SZYBY?
Końcowa część wanny szklarskiej stanowi wyprowadzenie masy szkła do kolejnego etapu jej przetwarzania - formowania. Sposób realizacji tego zadania zależy od rodzaju produktu końcowego - inaczej przebiega w przypadku szkła płaskiego, a inaczej produkuje się butelki.
Jedną z technik wytwarzania szkła płaskiego jest metoda float. Korzysta się w niej z dwóch, połączonych ze sobą wanien. W pierwszym zbiorniku topi się surowce, z kolei drugi, który jest płytszy, wypełnia się roztopioną cyną. Stanowi ona podłoże, po którym rozlewa się masa szklana, która wypływa z pierwszej wanny.
W ten sposób powstaje tafla. Jej grubość reguluje się przez zmianę szybkości, z jaką masa szklana wpływa do drugiego zbiornika. Szkło utrzymuje się na powierzchni cyny, ponieważ gęstość tego materiału jest kilka razy mniejsza niż gęstość metalu. W związku z tym, że cyna się utlenia, w otoczeniu drugiej wanny trzeba wytworzyć, a potem utrzymać atmosferę o składzie chemicznym, który zapobiegnie postępowi tego procesu. W tym celu używa się mieszanki azotu z wodorem. Gotowe tafle szklane rozcina się na mniejsze, korzystając z różnych narządzi i maszyn, m.in. laserów (patrz ramka).
W przypadku butelek masa szklana z wanny topliwej wypływa przez specjalne kanały (tzw. zasilacze). Stamtąd wprowadza się ją do automatów do formowania opakowań, wcześniej rozdzielając ją na porcje (krople). Są to maszyny specjalistyczne, których działanie jest wzorowane na pracy hutników wydmuchujących szklane przedmioty.
MASZYNY SPECJALISTYCZNE DO PRODUKCJI BUTELEK SZKLANYCH
W zależności od rodzaju butelek, tzn. grubości ich ścian i rozmiaru otworów, stosuje się różne techniki produkcji. Na przykład butelki o grubych ściankach i wąskich otworach wytwarza się metodą blow and blow.
Jest to proces dwuetapowy - w pierwszej kolejności w porcji szkła wyrabia się otwór i wydmuchuje z niego bańkę. Następnie przekłada się ją do formy w kształcie wyrobu gotowego i znów wydmuchuje, tym razem właściwy, kształt.
Butelki z cienkimi ściankami, wykonywane metodą press and blow, też produkuje się w dwóch krokach. W pierwszym bańkę wyrabia się przez sprasowanie środka masy szklanej za pomocą tłoka. Wtedy wykonuje się też wylot butelki. W drugim kroku bańkę przenosi się do formy końcowej i wydmuchuje się gotowy wyrób.
Gdy butelka uzyska ostateczny kształt, jest schładzana do temperatury poniżej temperatury deformacji. Następnym etapem jest odprężanie, polegające na powolnym studzeniu szkła w celu relaksacji naprężeń termicznych. Dalsze etapy obróbki zależą już od specyfiki produktu - butelki znakuje się albo zdobi.
Jak wykryć uszkodzenia szklanej butelki?![]() Układ inspekcji szklanych opakowań
|
PO CO MIERZYĆ TEMPERATURĘ SKLEPIENIA PIECA?
Warunki, jakie panują w wannie szklarskiej i zasilaczach, mają wpływ na właściwości szklanych wyrobów i efektywność ich produkcji. W związku z tym jednocześnie mierzyć powinno się wiele różnych wielkości - kluczową jest temperatura. Mierzy się ją w różnych miejscach pieca szklarskiego. Przykładowe lokalizacje czujników tej wielkości to: sklepienie wanny, sklepienia regeneratorów, dno wanny, dół regeneratorów i zasilacze.
Temperatura sklepienia pieca musi być kontrolowana z kilku powodów. Utrzymanie tej właściwej ma na przykład wpływ na żywotność pieca, jego przegrzanie przyspiesza bowiem erozję ogniotrwałego wyłożenia. Za niska temperatura ma natomiast znaczenie dla efektywności topienia surowców oraz zużycia paliwa. Analogiczne przesłanki skłaniają do mierzenia tej wielkości na dnie wanny.
Do pomiaru temperatury w sklepieniach oraz na dnach części pieców szklarskich wykorzystuje się na przykład termopary. Czujniki te są także używane do kontroli temperatury masy szklanej w zasilaczach. Ponadto w tym celu korzysta się z pirometrów.
POMIARY I STEROWANIE W PRODUKCJI SZKŁA
W piecach szklarskich mierzy się również takie wielkości jak: ciśnienie, poziom i przepływ. Ciśnienie i przepływ należy kontrolować na przykład w przypadku paliwa (gazu) oraz powietrza. Ciśnienie powinno się także mierzyć w przestrzeni ogniowej pieca i w kanałach spalinowych. Dzięki temu można przykładowo sprawdzić szczelność pieca. Ważną wielkością jest oprócz tego poziom masy szklanej.
Na podstawie informacji z systemu pomiarowego kontroluje się elementy wykonawcze. Na przykład zaworami, które dozują paliwo i powietrze do palników, steruje się w oparciu o odczyty temperatury, z kolei automatami, które ładują surowce do wanny - na podstawie zmian w poziomie stopionej masy szklanej.
W związku z tym, że w procesie wytopu szkła występuje wiele zaburzeń, na przykład waha się temperatura powietrza do spalania, zmienia się skład surowców oraz właściwości paliwa (kaloryczność), w sterowaniu piecami szklarskimi stosuje się m.in. algorytmy adaptacyjne. W kontroli pracy tych obiektów znajduje również zastosowanie logika rozmyta.
Ważnym etapem produkcji szklanych wyrobów jest inspekcja jakości. W czasie ich wytwarzania i obróbki w szkło mogą bowiem wnikać rozmaite zanieczyszczenia. Może też ono ulec uszkodzeniu.
Czym ciąć szkło?
Cięcie laserem Laser czy cięcie mechaniczne? |
JAKOŚĆ WYROBÓW SZKLANYCH
Do szkła płaskiego mogą przylegać drobiny cyny. Na jego powierzchni powstają zarysowania, stłuczenia i mikropęknięcia, natomiast w środku mogą utrwalać się pęcherze powietrza. Skazy powstają też na krawędziach szklanych tafli. Te poddawane dalszej obróbce, na przykład hartowaniu lub wyżarzaniu, pod wpływem dużego ciśnienia i temperatury, łatwiej wtedy pękają, zanieczyszczając piec.
Kontrola jakości jest też ważna na liniach pokrywania paneli szklanych specjalnymi powłokami. Przykładowe pokrycia wykonywane są z tlenku cynku, tlenku indowo-cynowego i innych przezroczystych przewodzących tlenków (Transparent Conductive Oxide, TCO). Materiały te są używane do produkcji m.in. paneli słonecznych, wyświetlaczy ciekłokrystalicznych i ekranów dotykowych.
Nieciągłość i nierówna grubość tych powłok mogą zaburzyć przepływ prądu i pogorszyć jakość pracy tych urządzeń. Ogniwa fotowoltaiczne pokrywa się również powłokami antyodblaskowymi, które ograniczają ilość światła odbijanego od panelu. Niedoskonałości w tych pokryciach zmniejszają sprawność konwersji promieniowania słonecznego w energię elektryczną.
KAMERY LINIJKOWE W INSPEKCJI SZKŁA
Do inspekcji długich tafli szkła transportowanych na przenośnikach używa się systemów wizyjnych z kamerami linijkowymi (linescan). Są one także popularne w kontroli jakości innych materiałów w ruchu, m.in. papieru, blach i tkanin. Zdecydowanie lepiej sprawdzają się bowiem w rejestracji ciągłego obrazu obiektów o dużej powierzchni niż kamery obrazowe (matrycowe, area-scan).
Te ostatnie zapisują wiele obrazów, które częściowo się pokrywają. Potem przetwarza się je w specjalnym oprogramowaniu, usuwając zdublowane fragmenty i zniekształcenia. Obraz w kamerze linijkowej tworzy się z kolei krokowo. Przetwornik, czyli pojedyncza linijka pikseli, rejestruje kolejne linie obrazu. W tym celu przesuwa się nad obiektem albo obiekt porusza się pod kamerą.
Aby uzyskać obraz dobrej jakości, kamery linijkowe powinno się zsynchronizować w czasie z ruchem obiektu, a skanowanie musi być równomierne. Dlatego zorganizowanie stanowiska pomiarowego może okazać się trudniejsze niż w przypadku kamer obrazowych. Za to unika się rozmazywania obrazów obiektów w ruchu, a ich obróbka linijka po linijce jest wydajniejsza.
Częścią stanowiska kontroli jakości szklanych tafli może być, oprócz systemu wizyjnego, na przykład zsynchronizowany z nim przecinak. W razie wykrycia uszkodzeń odcina on uszkodzony odcinek szkła. Odpady są gromadzone i wykorzystywane do produkcji kolejnej partii szkła jako stłuczka. W ramce przedstawiamy przykład stanowiska do inspekcji opakowań ze szkła.
CZĘŚĆ 2 - PRODUKCJA STALI
Mianem stali określa się plastycznie i cieplnie obrabialne stopy żelaza z węglem oraz innymi pierwiastkami. Proces produkcji tego materiału składa się z dwóch głównych etapów. W pierwszym, w wielkim piecu, wytwarza się surówkę żelaza. Drugim etapem jest jej utlenianie (świeżenie), które przeprowadza się w konwerterze tlenowym. W międzyczasie, jak i po świeżeniu, wykonywane są różne dodatkowe czynności, na przykład wstępne oczyszczanie surówki oraz obróbka pozapiecowa stali.
JAK PRODUKUJE SIĘ STAL?
Surówka żelaza produkowana jest z koksu oraz rudy żelaza. Najpierw drobnoziarnista ruda trafia do spiekalni, w której wytwarzany jest spiek gruboziarnisty. Równocześnie w piecu koksowniczym z węgla otrzymuje się koks. Następnie mieszankę spieku rudy żelaza z koksem ładuje się do wielkiego pieca, gdzie jest ona spalana w temperaturze kilku tysięcy stopni. Koks w tym procesie dostarcza ciepło i redukuje żelazo.
Powstała w ten sposób surówka jest przewożona w kadziach do stalowni. W tym celu wykorzystuje się m.in. kadzie, które jednocześnie pełnią funkcję mieszalnika. Są to zbiorniki o pojemności nawet kilkuset ton, o specjalnej konstrukcji, tzn. wyłożone tworzywem ogniotrwałym, z warstwą izolującą, która zapobiega stratom ciepła.
Surówka w stalowni najpierw poddawana jest wstępnemu oczyszczaniu. Dokonuje się tego w procesie odsiarczania. Realizuje się go na przykład, wprowadzając do metalu mieszankę substancji odsiarczających, m.in. wapna. Efektem tego procesu jest zbieranie się siarki na powierzchni surówki, w żużlu.
PO CO ŚWIEŻYĆ SURÓWKĘ?
Następnie żużel jest usuwany, a surówkę załadowuje się do zasadowego konwertera tlenowego. Na tym etapie produkcji dodaje się do niej złom oraz topniki. Celem świeżenia jest wypalenie, czyli utlenienie, niepożądanych zanieczyszczeń zawartych w surówce. Główne pierwiastki, które są przetwarzane w taki sposób na tlenki, to: węgiel - jego zawartość jest obniżana z około 4% do poniżej 1%, krzem, mangan, fosfor oraz siarka. Zanieczyszczenia są usuwane z gazem odlotowym lub z płynnym żużlem.
Po zakończeniu świeżenia stal jest znowu przelewana do kadzi. Aby uzyskała odpowiednie właściwości, poddawana jest dalszej obróbce (pozapiecowej). Przykładem jest odgazowanie, które przeprowadza się w komorze próżniowej.
Kolejnym etapem jest odlewanie ze stali różnych półproduktów, m.in. wlewek i kęsisk (slab). Następnie, w celu uzyskania produktu finalnego, najpierw poddaje się je walcowaniu, na gorąco lub na zimno, a potem, w zależności od potrzeb, na przykład tłoczy, ciągnie, prasuje albo wyciska.
CO POPRZEDZA WALCOWANIE?
Walcowanie polega na odkształcaniu półproduktów stalowych przez ich zgniatanie pomiędzy obracającymi się walcami. Ma ono na celu zmianę ich kształtu, na przykład wydłużenie i spłaszczenie, zmianę ich struktury, właściwości lub stanu powierzchni. Tak produkuje się m.in. blachy grube. Przed i po walcowaniu półprodukty poddaje się dodatkowej obróbce.
Pierwszym etapem walcowania na gorąco, gdy nie ma możliwości użycia gorącego wsadu, który jeszcze nie ostygł po procesie odlewania, jest jego rozgrzanie w piecu do odpowiednio wysokiej temperatury. Zwykle mieści się ona w przedziale od +1100°C do +1250°C. Dzięki ogrzaniu stali do jej odkształcania można użyć mniejszej siły. Ważne, aby półprodukty zostały ogrzane równomiernie oraz odpowiednio szybko. W strukturze materiału zachodzą wówczas mniejsze zmiany.
Kolejnym krokiem jest usunięcie ze stalowej powierzchni zgorzeliny. Jest to warstwa tlenków żelaza, które wytwarzają się samoistnie na rozgrzanym metalu po wyjęciu go z pieca. Zgorzelinę trzeba usuwać, gdyż jest krucha i nie ulega odkształceniu. W tym celu używane są zbijacze zgorzeliny. Urządzenia te pompują wodę pod dużym ciśnieniem, która odbija skorodowaną warstwę stali.
POMIARY I STEROWANIE W PRODUKCJI BLACH
Następnym stanowiskiem jest zespół walcowniczy. Składa się on, w zależności od specyfiki produktu końcowego, z kilku walcarek. Z kolei obróbka wykończeniowa blach polega na ich prostowaniu, chłodzeniu, cięciu, obróbce cieplnej i nakładaniu powłok ochronnych.
Kontrola pracy linii walcowniczej to złożone zadanie, które wymaga zintegrowanego sterowania poszczególnymi etapami tego procesu. Na przykład w przypadku pieców mierzy się temperaturę i na tej podstawie reguluje się dopływ paliwa. Działanie walcarek nadzoruje z kolei system automatycznej kontroli oraz regulacji szerokości szczeliny walcowniczej (Automatic Gauge Control, AGC).
Za pośrednictwem systemu AGC zmieniane są nastawy hydraulicznego układu regulacji położenia walców. Żeby uzyskać wymaganą grubość arkusza blachy, zadana szerokość szczeliny pomiędzy walcami powinna uwzględniać jej przyrost pod wpływem obciążenia walcarki. W tym celu mierzy się nacisk blachy na walce oraz szacuje się ich odkształcenie tym spowodowane.
Kontrolować trzeba także szybkość schładzania blachy, od niej bowiem zależą jej właściwości. Reguluje się ją na przykład, zmieniając prędkość taśmociągu, na którym przenoszone są arkusze lub włączając dodatkowe wentylatory przyspieszające schładzanie. Do pomiaru temperatury blach wykorzystywane są kamery termowizyjne.
Te ostatnie, w związku z wysokimi temperaturami występującymi w produkcji i obróbce stali oraz z kluczowym znaczeniem, jakie ma ta wielkość dla ich przebiegu, są w hutach używane powszechnie. Przykłady zastosowania termowizji w hutnictwie metali przedstawiamy w ramce.
CIĘCIE BLACH LASEREM
Blachy są następnie gięte, przecinane i spawane. Do rozcięcia materiału dochodzi wtedy, gdy siła tnąca do niego przyłożona przekracza wartość graniczną. Oddziaływanie to jest wywierane przez dwa narzędzia, nad i pod arkuszem, na przykład górne i dolne ostrze. Przeważnie drugie jest nieruchome. Pomiędzy ich krawędziami zachowuje się odstęp (5 do 10% grubości arkusza), ułatwiający rozcięcie materiału.
W cięciu blach korzysta się także z metod bezdotykowych, m.in. lasera. Jego promień jest kierowany i skupiany przez układ luster i soczewek na powierzchni arkusza. W miejscu, gdzie pada taka wiązka o dużej energii, metal topi się i odparowuje. Następnie jego pozostałości są zdmuchiwane z blachy przez strumień gazu, zazwyczaj tlenu albo azotu. Do cięcia blach zwykle używane są lasery gazowe CO2, o mocy do 2 kW. Głowica lasera może być ruchoma i przemieszczać się nad nieruchomym arkuszem albo pozostaje nieruchoma, a cięty materiał znajduje się na obrotowym stole.
Termowizja w produkcji i przetwórstwie staliKamer termowizyjnych używa się do badania temperatury powierzchni kadzi, którymi transportuje się roztopioną stal przed rozlaniem do form. Jeśli na termogramie widoczne są gorące punkty, oznacza to, że w tych miejscach wewnętrzna ogniotrwała powłoka zbiornika jest uszkodzona albo nadmiernie zużyta. W obu przypadkach możliwy jest wyciek stali. Jest on niebezpieczny dla osób, które znajdują się w pobliżu. Trzeba się również liczyć ze stratą surowca, kosztami naprawy zalanych urządzeń i wstrzymaniem produkcji na czas usuwania skutków wycieku.
Wykrywając zagrożenie wcześniej, kadź można zawrócić, a stal wlać do nieuszkodzonego zbiornika. Rejestrując obraz termiczny kadzi okresowo, można natomiast śledzić postęp jej zużycia i, w razie potrzeby, zawczasu ją wymienić. Kamerami termowizyjnymi bada się także bloki stali przed walcowaniem. Jeżeli nie są równomiernie ogrzane i na obrazie termowizyjnym widoczne są obszary zimniejsze, należy wyregulować temperaturę pieca. Przyczyną mogą być też straty ciepła w czasie przelewania stali do formy. Wówczas należy pogrubić jej ściany w miejscach widocznych na termogramie jako obszary, przez które ciepło jest tracone. |
ZALETY WYCINAREK LASEROWYCH
Lasery są używane do cięcia metali żelaznych i nieżelaznych. Najłatwiej w ten sposób tnie się materiały o małej odblaskowości i małej przewodności cieplnej, takie jak stal węglowa i nierdzewna. Te, które silnie odbijają światło i dobrze przewodzą ciepło, jak aluminium i stopy miedzi, wymagają użycia laserów o większej mocy.
Cięcie laserem jako metoda bezkontaktowa ma wiele zalet. Krawędzie są gładsze i nie potrzebują dodatkowej obróbki. Blacha odkształca się w niewielkim stopniu i jest nagrzewana w wąskim obszarze. Zaletą wycinarek laserowych jest ponadto duża precyzja.
Blachy tnie się też przy użyciu strumienia wody pod dużym ciśnieniem, czystej lub zmieszanej ze ścierniwem. Uderzając w powierzchnię metalu, powoduje ona jej erozję. Jakość krawędzi rozcięć tak wykonanych jest zadowalająca. Ponadto cięty materiał nie jest podgrzewany. Do cięcia blach używa się również plazmy (patrz: ramka).
Wstępnie ukształtowane arkusze blach łączy się, spawając je ze sobą. Polega to na ich miejscowym stopieniu i zestaleniu. Złącze wypełnia się spoiwem, które stapia się wraz z materiałem rodzimym. Wyróżnia się kilka metod spawania, m.in. gazowe i elektryczne.
JAK SPAWAĆ BLACHY?
W spawaniu gazowym źródłem ciepła jest płomień palnika powstający w wyniku spalania gazu, zazwyczaj acetylenu, rzadziej wodoru lub propanu. Do zalet tej metody zalicza się: szybkość, wydajność, możliwość łączenie zarówno blach cienkich, jak i grubych, oraz niższą cenę urządzeń niż w przypadku innych technik.
Niestety pewnych materiałów nie da się w ten sposób spawać albo jest to trudne. Problem ten dotyczy stali o wyższej zawartości węgla, odpornych na korozję oraz aluminium. Ponadto spoiny są mniej estetyczne od tych wykonanych pozostałymi metodami.
W drugiej metodzie źródłem ciepła jest łuk elektryczny. Jej odmianą jest spawanie w osłonie gazowej, na przykład metodą TIG (Tungsten Inert Gas). Łuk elektryczny wytwarza nietopliwa wolframowa elektroda w osłonie gazu obojętnego, zwykle argonu lub helu. Jego zadaniem jest ochrona roztopionego metalu przed utlenianiem.
Metoda TIG ma wiele zalet, m.in. umożliwia łączenie różnych metali w zasadzie bez ograniczeń i pozwala na scalanie cienkich blach. Oprócz tego spoina jest wysokiej jakości i nie wymaga czyszczenia. Wadą jest wolne spawanie.
Jak ciąć blachy plazmą?![]() Gaz z dyszy, przepływając przez łuk elektryczny, ulega jonizacji - strumień powstałej w ten sposób plazmy przecina materiał Osiąga ona wysoką temperaturę i uderzając w rozcinany materiał, wytapia go miejscowo, jednocześnie wydmuchując jego resztki z powstałej w ten sposób szczeliny. Plazmę wytwarza się m.in. z azotu, argonu, wodoru, tlenu lub suchego sprężonego powietrza. Wybór gazu zależy od ciętego materiału. Tlenem tnie się stal węglową i stal niskostopową o grubości maksymalnie 20 mm, a sprężonym powietrzem - cienkie blachy. Azot jest używany do cięcia na przykład stali nierdzewnej i aluminium, a mieszanina argonu z wodorem - grubych materiałów (do 100 mm), m.in. stali nierdzewnej, miedzi, tytanu i aluminium. Wycinarki plazmowe są mniej dokładne niż laserowe. Ponadto krawędzie nimi rozcięte są szorstkie, szczególnie w grubszych blachach. Możliwość przecinania tych ostatnich jest jednak ważną zaletą tej techniki, w porównaniu do cięcia laserem. |
ROBOTYZACJA SPAWANIA
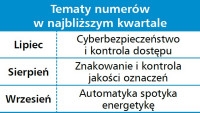
Tematy numerów w najbliższym kwartale
Ręczne spawanie nadal jest popularne, ponieważ operator szybciej niż system automatyczny adaptuje się do zmieniających się warunków. Po wstępnej ocenie jakości krawędzi, które ma połączyć, jest on w stanie, wykonując kolejne fragmenty spawu, na bieżąco regulować ustawienia spawarki. Jeżeli zauważy jakiś ubytek na krawędzi, przez który arkusze dzieli większa szczelina, wykonuje grubszą spoinę. Jeśli z kolei z powodu nierówności brzegi są zbyt blisko siebie, wykona on odpowiednio cieńszy spaw.
Z drugiej strony automatyzacja ma wiele zalet, m.in. większą wydajność i powtarzalność. Ciągłość i jakość produkcji nie zależy od dostępności oraz kwalifikacji operatorów. Wyręczenie tych ostatnich robotami poprawia też ich bezpieczeństwo.
Podobnie jak operatora, tak też robota trzeba "nauczyć" spawania, aby wykonywał je w sposób powtarzalny. Cel ten osiąga się przez programowanie. Podobnie jak człowiek musi się on też dostosowywać do zmiennych warunków. W tym celu kontroler robota powinien modyfikować parametry ruchu ramienia spawającego.
Realizuje się to, sterując nim na podstawie informacji z czujników. Ich zadaniem jest m.in.: detekcja krawędzi złącza, śledzenie jego przebiegu, żeby odpowiednio do niego zmieniało się położenie płomienia palnika i pomiar szerokości złącza w celu wykrycia wszelkich nieregularności i nieciągłości krawędzi.
Do wykrycia początku złącza lub krawędzi arkusza używa się sensorów dotykowych oraz zbliżeniowych. Pierwsze realizuje się, doprowadzając napięcie do dyszy, którą dostarczany jest gaz osłonowy, spawalniczego drutu albo dodatkowego próbnika. Kiedy ich końcówka dotknie blachy, sterownik robota wykrywa zwarcie. Sensory zbliżeniowe to zazwyczaj sensory indukcyjne. Do śledzenia przebiegu i wyznaczania wymiarów złącza używane są systemy wizyjne i skanery laserowe.
Monika Jaworowska