Pierwsze przepisy dotyczące tytułowych urządzeń zaczęto wprowadzać już z końcem XIX wieku. W latach 70. zeszłego stulecia opracowano pierwszą wersję normy IEC 60439, która na lata stała się dokumentem obowiązującym. Dopiero 2009 roku została opublikowana pierwsza wersja "nowej" normy IEC 61439.
Wprowadzono w niej znaczące modyfikacje w porównaniu do starej IEC 60439. Zmiany były konieczne, ponieważ w stosunku do tej ostatniej projektanci, producenci oraz prefabrykatorzy rozdzielnic niskiego napięcia zgłaszali liczne zastrzeżenia.
Powszechnie narzekano, że norma IEC 60439 została po prostu źle napisana, przez co jej treść była nieuporządkowana, a wiele zagadnień nie zostało doprecyzowanych. Dlatego trudno było ją zrozumieć, a subiektywne interpretacje nie zawsze okazywały się najtrafniejszymi.
Największe trudności sprawiało rozróżnienie badań częściowych PTTA i badań pełnych TTA. Ponadto w pierwszej części normy IEC 60439 granica między wymaganiami wspólnymi dla wszystkich dokumentów z tej serii, a wymaganiami dla poszczególnych grup produktów była zatarta.
Wszystkie powyższe problemy zostały rozwiązane w normie IEC 61439 (PN-EN 61439 pt. Rozdzielnice i sterownice niskonapięciowe). Podobnie jak wcześniejszą, podzielono ją na części. Nowością była w niej część zerowa.
JAKIE NORMY NALEŻĄ DO SERII IEC 61439?
Dokument IEC 61439-0, który nie został przyjęty przez PKN, stanowi przewodnik projektowania rozdzielnic niskonapięciowych. Z kolei PN-EN 61439-1 pt. Postanowienia ogólne określa wspólne wymagania dotyczące tytułowych urządzeń różnych typów.
Jest to dokument podstawowy. Aby określić wymogi, które należy spełnić podczas planowania, produkcji (montażu), badań i przygotowywania dokumentacji rozdzielnic niskonapięciowych równocześnie trzeba się stosować do zapisów odpowiedniej normy produktowej.
Opracowano pięć norm tego typu. Druga część PN-EN 61439 dotyczy rozdzielnic oraz sterownic do rozdziału energii elektrycznej. W PN-EN 64139-3 zostały opisane wymagania dla rozdzielnic instalacyjnych, natomiast w części czwartej dla rozdzielnic, które zostaną zainstalowane na placu budowy.
Do tej serii norm zalicza się również dokumenty: PN-EN 64139-5 pt. Zestawy do dystrybucji mocy w sieciach publicznych oraz PN-EN 61439-6 pt. Systemy przewodów szynowych. Część siódma IEC 61439, która dotyczy rozdzielnic oraz sterownic dla szczególnych miejsc prowadzenia działalności, pomieszczeń i urządzeń szczególnego rodzaju, na przykład kempingów i stacji ładowania pojazdów elektrycznych, nie została wprowadzona przez Polski Komitet Normalizacyjny.
Normy PN-EN 60439 i PN-EN 61439 przez pewien czas obowiązywały jednocześnie. Okresy przejściowe już jednak minęły (patrz ramka).
Od marca 2015 roku przestała obowiązywać norma PN-EN 60439-3 pt. Wymagania dotyczące niskonapięciowych rozdzielnic i sterownic przeznaczonych do instalowania w miejscach dostępnych do użytkowania przez osoby niewykwalifikowane - Rozdzielnice tablicowe. Zastąpiła ją norma PN-EN 61439-3. W czerwcu 2015 roku wycofano PN-EN 60439-2 pt. Wymagania dotyczące przewodów szynowych, którą zastąpiła PN-EN 61439-6, a w grudniu 2015 normę PN-EN 60439-4 na rzecz PN-EN 61439-4. W styczniu 2016 roku analogicznej zamiany dokonano w przypadku szóstych części obu dokumentów. Jeżeli badania rozdzielnic zostały wykonane zgodnie z wcześniej obowiązującymi normami serii PN-EN 60439, a wyniki badań spełniają wymagania odpowiedniej części norm PN-EN 61439, to ponowna weryfikacja takich rozdzielnic nie jest wymagana. |
ROZDZIELNICE ELEKTRYCZNE - CO ZMIENIONO W PN-EN 61439?
Dzięki oddzieleniu pierwszej części ogólnej od pozostałych części szczegółowych norma PN-EN 61439 w porównaniu do PN-EN 60439 jest bardziej uporządkowana. Jasno określono w niej także, kto i za co jest odpowiedzialny w procesie powstawania rozdzielnicy, wyróżniając kilka stron, które biorą w tym udział i każdej z nich przypisując konkretne zadania.
Ponadto zrezygnowano z pełnych badań typu TTA oraz częściowych badań typu PTTA, zastępując je weryfikacją konstrukcji. Tę można przeprowadzić na kilka równoważnych sobie sposobów. Do PN-EN 61439 włączono również normę, która dotyczy pustych obudów (PN-EN 62208).
W normie PN-EN 61439 odpowiedzialność za rozdzielnicę wprowadzaną na rynek rozdzielono wyraźnie między trzech uczestników procesu jej powstawania. Pierwszym z nich jest użytkownik, który ją kupi i będzie używać lub obsługiwać. Zazwyczaj jest on reprezentowany przez projektanta. Pozostałych dwóch to: producent pierwotny (oryginalny producent systemu) i producent zestawu rozdzielnicy (prefabrykator rozdzielnicy).
Użytkownik / projektant ma obowiązek opisać rozdzielnicę jako "czarną skrzynkę", czyli zbiór parametrów widzianych z zewnątrz, na podstawie których dobrane zostanie jej wyposażenie. Norma PN-EN 61439 wyróżnia cztery grupy tych cech, które charakteryzują:
- warunki instalacji i otoczenia,
- obsługę i konserwację,
- podłączenie do sieci elektrycznej,
- obwody elektryczne i odbiorniki.
JAK OPISAĆ WARUNKI INSTALACJI I OTOCZENIA ROZDZIENIC ELEKTRYCZNYCH NISKIEGO NAPIĘCIA?
Jeśli chodzi o tytułowe wymogi, to podać trzeba, czy rozdzielnica będzie użytkowana w warunkach standardowych, czy przemysłowych. Zaznaczyć należy, jeżeli może być narażona na nietypowe oddziaływania, na przykład środków chemicznych lub dużych obciążeń mechanicznych oraz określić zakres temperatur i wilgotności otocznia. Ważne, czy będzie użytkowana wewnątrz budynku, a jeżeli tak, to czy będzie się znajdować w zamkniętym, wydzielonym pomieszczeniu, czy w otwartej hali.
Jeśli zostanie zamontowana poza budynkiem, należy doprecyzować, czy w miejscu osłoniętym, czy nie. W drugim przypadku materiał obudowy trzeba będzie przetestować pod kątem odporności na promienie UV i uwzględnić wzrost temperatury pod wpływem jej nagrzewania przez promienie słoneczne. Określić należy wymagany stopień ochrony IP (pyłoszczelność, wodoszczelność).
KTO BĘDZIE OBSŁUGIWAŁ ROZDZIELNICĘ?
Do warunków instalacji zalicza się ponadto rodzaj montażu (naścienny, wolno stojący), dostępną przestrzeń (szerokość, wysokość, głębokość) i maksymalną dopuszczalną wagę. Istotną kwestią są warunki transportu: maksymalne dopuszczalne rozmiary i waga rozdzielnicy w opakowaniu.
W zakresie obsługi i konserwacji zasadniczą kwestią jest, czy do rozdzielnicy będą miały dostęp wyłącznie osoby posiadające odpowiednie kwalifikacje, czy także osoby niewykwalifikowane. Urządzenia, które mogą być użytkowane tylko przez elektryka, powinno się umieszczać za drzwiami albo pokrywami otwieranymi tylko przy użyciu specjalnych narzędzi.
Osoby niewykwalifikowane muszą mieć natomiast możliwość obsługi ręcznej oraz ułatwiony dostęp przez drzwi i pokryw na zawiasach. Użytkownik powinien też podać parametry sieci zasilającej (napięcie, prąd, typ, itp.) oraz zapotrzebowanie na moc odbiorników, ich charakter (rezystancyjny, indukcyjny, pojemnościowy), sposoby ich użytkowania i rodzaje zabezpieczeń.
Jak obliczyć graniczne przyrosty temperatury?Wyróżnia się dwie metody obliczania granicznych przyrostów temperatur, których zastosowanie jest możliwe, jeżeli spełnione są określone warunki. W przypadku pierwszej prąd znamionowy urządzenia musi być mniejszy niż 630 A, a zestaw rozdzielnicy powinien być zamontowany w jednej szafie. Ponadto należy znać parametry strat mocy wszystkich przewidzianych środków roboczych, źródła strat mocy powinny być rozmieszczone równomiernie, zaś mechaniczne elementy zabudowy i środki robocze nie mogą zaburzać konwekcji powietrza. Obciążenie tych ostatnich przy danym prądzie znamionowym obwodu elektrycznego nie może przekraczać 80%. Ponadto przewody, którymi płyną prądy o natężeniu powyżej 200 A, należy ułożyć tak, żeby nie powodowały dodatkowego wzrostu temperatury przez prądy wirowe i straty histerezy, natomiast przewody głównych torów prądowych muszą być zaprojektowane na min. 125% przewidywanego prądu znamionowego obwodu prądowego. Trzeba również znać zdolność oddawania strat mocy obudowy w zależności od rodzaju montażu i moc chłodniczą aktywnych środków chłodzenia. Na podstawie powyższych danych dla każdego obwodu elektrycznego wyznacza się stratę mocy przy prądzie znamionowym, straty mocy urządzeń i przewodów. Na podstawie ich sumy, zdolności oddawania ciepła obudowy oraz mocy chłodniczej wyznaczany jest przyrost temperatury zestawu rozdzielnicy. Jeśli nie przekracza ona maksymalnych dopuszczalnych temperatur pracy urządzeń rozdzielczych weryfikację uznaje się za zaliczoną. Podobne dane potrzebne są do obliczenia granicznych przyrostów temperatur drugim sposobem. W tym przypadku prąd znamionowy urządzenia nie powinien przekraczać 1600 A, zestaw rozdzielnic może się mieścić w więcej niż jednej szafie, a przyrost temperatury zestawu oblicza się z łącznej straty mocy metodą według normy IEC 60890. |
ZA CO ODPOWIADA PRODUCENT PIERWOTNY?
Według nowej normy do obowiązków producenta oryginalnego rozdzielnicy niskonapięciowej należy zaprojektowanie i zweryfikowanie tego produktu / konstrukcji. Weryfikacja powinna w tym przypadku polegać na udowodnieniu, że produkt został wykonany zgodnie z wymaganiami PN-EN 61439, które zostały zapisane w kilkunastu punktach w dziesiątym rozdziale pierwszej części tego dokumentu.
W nowej normie wprowadzono trzy metody weryfikacji. Są to sprawdzenia przez: badanie, porównanie albo obliczenia / ekspertyzę. Choć sposoby te są sobie równoważne, w praktyce najbardziej wiarygodne wyniki zapewnia rzeczywiste przetestowanie produktu, który jest poddawany weryfikacji (badania przeprowadza się na jego reprezentatywnych próbkach).
Z drugiej jednak strony jest to metoda droższa od pozostałych, a ponadto w przypadku niektórych punktów kontrolnych trzeba przeprowadzić badania niszczące. Dlatego, mimo że dla części z nich norma narzuca jeden sposób, dla większości dopuszcza różne metody sprawdzenia.
JAK ZWERYFIKOWAĆ ODPORNOŚĆ NA KOROZJĘ?
PN-EN 61439 wymaga m.in. sprawdzenia wytrzymałości materiałów i części. W tym punkcie wyróżniono aż siedem podpunktów. Wśród nich jest na przykład sprawdzenie odporności na korozję. Weryfikacji w tym przypadku można dokonać wyłącznie przez badanie. Pozostałe podpunkty dotyczą właściwości materiałów izolacyjnych.
Są to m.in.: wytrzymałość cieplna, odporność na ciepło nadzwyczajne i ogień na podstawie wewnętrznych oddziaływań elektrycznych i odporność na promieniowanie ultrafioletowe (dotyczy tylko obudów i części instalowanych na wolnym powietrzu). W przypadku pierwszej cechy należy przedstawić wynik badania w temperaturze +70°C trwającego 168 godzin z czasem odpoczynku trwającym 96 godzin. Sprawdzenie jest wymagane w przypadku części, które są umieszczone na zewnątrz obudowy i mają wpływ na stopień ochrony. Jedyną dopuszczalną metodą jest badanie. Jeżeli chodzi o drugą cechę, to temperatura, którą powinna wytrzymać dana część, zależy od jej przeznaczenia.
PRZEGLĄD PUNKTÓW KONTROLNYCH
Odporności na najwyższą, wynoszącą +960°C, oczekuje się od elementów, które podtrzymują przewody; +850°C powinny wytrzymać obudowy, które będą instalowane w ścianach pustych wewnątrz, a +650°C pozostałe części. Cechę tę można potwierdzić badaniem albo na podstawie dokumentacji danego tworzywa sztucznego. Podobnie jest w przypadku sprawdzania odporności na promieniowanie UV. Do tej grupy zalicza się także badanie wytrzymałości na uderzenia i podczas podnoszenia oraz na znakowanie.
Kolejne podpunkty dotyczą stopnia ochrony obudowy oraz powietrznych i powierzchniowych odstępów izolacyjnych. Te ostatnie można zweryfikować tylko przez badanie. Jeżeli chodzi o podpunkt dotyczący ochrony przed porażeniem prądem elektrycznym oraz drożności obwodów przewodu ochronnego, sprawdzenia wymagają: drożność połączenia między korpusami rozdzielnic z obwodami prądowymi przewodu ochronnego oraz wytrzymałość zwarciowa obwodu przewodu ochronnego. Pierwszą trzeba zbadać, zaś drugą można wykazać przez porównanie.
KIEDY NIE TRZEBA BADAĆ WYTRZYMAŁOŚCI ZWARCIOWEJ?
Norma PN-EN 61439 wymaga również sprawdzenia, czy wewnętrzne obwody i połączenia elektryczne oraz przyłącza przewodów zewnętrznych zostały wykonane prawidłowo. Oba punkty wymagają weryfikacji przez ekspertyzę. W przypadku właściwości izolacji należy przebadać napięcie przebicia przy częstotliwości roboczej oraz zbadać albo wykazać przez ekspertyzę odporność na napięcie udarowe. Poza tym kontroli wymaga wytrzymałość zwarciowa, kompatybilność elektromagnetyczna i funkcja mechaniczna. Z konieczności sprawdzenia pierwszego parametru wyłączona jest pewna grupa urządzeń.
Weryfikacja wytrzymałości zwarciowej nie jest wymagana w przypadku:
- rozdzielnic o znamionowej krótkotrwałej wytrzymałości prądowej lub uwarunkowanym znamionowym prądzie zwarciowym o maksymalnej wartości skutecznej 10 kA,
- rozdzielnic lub obwodów elektrycznych chronionych przez urządzenie zabezpieczające ograniczające prąd przewodzenia do maksymalnie 17 kA,
- obwodów pomocniczych, które są podłączone do transformatorów o znamionowym napięciu wtórnym 110 V lub wyższym i o maksymalnej mocy znamionowej 10 kVA,
- obwodów pomocniczych o napięciu poniżej 110 V i maksymalnej mocy znamionowej 1,6 kVA.
Sprawdzić trzeba również graniczne przyrosty temperatury.
Sprawdzenie produktu oraz konstrukcji i kontrola wyrobu zapewniają liczne korzyści w zakresie bezpieczeństwa obsługi rozdzielnicy i instalacji, do których jest ona podłączona. Na przykład weryfikacja granicznych przyrostów temperatury ma wpływ na wydłużenie żywotności całej rozdzielnicy i jej wyposażenia. Zmniejsza też zagrożenie pożarem. Weryfikacja właściwości dielektrycznych pozwala natomiast zapobiec szkodom, jakie mogą spowodować przepięcia. Sprawdzenie ochrony przeciwporażeniowej i integralności obwodów ochronnych zabezpiecza obsługę przed niebezpiecznymi napięciami na nieosłoniętych elementach przewodzących oraz na tych normalnie nieprzewodzących prądu. Weryfikacja funkcji mechanicznej przedłuża żywotność ruchomych części rozdzielnicy, a sprawdzenie wytrzymałości materiałów oraz części zapobiega zniszczeniu ich przez korozję, promieniowanie UV, przegrzanie, w wyniku pożaru i na skutek oddziaływań mechanicznych. Jeśli z kolei chodzi o kontrolę gotowego wyrobu to m.in. daje ona gwarancję prawidłowego montażu właściwego wyposażenia, zgodnie z wytycznymi producenta rozdzielnicy. Dzięki weryfikacji zacisków do przewodów zewnętrznych łatwiejszy jest montaż przewodów i kabli, a sprawdzenie funkcji mechanicznych dowodzi prawidłowego działania elementów ruchomych i wyjmowanych. Weryfikacja funkcjonalności rozdzielnicy gwarantuje, że realizuje ona zadania zgodnie ze swoim przeznaczeniem. |
JAK WYZNACZYĆ GRANICE NAGRZEWANIA SIĘ?
Graniczne przyrosty temperatury można zweryfikować każdym z trzech dopuszczonych w normie sposobów. W przypadku metody badania wybrać trzeba jeden z trzech wariantów.
W pierwszym sprawdzany jest cały zestaw rozdzielnicy. Jego zaletą są mniejsze koszty, jednak w ten sposób można testować tylko urządzenia, których typ wykonywany jest zawsze tak samo. W drugim wariancie badane są indywidualne jednostki funkcyjne i kompletny zestaw rozdzielnicy. Można także wykonać osobne badania indywidualnych jednostek funkcyjnych, głównych szyn zbiorczych, szyn rozdzielczych i kompletnego zestawu rozdzielnicy. Wariant ten jest zalecany wówczas, gdy liczba i wyposażenie pól są modułowe i zmieniają się.
W przypadku metod badania i porównania nie ma ograniczeń. Z obliczania można natomiast skorzystać tylko przy wyznaczaniu granicznych przyrostów temperatury rozdzielnic o prądach o natężeniu do 1600 A. W ramce przedstawiamy szczegółowo ten sposób weryfikacji.
ZADANIA PREFABRYKATORA
Prefabrykator rozdzielnicy odpowiada za jej produkcję zgodnie z wytycznymi producenta oryginalnego, tak by była ona zgodna z projektem, który został przez niego zweryfikowany. Jeżeli producent zestawu nie wprowadzi żadnych zmian w stosunku do pierwotnego systemu, wówczas jego obowiązkiem jest wyłącznie wykonanie końcowego testu rutynowego wyrobu.
W ramach niego powinien sprawdzić m.in.: stopnie ochrony obudów, odstępy izolacyjne powierzchniowe i powietrzne, czy zapewniona jest ochrona przed porażeniem prądem elektrycznym i drożność obwodu przewodu ochronnego, wewnętrzne połączenia obwodów elektrycznych, przyłącza przewodów doprowadzonych z zewnątrz, sprawność działania zamków, blokad i elementów wyzwalających oraz to, czy zakładane parametry i funkcjonalność rozdzielnicy są zapewnione.
Jeżeli jednak prefabrykator dokona jakichkolwiek modyfikacji, na przykład zamontuje urządzenia innego producenta, wówczas automatycznie sam staje się producentem oryginalnym. W związku z tym jest wtedy zobowiązany do przeprowadzenia własnej weryfikacji według opisanych powyżej punktów zalecanych w normie PN-EN 61439.
Hagercad.one HagerSoft, Elcom 5.1 PowerDesign Power Engineering |
NAJLEPSZA ROZDZIELNICA... CZYLI JAKA?
Producenci rozdzielnic niskonapięciowych opisują swoje produkty różnymi przymiotnikami. Przeważnie urządzenia te są reklamowane jako bezpieczne dla personelu w czasie użytkowania i konserwacji, ergonomiczne, łatwe do obsługi oraz do serwisowania, niezawodne oraz o modułowej konstrukcji w zakresie elektrycznych i mechanicznych komponentów.
Dzięki tej ostatniej łatwo można je zmodyfikować, przebudować albo rozbudować, w zależności od potrzeb. Przeważnie dopuszcza się również możliwość późniejszej rekonfiguracji w trakcie pracy urządzenia, przy równoczesnym zachowaniu ciągłości zasilania odpływów.
Oprócz tego ich konstrukcję zazwyczaj charakteryzuje kompaktowość, dzięki której optymalnie wykorzystują dostępną przestrzeń. Kolejną podkreślaną zaletą jest wykonanie z zachowaniem przejrzystego podziału przestrzenno-funkcjonalnego.
Klientów zachęca się rozbudowanymi możliwościami komunikacyjnymi oraz oprogramowaniem, które ułatwiają zintegrowanie rozdzielnic z innymi systemami w zakładzie. Wśród ich zalet wymienia się łatwość wdrożenia i niskie koszty eksploatacji, nie zapominając o nowoczesnym wzornictwie oraz wygodzie użytkowania. Niektórzy producenci mają też w swojej ofercie rozdzielnice w specjalnym wykonaniu, na przykład odporne na drgania i wstrząsy. Dalej przedstawiamy wybrane rozwiązania konstrukcyjne, dzięki którym producenci realizują swoje obietnice.
IEC 61641 - NORMA UZUPEŁNIAJĄCA
Bezpieczeństwo rozdzielnic niskonapięciowych jest zapewniane przez zgodność z normami PN-EN 61439-1 i PN-EN 61439-2. Dodatkowo niektórzy producenci w tym celu przeprowadzają badania rozdzielnic na zgodność z normą IEC 61641, chociaż stosowanie się do niej jest opcjonalne.
Badania te mają na celu sprawdzenie, czy rozdzielnica ma zdolność do ograniczenia ryzyka obrażeń u personelu i uszkodzenia instalacji w razie wystąpienia wewnętrznego zwarcia łukowego. Jest to jedno z najbardziej niebezpiecznych zjawisk w systemach elektroenergetycznych, do którego przyczyn zalicza się m.in. pozostawienie narzędzi lub materiałów po zakończeniu naprawy oraz gromadzenie się osadów przewodzących na elementach izolacji.
Łuk elektryczny, który powstaje w wyniku zwarcia łukowego, ma bardzo dużą energię. Ta przekłada się na gwałtowny wzrost ciśnienia, co w przypadku zamkniętej przestrzeni w rozdzielnicy może spowodować nagłe otwarcie jej drzwi, a nawet wybuch i rozerwanie obudowy. Zjawisku temu towarzyszy też bardzo wysoka temperatura, co z kolei grozi poparzeniem personelu, a nawet pożarem.
Żeby uniknąć takich sytuacji, przede wszystkim nie wolno dopuścić do powstania wyładowania łukowego, co osiąga się przez właściwą konstrukcję i wymiarowanie wyposażenia rozdzielnicy. Jeśli już jednak do niego dojdzie, należy dążyć do ograniczenia jego skutków, głównie przez jego wygaszenie w przedziale, w którym się wytworzył.
CZYM JEST MODUŁ FUNKCJONALNY?
W tym celu m.in.: wydziela się przedziały dla szyn zbiorczych, rozdzielczych i aparatów, pomiędzy nimi umieszcza się gazoszczelne połączenia, wprowadza się rozwiązania zapobiegające odkręcaniu się śrub, izoluje od siebie jednofazowe styki oraz stosuje odpowiednio duże odstępy pomiędzy szynami. Norma IEC 61641 wymaga też sprawdzenia, czy m.in. drzwi i pokrywy są odpowiednio zabezpieczone i się nie otwierają, a także czy żadne elementy, które są potencjalnie groźne, nie odpadają oraz czy w obudowie nie tworzą się żadne otwory.
Elastyczność w zakresie wyposażenia rozdzielnic osiąga się przede wszystkim dzięki korzystaniu z modułów funkcjonalnych. Są to zespoły, które zawierają aparaturę elektryczną oraz inne elementy konstrukcyjne, które można demontować i montować stosownie do potrzeb. Używa się modułów różnego rodzaju. Przykładowe rozwiązania to moduły, które są podłączane do szyn połączeniami śrubowymi oraz moduły wtykowe, rozłączane i wyjmowane, które są podłączane przez styki siłowe (plug-in).
PRZYKŁADY UDOGODNIEŃ
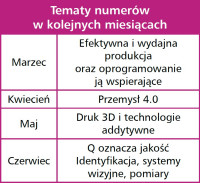
Tematy numerów w kolejnych miesiącach
Aby zapewnić bezpieczeństwo ich użytkowania, m.in. wyposaża się je we wskaźniki stanu pracy i blokady, natomiast wygodę zapewniają na przykład: prowadzenie szuflad na łożyskach kulkowych, które minimalizują wysiłek podczas ich wysuwania i ergonomiczne rączki, ułatwiające uchwycenie części ruchomej. By wydłużyć żywotność modułów funkcjonalnych, stosuje się m.in. rozwiązania spowalniające zużywanie się ich styków.
Do rozwiązań ułatwiających użytkowanie zalicza się możliwość zmiany kierunku otwierania drzwi rozdzielnic dzięki uniwersalnym zawiasom. Aby z kolei zwiększyć odporność na drgania i wstrząsy, na przykład instaluje się system tłumienia energii wstrząsów, stosuje aparaturę odporną na wstrząsy i wzmacnia korpus, obudowę i inne elementy.
Aby korzystanie z rozdzielnic od początku odbywało się jak najsprawniej, ich producenci wprowadzają rozwiązania ułatwiające ich instalację i podłączenie w miejscu docelowym. Przykładowe z nich to m.in.: umieszczenie uchwytów transportowych na dachu rozdzielnicy, możliwość demontażu pozwalająca na przewóz bloku za pomocą środka transportu, na przykład wózka widłowego i ułatwienia w dostępie do przedziałów z kablami, dzięki którym szybciej można je wyprowadzić na zewnątrz.
Monika Jaworowska