Roboty w kopalniach
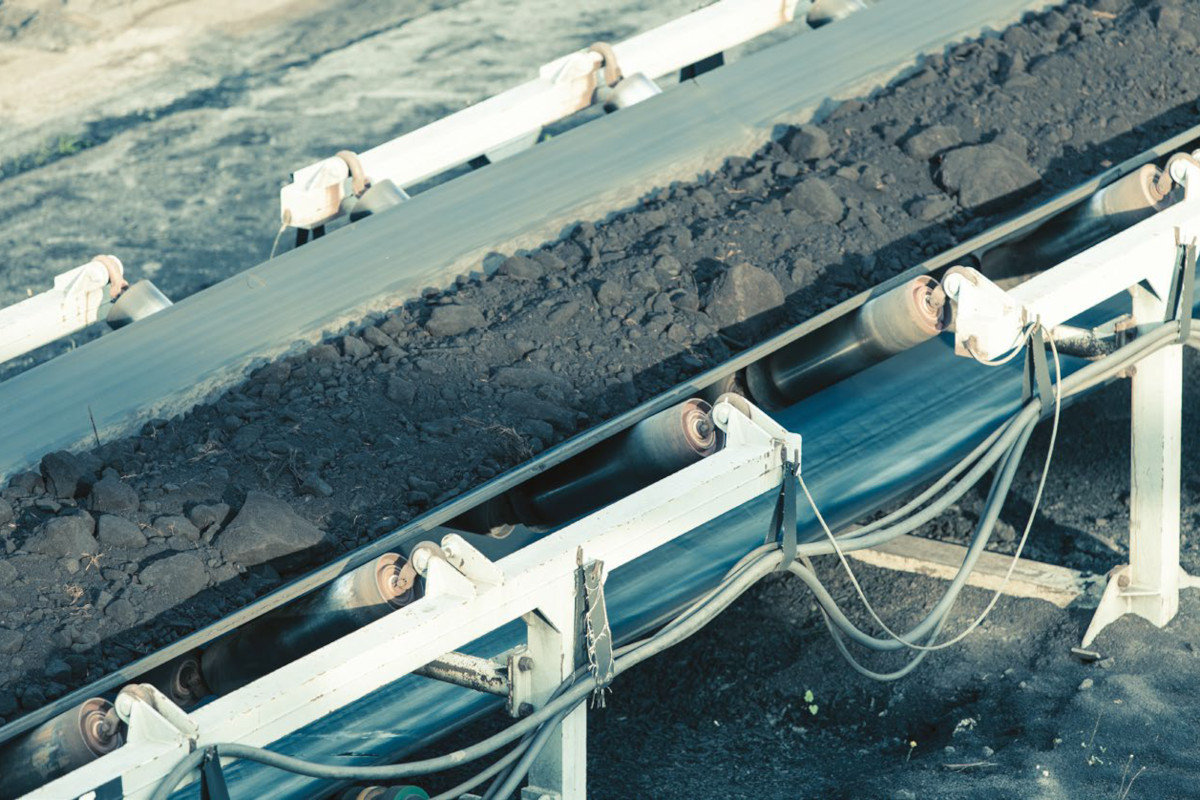
Ze względu na specyfikę pracy w kopalniach, podziemnych i odkrywkowych, dąży się do ograniczania obecności ludzi w szczególnie niebezpiecznych rejonach tych zakładów. W tym celu m.in. wykorzystuje się w nich roboty. Są one jak na razie głównie wykorzystywane w zadaniach nietypowych jak eksploracja zamkniętych kopalni. Wiele z nich jest bowiem coraz częściej poddawanych ponownej ocenie pod kątem występowania w nich złóż kopalin rzadkich, które dawniej uważano za niewartościowe, a które obecnie są niezbędne na przykład w produkcji elektronicznej, jak pierwiastki ziem rzadkich. Badania pod tym kątem są prowadzone zwłaszcza w Unii Europejskiej, która w związku z problemami z dostępnością do surowców o krytycznym znaczeniu dla branż strategicznych zamierza uniezależnić się od ich niepewnych zewnętrznych źródeł.
W Europie jest nawet kilka tysięcy opuszczonych kopalń, obecnie zazwyczaj zalanych, które wymagają sprawdzenia. Wysłanie tam ludzi, by penetrowali zatopione, wąskie korytarze, poruszając się w mętnej wodzie i w ciemnościach, wiązałoby się, poza kosztami, z narażeniem nurków na ogromne niebezpieczeństwo. Zaprojektowania robotów do tego zadania również nie jest jednak łatwe. Główne wyzwanie to opracowanie konstrukcji umożliwiającej poruszanie się w ciasnej przestrzeni przy ograniczonej widoczności, a więc o odpowiednio małych rozmiarach, w której należy jednak zmieścić dużą liczbę wyposażenia, w tym napęd, systemy nawigacyjne i komputer pokładowy, urządzenia pobierające próbki i rejestrujące dane geologiczne i przestrzenne.
Pracuje się też na rozwiązaniami, które mają poprawić bezpieczeństwo górników dzięki łącznemu wykorzystaniu Internetu Rzeczy i robotów. Przykładem jest detekcja oraz sprawdzanie wycieków toksycznych substancji. W tym celu tworzy się sieci IoT czujników, które monitorują środowisko kopalni i zapewniają wczesne ostrzeganie o zagrożeniu, co pozwala na czas ewakuować górników. Wówczas w niebezpieczny rejon wysyła się roboty, by zbadały wyciek. Wyzwaniem w tworzeniu i utrzymaniu infrastruktury Internetu Rzeczy w kopalniach jest to, że inaczej niż w fabryce, gdzie maszyny, stanowiska robocze i linie produkcyjne mają określoną lokalizację, środowisko pracy pod ziemią ciągle się zmienia, a przestrzeń jest nieregularna i zamknięta. Pracuje się również nad cobotami, które współpracując z ludźmi będą wysyłane jako pierwsze do zbadania otoczenia pod kątem występujących w nim zagrożeń (na przykład osunięć skał), zanim na dane stanowisko wejdą górnicy.
Case study – Kopalnie autonomiczneRio Tinto jest pierwszą firmą, która zrealizowała całkiem zautomatyzowane wiercenie otworów bez interwencji człowieka. Cel ten osiągnięto w ramach systemu ADS (Autonomous Drill System), który pozwala operatorowi korzystającemu z pulpitu sterowniczego w zdalnej lokalizacji nadzorować kilka autonomicznych wiertnic różnych producentów jednocześnie. Ponadto w australijskich kopalniach Rio Tinto pracują autonomiczne, bezzałogowe ciężarówki (Autonomous Haulage System). Wyposażono je w liczne czujniki (m.in. radarowe i laserowe). Wyniki pomiarów są wykorzystywane przez program sztucznej inteligencji, dzięki któremu pojazdy uczą się topografii terenu kopalni. Trasy wywrotek, śledzone dzięki zamontowaniu w nich odbiorników GPS, są także poddawane analizie w centrum sterowania. Pozwala to koordynować ich przemieszczanie się i optymalizować przyszłe ścieżki i parametry ruchu (prędkość). Ponadto ciężarówki wyposażono w autonomiczny system detekcji kolizji. Na podstawie danych z licznych czujników, gdy na drodze pojawi się przeszkoda, automatycznie modyfikuje on zadaną trasę pojazdu. Sensory monitorują również stan wywrotki, m.in. ciśnienie w oponach, temperaturę płynów chłodzących, ich ciśnienie, poziom i stopień czystości, temperaturę oraz poziom wibracji łożysk, temperaturę i ciśnienie w układzie hamulcowym. Dzięki temu zamiast angażować personel do wykonywania okresowych przeglądów floty, można przewidywać problemy eksploatacyjne i na bieżąco na nie reagować. W zakładach górniczych Rio Tinto uruchomiono również autonomiczne pociągi. Długodystansowa sieć kolejowa o dużym zasięgu działa w następujący sposób: po wprowadzeniu przez kontrolera, który znajduje się w centrum operacyjnym, informacji o trasie przejazdu i uruchomieniu przez niego systemu, komputery pokładowe składu oraz komputery w centrum sterowania przejmują kontrolę i podejmują wszystkie dalsze decyzje odnośnie do sterowania pojazdem samodzielnie. Odpowiadają one m.in. za to, aby pociąg nie przekraczał limitów prędkości, nie zderzył się z innymi składami i przejeżdżał tylko przez puste przejazdy kolejowe. Również jeżeli wykryją awarię jakiegokolwiek podzespołu pojazdu, muszą go bezpiecznie zatrzymać. |
Kopalnie autonomiczne
Wszystkie innowacje opisane powyżej zbliżają kopalnie do celu, którym jest ich w pełni autonomiczna praca. Podejmowane są już pierwsze próby w tym zakresie. Sztandarowy przykład to projekt realizowany w kopalniach rudy żelaza w regionie Pilbara w Australii Zachodniej przez firmę Rio Tinto. Sukcesywnie wdraża ona w swoich zakładach górniczych rozwiązania autonomiczne. Jak do tej pory skupiano się w tym zakresie na dwóch segmentach działalności kopalń: wierceniu i transporcie urobku (patrz: ramka).
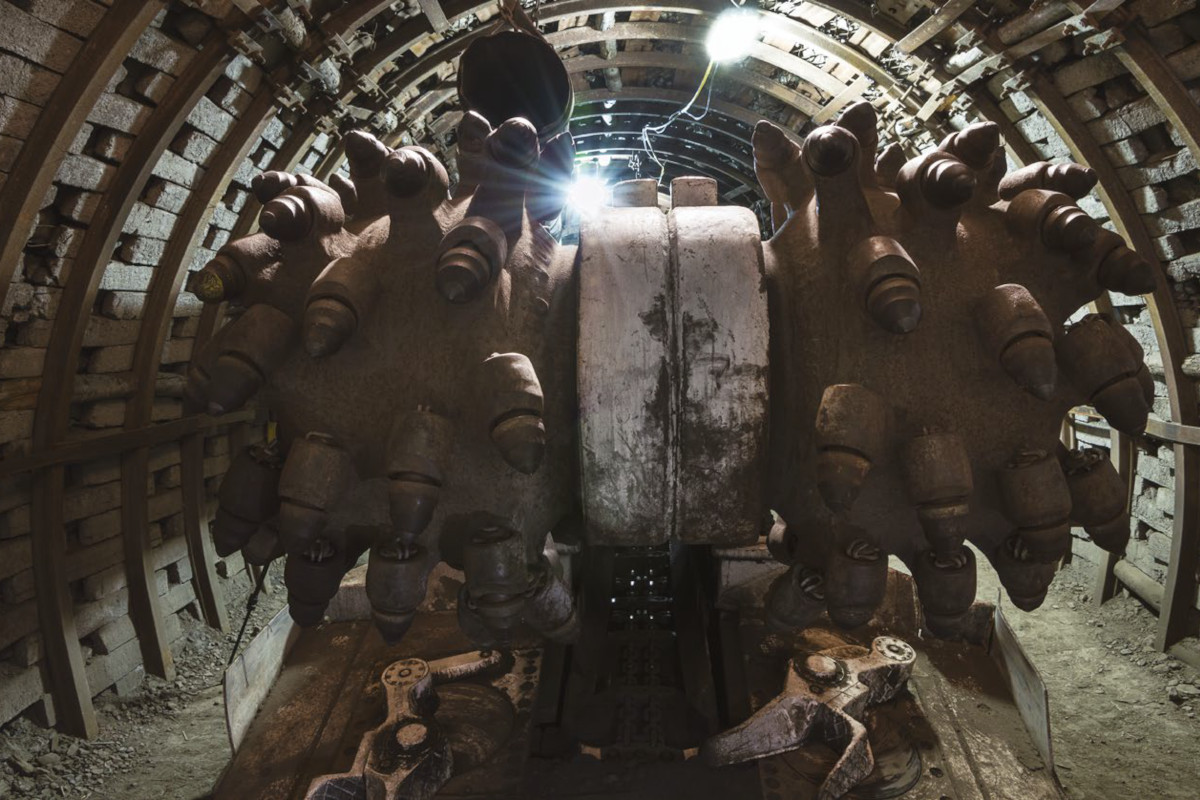
Monika Jaworowska