Inteligentne koparki
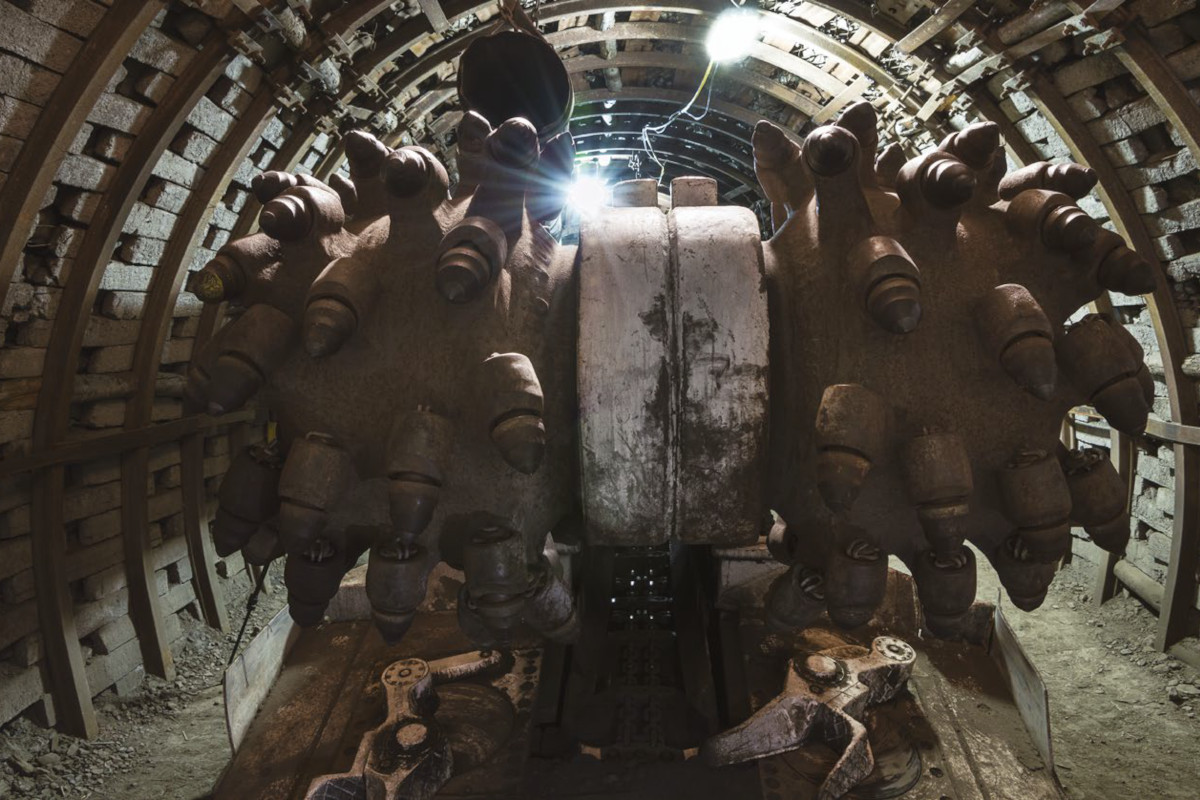
Nagromadzenie komponentów automatyki i czujników stanowią też systemy pokładowe koparek. Przykład to te automatycznie ograniczające odchylenie łyżki, co ma zapobiegać rozsypywaniu się urobku i utrzymujące wymagany kąt jej ustawienia, w poziomie i pionie. Dzięki sensorom koparki, uważane raczej za maszyny o prostej funkcjonalności (pobierz łyżką materiał i go rozładuj), mogą też jednak działać inteligentniej. W jednym z przykładowych rozwiązań wyposaża się je w czujniki rentgenowskie. Działają one, wykorzystując technikę rentgenowskiej spektroskopii fluorescencyjnej, która pozwala na jakościową oraz ilościową ocenę składu pierwiastków próbki. Zasada pomiaru jest następująca: naświetlenie próbki promieniowaniem rentgenowskim powoduje wybicie elektronów z powłok. Powstałe w efekcie dziury zapełniają się elektronami przechodzącymi z wyższych powłok, czemu towarzyszy emisja promieniowania X o energii charakterystycznej dla danego pierwiastka, co pozwala na jego identyfikację. Intensywność linii specyficznych dla konkretnego pierwiastka w widmie promieniowania pozwala określić ilościowy skład próbki. Jest to metoda szybka oraz nieniszcząca.
się w łyżkę koparki. Wyniki pomiarów są w czasie rzeczywistym analizowane w oprogramowaniu, w którym zaimplementowano algorytmy uczenia maszynowego. Pozwala to na zidentyfikowanie na miejscu składu właśnie wykopanego ładunku i przyspiesza jego sklasyfikowanie jako materiału wartościowego, który należy poddać dalszej obróbce lub odpad, który trzeba przekierować na składowisko odpadów. Jest to efektywniejsza metoda niż podejście tradycyjne, w którym skład bloku skalnego ocenia się na podstawie próbek pobranych ze skały w kilku miejscach. Wiarygodność tej techniki jest ograniczona ze względu na założenie, że cały blok jest strukturą jednorodną, podczas gdy w rzeczywistości jest niejednolity. Przez to liczyć się trzeba ze stratą surowca uznanego za odpady, jak i ich obecność w wartościowej skale, co podnosi koszty operacyjne oraz zużycie energii. Inteligentne koparki pozwalają tego uniknąć. Poza tym dane dzięki nim gromadzone można wykorzystać do mapowania złóż ze znacznie większą dokładnością. To pozwala lepiej planować eksploatację kopalni, w tym roboty strzałowe.
Jak zapewnić skuteczną wentylację?
Sensory są również wykorzystywane poza specjalistycznym sprzętem górniczym, głównie do monitorowania warunków w kopalniach. W tych podziemnych przykładowo występuję gazy jak tlenki azotu, dwutlenek i tlenek węgla, których źródłem są roboty strzałowe oraz silniki spalinowe maszyn górniczych, jak też naturalnie występujące metan oraz radon. Ponieważ są szkodliwe dla pracowników, aby zapewnić im bezpieczne środowisko pracy, wymagana jest efektywna wentylacja, dostarczająca czyste powietrze w strefach przebywania ludzi. Skuteczność cyrkulacji i wymiany zanieczyszczonego powietrza zależy od jego ciśnienia i przepływu. Te wielkości są w związku z tym jednymi z częściej mierzonych. Korzysta się w tym celu z różnych sensorów.
Przykład to anemometry łopatkowe. Przepływ powietrza w tym przypadku jest obliczany na podstawie pomiaru prędkości obrotów łopatki, którą w ruch wprawia powietrze przepływające przez przyrząd. Zakres pomiaru anemometrów łopatkowych typowo wynosi 1 – 15 m/s. Wartości spoza są za niskie, żeby uzyskać dokładny odczyt lub zbyt duże, przez co pęd powietrza może uszkodzić czujnik. Przepływ w tunelu nie jest równomierny, zatem aby wynik był wiarygodny odczyty z anemometrów rozmieszczonych w kilku punktach, trzeba uśrednić. Kolejny przykład to rurka Pitota. Przyrząd taki mierzy różnicę statycznego i dynamicznego ciśnienia medium, które przez niego płynie. Na tej podstawie, wykorzystując prawo Bernoullego, można obliczyć przepływ. W kopalniach montuje się poza tym przepływomierze ultradźwiękowe. Wyróżnia je szybkość i precyzja pomiaru. Są też w stanie mierzyć bardzo mały przepływ, jak i wykryć jego brak.
Obudowy w wykonaniu przeciwwybuchowym![]() Podstawowym zabezpieczeniem urządzeń elektrycznych i mechanicznych są obudowy. W strefach zagrożonych wybuchem wolno korzystać tylko z tych spełniających wymagania dyrektywy ATEX. Przystosowując sprzęt elektryczny oraz nieelektryczny do pracy w takich warunkach, trzeba przede wszystkim zapobiec zapłonowi atmosfery wybuchowej, którego mógłby on być źródłem. Oznacza to, że nie można dopuścić do wystąpienia iskrzenia, na przykład na skutek tarcia, uderzenia lub w wyniku wyładowania elektrostatycznego. Warunkiem jest też to, aby części, które mają kontakt z mieszaniną wybuchową, nie osiągały temperatury jej zapłonu. Zalecenia projektowe na ten temat zostały zamieszczone w normach z serii PN- EN 60079 zharmonizowanych z dyrektywą ATEX. Wyróżniono w nich cztery przypadki, w których środki ochronne nie pozwalają na zaistnienie niebezpiecznej sytuacji. W pierwszym przedostanie się mieszaniny wybuchowej do sprzętu, w którym może znajdować się źródło zapłonu i to, że do niego dojdzie, jest dopuszczalne, jednak wyklucza się przeniknięcie ognia do otoczenia. Przykładowe typy zabezpieczeń spełniające ten wymóg to: obudowy ognioszczelne (Ex d według PN-EN 60079-1) oraz osłony piaskowe (Ex q, PN-EN 60079-5). Ochrona w postaci obudowy gazowej z nadciśnieniem (Ex p, PN-EN 60079-2), przez zanurzenie w cieczy (Ex o, PN-EN 60079-6) lub hermetyzację (Ex m, PN-EN 60079-18), to natomiast przykłady zabezpieczeń zapobiegających wnikaniu mieszaniny wybuchowej i/albo jej zetknięciu z wewnętrznymi wynikającymi z funkcji urządzenia potencjalnymi źródłami zapłonu. Zabezpieczenie urządzeń za pomocą budowy wzmocnionej (Ex e, PN-EN 60079-7) gwarantuje zaś, że nawet jeśli mieszanina wybuchowa przedostanie się do obudowy działającego sprzętu, to się nie zapali. Iskrzenie ani podwyższone temperatury nie wystąpią również w urządzeniach iskrobezpiecznych (Ex i, PN-EN 60079-11). |