Co wyróżnia wodne młoty wgłębne?
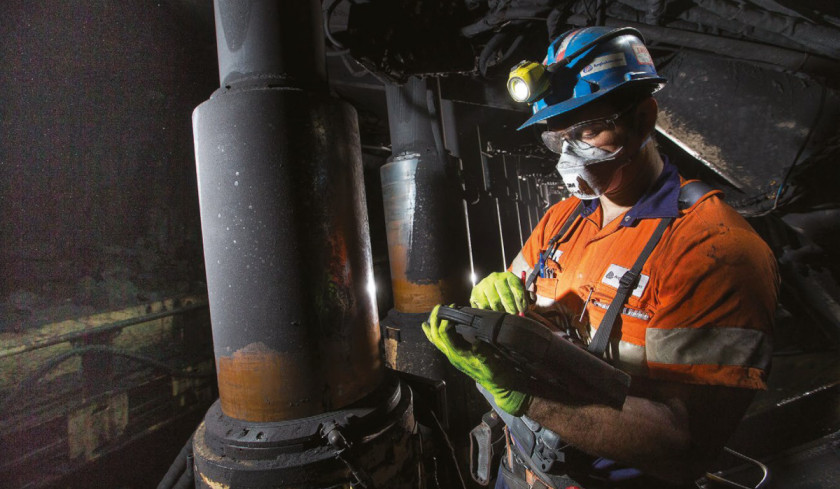
Zmechanizowane wiercenie w górnictwie ma długą tradycję. Rosnące przez lata wymagania w zakresie dokładności, głębokości, prostoliniowości odwiertów wymuszały udoskonalanie jego technik. Najnowszym osiągnięciem w tej dziedzinie są wodne młoty wgłębne. Mają one wiele zalet w porównaniu z konkurencyjnymi metodami wykonywania odwiertów (hydraulicznymi, pneumatycznymi), pod względem mniejszego zużycia energii i oddziaływania na środowisko oraz lepszych warunków i efektów wiercenia (głębsze otwory z minimalną odchyłką).
W przykładowym wykonaniu młot wodny zbudowany jest tylko z dwóch ruchomych części: tłoka i zaworu. To zwiększa żywotność tych urządzeń i umożliwia im pracę w najtrudniejszych warunkach. Zasada ich działania jest następująca: woda pod dużym ciśnieniem napędza mechanizm udarowy młota, a gdy go opuszcza, chociaż wytraciła prędkość, ma jeszcze wystarczającą siłę spłukiwania, żeby móc wypchnąć zwierciny na powierzchnię, oczyszczając odwiert. Oprócz tego kolumna hydrostatyczna, która tworzy się nad młotem zapobiega zapadnięciu się otworu oraz wciąganiu wody z otoczenia do odwiertu. To poprawia jego stabilność.
Zalety młotów tego rodzaju wynikają z właściwości wody. Przede wszystkim w porównaniu z powietrzem ma mniejszą ściśliwość. Oznacza to, że wymagana jest jednakowa objętość wody niezależnie od docelowego ciśnienia, natomiast im większe docelowe ciśnienie powietrza, tym odpowiednio większy musi być jego przepływ. Większe ciśnienie to większa liczba uderzeń na minutę. Przykładowo porównamy dwa młoty o jednakowym rozmiarze, pneumatyczny i wodny. Ten drugi, pracując pod ciśnieniem 180 barów zapewni 3600 uderzeń na minutę zużywając tylko 3‒6 litrów wody na sekundę, z kolei pneumatyczny zasilany sprężonym powietrzem o ciśnieniu zaledwie 30 barów, zapewniając tylko poniżej 2700 uderzeń na minutę, zużyje w tym celu aż około 100 razy więcej medium, pobierając około 350‒450 litrów powietrza na sekundę.
Kolejna różnica dotyczy sytuacji, w której otwór wypełni się wodą przesiąkającą z otoczenia – jej wypompowanie przez młot pneumatyczny może spowodować znaczący spadek ciśnienia roboczego. Oprócz tego sprężone powietrze, rozprężając się wnika w grunt w otoczeniu odwiertu, mogąc go uszkodzić. Z kolei młoty wodne nie wytwarzają pyłów ani nie wymagają smarowania. Pozwalają również na wykonywanie bardzo wąskich otworów, gdyż średnice żeber stabilizujących, a więc i prześwit między młotem a otworem, mogą być bardzo małe. Wynika to ze stosunkowo małej prędkości wody powrotnej (kilka m/s) w porównaniu z rozprężającym się powietrzem (kilkadziesiąt m/s), co wymusza dostępność większej przestrzeni do jego odprowadzenia. Młoty wodne są również dokładniejsze i pracują ciszej, gdyż jednostka udarowa jest umieszczona na dnie odwiertu.
Jak działa strug?
Praktykowane są różne sposoby podziemnej eksploatacji surowców. Popularną m.in. w kopalniach węgla w Europie jest metoda ścianowa. Korzysta się w niej z dwóch rodzajów maszyn górniczych, które różnią się techniką urabiania kopalin: kombajnów ścianowych albo strugów.
Głównymi komponentami maszyn drugiego typu są: korpus, głowica z końcówkami skrawającymi, przenośnik czołowy i napęd. Zasada działania strugów jest następująca: korpus z głowicą urabiającą jest przeciągany za pomocą łańcuchów wzdłuż transportera czołowego od początku do końca ściany przodka. Łańcuchy są wprawiane w ruch przez napędy, które są zabudowane na końcach maszyny. Równocześnie przenośnik, a razem z nim korpus i głowica, są dociskane do skały. To sprawia, że przy przesuwaniu struga wzdłuż przodka kolejne jej warstwy o określonej grubości są usuwane. Głębokość skrawania można zmieniać, regulując docisk głowicy do ściany.
W urządzeniach tego typu wprowadzane są specjalne rozwiązania konstrukcyjne wymuszane specyfiką ich zastosowania. Ważnym komponentem strugów jest korpus. Często możliwa jest zmiana jego wysokości przez dołączenie lub odłączenie bloków ostrzy skrawających i regulację podniesienia głowicy. Strug wyposaża się również w amortyzator. Tę funkcję pełni przykładowo elastyczne sprzęgło zamontowane w zespole ciągnącym. Dzięki temu maszyna pracuje płynniej, a łańcuch i napędy są mniej obciążone i wolniej się zużywają. Prowadnicę struga wykonuje się w formie odlewu, dzięki czemu jest wytrzymalsza. Jest również projektowana w taki sposób, żeby ograniczyć tarcie pomiędzy nią a łańcuchem i wbudowuje się w nią drzwiczki inspekcyjne, zapewniające łatwy dostęp do łańcucha. Strugi wyposaża się w napędy ze zmienną prędkością obrotową. Ważnym elementem jest ochrona przed przeciążeniem. W tym celu napęd wyposaża się w wielotarczowe sprzęgło z zespołem dociskowym, zapewniające moment obrotowy mniejszy niż ten zrywający łańcuch. W razie wykrycia poślizgu moment obrotowy przekładni jest od razu obniżany i jednocześnie wyłączane są silniki. Zapobiega to uszkodzeniu łańcucha.
Strugiem zwykle steruje się zdalnie. Dzięki temu operator nie musi przebywać w pobliżu wyrobiska w trakcie eksploatacji zasobów, podczas której warunki są dla niego niekorzystne. Zamiast tego może z bezpiecznej odległości, pod ziemią lub na powierzchni, ręcznie sterować maszyną albo nadzorować jej pracę w trybie automatycznym. Położenie głowicy jest określane przez monitorowanie ruchu łańcuchów. Ustawienia struga są regulowane w pionie i w poziomie za pomocą siłowników, wydłużanych i skracanych dla zwiększenia lub zmniejszenia głębokości skrawania. Dzięki temu jego przesuw odwzorowuje pofałdowania pokładu, co zmniejsza zużycie ostrzy i energii przy jednocześnie efektywnej eksploatacji dostępnych zasobów. Automatycznie korygowany jest także nadmierny lub niedostateczny nacisk, co zapewnia proste czoło przodka. Poza tym siłowniki zamontowane między przenośnikiem czołowym a wspornikiem stropowym na końcach chodnika kontrolują pełzanie transportera i zapewniają utrzymanie odpowiedniego naprężenia łańcucha struga.
Zagrożenia wybuchem w kopalniach![]() W kopalniach występuje atmosfera wybuchowa, czyli mieszanka palnych gazów, par, pyłów z powietrzem (w kopalniach węgla kamiennego głównie metanu i pyłu węglowego), w której po zainicjowaniu źródłem zapłonu spalanie będzie rozprzestrzeniać się samorzutnie. Przebywający w pobliżu są wówczas narażeni na działanie wysokich temperatur i fali uderzeniowej. Groźne są też przemieszczające się w niekontrolowany sposób resztki zniszczonych przez wybuch obiektów, brak tlenu oraz trujące produkty reakcji spalania. Dlatego zapobieganie eksplozjom jest kluczowe. Przede wszystkim nie wolno dopuścić do powstanie mieszanki wybuchowej. Tutaj warto wyjaśnić, że by substancja łatwopalna wytworzyła w połączeniu z powietrzem atmosferę wybuchową, muszą zostać spełnione określone warunki. Na przykład w przypadku pyłu węglowego musi on zawierać więcej niż 10% części lotnych w przeliczeniu na bezwodną i bezpopiołową substancję węglową i być odpowiednio rozdrobniony. Warunkiem koniecznym jest również, aby stężenie substancji łatwopalnej zawierało się pomiędzy dolną a górną granicą wybuchowości – w przypadku pyłu węglowego wartości graniczne to 50 g/m³ i 1000 g/m³. W obecności metanu wybuchowość pyłu węglowego jest większa. Na przykład przy 2% zawartości CH4 minimalne stężenie pyłu węglowego, przy którym powstanie mieszanka wybuchowa, wynosi 10 g/m³. By zapobiec wytworzeniu się atmosfery wybuchowej, powinno się więc przede wszystkim zapobiec zgromadzeniu się substancji łatwopalnej o odpowiednich właściwościach. W przypadku pyłu węglowego trzeba w tym celu m.in. stosować techniki urabiania węgla powodujące jak najmniejsze zapylenie, regularnie go usuwać, na przykład zmywając wodą i pozbawiać lotności przez zraszanie go wodą. |