- Jednym z tematów, który pojawił się podczas naszej poprzedniej rozmowy kilka lat temu, były kamery termowizyjne. Na początku 2007 roku pokazywaliście ich prototypy. Jak potoczyły się te sprawy?
Tematem tym zajmowaliśmy się od 2005 roku i doprowadziliśmy go do końca. Kamery produkowane były w seriach prototypowych i pokazywane na targach i wystawach branżowych. Zostały one całkowicie i od podstaw zaprojektowane przez naszych inżynierów, a ich głównym zastosowaniem, oprócz funkcji obserwacyjnych, były przemysłowe pomiary temperatury wszędzie tam, gdzie klasyczne metody pomiarowe zawodziły.
Uczestniczyliśmy w wielu bardzo ciekawych projektach z zakresu ochrony przeciwpożarowej, nadzoru obiektów hydrologicznych, w energetyce zawodowej przy diagnostyce urządzeń technicznych i technologicznych oraz w medycynie. Dla mnie oraz całego zespołu była to również fascynująca przygoda inżynierska.
Niestety życie sprawiło, że nie mogliśmy dalej kontynuować tego tematu. W tamtym czasie nastąpił gwałtowny wzrost zapotrzebowania na wykorzystanie termowizji w sektorze zbrojeniowym i na tym skupili się producenci niechłodzonych detektorów mikrobolometrycznych. Zmieniła się znacznie struktura cen kluczowych materiałów do produkcji oraz znacznie wydłużyły terminy ich dostaw. Producenci elementów optyki germanowej w USA czy Izraelu byli nastawieni wyłącznie na dostawy dla firm zbrojeniowych, a nasze potrzeby z rzadka realizowane były w terminie. Szybkie procesory do analizy obrazu były również poważnym problemem w zakresie zabezpieczenia materiałowego.
Z kolei krajowy rynek odbiorców okazał się zbyt płytki. Większość firm działających na rynku urządzeń termowizyjnych oferujących urządzenia do zastosowań przemysłowych faktycznie była i jest powiązana z przemysłem zbrojeniowym. W tamtym czasie na rynku pojawiły się także niskiej jakości bardzo tanie moduły kamer termowizyjnych produkowane w Chinach. My nie chcieliśmy i nie mogliśmy uczestniczyć w masowym rynku, gdzie oferowane były urządzenia najtańsze. Oczekiwaliśmy rozwoju sektora specjalistycznego, co nie nastąpiło.
Utrzymanie zespołu inżynierów konstruktorów, wysokiej klasy programistów oraz inżynierów sprzedaży stanowiło coraz większe obciążenie finansowe dla firmy. Przy braku sprzedaży na odpowiednim poziomie stało to u podstaw trudnej decyzji o wstrzymaniu realizacji tematu pomiarowej kamery termowizyjnej. Gorycz porażki nie przesłoniła nam potrzeby gruntownej analizy przyczyn popełnionych błędów. Wkrótce pojawił się w firmie nowy temat - pomiar wilgotności gazów. Z tym tematem związaliśmy swoją przyszłość.
- Skąd zainteresowanie higrometrią?
Całość zaczęła się wiele lat temu, kiedy na bazie dostarczonej dokumentacji technicznej uruchomiliśmy produkcję przetworników wilgotności gazów na rzecz angielskiej firmy Michell Instruments z Cambridge. Wszystkie elementy mechaniczne oraz elektronika były produkowane i montowane u nas, a gotowy przetwornik przed wysyłką był także kalibrowany temperaturowo.
W firmie Michell Instruments przylutowywany był detektor, a sam przetwornik poddawany procesowi kalibracji wilgotności i następnie wysyłany do klienta. My nie znaliśmy ani szczegółowych parametrów technicznych czy technologicznych detektorów, ani metod kalibracji wilgotności, gdyż stanowiło to ścisłą tajemnicę Michell Instruments. W tym okresie byliśmy jedynie rzetelnym kooperantem.
Na rzecz wymienionej firmy opracowaliśmy także elektroniczne moduły pomiarowe, które są dla nich produkowane do dnia dzisiejszego. Jednakże nasza wiedza i doświadczenie w zakresie pomiarów wilgotności gazów były niewielkie. Wkrótce po tym jak lider i założyciel Michell Instruments ją sprzedał, wzajemna współpraca w ciągu kilku lat praktycznie ustała.
Pewnego dnia zgłosili się do nas przedstawiciele japońskiej firmy z Tokio, którzy poszukiwali możliwości produkcyjnych i kooperacyjnych do swojego przetwornika wilgotności. Prawdopodobnie dowiedzieli się od przedstawicieli Michell Instruments, że przez wiele lat dostarczaliśmy jej szereg komponentów, w tym filtry ze spieków spawane wiązką elektronów w próżni. Filtry te notabene sprzedajemy im do dnia dzisiejszego.
Efektem podjętej współpracy było opracowanie i uruchomienie produkcji miernika wilgotności gazów z chłodzonym lustrem głównie na potrzeby japońskiego przemysłu motoryzacyjnego. Było to dla nas wielkie wyzwanie również w zakresie zapewnienia odbiorcy łatwej podmiany nowego oprogramowania w dowolnym miejscu na świecie poprzez pobranie go z Internetu zamiast wysyłania urządzenia do producenta w celu jego aktualizacji.
- Jak powstała idea produkcji nowych przetworników, które dzisiaj oferujecie na rynku?
Z byłym właścicielem Michell Instruments, Andrzejem Miczykiem, spotkaliśmy się kilka lat temu podczas warszawskich targów Automaticon. Powiedział mi wtedy, że pracuje nad całkowicie nowatorskim projektem detektora wilgotności gazów, którego nie udało mu się jednak wdrożyć w Michell Instruments. Wtedy postanowiliśmy połączyć wysiłki.
Firma Czaki Thermo-Product zaoferowała zaprojektowanie nowoczesnej wersji elektroniki pomiarowej oraz pełne przygotowanie produkcji nowego przetwornika z nowym detektorem, zaś Andrzej Miczyk - przeszkolenie naszych pracowników technicznych w zakresie pomiarów i systemów kalibracji wilgotności gazów, a także nadzór nad wykonaniem i konstrukcją systemu kalibracyjnego oraz oczywiście opracowanie i uruchomienie produkcji nowego detektora.
Wykorzystanie wiedzy i doświadczenia niekwestionowanego w świecie lidera w branży pomiarów wilgotności stało się podstawą do naszego wejścia w niszowe zakresy pomiarów wilgotności gazów od -100°Cdp do + 20°Cdp. Pomiary w tym zakresie oferuje jedynie kilka firm na świecie.
Na dzień dzisiejszy dysponujemy systemem kalibracyjnym opartym na definicji temperatury punktu rosy w zakresie -100°C do +20°C, którego nie powstydziłaby się nawet najbardziej wybredna jednostka metrologiczna. Detektory produkowane są w naszym laboratorium w Krakowie w oparciu o najnowsze zdobycze nanotechnologii. Elektronika przetwornika została również zaprojektowana z zastosowaniem najnowszych podzespołów elektronicznych. Przed nami jednak najtrudniejszy test - marketing na rynkach Europy, Azji oraz obu Ameryk.
- Czym różnią się pomiary wilgotności gazów od pomiarów temperatury?
Podstawową jednostką przy pomiarach wilgotności gazów jest temperatura punktu rosy - jest to taka temperatura, przy której następuje wyroszenie się pary wodnej w postaci kropelkowej lub drobnych kryształków szronu na gładkiej powierzchni. Higrometr z chłodzonym lustrem realizuje definicyjny pomiar wilgotności gazu.
Metalowe, wysokiej gładkości lustro pokryte złotem i rodem chłodzone jest przez ogniwo Peltiera, zaś nad lustrem przepuszczany jest badany gaz. System optyczny dokonuje ciągłej detekcji odbitego od powierzchni lustra światła. Z chwilą gdy promień światła zostaje rozproszony na wykroplonej rosie lub kryształkach szronu, detektor wysyła sygnał do układu elektronicznego w celu pomiaru temperatury panującej na lustrze.
![]() ![]() System do kalibracji czujników wilgotności |
Układ sterujący dokonuje ciągłego próbkowania, podgrzewając lub chłodząc naprzemiennie lustro, celem uzyskania możliwie najlepszej dokładności pomiaru. Wyświetlona wartość w stopniach Celsjusza jest miarą wilgotności bezwzględnej badanego gazu. Higrometry z chłodzonym lustrem umożliwiają dokładny pomiar wilgotności na poziomie ± 0,1°C punktu rosy, zaś typowy ich zakres pomiarowy wynosi od -40°Cdp do +60°Cdp.
W wersjach laboratoryjnych higrometry często wyposażone są w precyzyjne układy mikroskopowe do indywidualnej obserwacji powierzchni lustra celem prawidłowej oceny, czy mamy do czynienia z kryształkami szronu, czy wody przechłodzonej na powierzchni lustra w zakresie ujemnych temperatur. Detekcja wody przechłodzonej na lustrze to ważny problem, gdyż w praktyce określa się jedynie temperaturę punktu szronu.
Pomiar wilgotności gazu w przypadku, gdy na lustrze znajduje się woda przechłodzona, obarczony jest znacznym błędem pomiarowym, który może nawet wynieść 4°C punktu rosy. W naszej firmie udało się opracować specjalny system detekcji wody przechłodzonej na lustrze - dodatkowy detektor optyczny przekazuje informacje do procesora, ten zaś wylicza stosowną poprawkę.
- Jak wyglądają pomiary w oparciu o detektory pojemnościowe?
Pomiar wilgotności gazu ma w tym przypadku charakter pośredni, gdyż efektywnie mierzymy wartości pojemności detektora. Tym ostatnim jest specjalny kondensator, którego warstwa dielektryczna reaguje na zmianę wilgotności, zmieniając w efekcie pojemność elementu. Omawiany detektor wymaga wyskalowania względem rzeczywistych wartości wilgotności gazu na stanowisku w laboratorium.
Pojemnościowe detektory wilgotności z dielektrykiem polimerowym produkowane są na masową skalę i można je spotkać zarówno w prostych termo-higrometrach możliwych do kupienia w każdym supermarkecie, jak też w wielu urządzeniach przemysłowych. Jednakże detektory tego typu nie dają możliwości pomiaru wilgotności w niskich zakresach poniżej -50°Cdp. Tylko nieliczni producenci na świecie oferują detektory pojemnościowe z dielektrykiem Al2O3 na najniższe zakresy wilgotności od -120°Cdp do +20°Cdp.
![]() ![]() Projektowanie i produkcja |
Te ostatnie - detektory na bazie Al2O3, mają jednak liczne ograniczenia. Ich reakcja jest powolna, a one same narażone są na dryf, czego skutkiem muszą być często rekalibrowane. Z kolei detektory naszej firmy wykorzystują nową technologię Bi-Ceramic Technology, która znacznie przyspiesza czas reakcji i eliminuje potrzebę częstej rekalibracji dzięki wysokiej stabilności parametrów w czasie.
Dodam, że możliwość pomiaru w niskich zakresach wilgotności gazów ma kluczowe znaczenie w wielu branżach, takich jak przemysł farmaceutyczny, chemiczny, metalurgiczny czy półprzewodnikowy. Przetworniki takie wykorzystywane są również w energetyce, branży spożywczej, a także w przemyśle lotniczym i zbrojeniowym.
- Jakie są cechy szczególne wytwarzanych przez Was detektorów?
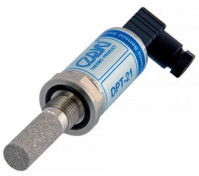
Przetwornik wilgotności gazów produkcji Czaki Thermo-Product
Na początek poddaliśmy analizie cechy detektorów produkowanych przez konkurencję. Okazało się, że głównym problemem jest wspomniana niestabilność czasowa parametrów detektora oraz zbyt wolna reakcja na zmiany wartości mierzonej wilgotności. Analizie poddany został również cały proces technologiczny wytwarzania pojemnościowych detektorów wilgotności.
Od wielu lat w ich przypadku do wytworzenia warstwy reagującej na wilgoć stosowany był dwutlenek aluminium (Al2O3) lub polimery. Niestety polimery mają zbyt małą czułość, aby mogły być stosowane w niskich zakresach. Z kolei detektory na bazie dwutlenku aluminium wytwarzane w procesie anodowania i trawienia aluminium mają warstwę reagującą na zmiany wilgotności o grubości 1000 nanometrów.
Grubość warstwy jest głównym czynnikiem powodującym, że czas reakcji w niskich zakresach wilgotności jest bardzo długi. Dodatkowym problemem jest powolny proces chemicznej przemiany Al2O3 w wodorotlenek aluminium, co objawia się długotrwałym dryftem parametrów detektora. Proces chemicznego dryftu detektora może trwać nawet ponad rok lub dłużej. Sytuacja ta wymaga więc częstej rekalibracji czujników.
Opracowany przez naszych inżynierów detektor pojemnościowy stanowi przełom technologiczny w konstrukcji detektorów wilgotności gazów. Jest on wykonany w technologii cienkowarstwowej z zastosowaniem najnowszych osiągnięć nanotechnologii. Detektor bi-ceramiczny ma dwie specjalne warstwy ceramiczne wykonane w technologii Low Temperature Co-fired Ceramics (LTCC).
Pierwsza warstwa o grubości 10 nm stanowi barierę izolacyjną i odpowiada za wysoką rezystancję wewnętrzną detektora wynoszącą około 2 MΩ. Dzięki niej udało się także zmniejszyć grubość warstwy czynnej reagującej na zmiany wilgotności. Skróciło to zdecydowanie czas odpowiedzi detektora na zmianę wilgotności. Druga warstwa o grubości 24 nm jest wspólnie wypalana - stąd określenie co-fired - z pierwszą. Warstwa ta, dzięki specjalnej recepturze, szybko reaguje na zmianę wilgotności, co powoduje zmianę pojemności detektora. Takie rozwiązanie zapewnia również wysoką stabilność parametrów w funkcji czasu.
Prace nad detektorem wymagały stworzenia własnego laboratorium pomiarowego wyposażonego w najnowszej generacji napylarkę próżniową, aparaturę pomiarową oraz niezbędny sprzęt i wyposażenie do badań chemicznych. Badania w naszym laboratorium w Krakowie trwały w sumie kilka lat. Po wielu próbach udało nam się dokonać optymalizacji parametrów technologicznych procesu wytwarzania detektorów bi-ceramicznych. Z kolei badania dokonane w niezależnych laboratoriach w Paryżu i Tokio potwierdziły nasze wyniki. To była ogromna satysfakcja dla nas, ale też jednocześnie wyzwanie na przyszłość związane z marketingiem tego produktu.
- Dziękujemy za rozmowę.