- Elmodis jest firmą o kilkuletniej historii, którą można by w zasadzie określić mianem start-upu. Szybko jednak jej działalność przybrała formę regularnego, dynamicznie rozwijającego się przedsiębiorstwa. Skąd pomysł na zajęcie się tematyką diagnostyki i predykcji pracy maszyn?
Koncepcja ta narodziła się na początku zeszłej dekady, gdy w trakcie pisania rozprawy doktorskiej zacząłem myśleć o produkcji nowoczesnych systemów do pomiarów elektrycznych. Badałem wtedy sposoby zastąpienia dotychczasowych metod pomiarowych z wykorzystaniem drgań - bardzo kosztownych i trudnych w utrzymaniu w warunkach przemysłowych, pomiarami elektrycznymi.
Wcześniej przez wiele lat zajmowałem się diagnostyką techniczną, przy czym rozumianą znacznie szerzej niż to, co robimy obecnie. Były to zarówno badania nieniszczące (NDT, non-destructive testing), jak też te związane z pomiarami drgań oraz wnioskowaniem na ich podstawie w oparciu na różnego rodzaju pomiarach wibroakustycznych.
Tego typu implementacje wykonywane w realnym przemyśle natrafiają na mnóstwo problemów. Dopóki bowiem pracuje się w obszarze badawczo-rozwojowym, wszystko działa nieźle. Kiedy jednak przygotowuje się konkretne aplikacje dla branży petrochemicznej, chemicznej czy górniczej, jak to przez wiele lat miało miejsce w naszym przypadku, to implementacja czujników drgań i systemów wibroakustycznych okazuje się bardzo trudna. Wtedy w grę wchodzą wymagania bezpieczeństwa oraz kwestie niezawodnościowe związane z ciężkimi warunkami pracy, z działaniem substancji chemicznych, często agresywnych, czy też możliwością występowania uszkodzeń mechanicznych. Jeśli w oparciu na takim systemie w realnych, przemysłowych warunkach rzeczywiście implementujemy diagnostykę i wspieramy proces utrzymania maszyn, pojawia się więcej problemów z samym układem monitorowania niż z maszyną. Okazuje się również, że utrzymanie takich systemów zaczyna być bardzo drogie.
Po tych doświadczeniach powstał pomysł, częściowo na bazie wspomnianej rozprawy doktorskiej, zastosowania pomiarów elektrycznych do monitorowania i diagnostyki stanu maszyny, tak aby nie dołączając dodatkowych czujników, móc wykorzystywać pomiary elektryczne. Potem okazało się, że takie podejście ma dodatkowe zalety, bowiem parametry elektryczne można bardzo łatwo korelować z procesem, sprawdzając, jak obciążenie, obszar rzeczywistej pracy, ale też proces i otoczenie zewnętrzne wpływają na stan oraz efektywność maszyny.
- Czy omawiana koncepcja była dekadę temu nowością? Dzisiaj coraz więcej producentów maszyn czy silników dodaje do nich również moduły diagnostyczno-pomiarowe…
Tak, w tamtym okresie była to rzecz nowa, choć teoria MCSA, będąca jedną z podstaw naszego rozwiązania, była już znana, a jej podwaliny powstały w latach 70. zeszłego wieku. Jej implementacja miała wówczas ograniczenia techniczne wynikające z kwestii wystarczająco wydajnego liczenia parametrów w czasie rzeczywistym. Na szczęście kilka lat temu okazało się, że nowe generacje procesorów mają już wystarczającą do tego celu moc obliczeniową.
Należy też zauważyć, że jeżeli liczymy parametry z przebiegów próbkowanych w wielu kanałach z częstotliwościami od kilku do kilkudziesięciu kHz, musimy przetwarzać ogromne ilości danych. Ich przesyłanie do chmury lub serwera jest bardzo uciążliwe i kosztowne, więc wdrożyliśmy tu nasz pomysł, którym jest wydajne przetwarzanie lokalne (tzw. brzegowe, krawędziowe). Ten przeskok technologiczny pozwolił na to, aby większość obliczeń, szczególnie czasu rzeczywistego, realizować przy maszynie.
Ponadto zwiększająca się dostępność i akceptacja chmur obliczeniowych, a także rozwój IoT spowodowały, że dane rzeczywiście można już było zbierać i analizować długoterminowo, robiąc przy okazji analizy porównawcze (benchmarkowe). Bez chmury lokalne serwery generowały mnóstwo problemów z wydajnością, zarządzaniem i komunikacją. Oczywiście samo przesyłanie danych nie bardzo nas interesowało - chodziło raczej o to, żeby stworzyć i wykorzystać narzędzia, które wspiera rewolucja cyfrowa.
- Czy jest Wam dzisiaj bliżej do producenta, integratora, projektanta, czy może patrzycie na siebie po prostu jako na dostawcę rozwiązań?
To bardziej złożony temat. Jesteśmy producentem i dostawcą kompletnego systemu, czyli sprzętu pomiarowego wraz z oprogramowaniem edge i cloud, który od początku istnienia firmy sami projektowaliśmy oraz produkowaliśmy - głównie ze względu na konieczność specyficznego sposobu prowadzenia pomiarów, cyfrowego przetwarzania sygnałów oraz uzyskiwania danych wysokiej jakości. Jednocześnie na początku działalności wdrażaliśmy rozwiązania u klientów końcowych, tak aby poznać problemy zarówno ich samych, jak też te związane z implementacją naszego systemu. Celem była też możliwość iteracyjnej poprawy oferowanych systemów.
Obecnie współpracujemy z partnerami wdrażającymi i integrującymi nasze rozwiązania u swoich klientów, zapewniającymi odpowiednie narzędzia, szkolenia i wsparcie. Kładziemy również duży nacisk na współpracę z OEM-ami, która daje konkretną wartość dla tych firm i ich klientów, nam zaś pozwala planować wzrosty sprzedaży.
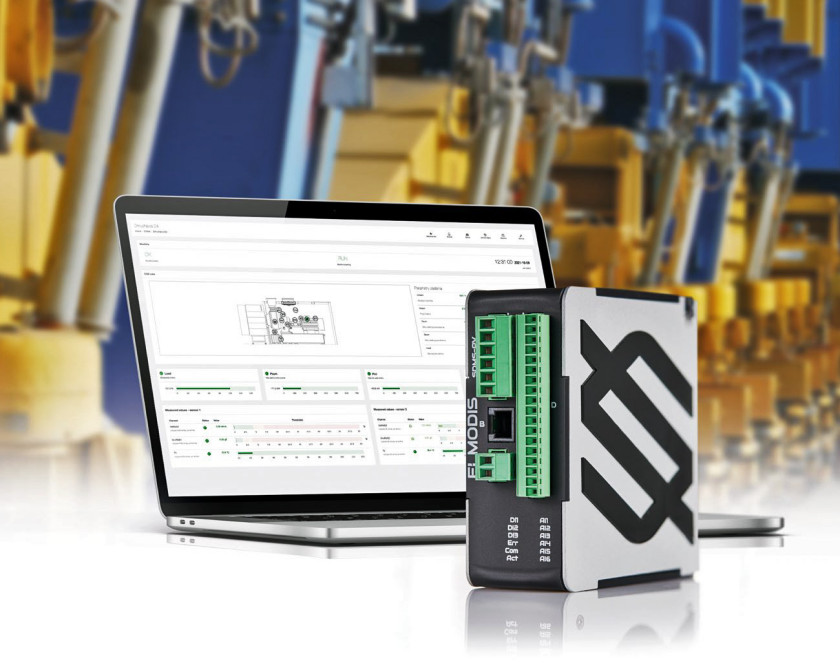
Wdrażanie omawianych systemów zawsze wymaga dostosowania się do harmonogramu pracy danego zakładu przemysłowego - do zaplanowanej w nim przerwy technicznej czy remontowej, kiedy można dostać się do linii produkcyjnej, aby zainstalować nowe urządzenia pomiarowe. To nie jest proste i dlatego zajmują się tym partnerzy, np. firma Partner Serwis, która w ramach swojej usługi opartej na systemie Elmodis - Maintenance 365, utrzymuje również maszyny i systemy przemysłowe. Specjaliści Partner Serwis, na bazie informacji z naszego systemu, są w stanie pomóc użytkownikom wyremontować i wyregulować maszyny, a także zapewniają kompleksową obsługę serwisową. Dzięki tego rodzaju współpracy możemy też zwiększyć liczbę instalowanych systemów. A ponieważ mamy podobnych partnerów również w innych krajach, np. Stanach Zjednoczonych czy Japonii, to liczba klientów stale się zwiększa. Nasza baza cały czas znajduje się przy tym w Polsce i nie musimy tworzyć dużych struktur korporacyjnych.
Co ciekawe, wśród zagranicznych partnerów są również producenci sprzętu, tacy jak japońska korporacja Meidensha, która jest też naszym inwestorem strategicznym. Głównym obszarem ich oferty jest wytwarzanie silników oraz zaawansowanych systemów elektrycznych. Współpraca z Meidensha Corporation to przykład synergii producenta z dostawcą techniki pomiarowej.
Dodam, że rynek przemysłowy jest w około 85% rynkiem maszyn starych, działających od wielu lat, a tylko 15% to urządzenia nowe. Jednak łatwość integracji i przygotowania rozwiązania wraz z producentem maszyn, który potem dokłada nasze rozwiązanie z software'em i wytwarza np. kilka tysięcy sztuk maszyn rocznie sprawia, że tyle samo naszych systemów trafia też do klientów końcowych.
- Czy to, że jesteście ściśle powiązani z partnerami, sprawia, że trudniej jest zaistnieć u innych, dowolnych producentów maszyn?
Możemy dostarczać rozwiązania do różnych odbiorców, ale to i tak wiąże się ze współpracą z partnerem, który ma zdefiniowaną politykę związaną z naszymi produktami. Musimy wspólnie przejść proces integracji z maszyną, uczenia i wykrywania tego, czego nasz partner rzeczywiście oczekuje (lub jego klienci), a potem to u niego wdrożyć. Przykładowo z partnerem japońskim pracujemy już ponad trzy lata. Pamiętajmy, że to nie tylko kwestia związana z dołożeniem pudełka i dostępem do platformy, ale też optymalizacją kosztów dla konkretnej aplikacji OEM.
Ogólnie mówiąc, nasza sprzedaż - czy to zagraniczna, czy na polskim rynku - wiąże się przede wszystkim z partnerami oraz integratorami, a w znacznie mniejszym stopniu korzystamy z kanałów sprzedaży bezpośredniej.
- Czy od początku mieliście globalny plan działań, tj. jako specjaliści obsługujący klientów z różnych krajów?
Tak, od początku myśleliśmy o ekspansji globalnej - i to z dwóch powodów. Po pierwsze zebraliśmy pod egidą Elmodisu doświadczony zespół, mający na koncie długą współpracę z klientami przemysłowymi w Polsce. Po drugie znaliśmy ograniczenia i problemy wynikające z działań w kraju, w tym ze spółkami skarbu państwa. Uważaliśmy, że mogłyby one znacznie efektywniej wykorzystywać rozwiązania z obszaru cyfryzacji. Po trzecie znaczenie miały też różne budżety, którymi dysponowały firmy w Polsce i za granicą. Stąd też nasze pierwsze kroki w poszukiwaniu zleceń skierowaliśmy do Stanów Zjednoczonych i Europy Zachodniej. W obszarze naszych zainteresowań znalazła się też współpraca z kalifornijskim instytutem EPRI (Electric Power Research Institute), do którego trafiali również amerykańscy klienci.
- Porozmawiajmy o dostarczanych przez Was rozwiązaniach. Co one obejmują?
Naszą ofertę tworzą przede wszystkim: specjalistyczny hardware, Distributed Edge Computing, czyli system rozproszonych obliczeń brzegowych/krawędziowych z wbudowanym zaawansowanym DSP (Digital Signal Processor) i ML (Machine Learning), bezpieczna komunikacja oraz rozwiązania chmurowe z możliwością analizy długoterminowej, predykcji stanu oraz analizy porównawczej dotyczącej wielu maszyn, które umożliwiają też optymalizację procesów utrzymania. Dodatkowym elementem są usługi związane z optymalizacją operacyjną i energetyczną, znacznie wydłużające bezobsługową eksploatację maszyn.
- Skąd pochodzą dane?
Większość danych pozyskujemy z pomiarów elektrycznych, tj. prądu i napięcia, wyliczając kilka tysięcy różnych wskaźników i parametrów. W szczególnych przypadkach uzupełniamy je o dane pomiarowe z pomiarów wibracyjnych oraz procesowych, takich jak temperatura, ciśnienia, przepływy, tak aby zapewnić kompletny obraz zarówno procesu, jak i maszyny. Wymienione wskaźniki z jednej strony pokazują stan bieżący, z drugiej są wsadem dla zaawansowanych algorytmów predykcji i optymalizacji. Co najistotniejsze - umożliwiają wykorzystanie algorytmów ML i AI (sztucznej inteligencji) do wypracowania optymalnych obszarów pracy. To z kolei pozwala na znaczne wydłużenie czasu bezobsługowego i bezawaryjnego działania maszyn, jednocześnie dostarczając możliwości optymalizacji energetycznej.
Nasz moduł brzegowy (edge module), który dołączamy do maszyny, zapewnia możliwość pozyskiwania danych o odpowiednio wysokiej jakości. Część informacji pochodzących z już istniejących w zakładach systemów jest obarczona wieloma problemami i błędami, przede wszystkim związanymi z synchronizacją oraz niewystarczającą rozdzielczością czasową. Gdy zestawy danych są składane z różnych systemów lokalnych, nieraz okazuje się, że ich różna rozdzielczość czasowa i słabo opisane warunki dodatkowe utrudniają wiarygodne wykorzystanie. Dlatego zdecydowaliśmy się na przygotowanie własnego sprzętu pomiarowo-obliczeniowego, który zapewnia zarówno wysoką jakość danych, jak też ich zaawansowane przetwarzanie w informacje. A to z kolei później przekłada się na odpowiednio wysokiej jakości efekty.
- Jak w praktyce wygląda wdrażanie takich rozwiązań? Czy klient musi wykonać dużo wstępnych dostosowań i zmian?
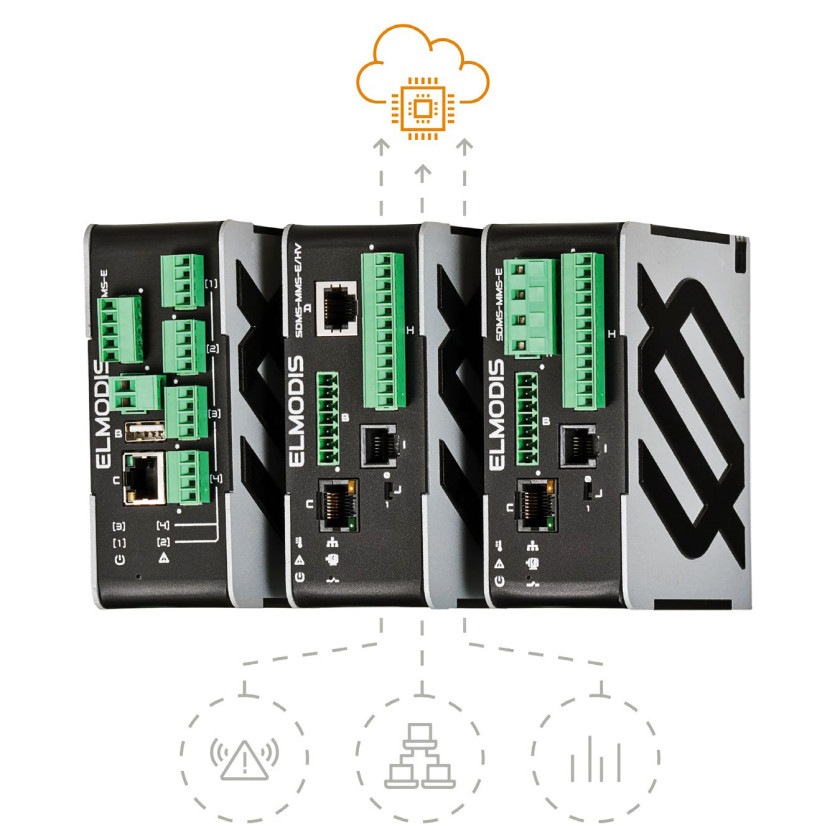
Nie, większość integracji odbywa się bez znaczącej ingerencji w istniejące systemy elektryczne - montaż czujników prądu i inne podłączenia nie są zbyt inwazyjne. Pomiary prądów wykonujemy bez rozłączania obwodów, podłączamy się do odpowiednich miejsc w celu pomiarów napięć, włączamy zasilanie i w zasadzie system w tym momencie zaczyna działać. Czasem konieczne jest zainstalowanie dodatkowych czujników dla zapewnienia odpowiedniego obrazu pracy maszyn w linii technologicznej. Nieraz też integrujemy moduły edge z istniejącymi systemami, np. ze sterownikami PLC czy oprogramowaniem SCADA, tak aby pozyskiwać wymagane, a już posiadane dane. To z kolei wymaga zaplanowania integracji. Przykładowo dla przepompowni mającej na wyposażeniu pięć do dziesięciu pomp zabiera to kilka dni oraz wymaga przygotowania kompletnej dokumentacji na potrzeby wdrożenia.
Przykładowo u klientów takich jak Saint Gobain, u których wdrożyliśmy nasz system i monitorujemy kilkadziesiąt maszyn podobnego typu, podłączenie kolejnej to głównie kwestia integracji mechanicznej oraz elektrycznej. W zakresie konfiguracji działamy na tzw. predefiniowanym szablonie. Do zdefiniowanej wcześniej maszyny z dostępnymi już parametrami podłączamy nową. Wprowadzamy wówczas do systemu tylko typ urządzenia, po czym z chmury trafiają pakiety oprogramowania do urządzeń krawędziowych. W ten sposób cały proces się skraca i nie ma potrzeby czasochłonnej konfiguracji.
Oczywiście w przypadku zupełnie nowych typów urządzeń lub bardziej złożonych maszyn musimy krok po kroku skonfigurować wszystkie parametry, zdefiniować panele wizualizacyjne (dashboards) oraz wygląd raportów dla klienta. Od strony konfiguracyjnej zajmuje to już od kilku godzin do nawet kilku dni, jeśli mówimy o dużym systemie - i to zanim zacznie on wysyłać dane!
Dobrym przykładem dużej optymalizacji był nasz projekt realizowany wspólnie z MPWiK Wrocław. Dotyczył on dużej liczby urządzeń oraz pomiarów, zaś w celu uzyskania konkretnych wyników potrzeba było aż roku pracy połączonych zespołów Elmodis oraz MPWIK. W zakresie prac realizowana była analiza danych, weryfikacja zastosowanych algorytmów, walidacja wyników. Wprowadzone w efekcie projektu modyfikacje sposobu obsługi oraz procesu technologicznego doprowadziły w 2020 roku do uzyskania aż 1,6 mln zł oszczędności na samej energii, zredukowania kosztów serwisowych, a także znaczącego wydłużenia czasów pomiędzy przestojami serwisowymi maszyn.
- Czyli najpierw system zapewnia dane i informacje i dopiero na ich podstawie są podejmowane decyzje o zmianach czy optymalizacji?
Najpierw system analizuje obszary i rozrzuty parametrów monitorowanych urządzeń, wskazując, które z nich przekraczają oczekiwany, wyuczony zakres - i to jest podstawa do wykrywania anomalii. Na bazie długoterminowych analiz możliwe jest estymowanie (predykcja) zmian parametrów w czasie. Dodatkowo, biorąc pod uwagę wyniki analiz danych, obszarów obciążeń oraz ich zmienności, pracujemy z klientem i prezentujemy ścieżkę obejmującą szczegółowo zdefiniowane oraz możliwe do implementacji optymalizacje. Kolejny etap to iteracyjna weryfikacja oraz modyfikacje analizy i wprowadzanych ustawień, co finalnie prowadzi do osiągnięcia założonego efektu.
- Czyli zasadniczo mówimy tu o dwóch obszarach - jeden to diagnostyka, monitorowanie i predykcja stanu, a drugi to ciągła poprawa funkcjonalności i optymalizacja…
Tak, system wspiera decyzje dzięki dedykowanym narzędziom do wykrywania anomalii, a także oceny i predykcji stanu. Takie anomalie mogą być związane ze stanem technicznym elementów maszyn (np. uszkodzenia łożysk czy typowe dla maszyn wirnikowych niewyważenia lub rozosiowania), jak też zachowaniem maszyn będącym wynikiem zmian w procesie (np. wykrywanie nieszczelności w układach poprzez analizę zachowania kompresora). Dotyczy to więc nie tylko stanu technicznego maszyn, ale też procesów, dając możliwość kompleksowego wykrywania anomalii. A to z kolei stanowić może podstawę procesów optymalizacji.
- Czy takie anomalie są zawsze czymś indywidualnym, czy czasem są też standardowe, spodziewane?
Jeśli mamy do czynienia z maszynami takimi jak wentylatory albo pompy, to wiemy, jak zdefiniować ich typowe uszkodzenia - np. niewyważenie czy uszkodzenie wirnika. Takie wydarzenia mają swoje odzwierciedlenie w określonych wskaźnikach, które wyliczamy i używamy do uczenia systemu. Standardowe uszkodzenia możemy więc już wykrywać na wstępnym etapie wdrożenia.
System monitoruje jednocześnie kilkaset albo kilka tysięcy wskaźników, które wykorzystywane są w procesie analizy stanu maszyny. Mogą one zachowywać się typowo, ale też w pewnych warunkach generować sygnały wskazujące na anomalię. I nie umiemy tutaj bez dalszych analiz oraz współpracy z klientem określić ich przyczyn. Wspólnie ustalamy, czy zaszło coś zamierzonego - np. w procesie zmieniono temperaturę, czy jednak trzeba sprawdzić działanie monitorowanej maszyny i zdefiniować w systemie anomalię jako konkretną usterkę.
- To zakłada stałą współpracę z odbiorcami już po zainstalowaniu systemu. Czy podpisujecie umowy usługowe?
Współpraca z klientami i użytkownikami oraz ich wspieranie to konieczny element rozwoju naszego systemu. W zakresie dodatkowych usług, jak już wcześniej mówiłem, współpracujemy z partnerami wspierającymi wykorzystanie systemów u klientów końcowych. Procesy uczenia systemu nowymi zdarzeniami oraz uwagi użytkowników staramy się integrować jako nowe funkcjonalności naszego rozwiązania. Jeśli chodzi o duże zmiany konfiguracji czy parametrów, to staramy się wkraczać z nimi dopiero wtedy, gdy pojawia się bardziej złożony przypadek.
- A więc klient musi dysponować dobrymi narzędziami i być przeszkolony…
Oczywiście. W końcu jeśli ktoś instaluje nasze rozwiązania dla kilkudziesięciu czy kilkuset urządzeń, to zdecydowanie chce wiedzieć, jak z nich korzystać. W niektórych aplikacjach wykrywamy zdarzenia niezwiązane z procesem, a jednak wymagające naszej interwencji. Przykładowo zmiany temperatury otoczenia mogą powodować nietypowe zachowania i skutkować wykryciem niezdefiniowanej anomalii. I w takim przypadku potrzebna jest dodatkowa informacja od użytkownika o zmianie parametrów pracy.
- Czy rynek na tyle już się zmienia, że klienci sami poszukują rozwiązań, jakie oferujecie, czy raczej musicie je aktywnie promować, uświadamiając odbiorców?
Dostrzegam tu dwa aspekty. Na pewno widać coraz większą akceptację dla rozwiązań takich jak IoT czy chmura, a także zrozumienie, że digitalizacja ma już stałe miejsce w przemyśle. Świadomość ta jest znacznie większa niż pięć czy sześć lat temu. Aczkolwiek jednocześnie ciągle niewielka część polskich przedsiębiorstw ma konkretne, przemyślane plany wdrożenia tego typu systemów. Z mojego doświadczenia z ostatnich lat wynika, że jeśli tego typu system nie jest wpisany w większą strategię digitalizacji firmy, to jego kompleksowa implementacja się nie uda. Zakładowy diagnosta może wprawdzie stwierdzić, że chciałby mieć system diagnostyczny, ale jeśli przedsiębiorstwo nie wypracowało strategii wdrażania dobrze zdefiniowanych rozwiązań, to wcześniej czy później będzie problem. Dodam, że gdy chcieliśmy wejść do polskich dużych firm, gdzie widzieliśmy określone potrzeby, to na którymś etapie okazywało się, że brakuje jakiegoś ogniwa lub po prostu nie ma na to budżetu. A cokolwiek by mówić – cyfryzacja wymaga inwestycji.
- Z kim najczęściej współpracujecie?
Zacznę od tego, z kim chcieliśmy współpracować - były to polskie spółki państwowe. Gdy przygotowywaliśmy dla nich oferty, przeważnie cały projekt już na starcie rozbijał się o to, że przedsiębiorstwa te wszystko mają, wszystko wiedzą i nic dodatkowego im nie potrzeba. Jedną z firm, co do której z pełnym przekonaniem mogę powiedzieć, że miała dobrze zdefiniowaną strategię digitalizacji, był Tauron. Wspólnie pracowaliśmy w ramach wspieranego przez nich akceleratora. Zrobiliśmy tam kilka ciekawych projektów pilotażowych i wydawało się, że będzie to dobry kierunek prowadzący do udanego wdrożenia. Nie udało się. Niestety dość typowe w tego typu spółkach zmiany personalne na poziomie zarządu oraz związane z nimi zmiany strategii korporacyjnych nie działają korzystnie na współpracę z niedużymi spółkami technologicznymi i startupami.
W przypadku gospodarek zachodnich widzę otwarcie i dużą akceptację dla rozwiązań takich jak te wytwarzane przez Elmodis, a więc związanych z digitalizacją i wsparciem optymalizacji eksploatacji maszyn oraz procesów. Przykładem może być branża wodno-kanalizacyjna z systemami pompowymi pracującymi w trybie ciągłym, które dostarczają wodę lub odprowadzają ścieki. W Polsce również dostrzegam spore możliwości w tym sektorze. Wspominałem o udanym projekcie na rzecz MPWiK Wrocław. Według mnie to przedsiębiorstwo stanowi absolutną awangardę w tym obszarze i wyznacza trendy, które będziemy obserwować w kolejnych latach u innych operatorów.
W branżach produkcyjnych, w zależności od przyjętej strategii i poziomu dojrzałości techniczno-technologicznej, jest różnie. W części zakładów produkcyjnych działa bardzo różnorodny sprzęt i wtedy wdrażanie naszych rozwiązań na dużą skalę staje się bardzo kosztowne. Związane jest to z koniecznością indywidualnych wdrożeń dla prawie każdej maszyny. Jednocześnie jako że obecnie składnik kosztowy związany ze zużyciem energii staje się bardzo istotny, wiele firm szuka - oprócz systemów wspierających utrzymanie maszyn - również narzędzi do poprawy efektywności energetycznej. Łatwo obliczyć, że przy obecnych kosztach energii oraz roboczogodzin optymalizacja na poziomie kilkunastu procent przekłada się nieraz na oszczędności rzędu dziesiątek lub setek milionów złotych.
- A czy problemem z wejściem do dużych i ciekawych zakładów jest to, że współpracują one tylko z określonymi dostawcami i nie decydują się na rozwiązania firm trzecich?
Jeśli chodzi o systemy sterowania - pewnie tak jest, jednak w przypadku systemów diagnostyki i optymalizacji duże firmy zazwyczaj przekonują się funkcjonalnością. Z reguły sprawdzają najpierw pilotażowe rozwiązania kilku dostawców i weryfikują ich działanie. Wtedy walka jest czysto merytoryczna.
- Co z otwartością systemów, możliwościami ich integracji i rozbudowy?
Dzisiaj klienci oczekują otwartości i optymalizacji - nie chodzi o jednorazowe wydarzenie, wdrożenie, ale o proces, który trzeba zmieniać, obserwować, modyfikować. Stąd też tak istotne jest, aby urządzenia monitorujące pracę i stan maszyn były inteligentne, zaś ich software uczył się dzięki mechanizmom machine learning. Zapewniamy też modyfikacje oprogramowania oraz dodawanie nowych funkcjonalności. Ponadto chmura daje możliwości porównywania parametrów tego samego typu maszyn i wyławiania tych jednostek, które mają problemy. Zapewnia to znaczne skrócenie procesu decyzyjnego w obszarze utrzymania u klientów.
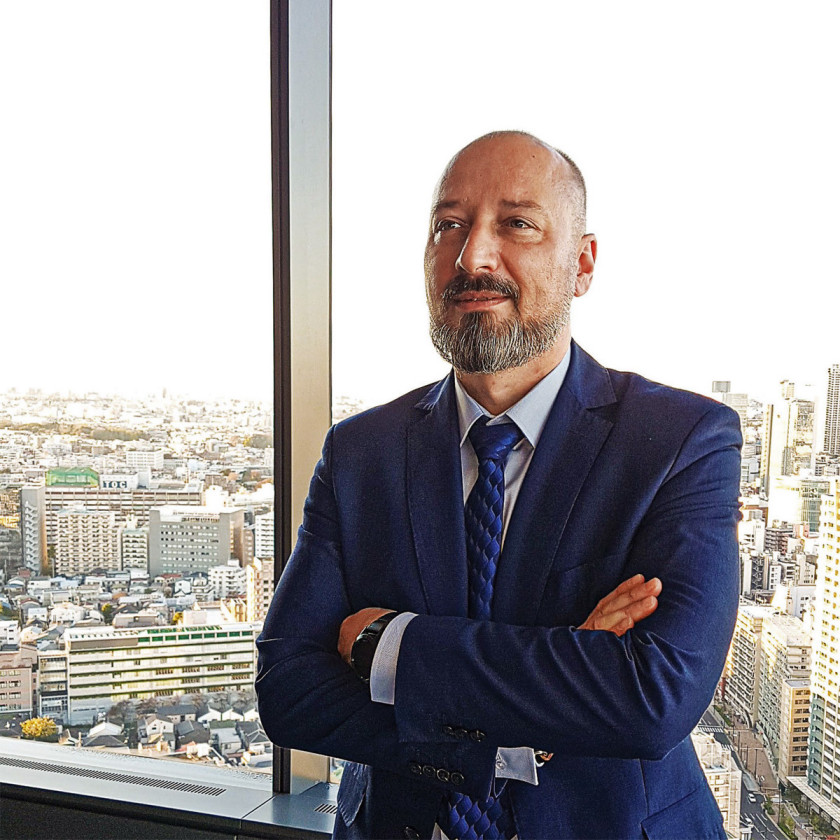
Liczba osób zajmujących się w zakładach produkcyjnych diagnostyką i utrzymaniem od wielu lat systematycznie maleje, coraz częściej zadania te są outsourcowane. Nieraz na miejscu zostaje tylko zredukowany zespół, który nie ma czasu na czasochłonną analizę danych z maszyn. W dodatku liczba wykwalifikowanych diagnostów spada - i dotyczy to całej Europy. Ciężar podejmowania decyzji musi więc spoczywać na dobrych, sprawdzonych narzędziach pomiarowych, analitycznych oraz finalnie raportujących. Staramy się ograniczyć ilość pierwotnych danych pomiarowych, często nieistotnych i niezrozumiałych dla użytkownika, skupiając się na podawaniu przetworzonych informacji, istotnych z punktu widzenia podejmowania decyzji.
Dodam, że właściwie od samego początku tworzyliśmy nasze rozwiązania tak, aby móc udostępniać i integrować dane z i do istniejących systemów. Jesteśmy na to otwarci, chcemy łączyć się z innymi systemami cyfrowymi na poziomie shop floor. Synergia z tego wynikająca może bowiem przynosić znaczącą wartość dla klientów. Z drugiej strony, jeżeli ktoś ma zamiar korzystać ze swoich danych i trzymać je we własnym oprogramowaniu SCADA czy systemem nadrzędnym - również zapewniamy taką możliwość.
- Czym dzisiaj się zajmujecie, jeżeli chodzi o technologie?
Zajmuje nas przede wszystkim aspekt związany z komunikacją i sposobem przetwarzania, czyli starcia się koncepcji edge oraz cloud computing. Z jednej strony mamy na rynku wszelkiego rodzaju wąskopasmowe, bardzo wydajne i niskokosztowe systemy komunikacyjne z rozproszonym obliczaniem. Z drugiej strony istnieją zaawansowane rozwiązania chmurowe proponowane przez firmy Google, Microsoft czy Amazon. Z tymi ostatnimi wiążą się nowe sieci komunikacyjne, bo do korzystania ze skupionego przetwarzania chmurowego potrzeba interfejsów szerokopasmowych takich jak np. 5G.
W naszej działalności koncentrujemy się na inteligentnych modułach brzegowych, bowiem jesteśmy w tym przypadku mniej zależni od dostępności i jakości możliwości komunikacji, z którą w przemyśle bywa bardzo różnie. Dostęp do sieci nie zawsze jest dobry i nie zawsze jest ona szerokopasmowa, tymczasem my generujemy naprawdę duże ilości danych. W dodatku uważamy, że bezpieczeństwo oraz szybkości reakcji są dużo większe, gdy obliczenia wykonujemy tuż przy maszynie, niż gdy korzystamy z szerokopasmowych sieci komunikacyjnych i chmury. Przykładem jest reakcja na zdarzenia takie jak blokada wirnika pompy albo kawitacja, z którymi nie można czekać, aż chmura dostanie dane, przetworzy je i wyśle do systemu. Potrzebna jest szybka informacja i współpraca z systemem sterowania - inaczej pompa zostanie uszkodzona. Stąd też interakcja związana ze zgłoszeniem zdarzenia i wysłaniem sygnału do PLC musi odbywać się na poziomie krawędzi systemu (edge computing).
Powyższe rozwiązanie daje nie tylko większe możliwości, ale też obniża koszty. W cyfryzacji długoterminowo istotne są bowiem wydatki związane z przemysłową komunikacją chmurową. Opłata za chmurę, za przechowywanie danych czy za komunikację 5G może być dzisiaj ogromna. Wtedy też cały system całościowo staje się mniej atrakcyjny dla klienta. Stąd też prowadzimy prace nad optymalizacją wykorzystania części edge oraz cloud, a także zapewnianiem takiego rozwiązania, aby było ono nie tylko skuteczne technicznie, ale też opłacalne biznesowo.
- Dziękujemy za rozmowę.