Praktycy zgadzają się co do jednego: w dziedzinie produkcji masowej presja na obniżenie kosztów będzie nadal rosnąć, podobnie jak wymagania dotyczące jakości. Zwiększa się zapotrzebowanie na rozwiązania, które umożliwiają wytwarzanie produktów dostosowanych do indywidualnych wymagań klienta, w niewielkich partiach - liczących nawet jedną sztukę, po konkurencyjnych cenach rynkowych, z zachowaniem szybkiego czasu dostarczenia produktu.
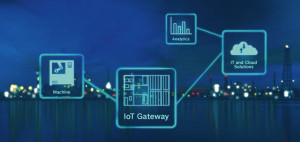
Fot. 1. IoT Gateway firmy Bosch Rexroth pozwala łączyć sensory oraz komponenty w maszynach niezależnie od istniejącego już układu sterowania
Aby wyobrazić sobie zakres czekających nas zmian, spróbujmy odpowiedzieć na inaczej sformułowane pytanie. Co w fabryce przyszłości - za około 10 czy 15 lat - pozostanie bez zmian w stosunku do typowej fabryki z 2018 roku?
Zapewne niewiele, m.in.: podłoga, ściany i dach. Cała reszta - maszyny, automatyzacja, sprzęt, sposoby komunikacji, a nawet pracownicy i sposób, w jaki będą oni współpracować i komunikować się z całą infrastrukturą - zmieni się diametralnie.
W jaki sposób przewidywane scenariusze wpłyną na technologię automatyzacji? Zdaniem firmy Bosch Rexroth można określić wyraźne kierunki jej rozwoju: w przyszłości wykorzystywane będą zdecentralizowane systemy zarządzania produkcją, a architektura automatyzacji będzie jeszcze bardziej zależna od rozproszonej inteligencji oraz łączności między wszystkimi urządzeniami uczestniczącymi w procesie produkcji.
Takie rozwiązanie wymaga zapewnienia zgodności sprzętowej i programowej na wszystkich poziomach klasycznej piramidy środowiska automatyzacji, do systemu informatycznego przedsiębiorstwa i aplikacji chmurowych włącznie.
Branża inżynierii mechanicznej potrzebuje nowych platform automatyzacji, które zapewnią nieograniczoną łączność oraz maksymalną elastyczność podczas konfigurowania urządzeń. Ułatwi to analizę olbrzymich ilości danych napływających z linii produkcyjnej.
Zbudowany w ten sposób wirtualny obraz pracy zakładu oraz produktu umożliwi łatwe śledzenie oraz optymalizację strumieni wartości procesu produkcyjnego. Równocześnie te nowe platformy automatyzacji muszą spełniać tradycyjne kryteria związane z czasem cyklu, dostępnością i sprawnością energetyczną systemów oraz bezpieczeństwem maszyn.
Projektowanie fabryki przyszłości nie musi kończyć się na projekcie 2D lub 3D na ekranie komputera. Obecnie stosowane systemy symulacji z wykorzystaniem elementów VR pozwalają zobaczyć wirtualną linię produkcyjną w docelowym miejscu instalacji, a nawet wejść z nią w interakcję - co pozwala na rozpoczęcie szkolenia pracowników, zanim fizyczne stanowiska pojawią się w zakładzie.
Jakie będą fabryki przyszłości?
|
Obecnie działające fabryki można już teraz zacząć wyposażać w rozwiązania I4.0 integrujące zainstalowane już maszyny i używane w zakładzie systemy, m.in. MES czy ERP. Rozwiązanie, takie jak IoT Gateway firmy Bosch Rexroth, pozwala łączyć sensory oraz komponenty w maszynach niezależnie od istniejącego już układu sterowania.
IoT Gateway można łatwo podłączyć do czujników i sterowników innych producentów, które są zgodne m.in. ze standardami PPMP, OPC UA i OPC DA. Informacja o stanie lub awarii podłączonych źródeł danych, a tym samym generujących je urządzeń, może być dostępna z dowolnej lokalizacji w zakładzie, a użytkownicy mogą i będą mogli korzystać ze wszystkich funkcji IoT Gateway w urządzeniach przenośnych.
W przypadku, gdy przesyłane dane o stanie maszyny wymagają dodatkowej mocy obliczeniowej i odpowiednich narzędzi analizy, IoT Gateway pozwala przesyłać takie dane do przygotowanych dedykowanych aplikacji w chmurze obliczeniowej Bosch, jak również do klasycznych "odbiorników" danych w tradycyjnych lokalizacjach zakładu (serwerownia, baza danych, chmura prywatna).
Decydenci, którzy już dziś muszą podejmować decyzje o inwestycjach, mogą jeszcze nie wiedzieć, jakich konkretnych typów urządzeń będzie wymagać fabryka przyszłości. Jedno jest pewne: odizolowane od siebie rozwiązania są bardzo ryzykowne, ponieważ ich integracja i łączenie wymaga w późniejszym okresie dużego nakładu pracy i wprowadza ograniczenia.
Należy przyjrzeć się bliżej inteligentnym, zdecentralizowanym rozwiązaniom, które oparte są na otwartych standardach zapewniających elastyczne możliwości zbierania i przekazywania danych. Rozwiązania te będzie można dużo łatwiej i szybciej integrować, a co za tym idzie lepiej przygotują one fabryki do wyzwań przyszłości.
Bosch Rexroth
Więcej na www.boschrexroth.pl