SENSORY LASEROWE - ZALETY...
Lasery, głównie z ośrodkiem czynnym w postaci ciała stałego lub lasery półprzewodnikowe wykorzystuje się jako źródło światła w czujnikach triangulacyjnych i tych mierzących czas przelotu ze względu na właściwości emitowanego przez nie promieniowania.
Istotna jest przede wszystkim możliwość uzyskania spójnej, silnie skoncentrowanej oraz monochromatycznej wiązki światła. To ostatnie zapewnia odporność na wpływ oświetlenia z otoczenia, natomiast dwie pierwsze właściwości gwarantują dużą rozdzielczość pomiaru.
Oprócz tego czujniki laserowe charakteryzuje większa odporność na warunki środowiskowe (na przykład zmiany wilgotności oraz ciśnienia) w porównaniu do sensorów pojemnościowych i ultradźwiękowych oraz brak ograniczeń pod względem właściwości elektrycznych wymiarowanych detali, które dotyczą czujników wiroprądowych.
Ponadto w przeciwieństwie do metody wykorzystującej zjawisko tłumienia promieniowania rentgenowskiego, w której do obliczenia grubości obiektu wymagana jest m.in. informacja o jego gęstości, w pomiarach laserowych nie jest konieczna znajomość fizykochemicznych parametrów mierzonego materiału.
Do zalet sensorów laserowych zalicza się też dużą dokładność, krótki czas pomiaru oraz przede wszystkim możliwość zamontowania w większej odległości od obiektu niż w przypadku pozostałych typów czujników bezkontaktowych.
To ostatnie ogranicza prawdopodobieństwo uszkodzenia czujnika w razie wystąpienia awarii lub innych nieprzewidzianych zdarzeń w obrębie linii produkcyjnej. Nie jest też dzięki temu konieczne modyfikowanie konfiguracji systemu pomiarowego w razie częstej i dużej zmienności rozmiarów mierzonych detali.
...I WADY
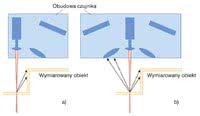
Rys. 5. Ze względu na kształt obiektu promienie odbite od jego powierzchni nie mogą dotrzeć do detektora (a); rozwiązaniem tego problemu jest czujnik z dwoma torami rejestracji obrazu (b)
Czujniki optyczne do prawidłowego funkcjonowania wymagają zachowania dobrej widoczności między źródłem światła a jego detektorem, w związku z czym na drodze promienia świetlnego nie mogą występować żadne przeszkody. Na wynik pomiarów negatywnie wpływają pyły i zadymienie, jak również zanieczyszczenia układu optycznego czujnika.
To ostatnie powoduje, że częste i dokładne czyszczenie oraz konserwacja elementów optycznych sensora powinny być obowiązkowe. Ponadto ze względu na komponenty elektroniczne będące częścią głowicy czujników tego typu, zakres ich temperatur pracy jest ograniczony (typowo do 40°C).
Oprócz tego integracja sensorów optycznych w ramach linii produkcyjnych nie zawsze jest prosta, a wszelkie niedociągnięcia na tym etapie skutkują zmniejszeniem dokładności pomiarów lub nawet nieprawidłowymi wynikami.
Dokładność pomiarów może też maleć na skutek drgań detalu. Poza tym niektóre typy powierzchni, na przykład odblaskowe lub różnokolorowe, wymagają zastosowania czujników o specjalnej konstrukcji.
PARAMETRY CZUJNIKÓW TRIANGULACYJNYCH
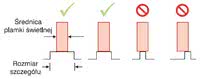
Rys. 6. Średnica plamki świetlnej powinna być mniejsza niż rozmiar najmniejszego szczegółu wymiarowanego detalu, który może mieć wpływ na dokładność pomiaru
Wybierając czujnik laserowy, należy przeanalizować jego parametry oraz szczegóły konstrukcji decydujące o jego przydatności w danym zastosowaniu, co przedstawimy na przykładzie sensorów triangulacyjnych. Ważnymi parametrami są zakres pomiarowy oraz długość tzw. strefy martwej.
Ta ostatnia to odległość między czujnikiem i początkiem zakresu pomiarowego, w której pomiar nie jest możliwy lub jego wyniki są niewiarygodne. Sensor powinien mieć wystarczająco duży zakres pomiarowy, by mógł zmierzyć odległość od obiektu w spodziewanym zakresie jej zmienności.
Długość strefy martwej warunkuje natomiast możliwość zainstalowania czujnika w dostępnych warunkach przestrzennych. Jeżeli wymagany odstęp między głowicą czujnika i początkiem zakresu pomiarowego jest zbyt krótki, może uniemożliwić zamontowanie go w bezpiecznej odległości, na przykład od taśmociągu.
Jeżeli z kolei konieczne jest zapewnienie dużej odległości instalacja czujnika może okazać się niemożliwa z powodu braku miejsca. Na oba te parametry wpływa konstrukcja układu optycznego czujnika. Odległość, w jakiej znajduje się jego ognisko (rys. 3), wyznacza środek zakresu pomiarowego.
W punkcie tym plamka światła jest najmniejsza, a jego obraz wyświetlany jest dokładnie na środku detektora. Zakres pomiarowy i długość strefy martwej zależą też od kąta nachylenia detektora. Im jest on mniejszy, tym zakres pomiarowy i strefa martwa są większe (rys. 4). Niestety jednocześnie wówczas rozdzielczość pomiarów jest mniejsza.
Ponadto jeżeli kąt ten jest zbyt mały (w czujnikach o małej rozdzielczości wynosić może zaledwie 10°) lub zbyt duży (przy dużej rozdzielczości nawet 45°), w danych warunkach pomiar może okazać się niemożliwy.
Może się tak zdarzyć, gdy na przykład ze względu na kształt obiektu promienie odbite od jego powierzchni nie dotrą do detektora rys. 5a. Rozwiązaniem jest wówczas zmiana ustawienia czujnika lub zastąpienie go sensorem z dwoma torami rejestracji obrazu (rys. 5b).