W kontroli jakości w przemyśle korzysta się z metod niszczących i nieniszczących. Badania nieniszczące (Nondestructive Testing, NDT) polegają na poddaniu obiektu testom pod kątem występowania niedoskonałości w jego wnętrzu albo na jego powierzchni, które nie wymagają podejmowania działań mogących go uszkodzić albo zniszczyć. Dzięki temu - w przypadku pozytywnie zakończonej inspekcji - będzie on w dalszym ciągu nadawał się do użytku. Ponadto badania nieniszczące można wielokrotnie powtarzać bez konsekwencji.
OGRANICZENIA BADAŃ NISZCZĄCYCH
Przeciwieństwem testów NDT są badania o charakterze destrukcyjnym, które powodują trwałe uszkodzenia produktów. W związku z tym badania niszczące przeprowadza się na wybranej - zazwyczaj losowo, grupie wyrobów o ograniczonej liczebności. Sprawdzają one przede wszystkim właściwości fizyczne produktów, na przykład ich wytrzymałość na: zginanie, łamanie, rozciąganie, uderzenia, korozję oraz twardość.
W ramce charakteryzujemy przykładowe metody badań niszczących. W dalszej części artykułu przedstawiamy natomiast przegląd najpopularniejszych technik nieniszczących. Do tych ostatnich zaliczanych jest wiele metod. Warto dodać, że w zakładach przemysłowych poza kontrolą jakości gotowych produktów, znajdują one zastosowanie także w utrzymaniu ruchu.
![]() ![]() Fot. 1. Aplikacja penetrantu i wynik jego działania |
JAKIE METODY NALEŻĄ DO GRUPY NDT?
Są to na przykład badania: akustyczne, polegające na pomiarze i analizie dźwięków i drgań, które są generowane pod wpływem oddziaływania na obiekt obciążenia mechanicznego, gwałtownej zmiany temperatury albo ciśnienia, elektromagnetyczne, falami ultradźwiękowymi, które rozchodzą się wzdłuż przedmiotu inspekcji, na przykład rurociągu oraz interferometryczne. W tych ostatnich dokonuje się analizy interferencji światła laserowego odbitego od badanej powierzchni.
Właściwości produktu - na przykład zawartość wilgoci w wyrobach spożywczych i budowlanych, sprawdza się również za pomocą mikrofal. Wykorzystuje się w tym przypadku fakt, że obecność wody powoduje tłumienie oraz przesunięcie fazy ich wiązki przenikającej badaną próbkę. W kontroli jakości używa się też ultradźwięków oraz kamer (patrz ramka).
Do grupy badań NDT należą oprócz tego testy szczelności - na przykład metodą bąbelkową (pęcherzykową), pomiary wycieku pola magnetycznego, badania penetracyjne i magnetyczno-proszkowe. Radiografia, termografia oraz pomiary wibracji również nie powodują zniszczenia obiektów poddawanych inspekcji.
Badania niszczące
Sprawdza ono odporność na działanie dużej siły w krótkim czasie. Wykonuje się je, uderzając w próbkę młotem wahadłowym Charpy’ego. Przeprowadza się także testy wytrzymałości na podwyższone temperatury i odporności na korozję. Ważną cechą jest oprócz tego twardość. Sprawdza się ją metodami statycznymi lub dynamicznymi. Te pierwsze wykorzystuje się częściej. Do grupy technik statycznych zalicza się m.in. metodę Rockwella. Polega ona na pomiarze głębokości wcisku w obiekt wzorcowego stożka diamentowego. Wśród jej zalet wymienia się: szybkość, łatwość realizacji oraz możliwość automatyzacji. W metodzie Vickersa w powierzchnię badanego materiału wgniata się diamentowy ostrosłup. Inaczej, niż w przypadku techniki Rockwella, ustawienie przedmiotu w mniejszym stopniu ma wpływ na wynik pomiaru. Metoda Brinella polega z kolei na wciskaniu kulki wykonanej ze stali hartowanej lub węglików spiekanych. W porównaniu do dwóch pierwszych technik, w jej przypadku powierzchnia obiektu badań ulega większemu uszkodzeniu. |
METODA PRĄDÓW WIROWYCH
W kontroli jakości w przemyśle w praktyce najczęściej korzysta się tylko z kilku spośród wyżej wymienionych metod. Jedną z nich są badania elektromagnetyczne. Do tej grupy zalicza się m.in. metodę prądów wirowych (Eddy Current Testing, ET). Jej podstawę stanowi zjawisko indukcji elektromagnetycznej, zaś inspekcji dokonuje się przy użyciu sondy pomiarowej.
Cewki tej ostatniej są zasilane prądem przemiennymi i generują zmienne pole magnetyczne. Po zbliżeniu ich do detalu, wykonanego z materiału przewodzącego prąd, powstają w nim prądy wirowe. Te zaś generują własne pole magnetyczne, które oddziałuje na cewkę sondy. Zmiany grubości albo defekty w obiekcie zmieniają amplitudę oraz rozpływ prądów wirowych, a w rezultacie wpływają na rozkład pola i prądy w cewkach sondy.
Gęstość prądów wirowych jest największa na wierzchu detalu. Tam więc uzyskuje się największą rozdzielczość pomiarową. Przyjmuje się, że głębokość penetracji tej metody odpowiada odległości od brzegu obiektu, na której gęstość prądów wirowych wynosi około 40% wartości na powierzchni.
CO WPŁYWA NA SKUTECZNOŚĆ BADANIA PRĄDAMI WIROWYMI?
Na efektywność tego typu badania wpływa kilka czynników. Na przykład im większa jest przewodność elektryczna materiału, tym skutecznej można wykryć defekty na jego powierzchni. Równocześnie jednak głębokość inspekcji będzie mniejsza.
Analogiczny wpływ ma też większa częstotliwość testowa. Natomiast im jest ona mniejsza, tym łatwiej jest wykryć skazy znajdujące się w głębi obiektu inspekcji. Im większe są cewki sondy pomiarowej, tym większą objętość detalu można skontrolować. Te mniejsze z kolei dokładniej wykrywają drobne defekty.
O ile na cechy materiału operator systemu nie ma wpływu, o tyle częstotliwość testowa, rodzaj oraz rozmiary cewki powinny być dobrane do specyfiki obiektu badania. Dlatego, żeby zapewnić jak największą rozdzielczość oraz wymaganą głębokość penetracji, w urządzeniach stosowanych w przemyśle można przestrajać częstotliwości oraz korzystać z sond różnego typu.
Kontrola jakości otworów wypalonych laseremJeden z producentów plastikowych elementów, będących częścią detektorów gazów, postanowił uzupełnić linię wypalania w nich otworów za pomocą lasera o system wizyjny, który badałby ich jakość. Miał on dokonywać inspekcji kilkunastu wariantów takich detali, o średnicach otworów w przedziale od kilkunastu, do kilkudziesięciu mikrometrów. Sprawdzane miały być: ich położenie i rozmiary, od strony wlotowej i wylotowej. Linia technologiczna Sterowanie robotem Kontrola jakości - etap 1 Kontrola jakości - etap 2 |
ZALETY I OGRANICZENIA METODY PRĄDÓW WIROWYCH
Badanie prądami wirowymi ma wiele zalet. Przede wszystkim inspekcja jest szybka i przebiega bezkontaktowo. Na skuteczność badania nie mają wpływu nieprzewodzące powłoki, którymi pokryta jest kontrolowana powierzchnia, takie jak farby, lakiery, uszczelnienia, natomiast sam obiekt inspekcji nie wymaga wcześniejszego przygotowania.
Oprócz tego metoda ta umożliwia wykrywanie drobnych skaz, charakteryzuje ją duża czułość, sprawdza się w kontroli jakości detali o skomplikowanych kształtach oraz umożliwia inspekcję miejsc trudno dostępnych, takich jak przykładowo rowki lub gwinty. Jej zaletą jest również niski koszt.
Jeżeli chodzi o wady, to największym ograniczeniem metody prądów wirowych jest możliwość jej wykorzystania wyłącznie do sprawdzania obiektów z materiałów przewodzących prąd. Oprócz tego chropowatość powierzchni ma wpływ na efektywność inspekcji. Istotne jest także to, że głębokość penetracji jest ograniczona. Ponadto defekty równoległe do uzwojeń cewki sondy i kierunku skanowania mogą nie zostać wykryte.
Systemy wizyjne w kontroli jakości
Kamera inteligentna Ważne jest też, żeby smart camera montowana bezpośrednio przy monitorowanym procesie była odporna na warunki, w których będzie pracować: temperaturę, pyły, wibracje, wodę i zaburzenia elektromagnetyczne. Odpowiednio zabezpieczona powinna być obudowa kamery i jej okablowanie. Oprogramowanie i algorytmy Polega on na porównywaniu obrazu obiektu ze wzorcem. Proces ten jest dwufazowy. W pierwszym kroku przetwarzany jest wzorzec. Wyznacza się wtedy jego cechy charakterystyczne, na przykład krawędzie. W drugim kroku podobne cechy będą wyszukiwane w przetwarzanym obrazie. Wybór wzorca jest bardzo ważny. Jeżeli jest asymetryczny, łatwo można określić jego położenie. Jeżeli będzie zbyt skomplikowany, jego wyszukanie w obrazie obiektu zajmie dużo czasu. Jeżeli natomiast będzie zbyt prosty, wyniki porównania mogą być mylące. W kolejnej ramce przedstawiamy przykład wykorzystania systemów wizyjnych w kontroli jakości. |
NA CZYM POLEGA METODA PĘCHERZYKOWA?
W sprawdzaniu szczelności korzysta się m.in. z metody pęcherzykowej (bąbelkowej). Technika ta opiera się na zjawisku przepływu gazu między ośrodkami, które różnią się pod względem panującego w nich ciśnienia, pod warunkiem że są one ze sobą połączone. Kanałami przepływowymi są nieszczelności, których obecności badanie ma dowieść albo ją wykluczyć.
Metoda ta może zostać zrealizowana na jeden z dwóch sposobów. W pierwszym obiekt inspekcji wypełniony powietrzem pod ciśnieniem jest zanurzany w zbiorniku z wodą. Drugie rozwiązanie polega na pokryciu takiego detalu powłoką ze specjalnego roztworu pianotwórczego, na powierzchni której mogą formować się bąbelki.
![]() Porównanie wybranych metod NDT |
W każdej z konfiguracji przez nieszczelności na granicy między dwoma ośrodkami przenika powietrze. Powoduje to powstanie po przeciwnej stronie pęcherzyków powietrza. Pojawienie się bąbelków jest więc dowodem na występowanie w danym miejscu niepożądanych otworów. Najefektywniej w ten sposób wykrywa się duże wycieki.
INNE SPOSOBY NA SPRAWDZANIE SZCZELNOŚCI
Szczelność testuje się również przy użyciu gazu znakującego. Wykonuje się to na kilka sposobów. Wyróżnia się tu trzy techniki:
- Próżniowa - z obiektu inspekcji wypompowuje się powietrze, a potem sprawdza się, czy gaz znakujący przeniknął do jego wnętrza;
- Ciśnieniowa - element napełniany jest gazem, na zewnątrz którego potem poszukuje się śladów obecności substancji znakującej;
- Próżniowo-ciśnieniowa - w ostatniej metodzie obiekt kontroli wypełniony specjalnym gazem umieszcza się w komorze próżniowej. Stężenie medium znakującego jest mierzone przy użyciu spektrometru masowego, który zapewnia dużą czułość pomiaru i przede wszystkim, inaczej niż w metodzie "bąbelkowej", pozwala ilościowo określić ubytek gazu.
Badanie szczelności - porady praktyczne
1. Jednym z ważniejszych ograniczeń metody bąbelkowej jest fakt, że wynik inspekcji zależy od subiektywnej interpretacji osoby wykonującej test. 2. Warto dobrze przemyśleć to, na jakim etapie produkcji powinno się kontrolować szczelność. Czasem lepiej jest zbadać integralność poszczególnych podzespołów, nim zostaną one zmontowane w całość. Na przykład dobrze jest najpierw sprawdzić, czy obudowa nie przecieka. Jeśli bowiem tak jest, a wykryjemy to dopiero, badając gotowy wyrób, czas i praca poświęcone na jego zmontowanie zostaną zmarnowane. 3. Jeśli z jakiegoś powodu obiekt inspekcji miał kontakt na przykład z olejem lub smarem, istnieje ryzyko, że mogły one przytkać drobne nieszczelności. Dotyczy to na przykład odlewów i metalowych detali poddawanych obróbce wykończeniowej. Żeby kontrola szczelności była wiarygodna, należy najpierw przedmiot umyć. Następnie trzeba go osuszyć, aby mieć pewność, że również ciecz czyszcząca nie zatkała mikrootworów. 4. Testy szczelności powinno się przeprowadzać w temperaturze, w której wyrób będzie używany. Często bowiem dopiero wtedy niepożądane otwory, w wyniku rozszerzenia lub skurczenia się materiału, stają się na tyle duże, aby przeciek można było wykryć. Badanie powinno się w takich przypadkach wykonywać w komorze klimatycznej. 5. Przed wypełnieniem obiektu gazem znakującym powinno się go dokładnie opróżnić z powietrza. Jest to szczególnie ważne w przypadku przedmiotów o długich i wąskich kształtach. Jeżeli bowiem tego nie dopilnujemy, powietrze zostanie "przepchnięte" i zgromadzi się w zakończeniach przedmiotu, gdzie gaz znakujący będzie miał zablokowany dostęp. Oznacza to, że to właśnie powietrze będzie przenikać występującymi tam nieszczelnościami, czego detektor gazu znakującego na zewnątrz oczywiście nie wykryje. 6. Powinno się znać specyfikę nieszczelności, których wykrycia możemy się w danym obiekcie spodziewać. Na przykład przeniknięcie helu przez otworki włosowate albo o znacznej długości może zająć sporo czasu. W rezultacie, jeżeli odstęp czasowy pomiędzy badaniami kolejnych przedmiotów będzie zbyt krótki, detektor nie zdąży wykryć przecieku. Podobnie stanie się wówczas, gdy gaz znakujący zbyt szybko przeniknie przez otworki w obiekcie, i zanim jeszcze pomiar się rozpocznie, zostanie usunięty z komory testowej. |
JAKIE SĄ ZALETY HELU?
Do zalet tej metody zalicza się również: krótki czas inspekcji rzędu kilku sekund, który, co ważne, zazwyczaj zapewnianie jakości nie rośnie znacząco wraz ze zwiększeniem objętości detalu, niezależność od temperatury i łatwość automatyzacji. Z drugiej strony, chociaż gazy znakujące są tanie, to sam sprzęt pomiarowy jest drogi. Wymaga też kalibracji i zwykle specjalnego czyszczenia.
Gazem znakującym jest zwykle hel, co ma wiele zalet. Jest nietoksyczny, niepalny, nie tworzy mieszanin wybuchowych. Jest to gaz obojętny, nie reaguje zatem z innymi substancjami ani nie ma wpływu na właściwości powierzchni, z którymi ma kontakt. Helu można używać w szerokim zakresie temperatur i ciśnień. Ponadto w powietrzu występuje w minimalnej ilości, która nie wpływa na dokładność pomiaru. Ze względu na mały rozmiar cząstki pozwala na wykrycie nieszczelności o bardzo małych rozmiarach. Hel jest też relatywnie tani. W ramce przedstawiamy porady praktyczne odnośnie do tego, jak skutecznie sprawdzać szczelność powyższymi metodami.
ULTRADŹWIĘKI W KONTROLI JAKOŚCI
Badania przy użyciu ultradźwięków (Ultrasonic Testing, UT) wykorzystywane są, poza wykrywaniem wewnętrznych nieciągłości i skaz detali, również w pomiarach ich grubości. Fala dźwiękowa emitowana jest w głąb materiału, gdzie ulega odbiciu od przeciwległej krawędzi. Znając czas powrotu fali powrotnej, obliczyć można grubość obiektu inspekcji.
Defekty wykrywa się natomiast, porównując falę odbitą z falą wzorcową, odebraną przy obiekcie bez wad. Różnice wskazują na obecność pęknięć, pęcherzy albo innych zmian w strukturze wewnętrznej materiału, które również odbijają ultradźwięki.
Częstotliwość fali dźwiękowej dobierana jest w zależności od badanego materiału oraz defektów, których wystąpienia można się spodziewać. Zwykle im jest ona wyższa, tym łatwiej jest wykryć mniejsze skazy. Niższe częstotliwości pozwalają natomiast na głębszą penetrację i minimalizują efekt rozpraszania oraz tłumienia fali dźwiękowej w materiałach, które charakteryzują się małą gęstością albo niejednorodną strukturą.
Kontrola jakości przy użyciu ultradźwięków jest jedną z najpopularniejszych technik w przemyśle. Jej uzupełnieniem są często badania radiograficzne (Radiographic Testing, RT). Obie te techniki zaliczane są do metod objętościowych, czyli umożliwiających wykrywanie defektów wewnątrz obiektu.
Badania NDT w kontroli jakości odlewów z żeliwa sferoidalnego![]() Rys. 1. Zasada pomiaru Po co badać jakość odlewów z żeliwa? Sprawdzić na przykład trzeba, czy procentowa zawartość form kulistych w ich strukturze jest odpowiednia. W tym celu odlewy można by poddać niszczącym badaniom mikrostruktury. Testy takie należałoby wykonać w laboratorium. Jakie są ograniczenia metod niszczących? Z drugiej strony, ze względu na specyfikę sprawdzanej właściwości, nie można by założyć, że wyniki badania dla grupy testowej będą reprezentatywne dla całej partii produktu. Dlatego wybiórcza kontrola jakości odlewów żeliwnych nie jest najlepszym rozwiązaniem. Badania NDT Dzięki temu w kontroli jakości odlewów wykonanych z żeliwa sferoidalnego świetnie sprawdza się jedna z metod zaliczanych do grupy badań nieniszczących, w której wykorzystuje się ultradźwięki. Testy można wykonywać ręcznie albo je zautomatyzować. Zasada pomiaru Po wyznaczeniu czasu TOF1, między nadajnikiem a odbiornikiem umieszcza się obiekt badania. Następnie mierzy się czas przelotu fali dźwiękowej, która przebywa drogę w wodzie, przed i za testowanym przedmiotem, i w nim, gdzie ulega odbiciu od jego krawędzi (TOF2). Prędkość fali akustycznej oblicza się na podstawie wartości TOF1, TOF2 oraz grubości obiektu inspekcji. Co wpływa na dokładność pomiaru? Aby go zminimalizować, dla każdego następnego obiektu powtarza się pomiar czasu przelotu fali akustycznej TOF1. Analogicznie, jeżeli kolejne odlewy znacząco różnią się temperaturą, jej zmienność należy skompensować. |
PODSTAWY RADIOGRAFII
W radiografii przedmiot inspekcji zostaje prześwietlony promieniowaniem rentgenowskim. Jest to promieniowanie elektromagnetyczne o długości fali od kilku pm do 10 nm. W kontroli jakości wykorzystuje się jego zdolność do przenikania materiałów, które są nieprzezroczyste dla światła widzialnego.
Stopień przepuszczalności zależy od gęstości detalu. Im jest większa, tym mniej promieni przez niego przenika. Dzięki temu na obrazie rentgenowskim rozróżnialne są elementy o różnej gęstości, na przykład zanieczyszczenia. Stanowisko do badania jakości z wykorzystaniem promieni X składa się z ich źródła i detektora, między którymi znajduje się obiekt inspekcji.
Tym pierwszym są lampy rentgenowskie w postaci szklanej bańki próżniowej, w której umieszcza się dwie elektrody: katodę i anodę połączone ze źródłem wysokiego napięcia. Katoda w postaci włókna wolframowego zasilanego z drugiego źródła niższego napięcia żarzy się i emituje elektrony. Cząstki te, przyspieszane w polu elektrycznym między elektrodami, bombardują anodę. W chwili zderzenia z nią emitują promieniowanie X.
Detektor promieniowania rentgenowskiego składa się natomiast ze wzmacniacza obrazu i kamery. Pierwszy element pochłania promienie X i przetwarza je na światło widzialne rejestrowane przez kamerę. W ten sposób powstaje monochromatyczny obraz obiektu. Odcienie szarości odpowiadają na nim konkretnym poziomom natężenia promieniowania RTG odebranego w detektorze.
BADANIA MAGNETYCZNO-PROSZKOWE
Metoda magnetyczno-proszkowa (Magnetic Particle Testing, MT), podobnie jak badanie prądami wirowymi, zaliczana jest do grupy technik wykrywających wady powierzchniowe i defekty, które występują bezpośrednio pod powierzchnią badanego materiału. Wykorzystuje się ją wyłącznie do inspekcji obiektów wykonanych z materiałów ferromagnetycznych. Przykładem tych ostatnich są stopy żelaza, niklu oraz kobaltu.
Metoda magnetyczno-proszkowa wymaga wzbudzenia w badanym obiekcie pola magnetycznego. Następnie na jego powierzchni należy zlokalizować miejsca, w których pole to "wycieka", czyli ulega rozproszeniu. Dochodzi do tego tam, gdzie defekty, na przykład pęknięcia, rysy, wtrącenia, są powodem powstania nieciągłości struktury.
JAK PRZEBIEGA BADANIE?
W praktycznej realizacji pierwszym etapem badania jest namagnesowanie przedmiotu inspekcji, na przykład przy użyciu elektromagnesu jarzmowego. W kolejnym kroku pokrywa się go proszkiem magnetycznym. Jego drobiny skupią się wówczas tam, gdzie występuje strumień rozproszenia. Gromadząc się w tych miejscach, proszek magnetyczny wskaże zatem, gdzie znajdują się skazy.
Używa się proszków różnego typu. Zwykle są to substancje kolorowe, które są widoczne w świetle widzialnym. Stosowane są też proszki fluorescencyjne albo ich mieszanki z proszkami barwnymi. Wówczas oględzin powinno się dokonywać w świetle ultrafioletowym.
Stosuje się dwie metody nanoszenia proszku na przedmiot inspekcji. W pierwszej namagnesowany obiekt jest nim posypywany. W drugiej zanurza się go albo polewa jego zawiesiną.
Badanie jakości połączeń spawanych
Przyjmuje się, że inspekcja wizualna powinna poprzedzać sprawdzenie innymi metodami. Jeżeli bowiem spoina nie przejdzie tej weryfikacji pozytywnie, nie ma sensu uciekać się do droższych i bardziej zaawansowanych technik. Kontrola wizualna nie wymaga użycia specjalistycznego sprzętu. Szkło powiększające i specjalna suwmiarka, czyli spoinomierz, którym można zmierzyć m.in. szerokość, wysokość, grubość spoiny, jej podcięcie, szerokość szczeliny oraz kąt ukosowania, to podstawowe wyposażenie. Osoba, która przeprowadza badanie, powinna mieć odpowiednie kwalifikacje oraz cieszyć się dobrym wzrokiem. Poza tym ważne jest odpowiednie oświetlenie stanowiska inspekcji. Etapy inspekcji wizualnej Obserwując postępy spawania, można z kolei zapobiec przewymiarowaniu spoiny, które powoduje straty materiałów, czasu oraz deformacje, jak i jej niedowymiarowaniu. Po zakończeniu spawania inspekcja wizualna pozwala wykryć szereg różnych wad złącza. Są to m.in.: pęknięcia, spowodowane na przykład przez nadmierne naprężenia własne w przypadku zbyt sztywnej konstrukcji, pęcherze gazowe, które powstają m.in. wówczas, gdy spoina ochładza się zbyt szybko i wtrącanie z żużlu, topnika, metali obcych. Wzrokowo można też zlokalizować braki połączenia spawu z materiałem bazowym, podtopienia i wycieki spoiny oraz wypaczenia. Inne metody NDT w kontroli jakości spoin Metoda magnetyczno-proszkowa jest wykorzystywana m.in. w kontroli jakości krawędzi przed ich zespawaniem. Jej czułość niestety jest tym mniejsza, im większy jest defekt. Najlepiej wykrywa ona pęknięcia, natomiast może przeoczyć okrągłe skazy w spoinie, na przykład pęcherze gazowe. W przeciwieństwie do badania magnetyczno-proszkowego, metoda penetracyjna znajduje zastosowanie w inspekcji stali austenitycznych i materiałów nieferromagnetycznych. Używając ultradźwięków, z kolei łatwo można przeoczyć pęcherze gazowe. Porowatość zdecydowanie skuteczniej wykrywa badanie rentgenowskie. |
METODA PENETRACYJNA
Badanie penetracyjne (Penetrant Testing) uważane jest za jedną z prostszych metod. Dzięki temu jest to również jedna z popularniejszych technik NDT. Wykorzystuje się w niej właściwość kapilarności powierzchni z defektami. Polega ona na tym, że wąskie szczeliny wsysają ciecz, wbrew sile ciężkości.
W badaniu penetracyjnym używa się obojętnej, kolorowej cieczy, tzw. penetranta. Nanosi się ją na powierzchnię poddawaną inspekcji. Ciecz ta wnika w skazy, takie jak szczeliny lub pory. Nadmiar penetranta jest usuwany.
Następnie powierzchnię pokrywa się drugą, bezbarwną lub białą substancją, proszkiem / zawiesiną, tzw. wywoływaczem. Wówczas penetrant wypływa z rowków i zabarwia wywoływacz. W taki sposób uwidocznione zostają miejsca, w których występują defekty.
KOLEJNE ETAPY BADANIA
Pierwszym krokiem jest dokładne oczyszczenie sprawdzanej powierzchni. Smary, pyły, oleje lub inne zanieczyszczenia mogą bowiem uniemożliwić penetrantowi wniknięcie w szczeliny. Środek czyszczący powinno się dobierać, uwzględniając właściwości powierzchni.
Na przykład w przypadku implantów medycznych, które są wykonane z tytanu, powinno się używać wyłącznie niechlorowanych rozpuszczalników. W przeciwnym razie na ich powierzchni mogą się z czasem pojawić pęknięcia spowodowane rozwojem korozji naprężeniowej.
Kolejnym etapem jest naniesienie penetranta. W tym celu obiekt inspekcji umieszcza się w zbiorniku wypełnionym tego typu płynem lub spryskuje się go nim. Penetrant można również rozprowadzić przy użyciu pędzelka.
Ciecz ta powinna pozostać na badanej powierzchni przez określony czas zwany czasem penetracji. Następnie penetrant zmywa się, na przykład strumieniem wody. Później obiekt inspekcji trzeba wysuszyć, na przykład nagrzanym powietrzem. Potem pokrywa się go wywołaczem. Także ta substancja musi pozostać na badanej powierzchni przez pewien czas (czas wywołania), zanim obiekt zostanie poddany oględzinom.
PODSUMOWANIE
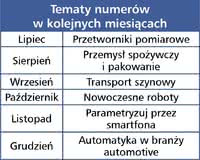
Tematy numerów w kolejnych miesiącach
Na zakończenie przedstawiamy porównanie wybranych wad i zalet opisanych metod nieniszczącej kontroli jakości. Na przykład jeżeli chodzi o koszty, to najdroższa jest inspekcja rentgenowska, natomiast najtańsza metoda penetracyjna.
W przypadku metody penetracyjnej i magnetyczno-proszkowej na wynik badania musimy trochę poczekać. Jeszcze dłużej trwa interpretacja wyników radiografii. Najszybciej defekty wykrywają badania ultradźwiękami i prądami wirowymi.
W przypadku inspekcji rentgenowskiej, ultradźwiękami i prądami wirowymi kształt obiektu badań ma wpływ na wiarygodność wyników. Inaczej jest w przypadku metody magnetyczno-proszkowej oraz penetracyjnej.
Jeżeli chodzi o czułość, to największa charakteryzuje badania ultradźwiękami i prądami wirowymi. Najsłabiej pod tym względem wypadają z kolei metody: magnetyczno-proszkowa i penetracyjna.
Te dwie ostatnie techniki nie wymagają natomiast od operatora wysokich kwalifikacji. Inaczej jest w przypadku na przykład radiografii. W tabeli przedstawiamy jeszcze inne zalety, m.in. możliwość automatyzacji, oraz ograniczenia metod UT, RT, ET, PT i MT.
Monika Jaworowska
Ilustracja tytułowa: Branża lotnicza korzysta z większości stosowanych w przemyśle metod testowania - na zdjęciu silnik General Electric GEnx podczas testu klimatycznego