Część 1. Technologie przemysłu 4.0
Czwartą rewolucję przemysłową umożliwiają i napędzają: Przemysłowy Internet Rzeczy, Big Data, chmura obliczeniowa, sztuczna inteligencja, cyfrowe bliźniaki, rzeczywistość wirtualna, druk 3D (wytwarzanie addytywne), autonomiczne roboty mobilne i roboty współpracujące. Są to zatem zarówno rozwiązania sprzętowe, jak i programowe, z których wiele się wzajemnie uzupełnia. Przykładem jest Przemysłowy Internet Rzeczy, który stanowi źródło danych Big Data oraz chmura obliczeniowa i sztuczna inteligencja, które dostarczają narzędzi, odpowiednio sprzętowych i programowych, do ich obróbki.
Aplikacje przemysłowego internetu rzeczy
Przemysłowy Internet Rzeczy (Industrial Internet of Things, IIoT) to segment Internetu Rzeczy, czyli sieci, w której przedmioty wyposażone w układy komunikacyjne i często także w czujniki wymieniają dane między sobą i z węzłami nadrzędnymi. W przemyśle IoT jest wykorzystywany przede wszystkim w pomiarach, nadzorze i zarządzaniu aktywami. Jednym z perspektywicznych zastosowań IIoT jest predykcyjne utrzymanie ruchu, w którym dane zebrane z opomiarowanych maszyn są centralnie przetwarzane w celu detekcji oznak możliwej awarii. Kolejny przykład to wykrywanie wąskich gardeł na podstawie analizy pozyskanych z sieci IIoT wskaźników wydajności, stopnia wykorzystania poszczególnych maszyn i linii technologicznych oraz informacji o przestojach. IIoT znajduje także zastosowanie w predykcyjnej kontroli jakości. W tym przypadku dane z sensorów w maszynach pozwalają na dobór ich nastaw, procedur bądź receptur, optymalnych pod względem pożądanych cech wyrobu końcowego, kompensujących jego specyfikę albo warunki produkcji, jak odchyłki narzędzi rosnące z czasem na skutek deformacji termicznych.
Case study: Sztuczna inteligencja w predykcyjnym utrzymaniu ruchuSztuczna inteligencja w tytułowej aplikacji ma zastosowanie w: szacowaniu, kiedy maszyna ulegnie awarii, co pozwala zawczasu zaplanować konserwację, która jej zapobiegnie, detekcji anomalii w jej działaniu, diagnozowaniu awarii i rekomendowaniu działań łagodzących oraz konserwacji. Jej przewaga nad podejściem tradycyjnym, w którym personel konfiguruje reguły aktywacji alarmów w systemie SCADA, polega na tym, że uwzględnia złożone dynamiczne wzorce w pracy maszyny i dane kontekstowe dotyczące procesu produkcyjnego, opierając się na danych z systemów OT (Operational Technology) (czujnikach, sterownikach, SCADA) i systemów IT (MES, ERP), na podstawie których algorytmy uczą się zachowania urządzenia. Uczenie maszynowe w praktyceZacząć należy od danych. Najważniejsze to: historia awarii, konserwacji, użytkowania oraz trendy zmian wydajności, specyfikacja maszyny, warunki pracy. Mając te informacje, można zdecydować, która strategia modelowania pasuje do dostępnych danych i oczekiwanego wyniku. Przykładowo można zastosować algorytm regresji do przewidzenia pozostałego czasu użytkowania i algorytm klasyfikacji do prognozowania niesprawności w określonym oknie czasowym. Oba w tym celu zamodelują relację pomiędzy danymi wejściowymi a przebiegiem degradacji systemu. Jeśli z kolei dysponujemy także odczytami z czujników monitorujących stan maszyny, na przykład z sensorów wibracji, trzeba rozważyć zastosowanie algorytmów głębokiego uczenia. Przykład to sieci neuronowe LSTM (Long Short Term Memory), które są podtypem rekurencyjnych sieci neuronowych, sprawdzającym się w przetwarzaniu danych sekwencyjnych. |
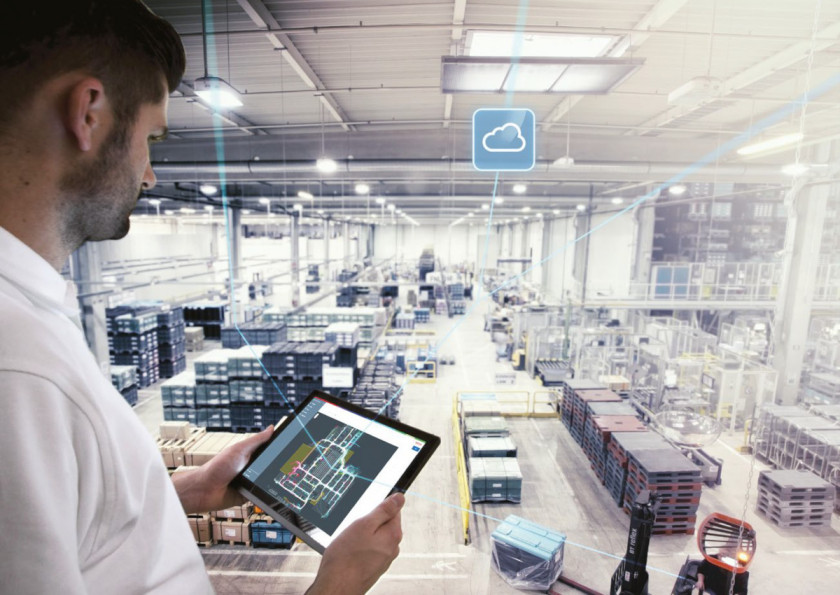
Internet Rzeczy popularyzuje się dzięki dostępności czujników smart i rozwojowi technologii komunikacyjnych. Pierwsze to zintegrowane jednostki, zbudowane z: elementu pomiarowego, bloku wstępnego przetwarzania wyników pomiarów oraz nadajnika wysyłającego odczyty. Są wbudowywane w nowe urządzenia, by fabrycznie przygotować je do podprzemysł łączenia do sieci IoT, albo domontowywane do tych starszych. W dziedzinie komunikacji z kolei nadzieje pokłada się w sieciach 5G, wyróżniających się wymaganymi w aplikacjach Industry 4.0 parametrami transmisji (dużą prędkością, małymi opóźnieniami, dużą przepustowością).
Dostępność danych i możliwość ich przesyłu jednak nie wystarczą. Trzeba je jeszcze bowiem przetworzyć, by uzyskać jak najwięcej użytecznych wniosków, bez nadmiernego obciążenia systemów za to odpowiedzialnych. Jest to trudne, gdyż dane pozyskiwane w sieciach IIoT są zaliczane do kategorii Big Data.
Czym są Big Data?
Big Data to ogromne i złożone zbiory danych, dla których nie sprawdzają się tradycyjne metody zarządzania, magazynowania i przetwarzania. Poddane odpowiedniej obróbce pozwalają jednak na zidentyfikowanie trendów, wzorców, powiązań, bez nich trudnych, a nawet niemożliwych do wykrycia. Oprócz sieci IIoT poza przemysłem ich źródłem są m.in. platformy społecznościowe i sklepy internetowe. Wyróżnia się trzy ich typy: ustrukturyzowane, częściowo ustrukturyzowane i nieustrukturyzowane. Pierwsze pozyskuje się, przechowuje i przetwarza w ustalonym formacie. Dzięki zorganizowanej i znanej z wyprzedzeniem strukturze ich obróbka jest łatwa. Przykład to tabele arkuszy kalkulacyjnych. Format tych trzeciego typu jest nieznany. Zwykle mają większy rozmiar niż ustrukturyzowane, w związku z nadmiarowymi informacjami, które wynikają z ich niejednorodnego charakteru. Przykład z życia codziennego to wyniki z wyszukiwarki w postaci stron, filmów, obrazów. Dane częściowo ustrukturyzowane są kombinacją ustrukturyzowanych i nieustrukturyzowanych, niesklasyfikowanych, ale ze znacznikami będącymi ich wyróżnikami.
Thomas Spranzel
Turck
Aby być konkurencyjnym, zawsze należy podążać za trendami, zaś aby zostać liderem, należy te trendy kreować. Sytuacja, z którą mamy do czynienia na rynku obecnie wymusza na przedsiębiorstwach przyspieszenie wdrożeń nowoczesnych rozwiązań. W dobie słabo dostępnych komponentów niezbędnych do produkcji ważne jest, aby zapewnić bezawaryjną pracę przez możliwie najdłuższy czas już istniejących systemów, a przy planowaniu inwestycji odpowiednio wcześnie zabezpieczyć zakup komponentów. Powyższe działania są możliwe dzięki analizie wyselekcjonowanych i prawidłowo zinterpretowanych danych powiązanych z ideą Przemysłu 4.0, które pozwalają zachować ciągłość produkcji, minimalizować koszty związane z obsługą oraz optymalizować procesy w przedsiębiorstwach wszelkiego rodzaju (nie tylko produkcyjnych), powodując maksymalizację zysków. Na dłuższą metę w wielu zakładach niemożliwe będzie pozostawanie konkurencyjnym bez wdrażania nowoczesnych technologii ze względu na rosnące koszty będące wynikiem braku odpowiednich analiz danych z obszaru produkcji.
W celu umożliwienia podążania za trendami powiązanymi z Przemysłem 4.0 praktycznie każdej z firm na rynku producenci automatyki i oprogramowania oferują systemy dostosowane do charakterystyki i rozmiaru przedsiębiorstw. Narzędzia pozwalające na zdalny dostęp do parametrów maszyny są w zasięgu zarówno dużych, jak i małych przedsiębiorstw. Analiza i archiwizacja danych produkcyjnych może być realizowana na serwerach klienta, zaś jeżeli nie posiada on odpowiedniej architektury, to ma możliwość skorzystania z gotowej usługi pozwalającej zrealizować to zadanie z pomocą partnera z wykorzystaniem jego infrastruktury. W skład Przemysłu 4.0 wchodzą komponenty które mają możliwości pozyskiwania dodatkowych danych i przesyłania ich w celu analizy np. do portalu chmurowego. Siła tkwi nie w samych danych, a w ich odpowiedniej interpretacji i właściwie wyciągniętych wnioskach. |
Big Data charakteryzuje: ilość, prędkość napływu, różnorodność, wiarygodność, odpowiedniość i zmienność. Niektóre z tych cech z jednej strony utrudniają ich obróbkę, a z drugiej decydują o ich użyteczności. Pierwsza często jest wyrażana w petabajtach, eksabajtach, a nawet zettabajtach czy jotabajtach. Wyzwaniem dla wielu przedsiębiorstw bywa już zatem samo magazynowanie takich ilości informacji. Są zwykle generowane z dużą szybkością, zatem równie prędko muszą zostać poddane analizie, aby można było z nią nadążyć za przychodzącymi nowymi informacjami. Na wydajność obróbki wpływa też ich różnorodność, ważna jest więc ich prawidłowa klasyfikacja. Wymagana jest także weryfikacja wiarygodności i jakości danych, pod kątem zduplikowanych rekordów, błędów, niespójności, szczególnie tych z różnych źródeł i różniących się formatem. Odpowiedniość decyduje o tym, czy zestaw danych sprawdzi się w danym przypadku użycia. Zmienność danych wpływa natomiast na możliwość ich ujednolicenia.
Jakie są korzyści z chmury?
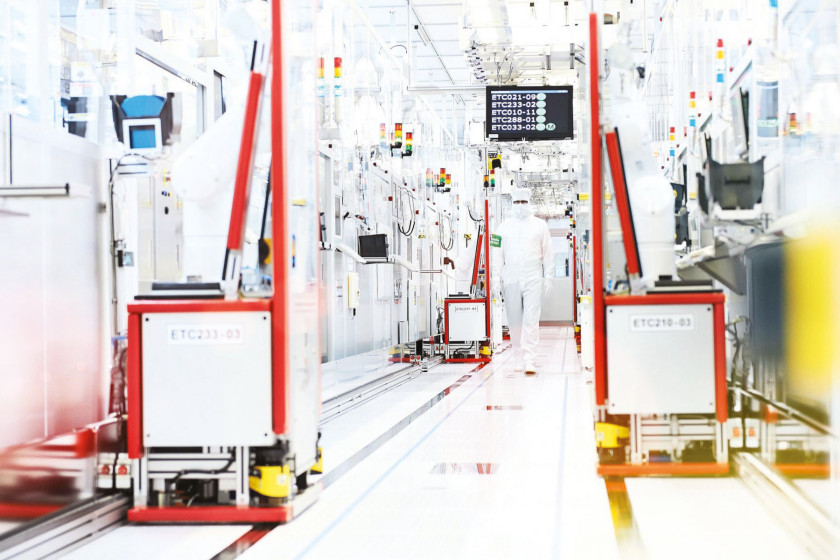
Przechowywanie i obróbka Big Data z IIoT w fabrykach wymaga więc dużych ilości pamięci, mocy obliczeniowej i odpowiednich algorytmów obróbki. W tym pomocne są: chmura obliczeniowa i sztuczna inteligencja. Pierwsza jest alternatywą w razie niewystarczających lokalnych zasobów infrastruktury informatycznej, jest to bowiem usługa, w której z serwerów, baz danych, sieci i oprogramowania można korzystać zdalnie. Z tym wiążą się liczne korzyści.
Przede wszystkim nie ponosi się wydatków na zakup sprzętu, oprogramowania, potem kosztów jego obsługi i utrzymania (płac specjalistów, opłat za energię elektryczną zasilającą serwery i systemy ich chłodzenia). Usługi w chmurze są dostępne na żądanie, więc nie trzeba ich zawczasu planować. Są też skalowalne, co oznacza, że stosownie do potrzeb i możliwości finansowych można skorzystać z większej mocy obliczeniowej, pamięci oraz przepustowości. Ponadto, ponieważ to usługodawcy dbają o stronę sprzętowo-programową, klient zawsze ma dostęp do najnowszych rozwiązań. Dotyczy to również zabezpieczeń przed cyberatakami.
Sztuczna inteligencja
Sztuczna inteligencja to zbiór technik rozwiązywania problemów analizy danych do tej pory trudnych lub niemożliwych do rozwikłania, odgrywająca coraz większą rolę w obróbce Big Data. Szczególne znaczenie ma uczenie maszynowe, w którym algorytm może się nauczyć klasyfikacji danych wejściowych na podstawie ich próbek. Wyróżnia się nadzorowane oraz nienadzorowane uczenie maszynowe. W pierwszym algorytm w oparciu o dane wejściowe i wyjściowe szuka funkcji określającej zależność pomiędzy nimi. Wyróżnia się dwa jego typy: klasyfikację oraz regresję. W pierwszej zmienną wyjściową jest kategoria, jak "prawidłowy" albo "nieprawidłowy", a w regresji jest to liczba rzeczywista. W uczeniu nienadzorowanym natomiast dostępne są tylko dane wejściowe, a celem algorytmu jest modelowanie struktury lub rozkładu danych. Podgrupą uczenia maszynowego jest głębokie uczenie wykorzystujące warstwową strukturę algorytmów w postaci sztucznej sieci neuronowej. Ponieważ wzoruje się ono w tym zakresie na ludzkim mózgu jest efektywniejsze niż inne algorytmy uczenia maszynowego.
Autonomiczne roboty mobilne![]() Autonomiczne roboty mobilne poruszają się po ścieżkach, które planują samodzielnie i które mogą na bieżąco zmieniać, wybierając tę najlepszą do wykonania zadania. W tym celu wyposaża się je w czujniki, a w ich sterownikach implementuje się specjalne algorytmy. Dzięki nim manewrują, żeby omijać przeszkody, zwalniając, żeby uniknąć zderzenia z ruchomymi obiektami i modyfikując trasę w locie, aby wybrać tę najkrótszą albo, jeżeli została wdrożona funkcja śledzenia poruszających się obiektów i przewidywania ich ruchu, tę, na której prawdopodobieństwo zderzenia jest najmniejsze. Pojazdy tego typu znajdują zastosowanie w transporcie wewnętrznym w zakładach przemysłowych, przykładowo przenosząc części między stanowiskami montażowymi i magazynach, w kompletowaniu zamówień. |
Komponenty cyfrowych bliźniaków
Cyfrowy bliźniak to wirtualna reprezentacja, odpowiadająca atrybutom i zachowaniu obiektu, którym może być urządzenie, linia produkcyjna lub system, która spełnia wymagania danego zestawu przypadków użycia, od których zależy stopień komplikacji odwzorowania. Dlatego implementacje cyfrowych bliźniaków czasem wykorzystują złożone modele obliczeniowe, a niekiedy mały zestaw atrybutów i informacji. W praktyce są to kompletne gotowe do użytku środowiska, złożone z wzajemnie ze sobą powiązanych danych, modeli i interfejsów. Ostatnie udostępniają dane, pozwalają wywoływać polecenia i uruchamiać modele, zapewniając łączność i interakcje między odrębnymi wirtualnymi reprezentacjami oraz nimi a innym oprogramowaniem. Źródłem danych jest rzeczywisty obiekt, którego odwzorowaniem jest cyfrowy bliźniak. Modele z kolei mogą być oparte na ogólnych zasadach matematyki, fizyki, chemii, inżynierii materiałowej, statystyce, opracowane z wykorzystaniem technik sztucznej inteligencji. Niezbędne są także te zorientowane na wizualizację, jak modele 3D i wykorzystujące rzeczywistość wirtualną albo rozszerzoną.
Rzeczywistość wirtualna a rozszerzona
Rzeczywistość wirtualna zapewnia użytkownikom dostęp do cyfrowo wygenerowanego środowiska, całkowicie odcinając ich od prawdziwego otoczenia. Wgląd w nią zapewnia im kask z wbudowanym wyświetlaczem, a interakcję umożliwiają różnego rodzaju kontrolery.
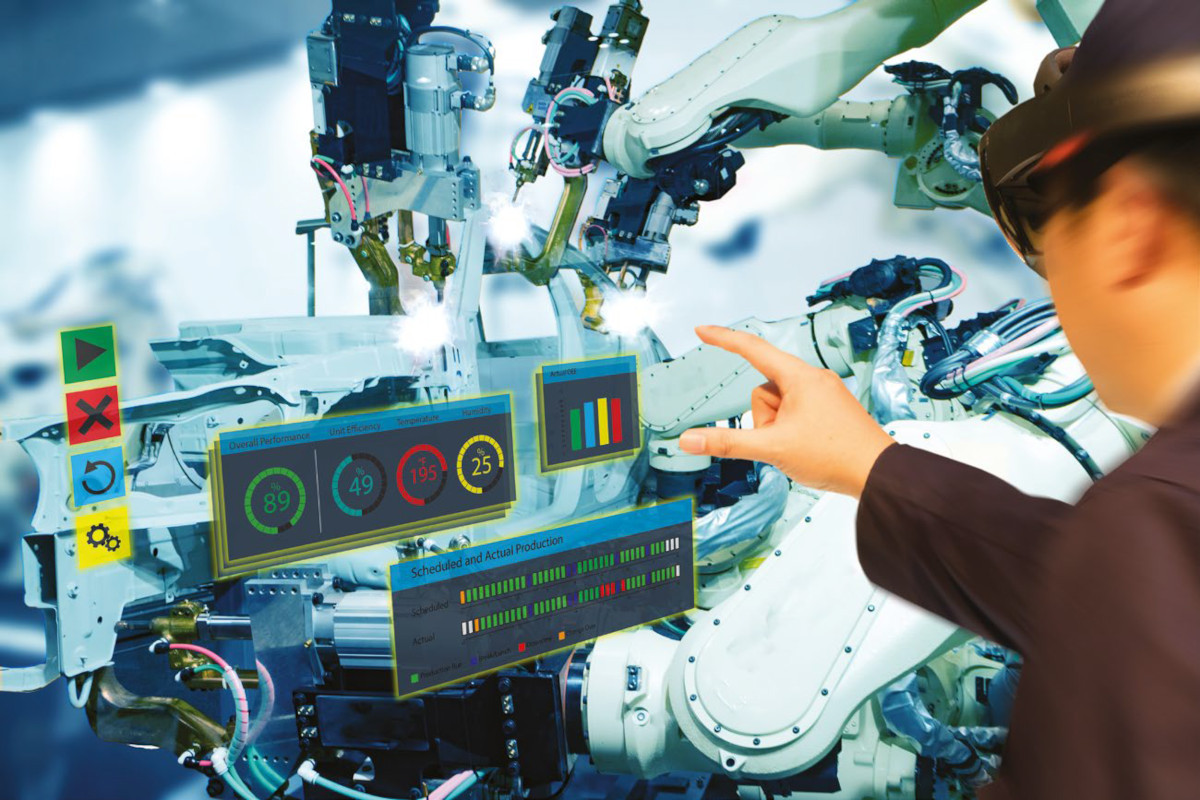
Rzeczywistość rozszerzona natomiast pozwala na nakładanie treści generowanych cyfrowo na rzeczywisty obraz. Realizuje się to w różny sposób zależnie od typu sprzętu użytkownika. Na przykład aplikacje mobilne wirtualne obiekty nanoszą na obraz na wyświetlaczu smartfona rejestrowany za pomocą jego aparatu. Technologia ta jest także dostępna za pośrednictwem kasków, jak w przypadku rzeczywistości wirtualnej, ale zamiast wirtualnego widoku na ten rzeczywisty nakładane są dane cyfrowe.
Przykład zastosowania rzeczywistości wirtualnej w przemyśle to szkolenia, tańsze, gdyż nie wymagają organizacji stanowiska pracy oraz bezpieczniejsze, jeśli przygotowują do pracy w warunkach wysokiego ryzyka. Technika ta umożliwia też współpracę ekspertów we wspólnej cyfrowej przestrzeni projektowej. Rzeczywistość rozszerzona sprawdza się w nawigacji oraz podczas napraw, gdy na widok obiektu nanoszone są instrukcje postępowania.
Dotychczas w artykule przedstawiliśmy rozwiązania programowe stanowiące trzon Industry 4.0. Sprzętowe charakteryzujemy pokrótce w ramkach.
Marek Łozowski
Pepperl+Fuchs
Technologia czujników Przemysłu 4.0 i wydajne komponenty infrastruktury otwierają nowe ścieżki do świata IT. W połączeniu ze standardowymi protokołami przesyłania danych i odpowiednią semantyką rozpoczęła się transformacja do np. Intralogistyki 4.0. Oprócz klasycznych czujników wyposażonych w interfejs IO-Link, przykładami mogą być skanery LiDAR idealnie nadające się do stosowania w szybko poruszających się pojazdach czy systemy służące do określania pozycji i prowadzenia pojazdów AGV po ścieżce. Oparta na kamerze głowica wykrywa albo taśmy torowe na podłodze hali, albo znaczniki pozycji złożone z kodów DataMatrix. Tego typu komponenty zapewniają dokładne wartości rzeczywiste przy wysokich częstotliwościach, a także inne istotne dane, takie jak identyfikacja, lokalizacja i stan pracy, np. liczbę godzin pracy i aktualną siłę sygnału, które pozwalają wyciągnąć wnioski dotyczące zanieczyszczenia lub zużycia. Aby dane te mogły być wykorzystywane w sensowny i skuteczny sposób, wymagane są odpowiednie ścieżki transmisji. Elastyczne moduły sterujące do czujników budują mosty z systemami IT, ponieważ otwierają równoległe kanały do lokalnych lub opartych na chmurze systemów platform danych i zapewniają komunikację w czasie rzeczywistym na poziomie sterowania. Mastery IO-Link komunikują się za pomocą protokołów, takich jak OPC UA i MQTT, i mogą bezpośrednio obsługiwać interfejsy API REST na platformach. Sieć pionową wymaganą dla Przemysłu 4.0 można wdrożyć bezpośrednio, bez dodatkowych komponentów sprzętowych lub programowych. Dane z poziomu terenowego mogą być dalej przetwarzane na platformach IoT, gdzie pojemność pamięci i moc obliczeniowa dla złożonych algorytmów analizy może być skalowana w zależności od potrzeb i gdzie zasoby są wystarczające do zastosowania sztucznej inteligencji. |