Jak się produkuje płytki ceramiczne?
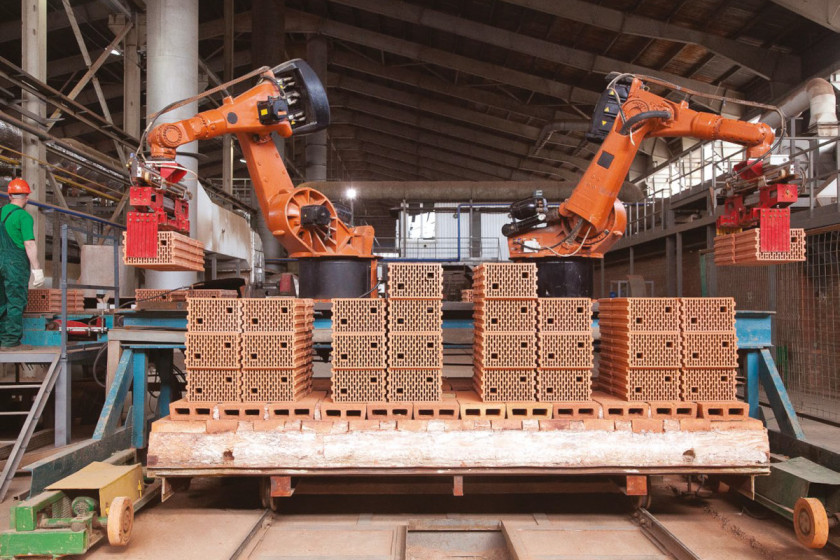
Potocznie ceramika to wypalona, wcześniej odpowiednio uformowana, glina. Szerzej definiuje się ją jako materiał nieorganiczny i niemetaliczny, który w procesie produkcji poddaje się działaniu wysokiej temperatury i który w postaci gotowego wyrobu też charakteryzuje się dużą odpornością na temperaturę. Oprócz gliny do produkcji ceramiki obecnie wykorzystuje się także tlenki, azotki, węgliki, krzemki, borki, fosforki, tellurki oraz selenki. Gama wyrobów ceramicznych jest również bardzo szeroka – obejmuje m.in. naczynia, dekoracje, izolatory elektryczne, armaturę łazienkową i płytki do wykładania ścian i podłóg.
Pierwszy krok w produkcji tych ostatnich to zmielenie surowców na proszek i wymieszanie ich we właściwych proporcjach. Następnie do tej mieszanki dodaje się wodę. W kolejnym etapie zawiesinę rozpyla się w strumieniu gorącego powietrza, co powoduje, że woda odparowuje, a w zbiorniku, nad którym się to odbywa, gromadzi się sproszkowany materiał ceramiczny. Można już z niego wtedy uformować korpus płytki ceramicznej. W tym celu wykorzystuje się połączone działanie ciepła i siły, umieszczając nagrzany proszek w formie poddawanej naciskowi w prasie. Zagęszcza go to, nadając płytkom kształt, rozmiar i, w przypadku płytek ceramicznych dekorowanych, ich fakturę. Następnie podsusza się je oraz glazuruje, czyli pokrywa powłoką ze szkliwa. Płytki są wówczas gotowe do dekorowania metodą sitodruku lub obecnie częściej, druku cyfrowego. Oprócz poprawy estetyki płytek, glazurowanie i zadrukowywanie zapewniają im wodoodporność, trwałość oraz właściwości higieniczne. Ostatnim etapem produkcji jest wypalenie płytek w piecu. Proces ten utwardza bryłę płytek, glazurę i farby dekoracyjne, utrwalając ich kształt oraz wzór zdobienia. Po stopniowym schłodzeniu są one gotowe do sprzedaży.
Kontrola jakości w produkcji farbJeżeli farba nie spełnia wymogów jakościowych, powłoka wykonana przy jej użyciu też nie będzie się cechowała dobrą jakością – spodziewać się można m.in. słabego pokrycia, zacieków, nie takiego wykończenia, jak zakładano (brak połysku, chropowatość) i nietrwałości. Zależnie od rozmiarów pomalowanej powierzchni może to powodować duże straty czasu, pracy i materiałów w związku ze zużyciem farby oraz koniecznością ponownego przygotowania podłoża, jeżeli zdecydowano się na poprawki. Aby temu zapobiec, trzeba dopilnować, żeby farba cechowała się odpowiednią lepkością – jest to kluczowy wyznacznik jakości dla tej kategorii materiałów budowlanych. Dlatego w czasie produkcji farb powinno się ją monitorować. Ze względu na specyfikę tego parametru nie jest to jednak łatwe. Dlaczego należy kontrolować lepkość farby?![]() W przemyśle farbiarskim lepkość jest parametrem warunkującym zastosowanie farby, na przykład do malowania ścian w budynkach lub do wykańczania powierzchni metalowych, drewnianych itp. Poza tym ma wpływ na sposób nakładania powłoki malarskiej – za pomocą pędzla, wałka, natrysku. Dla każdego z tych zastosowań i metod aplikacji lepkość musi mieć optymalną wartość, jest ona bowiem zasadniczo miarą grubości powłoki. To natomiast wpływa na właściwości użytkowe farb i w efekcie nanoszonych powłok, w tym ich strukturę, zgodność kolorów, trwałość, odporność na środki chemiczne, występowanie pęcherzy powietrza. Generalnie także farba nie powinna zmieniać swoich właściwości podczas przechowywania i być łatwa do nałożenia. Jaka jest optymalna lepkość?Lepkość farby zmienia się na skutek różnych czynników podczas produkcji i aplikacji powłoki. Na przykład w fabryce, gdy jest pompowana między kolejnymi stanowiskami produkcyjnymi, poddaje się ją ścinaniu od umiarkowanego do silnego, jej przechowywanie oraz transport to z kolei zwykle etapy charakteryzujące się małym ścinaniem. Także proces jej nanoszenia cechuje się różnym, od umiarkowanego (przy malowaniu pędzlem) do silnego ścinania (powlekanie wałkiem, natrysk). W związku z tym oczekuje się, że generalnie farby będą spełniały następujące warunki: przy małym ścinaniu (<10[1/s]) powinny mieć dużą lepkość przypominając pod tym względem ciała stałe, co pozwala zapobiec rozdzielaniu się faz i sedymentacji, przy średnim (10–1000 [1/s]), na które są narażone typowo podczas produkcji, muszą mieć średnią lepkość, tak by były łatwe do pompowania i mieszania. Podczas nakładania (>1000[1/s]) farba musi być z kolei na tyle rzadka, aby można ją było łatwo aplikować pędzlem, wałkiem itp. Zalety ciągłych pomiarów lepkościPomiar lepkości w hali produkcyjnej lub w laboratorium kontroli jakości przy użyciu tradycyjnych przyrządów, takich jak wiskozymetry, którymi bada się pobrane próbki, jest pracochłonny, czasochłonny i podatny na niedokładności oraz błędy ludzkie. Ponadto pojedyncze wyniki nie zapewniają pełnej informacji o właściwościach farb – pomiar punktowy byłby wystarczający tylko wówczas, gdyby farby miały taką samą lepkość dla wszystkich prędkości ścinania występujących podczas produkcji i aplikacji, co nie jest prawdą. W kontroli jakości produkcji znacznie użyteczniejsze są w związku z tym krzywe lepkości, które obejmują określony zakres szybkości ścinania. Do zbierania takich danych wykorzystywane są procesowe analizatory lepkości, które w sposób ciągły monitorują tę wielkość podczas produkcji farb. Przynosi to licznie korzyści. Przede wszystkim pozwala szybko zidentyfikować i skorygować błędy podczas procesu produkcyjnego, jeśli zaś problem z lepkością zostanie wcześnie wykryty, można zmniejszyć liczbę wybrakowanych partii farb. Zmniejsza to koszty produkcji i poprawia jej wydajność. |