Jakie są rodzaje styropianu?
Tytułowy materiał jest odmianą polistyrenu, tworzywa sztucznego powszechnie wykorzystywanego w budownictwie i m.in. branży opakowaniowej. Polistyren to twardy, sztywny materiał, który wytwarzany jest w procesie polimeryzacji styrenu. Ten ostatni otrzymuje się z kolei w dwóch etapach, najpierw przez połączenie etylenu z benzenem w obecności katalizatora w celu uzyskania etylobenzenu, a potem jego odwodornienie przez przepuszczenie z parą wodną nad katalizatorem. Popularność polistyrenu wynika z różnorodności form, w jakich jest dostępny.
Przykłady to polistyren ogólnego przeznaczenia (General Purpose Polystyrene, GPPS) i polistyren wysokoudarowy (High Impact Polystyrene, HIPS). GPPS jest przezroczysty, ale kruchy, natomiast HIPS jest nieprzezroczysty, ale znacznie wytrzymalszy niż GPPS, dzięki dodaniu kopolimerów butadienu. Najpopularniejszą formą polistyrenu jest jednak pianka, która potocznie jest nazywana styropianem. Wyróżnia się dwa jego rodzaje: polistyren ekspandowany (Expanded Polystyrene, EPS) i polistyren ekstrudowany (Extruded Polystyrene, XPS).
Główną różnicą między nimi jest sposób produkcji. EPS jest wytwarzany przez stapianie ekspandujących polistyrenowych kulek w formie, która może mieć dowolny kształt. XPS z kolei jest produkowany przez ciągłe wytłaczanie w miarę rozszerzania się kulek. W ten sposób powstają płaskie płyty, które można następnie formować termicznie i przycinać do różnych zastosowań. Oba rodzaje pianek składają się głównie z powietrza, dzięki czemu są bardzo lekkie i mają właściwości izolacyjne. Charakteryzuje je także wytrzymałość na ściskanie.
Proces produkcji EPS pozwala na wykonanie go w dowolnym kształcie, dzięki czemu nadaje się do bardziej różnorodnych zastosowań. Ponieważ XPS jest z kolei produkowany w płaskich płytach, jest często używany jako izolacja w budownictwie, chociaż płyty XPS również można formować termicznie i przycinać na dowolne kształty. Główna różnica strukturalna między EPS i XPS polega na tym, że pomiędzy stopionymi kulkami EPS nadal istnieją przestrzenie, co umożliwia łatwiejsze przechodzenie powietrza i wilgoci. Inaczej jest w przypadku XPS, który zapewnia lepszą izolację termiczną oraz wodoodporność, z drugiej jednak strony po przedostaniu się wilgoci EPS wysycha szybciej.
Maszyny specjalistyczne w produkcji EPS
Produkcja styropianu ekspandowanego obejmuje kilka etapów. Pierwszym jest wstępne rozprężenie przy użyciu środka porotwórczego (spieniającego, poroforu). W tym celu polistyrenowy granulat ogrzewa się za pomocą pary (jest to najpopularniejsza metoda) albo gorącego powietrza. Powoduje to przemianę środka porotwórczego, który zmienia się w gaz pod wpływem wysokiej temperatury, powodując spienienie granulatu. Proces ten zachodzi przy jego ciągłym mieszaniu, co ma zapobiec stopieniu się ze sobą polistyrenowych kulek.
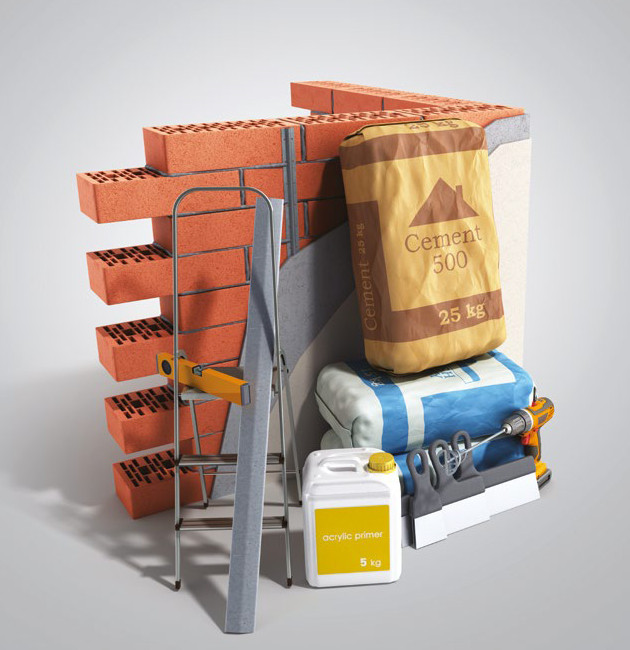
Rozprężanie wstępne jest przeprowadzane w specjalistycznych maszynach – ekspanderach. Są to zazwyczaj urządzenia pracujące w trybie wsadowym, gdyż w przypadku pracy ciągłej trudno jest efektywnie kontrolować parametry procesu mające kluczowe znaczenie dla właściwości styropianu. Rezultat końcowy jest wypadkową skuteczności regulacji głównie: ciśnienia, temperatury i czasu. Jeśli na przykład rozprężanie wstępne trwa za długo, kulki granulatu mogą się zapadać. Ekspander w związku z tym ma zwykle postać uszczelnionej komory parowej, do której w kolejnych cyklach doprowadzany jest wsad granulatu polistyrenowego. Wyposaża się ją w reduktor ciśnienia i czujniki tej wielkości. W przypadku ogrzewania za pomocą gorącego powietrza w komorze ekspandera montuje się dodatkowe sensory temperatury i zawór proporcjonalny, którym doprowadzane jest sprężone powietrze. Żeby z kolei kontrolować gęstość materiału, mierzone są również: waga zawartości zbiornika oraz poziom jego wypełnienia – aby odczyty tej wielkości nie były zafałszowane przez drgania, które towarzyszą pracy maszyny, korzysta się zwykle z wibracyjnych sygnalizatorów poziomu.
Gdy ekspandowane kulki EPS osiągną określony rozmiar, są odsysane z ekspandera wstępnego do zbiorników, w których są magazynowane, wstępnie spienione kulki wymagają bowiem zazwyczaj „starzenia” przez co najmniej 24 do nawet 72 godzin. Pozwala to na dyfuzję powietrza do kulek, ochłodzenie ich i stwardnienie. Po starzeniu kulki wprowadza się do formy o pożądanym kształcie. Pod wpływem pary wodnej i wysokiego ciśnienia kulki ponownie się rozszerzają i stapiają ze sobą. Następnie formę chłodzi się, na przykład przez opryskiwanie jej zimną wodą z zewnątrz.
Monika Jaworowska