Jak się produkuje cement?
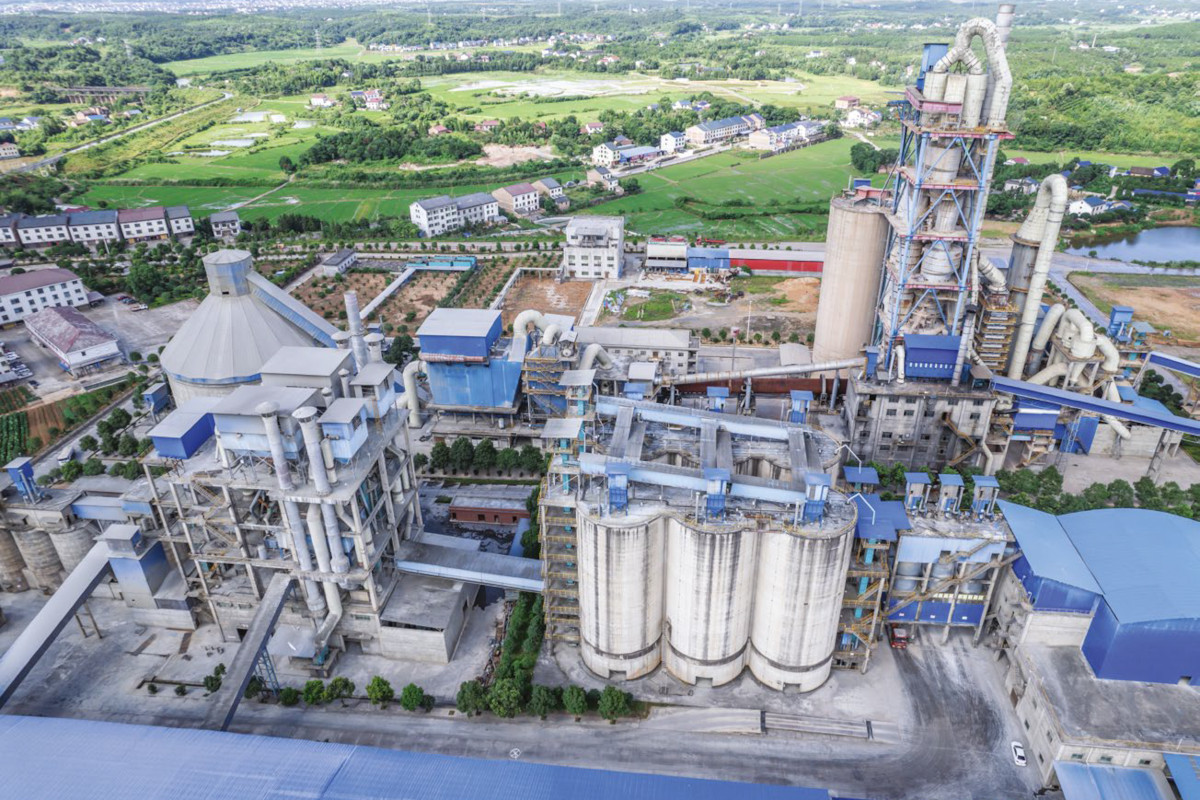
Cement to spoiwo budowlane z grupy hydraulicznych – po zmieszaniu z wodą wiąże i twardnieje w procesie hydratacji (uwodnienia), a po stwardnieniu pozostaje wytrzymały i trwały także pod wodą. Jest jednym ze składników do produkcji betonu. Chociaż technologia jego produkcji jest znana od stuleci, sukcesywnie się ją udoskonala. Generalnie jest to proces ciągły, choć wyróżnić można także etapy w trybie wsadowym.
Surowce do produkcji cementu dobierane są na podstawie ich składu chemicznego. Jego głównym składnikiem jest źródło tlenku wapnia – najczęściej jest to wapień, ale mogą to być również kreda, margiel, dolomit, a nawet muszle ostryg. Kolejne dwa składniki to krzemionka i tlenek glinu, które otrzymuje się z gliny albo łupków. Można też użyć kwarcu i boksytu lub innych minerałów. Ważny składnik to poza tym tlenek żelaza, uzyskiwany z rudy żelaza, pirytu albo żużla wielkopiecowego. Surowce, po przetransportowaniu do zakładu, są zwykle składowane w silosach.
W kolejnym kroku mieli się je i miesza, metodą suchą lub mokrą. Rozdrabnianie jest kontynuowane aż do uzyskania cząstek o wielkości wymaganej w kolejnym etapie produkcji. Mielenie odbywa się na ogół w młynach kulowych, przeważnie po użyciu kruszarki wstępnej. W procesie mieszania na sucho surowce łączy się w odpowiednich proporcjach i magazynuje w silosach. Są to przeważnie zbiorniki homogenizujące, wykorzystujące powietrze do mieszania swojej zawartości. W procesie mokrym do surowców dodaje się wody, co ułatwia ich mieszanie. Wadą tej metody jest konieczność odparowania wody, która zwiększa energochłonność procesu. Zawiesina uzyskiwana metodą mokrą jest przechowywana w zbiornikach z ciągłym mieszaniem.
Kolejnym, kluczowym, etapem w produkcji cementu jest wypalanie mieszanki surowców, w postaci mączki albo zawiesiny, na klinkier w piecu obrotowym. W przykładowym wykonaniu jest to długa, cylindryczna, stalowa rura, nachylona w dół od strony wlotu i wyłożona od wewnątrz materiałem ogniotrwałym, która obraca się wokół własnej osi. Z jednej strony podawany jest surowiec, a druga jest ogrzewana przez gazy spalinowe przemieszczające się w przeciwprądowym wymienniku ciepła w górę pieca w stronę wlotu surowca. Przepływ ciepła przyspiesza wbudowany w piec wentylator. W procesie wypalania klinkieru wyróżnia się cztery fazy. W pierwszej z nich w przypadku obróbki zawiesiny odparowywana jest woda. Następnie dalsze ogrzewanie surowca powoduje rozpoczęcie rozkładu węglanu wapnia – jest to strefa kalcynacji. Produkt uboczny tej reakcji – dwutlenek węgla – jest usuwany z pieca, a materiał wzbogacony tlenkiem wapnia przesuwa się do strefy o najwyższej temperaturze (około +1400°C). W niej zachodzą reakcje łączenia tlenku wapnia, krzemionki, tlenku glinu i tlenku żelaza, których wynikiem jest klinkier. Materiał ten na wyjściu z pieca jest schładzany podczas transportu przez chłodnicę rusztową wyposażoną w zestaw wentylatorów wymuszających obieg zimnego powietrza. W ten sposób obniża się jego temperaturę do takiej, która umożliwia jego dalszą obróbkę, wymaga on bowiem rozdrobnienia, przeważnie w młynie kulowym. Dodaje się do niego także niewielką ilość gipsu w celu zahamowania szybkiego wiązania.
Case study: Produkcja cementuPewien zakład produkujący cement został wyposażony w nową maszynę pakującą. Wkrótce po instalacji zgłoszono problemy w jej działaniu – tolerancja wag oraz szybkość workowania były inne, niż oczekiwano. Ponadto maszyna została zaprojektowana tak, by całkowicie opróżniała się wraz z końcem cyklu produkcyjnego. Niestety okazało się, że gdy jej zasobnik wypełniony był jeszcze cementem w ilości wystarczającej do napełnienia 2–3 worków, materiał ten przestawał się z niego wysypywać. Stanowiło to duży problem, ponieważ w zakładzie produkowane były głównie krótkie serie produktu. W związku z tym częsta zmiana gatunku cementu wymagała każdorazowego otwierania i czyszczenia zasobnika między partiami. Oznaczało to spore straty produktu oraz czasu, przekładając się na spadek wydajności pakowania. By rozwiązać problem, zwrócono się o pomoc do dostawcy maszyny. Wstępny przegląd nie ujawnił żadnych nieprawidłowości w pracy elementów mechanicznych i sterujących, zauważono jednak, że manometr przy komorze pakowarki nie mierzy ciśnienia. Przeprowadzono więc diagnostykę układu ciśnieniowego składającego się oprócz komory również z układu wytwarzania poduszki powietrznej fluidyzującej cement oraz zaworu sterującego dmuchawą. Najpierw szukano ewentualnych przeszkód, które blokowałyby przepływ powietrza do układu wytwarzania poduszki powietrznej, ale ich nie znaleziono. Potem sprawdzono dmuchawy – jak się okazało, zamiast tych oryginalnych, zaprojektowanych do dostarczania powietrza w objętości i pod ciśnieniem wymaganymi do prawidłowego działania pakowarki, wykorzystano te z poprzednio tu pracującej maszyny. Były one zużyte i mniejsze, a oprócz tego zauważono, że ich odpowietrzniki zmodyfikowano w taki sposób, że połowa powietrza, które miało zasilić pakowarkę, była usuwana na zewnątrz. Oczywistą decyzją w takim przypadku była wymiana starych dmuchaw na oryginalne. Niestety nie było to możliwe, ponieważ ze względu na trwający cykl produkcyjny linii workowania cementu nie można było całkiem zatrzymać. Dlatego zdecydowano się na rozwiązanie doraźne – wymianę zaworów bezpieczeństwa na te oryginalne, po wcześniejszym wprowadzeniu w nich drobnych zmian hydraulicznych. Niestety nie rozwiązało to problemu – wydajność dmuchaw wciąż była zbyt mała. Wówczas zmodyfikowano działanie pakowarki – zamiast rozdziału strumienia powietrza z dmuchaw na dwa: regulujący ciśnienie w głowicy napełniającej oraz zasilający proces fluidyzacji, w całości przekierowano go do układu wytwarzania poduszki powietrznej. Chociaż rozwiązanie to nie było pozbawione wad, w stopniu wystarczającym poprawiło dokładność wag worków i szybkość ich napełniania. Po jakimś czasie jednak zauważono, że waga paczek z cementem znowu zaczyna się wahać. Okazało się, że przyczyną jest zbyt niskie ciśnienie w głowicy napełniającej w związku z odłączeniem dmuchawy. Przez część cyklu produkcyjnego było to rekompensowane przez ciśnienie produktu w zasobniku, ale gdy jego poziom spadał poniżej określonego, malało również ciśnienie w dozowniku, co wpływało na konsystencję pakowanego materiału, a w efekcie wagę worków. Jako rozwiązanie tego problemu wdrożono system kontroli poziomu cementu w zasobniku – jeżeli jest za niski, maszyna workująca jest automatycznie zatrzymywana do czasu jego uzupełnienia. |
Pomiary i sterowanie w wypalaniu klinkieru
Pracę pieców do wypalania klinkieru nadzorują sterowniki w oparciu o dane z licznych czujników. Ich celem jest regulowanie krytycznych zmiennych procesowych pieca oraz współpracującej z nim chłodnicy rusztowej, przy jednoczesnym ograniczaniu zużycia paliwa w piecu i energii elektrycznej przez zespoły wentylatorów zimnego powietrza w chłodnicy. Kluczową wielkością mierzoną oraz regulowaną jest oczywiście temperatura – w piecu monitorują ją zwykle czujniki kontaktowe, a na etapie chłodzenia pirometry. Mierzone jest również stężenie tlenku węgla i poziomy tlenu i tlenków azotu. Kontrolowana jest ponadto wysokość złoża klinkieru w chłodnicy rusztowej. Trzeba też monitorować zawartość wolnego wapna. W tym celu przeprowadza się analizę laboratoryjną próbek klinkieru, które są pobierane na wyjściu pieca typowo nawet kilka razy dziennie.
W zakresie sterowania natomiast lokalne regulatory, zwykle PID, zarządzają pętlami sterowania: natężeniem przepływu mączki (lub zawiesiny), dopływem powietrza oraz paliwa w sekcji spalania, ciśnieniem w piecu, prędkością wentylatorów w piecu i w sekcji chłodzenia. Oprócz ograniczenia zużycia energii ich celem jest stabilizowanie i optymalizacja procesu spalania w oparciu o dane o jakości surowca i klinkieru, w tym uzyskanie tego ostatniego o założonej jakości charakteryzowanej stężeniem wolnego wapna oraz przestrzeganie ograniczeń systemu, mechanicznych (parametry pracy silnika, pieca, jego pojemność), termodynamicznych (temperatura i stężenie tlenu w piecu) oraz środowiskowych, odnoszących się do stężenia tlenku węgla, tlenków azotu i innych gazów w spalinach.
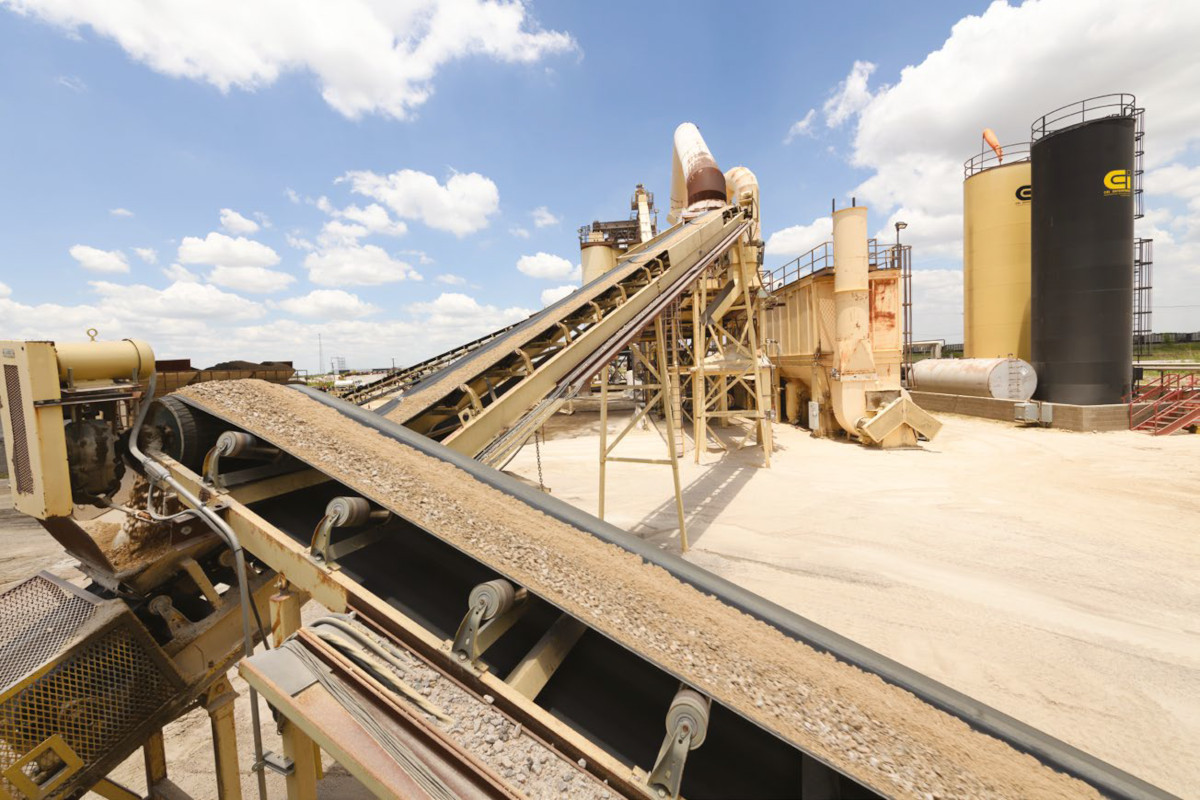