Dekorowanie płytek ceramicznych – ograniczenia sitodruku
Wypalanie jest najdroższym etapem produkcji płytek ceramicznych – żeby zmniejszyć jego koszt, piec często pracuje nieprzerwanie, co zapobiega marnowaniu energii na każdorazowe rozgrzewanie go do wymaganej temperatury powyżej +1000°C. W związku z tym wymagana jest również ciągła dostawa płytek gotowych do wypalenia, dlatego zwykle w takiej fabryce musi pracować więcej niż jedna linia ich produkcji. Ponadto piec można wykorzystać najefektywniej, jeśli jest załadowany do pełna, tymczasem klienci coraz częściej zamawiają krótkie, spersonalizowane serie. Do niedawna wyzwaniem był również proces dekorowania płytek ceramicznych, gdyż powszechnie stosowana metoda sitodruku ma wiele wad, przekładających się na koszt i wydajność produkcji.
Kluczową jest długi czas przygotowania szablonu i rolek za każdym razem, gdy zmienia się treść nadruku. Czaso- i pracochłonne jest również zapewnienie spójności kolorów, bowiem pod wpływem ekstremalnie wysokich temperatur podczas wypalania między pigmentami w tuszu i glazurą zachodzą reakcje, które powodują zmianę barw nadruku w stosunku do tych nanoszonych. Dlatego, aby sprawdzić ostateczne kolory, trzeba wykonać próbne wypalenie zadrukowanej płytki, w przypadku sitodruku – po każdej wymianie rolki. To zwiększa koszty i straty materiału. Długie przezbrajanie oraz trudne zarządzanie kolorami utrudnia planowanie produkcji, zwłaszcza krótkich serii. Przygotowanie szablonu (wzoru na rolce) też nie jest łatwe i bez odpowiednich umiejętności trudno uzyskać realistyczne i wysokiej jakości nadruki, co zwiększa koszt płytek zdobionych przez wyspecjalizowanych producentów. Ponadto metodą sitodruku można dekorować wyłącznie płaskie płytki – ponieważ jest to metoda kontaktowa, nie nadaje się do wykonywania nadruków na płytkach z teksturą. Nie można też zadrukowywać krawędzi, dlatego płytki zdobione tą techniką mają białe, niezadrukowane obramowanie. Konsekwencją tego, że jeszcze niewypalone, kruche płytki wchodzą w kontakt z rolką, jest oprócz tego możliwość ich uszkodzenia, z czym wiążą się straty materiałów (płytki, szkliwa, tuszu). Ograniczenia te sprzyjają produkcji długich serii i utrzymywaniu zapasów wyrobów gotowych – wówczas w przypadku powtórnego takiego samego zamówienia można je zrealizować łatwiej i taniej, niż próbując odtworzyć oryginalne kolory.
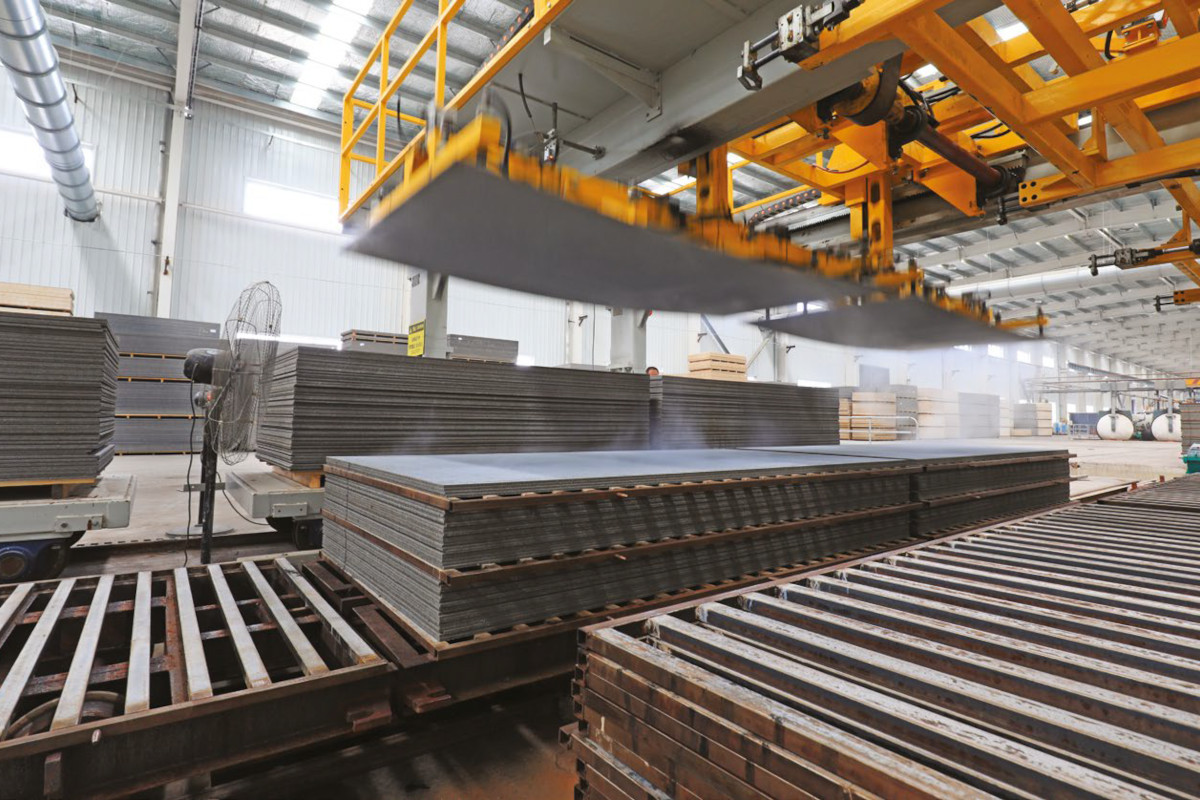
Druk cyfrowy w produkcji płytek ceramicznych
Alternatywą jest druk cyfrowy rozwiązujący większość problemów, których źródłem jest sitodruk. W przypadku dekorowania płytek ceramicznych jego największą zaletą jest to, że jest to proces bezkontaktowy – odległość pomiędzy zadrukowywanym podłożem a głowicą drukującą wynosi zazwyczaj kilka milimetrów. Dzięki temu płytki nie ulegają uszkodzeniu pod wpływem nacisku. Można również dekorować te teksturowane, wypełniając tuszem zagłębienia wzorów będące poza zasięgiem rolek maszyn do sitodruku. Technika ta pozwala ponadto na pokrycie nadrukiem całej płytki, aż po jej krawędzie. Druk cyfrowy pozwala na wykonywanie bardziej skomplikowanych i większych wzorów – dostępne są drukarki, które mają wystarczającą ilość pamięci, aby odtworzyć te o powierzchni nawet kilkudziesięciu m² bez powtórzeń, płytkami z indywidualnym wzorem można zatem wyłożyć całe pomieszczenie. Technikę tę wyróżnia też duża rozdzielczość wydruków, dzięki której na nadrukach rozróżnialne są najdrobniejsze szczegóły, a zdobienia płytek są bardziej realistyczne – trudno je na przykład odróżnić od prawdziwego marmuru lub kamienia. Konfiguracja drukarek, zmiana wzorów oraz zarządzanie kolorami są realizowane programowo, co upraszcza powielanie dekoracji i barw. Łatwo i tanio można zatem zadrukowywać nawet krótkie serie płytek.
Warto dodać, że chociaż obecnie metoda cyfrowa jest dominującą w zdobieniu płytek ceramicznych od wprowadzenia na rynek pierwszej takiej drukarki pod koniec lat 90. zeszłego wieku do ich upowszechnienia się upłynęła prawie dekada. Wynikało to stąd, że ich producenci potrzebowali czasu, by dopracować konstrukcje głowic drukujących, dostosowując je do wyzwań, jakie stawia im drukowanie na ceramice. Po pierwsze, proces produkcyjny płytek generuje dużo pyłu. Po drugie, po opuszczeniu prasy te niewypalone są kruche, gorące oraz parujące. Ponadto tusz do drukowania na ceramice, żeby można było uzyskać żywe kolory, musi zawierać duże, nierozpuszczalne cząsteczki pigmentu utrzymywane w zawiesinie. Przez to jest bardzo lepki oraz podatny na wytrącanie się osadów. Z tych powodów w pierwszych drukarkach często dochodziło do zatykania się dysz, przez co jakość druku była słaba, a dysze wymagały częstego czyszczenia. To powodowało przestoje i nie pozwalało na korzystanie z druku cyfrowego w produkcji na masową skalę. Ponadto początkowo, z powodu małej rozdzielczości, wydruki były ziarniste, zaś części zamienne do drukarek i tusze – drogie.
Kontrola jakości płytek ceramicznych
Z czasem problemy te nie tylko udało się rozwiązać, ale poza udoskonaleniem konstrukcji głowic, wprowadzono także szereg innych ulepszeń. Przykładowo nowoczesne systemy druku cyfrowego, wykorzystując kamery, wykrywają ułożenie płytki na taśmie z dużą dokładnością i same się regulują, co gwarantuje prawidłową orientację i położenie drukowanego obrazu. Dzięki temu nie trzeba stosować rozwiązania, w którym nanoszony obraz celowo poszerza się tak, żeby zrekompensować ewentualne przesunięcie płytki względem jej pożądanego ustawienia i w ten sposób uniknąć pozostawienia na niej niezadrukowanych fragmentów. Główne wady takiego podejścia to jednak: strata atramentu oraz zabrudzenie nim taśmy. Poza ograniczeniem kosztów tuszu i konserwacji dzięki funkcji automatycznego centrowania obrazu nie są też potrzebne prowadnice do układania płytek w linii ani ręczne centrowanie tych wielkogabarytowych, które są ciężkie.
Postęp w zakresie wykonywania nadruków nie oznacza jednak, że są one bez skazy, więc kontrola jakości jest obowiązkowym etapem w produkcji płytek ceramicznych. W jej ramach sprawdza się je nie tylko pod kątem nieprawidłowości w zdobieniach, ale i innych braków. Dostępne są stanowiska kontroli wizyjnej, które rozpoznają różnego typu wady w strukturze i dekoracji płytek, wyposażone w zestaw kamer i oświetlenie zoptymalizowane pod kątem inspekcji wyrobów ceramicznych o dużej odblaskowości. W nowoczesnych rozwiązaniach tego typu coraz powszechniej wdraża się techniki sztucznej inteligencji, na przykład w funkcji samouczenia się, która autonomicznie ustala poziomy akceptacji dla poszczególnych cech płytek lub funkcji detekcji koloru, która uwzględnia zacienienie. Oprócz kamer stanowiska kontroli jakości płytek ceramicznych wykorzystują lasery, dzięki którym można wykryć krzywiznę i ubytki na ich bokach, sprawdzić wymiary, wykryć brak kątów prostych i zweryfikować płaskość – w tym celu na ich powierzchni wyświetla się matrycę punktów albo serię linii i porównuje się je z ich obrazem dla płytki wzorcowej.