- Rozmawiamy w sytuacji szczególnej, bowiem jesteśmy po szczytowym okresie pandemii COVID-19, która niewątpliwie też zmieniła sposoby funkcjonowania firm przemysłowych. Jak ostatnie kilka miesięcy wyglądało z Waszej perspektywy i jak w tym czasie sprawdzały się cyfrowe narzędzia do zarządzania produkcją?
Sytuacja związana z COVID-19 zaskoczyła wiele organizacji. Jeżeli chodzi o kluczowe dla nas sektory - energetykę, branżę spożywczą czy farmaceutyczną, to nie zanotowaliśmy u naszych klientów przestojów w produkcji. Sądzę, że korzystanie przez nich z rozwiązań takich jak oprogramowanie zenon pomogło ograniczać liczbę osób znajdujących się w zakładach i kontakty między nimi. Menadżerowie, dzięki zdalnemu dostępowi do raportów oraz agregowaniu danych z wielu obszarów produkcji, mogli prowadzić spotkania ze swoich biur i zarządzać operacjami.
Z kolei dzięki możliwościom monitorowania i obsługi linii produkcyjnych z jednego panelu można było zoptymalizować liczbę operatorów, tak aby zapewnić wymagane odstępy i zapobiegać konieczności przemieszczania się osób. Do tego zagwarantowany był pełen zdalny dostęp do wszystkich maszyn w hali poprzez panele umieszczone w centrach zarządzania. W efekcie tego w czasie pandemii udało się utrzymywać restrykcje przy jednoczesnym zapewnianiu ciągłości produkcji.
Co również istotne, przedsiębiorstwa z nami współpracujące realizowały wszystkie zaplanowane wcześniej inwestycje. My również wspieraliśmy klientów, obsługując zamówienia, udzielając wsparcia technicznego oraz prowadząc szkolenia online. Koronawirus wywołał natomiast falę pytań i dyskusji o tym, jak w przyszłości zabezpieczać się przed podobnymi wydarzeniami. Jestem pewna, że jednym z rozwiązań jest zastosowanie Platformy Programowej zenon, która daje możliwość zdalnej pracy personelu i jednocześnie kontroli procesów produkcyjnych. Ogólnie zaś sądzę, że dzięki omawianej sytuacji wiele firm otworzy się na możliwości, jakie niesie ze sobą cyfryzacja.
- O cyfryzacji chciałbym porozmawiać szerzej, bowiem jej rozwój sprawia, że dzisiaj granica pomiędzy oprogramowaniem SCADA/HMI, MES i innymi narzędziami IT dla przemysłu zaciera się. Jak w ten trend wpisuje się rozwijany przez Was system?
Oprogramowanie zenon nigdy nie było produktem zamkniętym. Główną wytyczną w jego rozwoju było zapewnianie możliwości komunikacji z praktycznie dowolnymi urządzeniami automatyki oraz różnymi systemami, a także możliwość działania na różnych urządzeniach końcowych. W efekcie klient może swobodnie dobierać swój hardware, a także całość łatwo wpasowywać w istniejącą w zakładzie infrastrukturę.
Powyższe cechy są bardzo ważne w kontekście trendów cyfryzacji i integracji systemów. O ile bowiem nowe fabryki buduje się od razu w określonych standardach, o tyle dawniej często kupowano maszyny z różnych źródeł, w efekcie czego infrastruktura wielu polskich zakładów jest silnie zróżnicowana. Mając możliwość komunikacji z różnymi sterownikami i maszynami, mamy przewagę nad dostawcami rozwiązań dedykowanych, w tym pochodzących od producentów sprzętu. Jednocześnie zenon może być z powodzeniem wykorzystywany w branżach, w których produkcja jest regulowana przez liczne normy i regulacje prawne - np. w sektorze energetycznym, gdzie przesyłane dane muszą być zgodnie z odpowiednimi protokołami, czy też w branży farmaceutycznej, gdzie produkcja musi być prowadzona zgodnie z GMP.
Od początku działalności COPA-DATA inwestuje aż 25% obrotów w rozwój produktów, co roku wprowadzając na rynek nową wersję oprogramowania zenon. Do tej pory było ich 27! W 2018 roku zarząd podjął strategiczną decyzję o zmianie nazewnictwa produktu - od tamtej pory funkcjonuje on jako zenon Software Platform, czyli Platforma Programowa zenon. Sądzę, że krok ten najlepiej pokazuje drogę, jaką przeszło oprogramowanie - tj. od software’u o określonych funkcjach z zakresu wizualizacji danych oraz sterowania maszynami, do platformy, która zawiera w sobie funkcjonalności: HMI, SCADA, EDMS, BMS, MES oraz BI. Jednocześnie dzisiaj zenon może być porównany do kompletu klocków, z których można złożyć praktycznie dowolny projekt o cechach i modułach ściśle dopasowanych do potrzeb klienta. Ponadto w każdej chwili można go też łatwo rozbudowywać - zarówno pod względem funkcjonalnym, jak też liczby zmiennych.
- Jakie są przykładowe nowości?
W nowych wersjach zenon 8.20 oraz zenon Analyzer 3.40, których premiera miała miejsce w kwietniu tego roku, wprowadziliśmy szereg modyfikacji i usprawnień. W przypadku zenona jedną z innowacji były Smart Objects, które stanowią gotowe komponenty znacznie upraszczające prace inżynieryjne przy projekcie. Dzięki nim można tworzyć i wielokrotnie używać powiązanych ze sobą elementów, a także nimi łatwo zarządzać w ramach jednego pakietu w bibliotece. W nowej wersji wdrożono też technologię kontenerową Docker, która izoluje od siebie usługi i procesy, pozwalając na uruchamianie kilku modułów zenon Runtime na jednym serwerze. Sprzyja to skalowalności i zapewnia oszczędności w zakresie inwestycji i utrzymania sprzętu. Z kolei w zenon Analyzer 3.40 największą zmianą było dodanie biblioteki pyZAN, która pozwala na korzystanie z języka Python, rozszerzając możliwości wykonywania analiz predykcyjnych.
Planowana na przyszły rok wersja zenon 10 z pewnością zaskoczy naszych użytkowników. Jedną ze zmian będzie udostępnienie oprogramowania zarówno dla systemów Windows, jak i Linux. Dopracowywane będą również funkcjonalności związane ze Smart Factory, zwłaszcza w zakresie dotyczącym wykonywania analiz predykcyjnych oraz zapewniania bezpieczeństwa danych.
- Jak definiujecie pojęcie Smart Factory? Czym jest inteligentna fabryka?
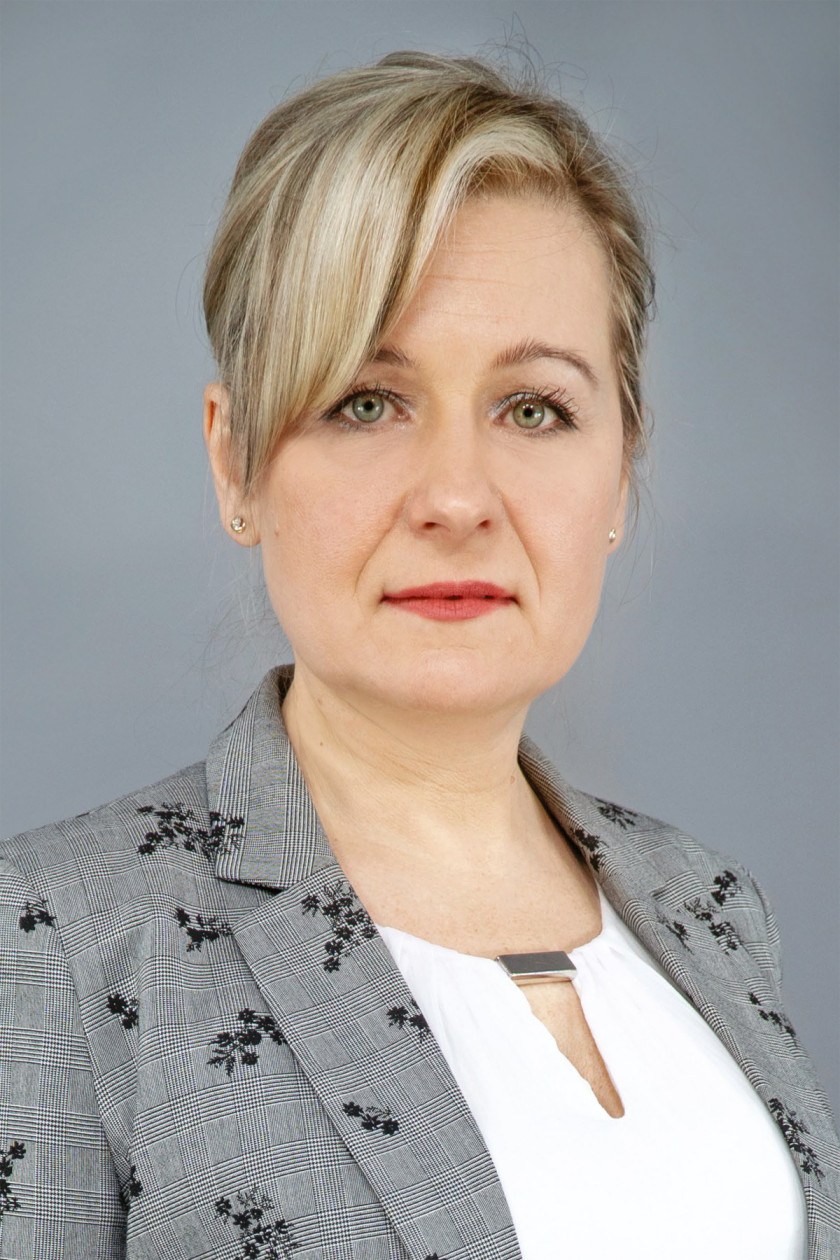
Rozwój Smart Factory związany jest z transformacją z tradycyjnego procesu automatyzacji do wykorzystania bardziej otwartego i elastycznego systemu. Jednocześnie dzięki połączeniu różnych zasobów - fizycznych, operacyjnych i ludzkich w całej fabryce, skuteczniej można zarządzać całym środowiskiem produkcyjnym. W szczególności obejmuje to komunikację pomiędzy maszynami, systemami produkcyjnymi, ale też produktami - np. z wykorzystaniem RFID. Wymiana danych i ich analiza pozwala na wprowadzanie zmian w czasie rzeczywistym, a także daje możliwość przewidywania, co zwiększa wydajność i elastyczność produkcji oraz redukuje liczbę przestojów.
W rozwoju inteligentnej fabryki szczególną rolę odgrywają rozwiązania z obszaru IoT. Są to różnorodne urządzenia podłączone do sieci komunikacyjnej - czujniki, przetworniki, kamery i wiele innych, które są potrzebne w zakładzie produkcyjnym do kontroli stanu i gromadzenia danych. Takie dane są następnie analizowane, zaś wyniki mogą być wykorzystywane do wizualizacji, kontrolowania różnych aspektów zautomatyzowanej produkcji oraz do jej optymalizacji. Są one również niezbędne do raportowania i efektywnego zarządzania procesami, obiektami czy sieciami zakładów. Platforma Programowa zenon firmy COPA-DATA zawiera w sobie rozwiązania wspierające te wszystkie zadania.
- Jak wyglądają w Polsce zagadnienia dotyczące inteligentnych zakładów produkcyjnych? Jak ogólnie podchodzić do rozwoju cyfrowych fabryk?
W Polsce tematyka ta jest często dyskutowana, otrzymujemy też wiele pytań od klientów z różnych branż i zakładów produkcyjnych. Dotyczą one różnorodnych zagadnień - tego, czy Smart Factory można wdrożyć w każdej fabryce, od czego zacząć, jakie są benefity, a także jakie są koszty i czas realizacji takich projektów. Świadomość klientów jest coraz większa, zaś u niektórych, zwłaszcza w firmach z kapitałem zagranicznym, tego typu wdrożenia są już zabudżetowane na przyszłe lata.
Natomiast jednak, z tego co obserwuję na różnych konferencjach, cyfryzacja jest ciągle przedstawiana jako wielki, skomplikowany projekt. Z tego też powodu firmy postrzegają Przemysł 4.0 jako wdrożenie długie, angażujące wiele osób i wymuszające zakup nowych maszyn produkcyjnych. A na takie zmiany patrzy się z niechęcią, zadając pytanie: "Czy warto?". Prawda jest jednak taka, że można je realizować krok po kroku, bazując na już posiadanych zasobach i zapewniając ich odpowiednią komunikację.
Oprogramowanie zenon ma ponad 300 driverów i protokołów komunikacyjnych, co umożliwia współpracę z praktycznie dowolnymi maszynami, a także łatwą integrację pionową i poziomą oraz komunikację z chmurą. Klient może zadecydować, jakie funkcje są mu potrzebne, a także później to odpowiednio rozbudować - np. o zarządzanie energią, zarządzanie produkcją, itd. Daje to możliwość wdrażania stopniowego lub obejmującego np. wybrane maszyny i stanowiska, a później dobudowania reszty. Docelowo wszystkie dane można wysyłać do chmury i dodawać kolejne zakłady produkcyjne. Tego typu cyfryzacja jest o wiele łatwiejsza do implementacji oraz nie wymaga dużych nakładów finansowych i kadrowych. I my, jako COPA-DATA, właśnie taką drogę do Smart Factory promujemy wśród klientów.
- Jak wygląda wspomniana chmura obliczeniowa w kontekście Waszej działalności?
Tematyką cloud computingu zajmujemy się od kilku lat współpracując tu z firmą Microsoft, i obecnie rekomendujemy w tym zakresie wykorzystanie modułu zenon Microsoft Azure. Jeśli chodzi o praktyczne zastosowania chmury obliczeniowej, to mamy już pierwsze wdrożenie w branży energetycznej. Projekt został wykonany w Gorenjske Elektrarne na Słowenii, gdzie stworzono system pozwalający na zdalne zarządzanie elektrowniami zlokalizowanymi w kilkunastu, odległych od siebie o kilkadziesiąt kilometrów lokalizacjach. Również w Polsce prowadziliśmy rozmowy dotyczące projektu chmurowego. Finalnie jednak zrealizowano go tradycyjnie z wykorzystaniem zenon Energy Edition, przy czym wskazano, że drugim etapem będzie udostępnianie danych w chmurze.
- Czy w przemyśle cloud computing ma również rację bytu?
Jak najbardziej! Za granicą, gdzie mamy takie realizacje, klienci mówią wyłącznie o plusach chmury. W Polsce niestety wciąż istnieją obawy, zwłaszcza w branżach silnie konkurencyjnych - takich jak farmacja czy motoryzacja, które dotyczą możliwości wycieku danych. Stąd też, jak na razie, nie udało się tutaj zrealizować takiego projektu. Niemniej jednak powstają wdrożenia o charakterze niekomercyjnym - na politechnikach i w instytutach badawczych. Dodam, że już w 2017 roku na targach Hannover Messe prezentowaliśmy z partnerami przykład aplikacji łączącej funkcje analityki predykcyjnej w maszynach i wymiany danych w chmurze. Oprogramowanie zenon w połączeniu z Microsoft Azure i algorytmami uczenia maszynowego pozwalało maszynie firmy KHS przesyłać do operatorów nie tylko dane dotyczące np. zużycia części, ale też podawać informacje o przewidywanym terminie serwisowania.
Sądzę, że zmiany niebawem nadejdą. Klienci coraz częściej skarżą się, że w ich zakładach przetwarza się tyle danych, że utrzymywanie całej infrastruktury staje się coraz kosztowniejsze. Do tego dochodzą kwestie bezpieczeństwa informacji, a tutaj zwykle najsłabszym ogniwem i tak jest człowiek. W mojej ocenie impuls do rozwoju może przyjść z zagranicy. Przetwarzanie w chmurze jest idealnym rozwiązaniem dla sieci zakładów należących do koncernów międzynarodowych, daje bowiem zarządom możliwość sięgania do danych z różnych fabryk - i to w czasie rzeczywistym! To bardzo duża zmiana, choć i tutaj pojawiają się dodatkowe kwestie do rozwiązania - choćby te dotyczące działów odpowiedzialnych za te projekty. Niemniej jednak kierunek został wytyczony i przechodzenie na rozwiązania chmurowe jest moim zdaniem kwestią niedługiego czasu.
- Jak ogólnie wygląda obsługa klientów lokalnych? Jakie są potrzeby firm?
Dzisiaj w projektach bardzo ważne jest zapewnianie kompleksowości. Realizujemy to poprzez trwający od 2011 roku program partnerski COPA-DATA Partner Community, w ramach którego współpracujący z nami integratorzy systemów oferują kompleksowe usługi wdrażania oprogramowania wraz z niezbędnym sprzętem, a także późniejsze utrzymywanie i serwisowanie instalacji. Mamy też odbiorców, którzy chcą być niezależni od partnerów i takim firmom udostępniamy środowisko zenon Editor, a także proponujemy odpowiednie szkolenia i wsparcie techniczne. Dzięki nim klienci mogą później wiele rzeczy robić samemu - np. rozbudowywać projekty o kolejne funkcje czy przeprowadzać aktualizacje.
Generalnie musimy być elastyczni, dopasowując się do potrzeb odbiorców. Dodatkowo, oprócz sprzedaży licencji, konsultingu i szkoleń, wprowadziliśmy też nową usługę - Professional Service, która dotyczy rozwoju funkcjonalności dla klientów. Nie chodzi tu o tworzenie aplikacji, ale o programowanie pewnych specyficznych funkcji na życzenie odbiorcy.
- A co z producentami maszyn oraz mniejszymi firmami produkcyjnymi?
Oprogramowaniem SCADA oraz MES interesowali się jeszcze niedawno głównie więksi przedsiębiorcy, zresztą uważano, że pewne narzędzia to domena tylko dużych firm. Dzisiaj jest to już przeszłość, bowiem system taki jak zenon jest zdecydowanie produktem również dla odbiorców z sektora MŚP. Mniejsi przedsiębiorcy mogą dzięki niemu optymalizować pracę swoich maszyn, stopień ich wykorzystania, ale też zarządzać produkcją i zużyciem energii. Dodatkowo inwestycja w elastyczne narzędzia zapewnia możliwość ich rozbudowy wraz z ewolucją samego zakładu.
Jeżeli chodzi o producentów maszyn i klientów końcowych, to są to zupełnie inne grupy firm, mające odmienne oczekiwania. Większość naszych kontrahentów w Polsce to odbiorcy końcowi, natomiast podmiotów OEM jest tu zdecydowanie mniej niż np. we Włoszech czy Niemczech. Aczkolwiek są to również bardzo ciekawe i rozwijające się przedsiębiorstwa - przykładem jest ZMR z Krakowa, który wytwarza maszyny dla przemysłu farmaceutycznego. Producenci maszyn korzystają z różnych możliwości oprogramowania zenon, przy czym często opierają się w swoich projektach na tzw. wizardach. Zapewniają one gotowe, dobrze przemyślane i łatwe do wdrożenia funkcjonalności dla różnych typów maszyn. I to trafia na podatny grunt, bowiem firmy preferują gotowe rozwiązania, które starają się jak najlepiej wykorzystać. Z kolei klienci końcowi oczekują bardzo indywidualnych funkcjonalności dopasowanych niejednokrotnie do stanowiska pracy czy też standardów danego zakładu - np. graficznych.
- Jakie są z Waszej perspektywy rozwijające się branże? Jakie projekty realizujecie poza typowym przemysłem i energetyką?
Coraz częściej wykraczamy poza rdzenne dla nas sektory. Przykładem są projekty związane z nowoczesnymi budynkami i miastami, gdzie wymagane jest zarządzanie energią i innymi mediami. Tutaj jako referencję mogę podać wdrożenie Smart City Barcelona, gdzie zenon odpowiada za nadzór nie tylko w zakresie energii, ale też zarządzanie oświetleniem ulicznym, parkingami i innymi obszarami miasta. Uważam, że sektor budynkowy jest bardzo ciekawy, choć też istnieje tu ogromna konkurencja i silna presja cenowa.
Rozwijamy obszar energetyki odnawialnej, w szczególności w zakresie fotowoltaiki, która jest obecnie w Polsce bardzo popularna. W centrum naszych ambicji pozostaje również rozwój wymagającej branży farmaceutycznej, gdzie firmy coraz częściej produkują na eksport. Jesteśmy silnie związani z tym rynkiem i oferujemy dla niego rozwiązanie zenon Pharmaceutical. Wiele projektów pojawia się też w sektorze napojowym, głównie w branży rozlewniczej. Tutaj ma obecnie miejsce dużo przejęć i pojawiają się nowe fundusze na inwestycje - np. w browarach craftowych.
Stawiamy ponadto na współpracę z uniwersytetami i uczelniami technicznymi głęboko zaangażowanymi w realizacje projektów z elementami Smart Factory. Niedawno przekazaliśmy na rzecz budowanego laboratorium badawczo-rozwojowego zlokalizowanego w Centrum Energetyki Katedry Energoelektroniki i Automatyki Systemów Przetwarzania Energii Akademii Górniczo-Hutniczej w Krakowie licencje zenon Energy Edition i sprzęt niezbędny do realizacji projektów typu smart w energetyce. Liczymy, że zenon Energy Lab przyczyni się do wyedukowania młodych inżynierów, którzy nabędą doświadczenie we wdrażaniu projektów cyfryzacji i będą je wykorzystywali w swojej dalszej karierze zawodowej.
Staramy się dywersyfikować obsługiwane przez nas rynki, jesteśmy otwarci na nowe projekty oraz wyzwania. Również nieustannie budujemy sieć współpracy i edukujemy obecnych oraz przyszłych klientów. W szczególności chcemy pokazywać, że tematyka Smart Factory nie jest czymś, czego powinniśmy się obawiać. Można tu zaczynać od małych kroków, rozwijać projekty ewolucyjnie, dochodząc na końcu z sukcesem do etapu zaawansowanych rozwiązań cyfrowych.
- Dziękujemy za rozmowę.