- Jak w polskich firmach rozwijany jest Przemysł 4.0? Czy nadal pokutuje jego postrzeganie jako produktu lub pojedynczej technologii?
Thomas Ilkow: Tak, niestety firmy nadal często traktują go jako rozwiązanie – produkt, który można wziąć z półki i zainstalować. A to błędne wyobrażenie o Przemyśle 4.0, bowiem mówimy również o zmianach organizacyjnych i całościowej transformacji firmy. My tutaj jesteśmy przede wszystkim dostawcą technologii umożliwiających łączenie maszyn oraz wszelakich urządzeń, odczytywanie z nich danych, ich dalsze przetwarzanie, analizę, a także innych rozwiązań cyfrowych i oczywiście powiązanej z tym wiedzy. Ale jak poszczególne firmy to wykorzystają – to już sprawa absolutnie indywidualna.
Adam Piszczatowski: Projekt Przemysł 4.0 bardzo często zaczyna się od jednej osoby, która interesuje się tym tematem i stara się do niego przekonywać innych. Tak jest zwłaszcza w mniejszych i średniej wielkości firmach, gdzie są pasjonaci. Niejednokroć zaczynają oni od rozwiązań typu smart home – przykładowo w domu instalują system kontroli działania żaluzji czy też ogrzewania, a później przychodzą do pracy i dostrzegają również tam miejsca do wprowadzania usprawnień. Takim obiektem może być problematyczna maszyna, którą trzeba cały czas kontrolować przez panel HMI i jednocześnie często wzywać do niej specjalistę będącego nieregularnie w firmie. A przecież lepiej by było, gdyby to wszystko widzieć i kontrolować z wykorzystaniem smartfona. Wtedy taki człowiek przychodzi do nas i mówi: „wiem, że macie możliwości monitorowania pracy urządzeń – czy możemy to rozwiązanie wypróbować u nas?”. I to są te pierwsze kroki. Po wdrożeniu, jak się okazuje, zaczynają przychodzić do niego pracownicy z innych działów z pytaniem: „dlaczego u was tak można, a u nas nie?”.
- Czyli każdy musi stworzyć Przemysł 4.0 wedle własnych potrzeb?
TI: Dokładnie tak! My nawet nie jesteśmy w stanie „wejść w buty” poszczególnych firm, bo bardzo często chodzi o konkretne procesy technologiczne i niuanse produkcyjne, o których wie tylko klient. Widziałem też próby powoływania organizacji konsultantów mających pomagać we wdrożeniach Przemysłu 4.0. Problem jednak w tym, że to nie za bardzo działa, bowiem trzeba zaczynać od procesów, a wiedzę w tym zakresie ma sam użytkownik instalacji.
AP: Przedstawię to na kolejnym przykładzie. Gdy przyjeżdżamy do klienta, to zazwyczaj pytamy go, z którą maszyną albo procesem ma największy problem i co chce poprawić. Wtedy odzywa się przykładowo pracownik utrzymania ruchu, który wskazuje maszyny stojące na końcu hali, do których musi codziennie chodzić, sprawdzać je itd. W sytuacji, gdy coś w nich się zepsuje, to część produkcji staje i trudno jest szybko przeanalizować problem, aby usunąć tę usterkę. Jest to temat dla nas, bowiem możemy pokazać, jak uzyskać z takiej maszyny potrzebne dane, jak ją monitorować, a nawet kontrolować zdalnie. W efekcie realizacji takiego relatywnie niedużego wdrożenia firma znacząco zmniejsza liczbę przestojów, bowiem teraz, przed każdą potencjalną awarią, może zaplanować przegląd i naprawę. I taki mały krok na początek wystarcza, aby rozpocząć przygodę z Przemysłem 4.0. Aczkolwiek dotyczy to najczęściej grupy MŚP, bo w firmach największych, szczególnie tych z kapitałem zagranicznym, bardzo często centrala wymusza pewne działania. Wtedy kontaktują się z nami ich przedstawiciele i od razu rozmawiamy o „zadanym” projekcie wdrożeniowym. Bardzo często zaczynamy tu od razu od rozwiązań condition monitoring i predictive maintenance, a później idziemy dalej.
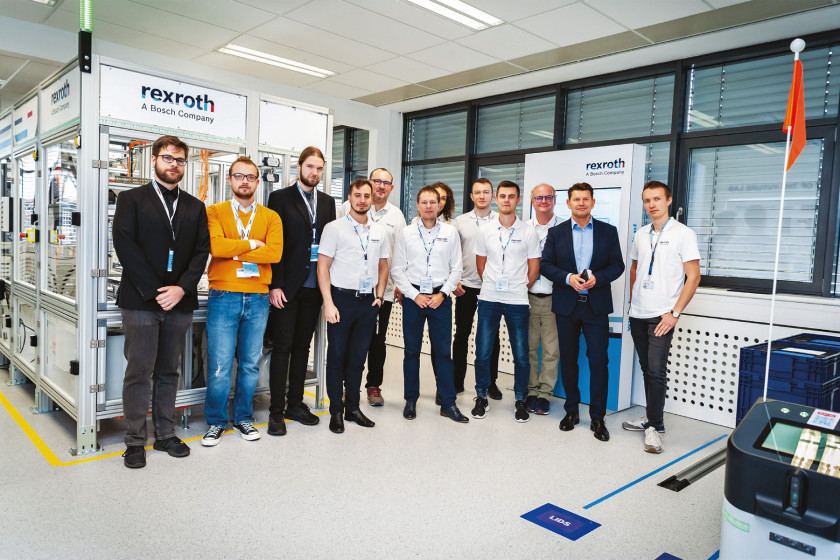
- Jaka była motywacja do stworzenia showroomu „Factory of the Future Lab”, na którego otwarciu spotkaliśmy się pod koniec września?
TI: Showroom jest odzwierciedleniem naszej wizji fabryki przyszłości. Jest ona miejscem, gdzie maszyny, urządzenia, instalacje technologiczne są elastyczne, można je przesuwać, dostosowywać do potrzeb rynku i zamówień klientów. Skoncentrowaliśmy się przy tym na istotnym dzisiaj aspekcie, którym jest możliwość kastomizacji przy zachowaniu masowości produkcji. Był to dla nas motyw przewodni w tworzeniu tej linii. Chcieliśmy też, aby była ona namacalnym przejawem Przemysłu 4.0, który zapewni naszym partnerom możliwości testowania nowych technologii i optymalizacji procesów produkcyjnych. Showroom miał być ponadto odpowiedzią na inne wyzwania rynku – związane z szybko rosnącymi kosztami energii, ale też problemami ze specjalistami branżowymi.
Przed rozpoczęciem projektu robiliśmy analizy, rozmawialiśmy z klientami i wielokrotnie zastanawialiśmy się, jak pokazać Przemysł 4.0. O ile pomysły, takie jak korzystanie z prezentacji w Power Point, już na wstępie odrzuciliśmy, o tyle rozważaliśmy wykorzystanie realnej linii produkcyjnej. Podobne rozwiązania znajdujemy zresztą w naszej fabryce Roberta Boscha w Mirkowie *), która jest wysoce zaawansowana, jeżeli chodzi o rozwój Przemysłu 4.0. Problematycznym okazało się jednak to, że z takiego obiektu nie można korzystać podczas jego pracy – a w każdym razie nie można wykorzystać go do eksperymentowania.
Stąd też wybraliśmy inną drogę – stworzenie własnego obiektu, który zaprojektowaliśmy, a do fazy jego realizacji i uruchomienia zaprosiliśmy parterów oraz studentów z Politechniki Warszawskiej. Integracja sytemu była dla nas dodatkową korzyścią, bowiem mogliśmy jeszcze lepiej poznać nasze urządzenia, dzięki czemu powstało dodatkowe know-how, z którego korzystamy w codziennej pracy z klientami. Linia w sposób namacalny połączyła też działy Factory Automation, co było ważne dla całego naszego zespołu i motywacji pracowników.
AP: Factory of the Future Lab służy rozpowszechnianiu wizji Przemysłu 4.0 – i to w bardzo praktyczny sposób. Pozwala dotknąć tych technologii, zapewnia klientom miejsce do rozwoju ich pomysłów i projektów, jest otwartym miejscem dla różnorodnych partnerów, uczelni i innych interesariuszy. Naszym zamierzeniem było pokazanie w nim całości procesu produkcyjnego z wykorzystaniem różnych technologii i rozwiązań automatyzacji, IT oraz cyfryzacji. Właściwie dotyczy to nie tylko samej produkcji, ale też intralogistyki, a więc dostarczania komponentów, przewozu produktów do magazynu, itd. Jest to również miejsce prezentacji działania nowoczesnych protokołów wymiany danych – pomiędzy urządzeniami, systemem, a także chmurą obliczeniową. Pozyskiwane informacje są wykorzystywane w celu optymalizacji procesów, kosztów, minimalizacji strat, a także stosowania strategii predictive maintenance. Zresztą ta ostatnia została przez nas wdrożona w zakładzie produkcyjnym BSH w Łodzi i zapewnia tam wymierne efekty w zakresie optymalizacji pracy pras do metali.
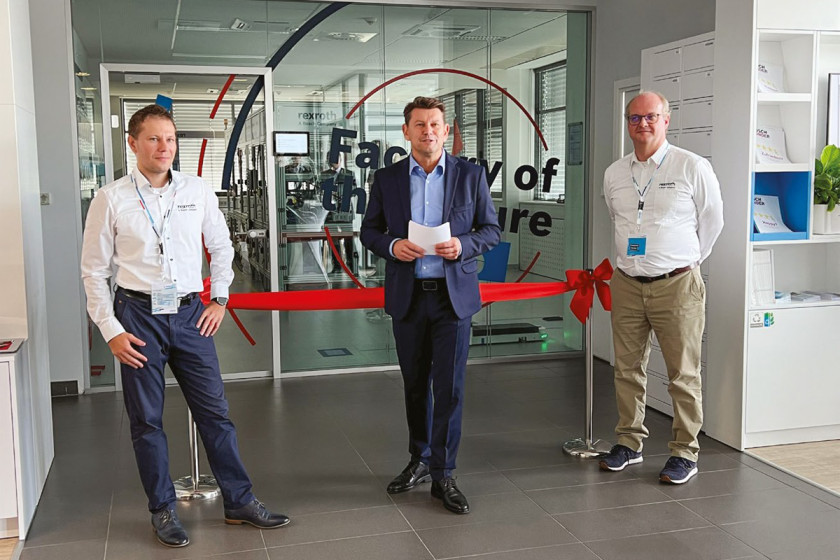
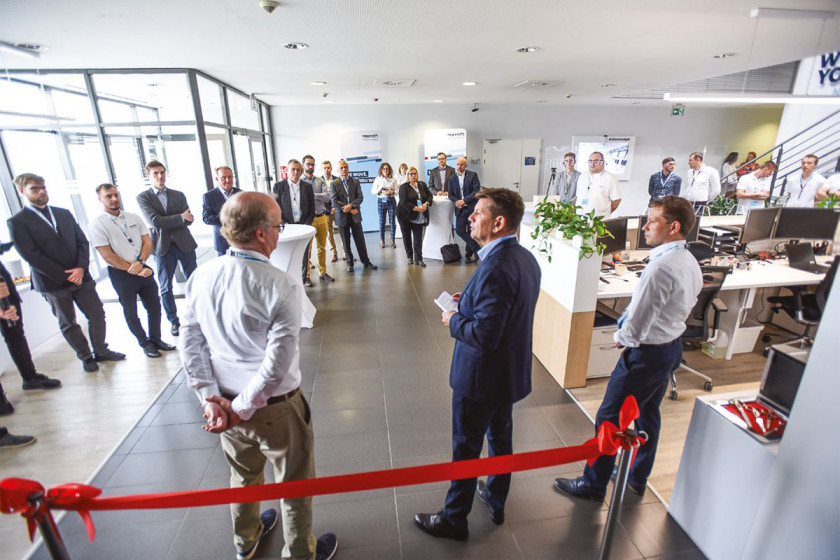
- Jakie technologie związane z Przemysłem 4.0 wdrożyliście?
TI: Zbudowana linia montażowa bazuje w większości na komponentach Bosch Rexroth, co obejmuje nasze napędy i serwonapędy, sterowniki i komputery przemysłowe, panele webowe, do tego m.in. też cobota oraz system z robotem mobilnym klasy AMR. Aczkolwiek wskazałbym tu trzy technologie Przemysłu 4.0, które stosujemy w showroomie i które sprawiają, że jest on naprawdę wyjątkowym obiektem.
Po pierwsze, korzystamy z oprogramowania napisanego w językach wysokiego poziomu. W ramach linii stworzyliśmy stanowisko oparte na ctrlX, czyli otwartej platformie automatyzacji bazującej na komputerze przemysłowym. W tym przypadku dodawanie kolejnych funkcjonalności wiąże się po prostu z dodawaniem aplikacji, które można pobierać z naszego serwisu internetowego. Do tego dochodzi możliwość korzystania ze wspomnianych języków wysokiego poziomu, popularnych w świecie IT, w tym graficznych, co zupełnie zmienia sposób projektowania systemów i ich elastyczność. Zresztą z wykorzystaniem platformy ctrlX z sukcesami wykonaliśmy szereg projektów u klientów i jest to rozwiązanie, które skutecznie łączy świat IT z przemysłowym.
Drugim z wyróżników są wyspecjalizowane aplikacje webowe. Dostarczają one oraz pobierają informacje z linii produkcyjnej, dzięki czemu maszyny mogą komunikować się ze sobą, z produktami oraz operatorami bez konieczności korzystania z systemów nadrzędnych.
Trzecią niezwykle istotną technologią jest cyfrowy bliźniak, a więc wirtualna reprezentacja urządzeń fizycznych. Zapewnia on odzwierciedlenie produktu realnego w świecie cyfrowym i pozwala na wykonywanie czynności na obiekcie rzeczywistym z pozycji wirtualnej, co przekłada się na możliwość lepszej optymalizacji, a także umożliwia pełne testowanie prototypów oraz wykluczanie błędów.
- Przespacerujmy się po showroomie…
AP: Podstawą naszej linii jest system Przemysłu 3.0 obejmujący mechanikę, napędy i wiele innych komponentów. Linia składa się ze stanowisk montażowych oraz systemu transportowego, w którym wykorzystujemy różnorodne silniki liniowe i obrotowe, do tego dołożyliśmy roboty. Z kolei w szafach są napędy, serwonapędy, sterowniki i różnorodne komponenty elektroniczne. W tej formie linia była gotowa do kolejnych działań – integracji ze światem Przemysłu 4.0.
Rdzeniem Industry 4.0 jest cyfryzacja i wykorzystanie rozwiązań IT. Zastosowane w linii czujniki cyfrowe, oprócz możliwości komunikacji z różnymi komponentami, takimi jak PLC czy serwonapędy, zapewniają też pozyskiwanie danych, które są następnie zbierane i przetwarzane. Wykorzystujemy je bezpośrednio do sterowania pracą linii, a także przesyłamy do chmury obliczeniowej, gdzie wdrożyliśmy różnorodne usługi zapewniające wartość dodaną. Możemy przykładowo wykorzystywać sieci neuronowe w celu podejmowania decyzji, analizować z ich użyciem dane wizyjne, itd. Połączenie światów IT/ OT jest w tym miejscu bardzo dobrze widoczne.
Inną z cech odróżniających instalację od rozwiązań klasycznych jest to, że nie mamy tutaj systemu nadzorującego, który przesyła dane z góry i musi zawsze pracować, aby linia mogła funkcjonować. Została ona tak stworzona, aby komunikacja występowała poziomo, tj. pomiędzy poszczególnymi stanowiskami. Aby to osiągnąć, wykorzystaliśmy możliwości związane z programowaniem współbieżnym i obiektowym. Przykładowo, gdy robot wykonuje pracę i opróżni się jego bufor, to sam wysyła żądanie do pojazdu AGV, aby zrealizował on zlecenie przywiezienia surowców. Jest to istotne skrócenie drogi komunikacji, ale też przykład na to, że nie trzeba stosować systemu scentralizowanego. Taka rozproszona architektura ogromnie sprzyja elastyczności.
Jeżeli mówimy o komunikacji end- to-end, to jest ona realizowana nie tylko na poziomie maszyna-maszyna, ale też pomiędzy maszynami i ludźmi, a także maszynami, produktami i ludźmi. W naszej linii również produkty są włączone w obieg cyfrowy i to one „wiedzą”, co przykładowo musi w danym momencie wykonać robot. Jest to koncepcja smart product, która prowadzi do tego, że każdy wyrób może być inny. Innymi słowy, realizujemy ideę masowej kastomizacji.
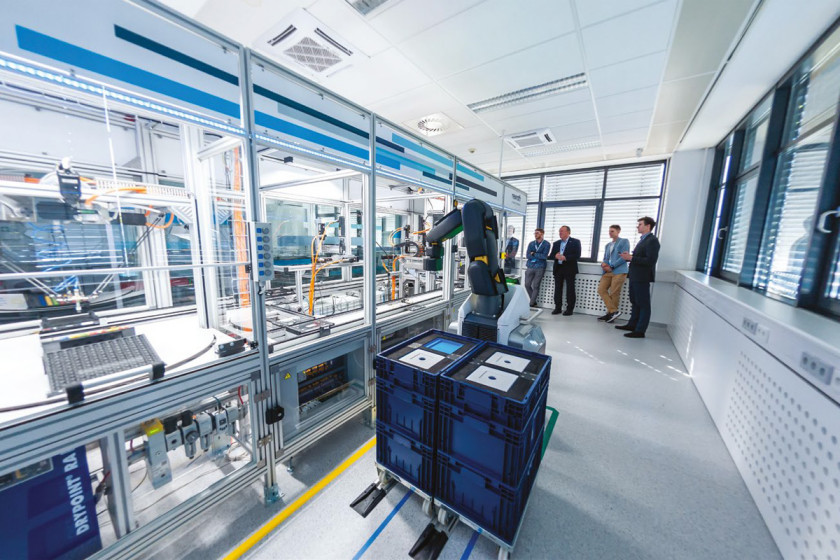
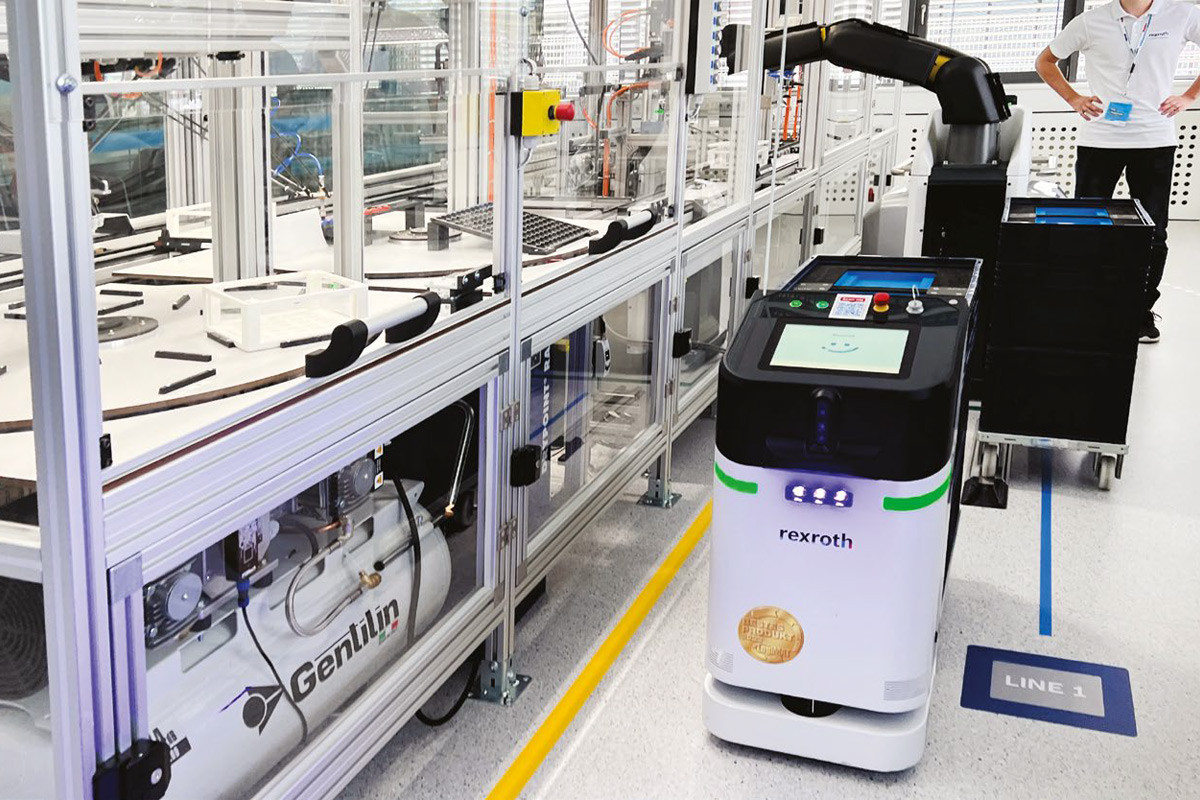
- Przyglądając się linii, można też zauważyć dodatkowe elementy, takie jak choćby wykorzystanie druku 3D czy systemów wsparcia dla montażu ręcznego…
AP: Tak, druk addytywny wykorzystaliśmy do przygotowania komponentów naszej linii. Dotyczy to m.in. pudełek na wytwarzane produkty oraz podajników, które zostały przez nas zaprojektowane i wydrukowane. Taka produkcja jest powiązana z Przemysłem 4.0, bowiem pozwala na pełną indywidualizację komponentów i części zamiennych.
Elementem linii jest także stanowisko montażu ręcznego, które jest również skomunikowane z resztą systemu. Zapewnia ono ergonomiczną, efektywną pracę dzięki możliwościom personalizacji – m.in. pod względem języka komunikatów, stosowanych narzędzi, prowadzenia operatora względem procesu i wsparcia wizualnego. System dynamicznie dokonuje nastaw narzędzi – np. wkrętaków i informuje operatora odnośnie do kolejnych czynności. To też dzieje się dzięki przekazywaniu informacji przez same produkty.
W Przemyśle 4.0 kluczowa jest dostępność danych i łatwa możliwość ich wymiany, dlatego też w przypadku naszej linii zrealizowaliśmy przykładową implementację lokalnej sieci komunikacyjnej. Bazuje ona na switchach firmy Phoenix Contact. Dołożyliśmy do tego funkcjonalność pozwalającą na zdalny dostęp do maszyny. Dzięki temu możemy oglądać wszystko na panelach webowych, co daje zarówno widoczność produkcji, jak też możliwość aktywnego wpływania na nią i przeprogramowywania systemów – również zdalnie. Dodatkowo zwróciliśmy uwagę na kwestie cyberbezpieczeństwa.
Dochodzimy tu jeszcze do tematyki Big Data, którą również chcieliśmy pokazać w praktyce. Jako że zbieramy duże ilości informacji cyfrowych podczas produkcji, możemy wykonywać na nich różnorodne analizy i korzystać z wyników w celu optymalizacji pracy systemu. Pozwala to na zwrotne wprowadzanie zmian w linii produkcyjnej, tak aby osiągać różne efekty, w szczególności optymalizować procesy wytwórcze. Jest to zresztą bardzo ciekawy, rozwojowy obszar do tworzenia projektów studenckich.
Finalnie linia pozwala na korzystanie z urządzeń przenośnych – smartfona, tabletu, a niebawem też okularów VR/ AR. Pozwala to operatorowi na łatwy dostęp do informacji i sterowanie systemami produkcyjnymi, w tym zdalnie. Tego typu rozwiązania cyfrowe stają się w przemyśle coraz bardziej popularne i, jak sądzę, z czasem wiele z nich będzie powszechnie stosowanych. W showroomie demonstrujemy też zagadnienia związane z energooszczędnością, w szczególności zwrotem energii do sieci oraz analizą zużycia mediów.
- Droga do Przemysłu 4.0 to proces zmian w organizacjach i wykorzystywanych przez nie technologiach. W którym miejscu znajdują się Wasi klienci?
AP: Zauważamy tu zarówno przykłady sukcesów, jak też, niestety, w wielu przypadkach porażek. I wcale nie wynikają one z przyczyn technologicznych. Pamiętam, jak raz pojechaliśmy do klienta z ciekawym rozwiązaniem edge’owym. Uruchomiliśmy je w ciągu jednego dnia, zaczęliśmy zbierać dane i przekazywać do chmury. Dodatkowo wdrożyliśmy prosty system webowy z panelem operatorskim oraz oprogramowaniem analitycznym. Gdy prowadziliśmy trzymiesięczne testy, zaczęliśmy zauważać, że po stronie klienta nie ma kompetencji pozwalających na korzystanie z tego rozwiązania. Pojawiały się przestoje, awarie, więc wróciliśmy do rozmów. Zdaniem użytkownika rozwiązanie było super, ale firma nie była na nie organizacyjnie przygotowana. Po pierwsze, nie miała analityka danych, czyli kogoś, kto mógłby wnioskować na podstawie uzyskiwanych danych. Po drugie, nie było osoby, która na bieżąco dostosowywałaby system do procesów i potrzeb w zakresie redukowania przestojów oraz ostrzegania o potencjalnych awariach. I sytuacja ta była bardzo typowa – w bardzo wielu zakładach brakuje kompetencji po stronie analizy danych, wnioskowania i zarządzania omawianą tematyką.
Inaczej jest w organizacjach większych, które mają kosztowne procesy – np. obejmujące duże prasy czy złożone ciągi maszynowe, gdzie koszty przestojów liczone są w dziesiątkach tysięcy euro. Przykładowo wdrażaliśmy monitorowanie procesu w zakładzie produkującym umywalki. Tam kierownictwo od razu wiedziało, że będą też potrzebni analitycy danych – i był to akurat jeden z przykładów udanych wdrożeń z obszaru Przemysłu 4.0. Swoją drogą w Grupie Bosch mamy też usługę konsultingu, który dostarczany jest przez dział będący autorem oferowanego przez nas systemu monitorowania. Zatrudnia on konsultantów oraz analityków danych, których można wynająć na czas projektu lub na dłuższy okres.
W projektach Przemysłu 4.0 oprócz zmiany technologicznej i procesowej wymagana jest także zmiana mentalna. W szczególności chodzi o współpracę inżynierów OT i IT – muszą oni jak najwięcej rozmawiać ze sobą. Powinien też powstać nowy rodzaj kompetencji – inżyniera Przemysłu 4.0, o czym mówi się w naszej branży już od pewnego czasu, ale wcale nie oznacza to faktycznej realizacji tego postulatu.
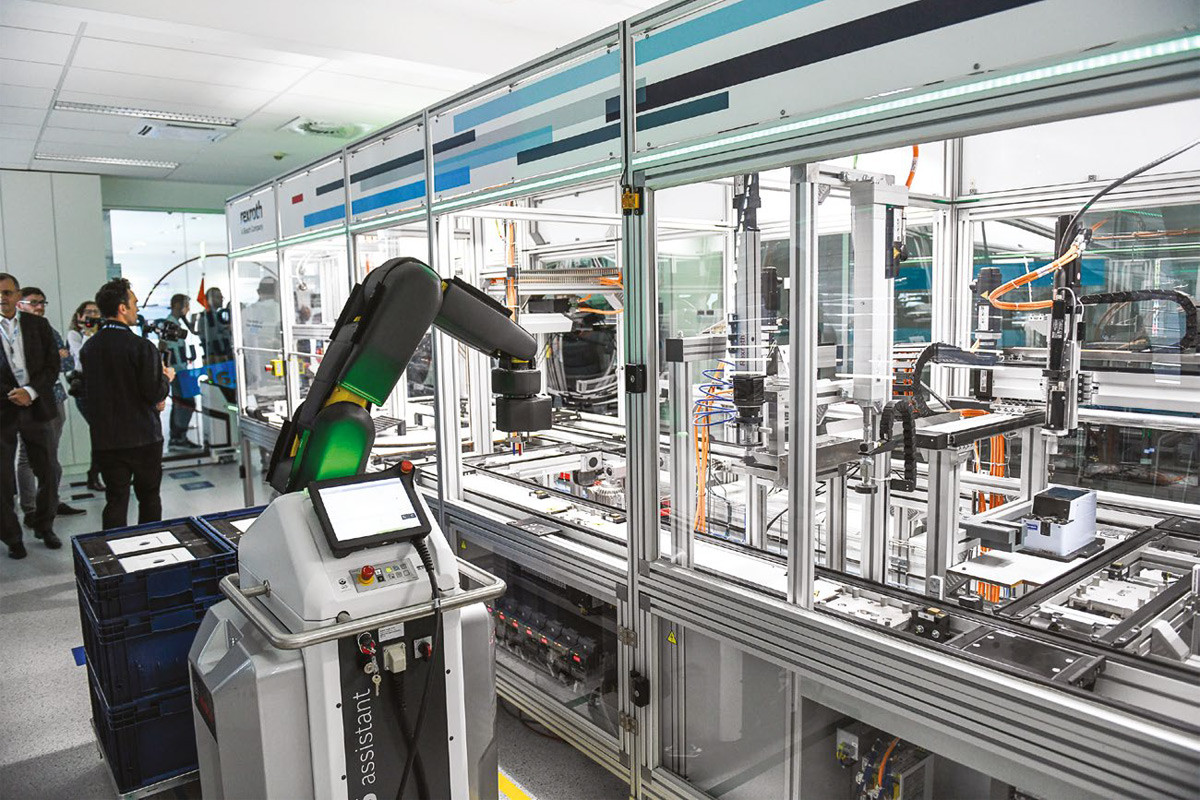
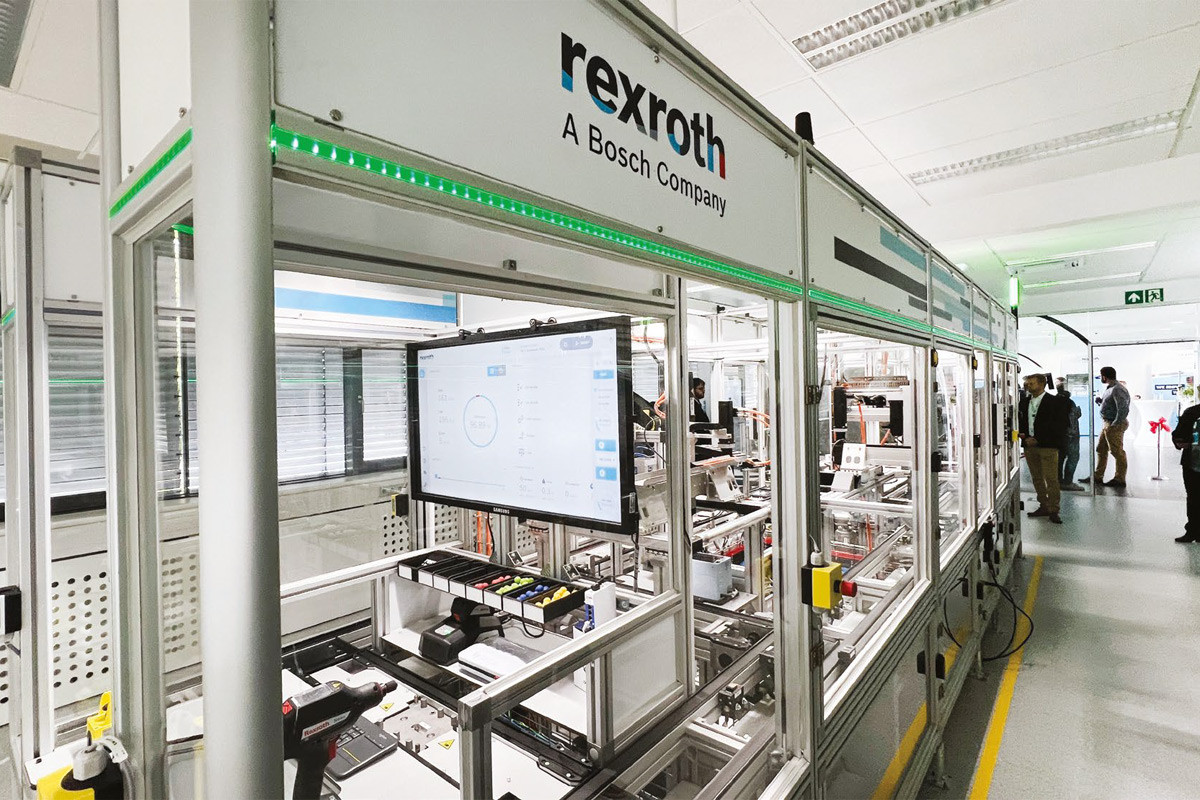
- Czy nowy showroom ma pełnić również funkcję takiego miejsca wymiany informacji i idei? Kogo do niego zapraszacie?
AP: Showroom jest miejscem dla naszych klientów, partnerów i innych interesariuszy. Pomimo że otwieramy go oficjalnie dopiero teraz, udało nam się już wcześniej przeprowadzić w nim szereg szkoleń. Z uczelniami współpracowaliśmy od samego początku – zarówno przy tworzeniu obiektu, jak też obecnie, zapraszając do odwiedzin zarówno politechniki, jak też szkoły techniczne.
W przyszłości będziemy organizować dodatkowo szkolenia tematyczne. Na razie działamy bardziej na zasadzie warsztatów – demonstrowania klientom, jakie są możliwości linii z zaimplementowanymi rozwiązaniami Przemysłu 4.0. Pokazujemy też, co można zrobić z już posiadanymi maszynami, szczególnie że podobny sprzęt mają klienci u siebie. Czasem wystarczy tylko włączyć daną opcję albo zainstalować określony serwer czy bazę danych. A jeśli klienci nie mają jeszcze jakiejś technologii, to poprzez wizytę w showroomie chcemy ich do niej przekonać. Mogą przyjechać, dotknąć, zobaczyć, nie bojąc się, że coś zepsują. To taki praktyczny warsztat Przemysłu 4.0.
TI: Sporo rozmawiamy tu o rynku przemysłowym, stacjonarnym, ale dodałbym, że widzimy też duży potencjał w sektorze maszyn samojezdnych – kombajnów, koparek, podnośników, dźwigów, itd. W tym kontekście pojawiają się następne aspekty – przede wszystkim bezpieczeństwa, gdzie wykorzystanie gatewayów, sensoryki i innych rozwiązań bardzo pomaga klientowi w monitorowaniu parametrów maszyn oraz ich śledzeniu.
Jako przykład mogę podać współpracę z firmą, która produkuje maszyny kopalniane. Podczas eksploatacji u jednego z jej klientów często dochodziło do awarii maszyny i nie wiadomo było, z jakiego powodu. Jako że byliśmy odpowiedzialni za jej napęd hydrauliczny, w okresach reklamacyjnych ciągle wracały do nas sygnały o dziwnych awariach. I my również dziwiliśmy się, że awariom ulegały tam z reguły bardzo niezawodne pompy układu hydrostatycznego. Po zamontowaniu sensoryki, wdrożeniu zbierania i przetwarzania danych okazało się, że użytkownik końcowy wykorzystywał tę maszynę w innym celu, niż została przewidziana! Stosowano ją do ścinania i szlifowania podłóg w kopalni. Była to więc analiza nie tyle w kontekście predictive maintenance, ale bezpośrednio w celu wykrycia parametrów pracy i użytkowania maszyny.
AP: Ten przykład jest bardzo ważny, bowiem naszymi klientami są nie tylko użytkownicy końcowi, ale też producenci maszyn. Mamy coraz więcej pytań, jak dołożyć do maszyny komponent, który pozwala zarówno zbierać na bieżąco dane, jak też zapewnia zdalną dostępność online. Oczywiście mamy takie rozwiązania, ale zawsze wymaga to przeanalizowania danej aplikacji, tak aby zapewnić jej bezpieczeństwo, w szczególności cyberbezpieczeństwo.
- Pokazujecie się jako kompleksowy dostawca technologii automatyzacji – nie tylko w przypadku showroomu, ale ogólnie na rynku. Jakie produkty w zakresie automatyzacji są dzisiaj kluczowe? Co jeszcze zmienia się w firmie Bosch Rexroth?
AP: Jest tym zmiana organizacyjna, w efekcie której ukierunkowaliśmy się również na projekty. Obecnie w naszej firmie dysponujemy nie tylko świetnymi automatykami, ale i deweloperami, w tym webowymi, a także specjalistami od sieci komunikacyjnych i cyberbezpieczeństwa. Oczywiście mówię tu o specjalistach działających w ramach całej Grupy Bosch w Polsce. Dzięki nim jesteśmy dobrze przygotowani do tego, aby obsłużyć dowolne wyzwania związane z automatyzacją, cyfryzacją i technologiami IT. Dotyczy to w szczególności pozyskiwania i przesyłania danych – między maszynami, do i z chmury, a także komunikowania informacji ludziom.
Właśnie to, o czym mówię, jest dla nas wyznacznikiem Przemysłu 4.0. Nie chodzi o sprzedanie klientowi produktu, który ma sobie sam implementować, ale liczy się podejście kompleksowe, projektowe. Proponujemy elementy składowe, coś na kształt klocków, z których budowane są intuicyjne dla użytkowników rozwiązania, które można później zmieniać zależnie od nowych potrzeb firmy i sytuacji na rynku.
TI: Mówiąc o kluczowych, przełomowych produktach, wskazałbym na ctrlX. Jest to uniwersalna platforma i tworząc ją, poszliśmy zupełnie inną drogą niż reszta rynku – postawiliśmy na pełną otwartość oraz kompatybilność z dowolnymi, również konkurencyjnymi produktami i systemami. Jest to rozwiązanie zarówno dla integratorów i odbiorców końcowych, jak też producentów maszyn. W przypadku firm OEM pozwala na implementację wszystkiego w jednym „pudełku”, tj. komputerze przemysłowym. Nieważne, czy potrzebujemy PLC, urządzenia brzegowego, bramki, czy chodzi o zbieranie danych i zdalny dostęp, czy też analizę danych – wystarczy wgrać odpowiednią aplikację i już! Dodatkowo ctrlX daje możliwość użycia w systemach z praktycznie dowolnymi technologiami stosowanymi w branży. Pozytywna reakcja z rynku oraz liczne przykłady aplikacji u naszych klientów na całym świecie potwierdzają nasze pierwotne założenia.
- Jakie zmiany planujecie w przyszłości, szczególnie w odniesieniu do showroomu?
TI: Pozytywny odzew klientów już nas odwiedzających i szkolących się tutaj sprawił, że podjęliśmy decyzję o rozszerzeniu naszego laboratorium. Powstaną dodatkowe pomieszczenia, które pozwolą na prezentację rozwiązań cyfrowych m.in. w zakresie hydrauliki stacjonarnej i mobilnej. Chcemy też zaprezentować nasz program eLion, czyli napędy elektryczne w technologii 700 V dla maszyn samojezdnych.
AP: W związku z tym, że rozwijamy nasze portfolio AGV, rozszerzając je o modele pozwalające na przewożenie europalet, bardzo interesuje nas praktyczne pokazywanie robotów mobilnych. Tyle że potrzeba na to dużo miejsca. Myślimy też o następnym fragmencie obejmującym system transportowy i aplikację pick&place, co ma pozwolić na demonstrację procesu transportu i pakowania produktów. Jesteśmy na rynku aktywni w obszarze food and packaging i chcemy pokazywać rozwiązania z tego zakresu.
Ponadto planujemy zaimplementować technologię Augmented Reality. Chodzi tu o wykorzystanie okularów AR, które dadzą możliwość zaawansowanych interakcji z linią produkcyjną. Mamy dużo projektów i pomysłów – wiele z nich przekazujemy do Politechniki Warszawskiej jako tematy projektowe. W efekcie showroom to bardzo ciekawe miejsce dla studentów, gdzie mogą dotknąć technologii, zaś dla nas jednocześnie okazja, aby znaleźć kompetentnych, mających pasję pracowników.
TI: Przez ostatnie dziesięciolecie z firmy o korzeniach hydrauliki przemysłowej staliśmy się przedsiębiorstwem technologicznym kompleksowo obsługującym przemysł. Jeszcze kilkanaście lat temu nikt chyba nie pomyślałby, że firma Bosch Rexroth będzie otwierała showroom z obszaru automatyki – i to nie teoretyczny, ale bardzo praktyczny. Wszystkie prezentowane u nas rozwiązania mają już realne zastosowania w przemyśle – zapraszamy klientów i inne osoby, aby przyjeżdżali do nas, poznawali je i wypróbowywali z własnymi pomysłami!
- Dziękujemy za rozmowę.
*)
- Industry 4.0 w zakładzie Robert Bosch w Mirkowie
- Relacja z fabryki referencyjnej Grupy Bosch w Haiger
- „Czym jest Przemysł 4.0” – wyjaśnienie w pigułce