Znajdujący się w podwrocławskim Mirkowie zakład koncernu Robert Bosch to producent podzespołów do systemów układów hamulcowych, takich jak zespoły mocy oraz pompy hamulcowe ze zbiornikiem. Jednostka należy do dywizji Robert Bosch Chassis System Control i współpracuje z większością producentów motoryzacyjnych na świecie, w tym z takimi markami premium jak BMW i Tesla.
Od września 2016 roku wytwarza zespoły mocy iBooster, które są przeznaczone do pojazdów hybrydowych i elektrycznych. Pozwalają one uzyskiwać ciśnienie w układzie hamowania trzykrotnie szybciej niż tradycyjne systemy korzystające z układu podciśnieniowego. Firma wdraża również wiele rozwiązań z obszaru Industry 4.0. Na temat produkcji oraz cyfryzacji fabryki rozmawiamy z jej lokalnymi przedstawicielami.
Osoby wypowiadające się w wywiadzie:
|
- Jak wyglądała rozbudowa wytwarzanego tutaj asortymentu produktów i historia samego zakładu?
Wojciech Grądalski: Fabryka Grupy Bosch zlokalizowana w Mirkowie należy do dywizji Bosch Chassis System Control. Historia zakładu sięga lat 60. zeszłego wieku, kiedy rozpoczął on działalność w Twardogórze. W 1996 roku został przejęty przez koncern Bosch od firmy Allied Signal już jako wytwórca komponentów dla przemysłu motoryzacyjnego.
Dwoma krokami milowym w historii były: wdrożenie produkcji zespołów mocy w 1997 roku oraz przeniesienie zakładu do nowej lokalizacji w Mirkowie. To ostatnie nastąpiło w 2003 roku, gdy od podstaw wybudowana została nowa hala produkcyjna. W kolejnych latach zakład kontynuował rozwój pod zarządem Boscha, rozpoczynając w 2006 roku produkcję nowoczesnego jak na owe czasy zespołu mocy NOAH.
W okresie od 2007 do 2010 roku byliśmy nominowani do dwóch dużych projektów. Związane one były z produkcją zacisków hamulcowych dla Volkswagena do platformy PQ35 oraz dla BMW do platform F25, F20 i F30, a także produkcją zespołów mocy w przypadku BMW. Były to bardzo duże wolumeny produkcyjne, przez co zakład rozrósł się pod względem liczby pracowników. Dodatkowo w 2009 roku zwiększyliśmy powierzchnię produkcyjną poprzez rozbudowę hali.
W 2012 roku Bosch zdecydował się sprzedać biznes związany z wytwarzaniem zacisków hamulcowych, czego efektem była wolna powierzchnia produkcyjna, która pozostała w Mirkowie po sfinalizowaniu transakcji. Kolejne lata wiązały się z prężnym rozwojem fabryki w kierunku produkcji konwencjonalnych zespołów mocy, aż do przełomowego wydarzenia, które miało miejsce w 2016 roku - rozpoczęcia produkcji zupełnie nowej generacji zespołu mocy - iBoostera. Później nastąpił dalszy wzrost produkcji obydwu grup produktów, a w 2018 roku uruchomiliśmy wewnętrzny proces anodowania.
Obecnie zakład przekroczył magiczną liczbę tysiąca zatrudnionych osób, a przed nami uruchomienie produkcji iBoostera generacji drugiej. W ostatnich latach, oprócz mających miejsce wzrostów i przemian związanych z produkcją, powstawał zespół R&D. Dzięki niemu zbudowane zostały lokalne kompetencje, które umożliwiły obecnie przejęcie przez nas całkowitej odpowiedzialność wewnątrz Grupy Bosch za design zbiornika płynu hamulcowego.
- Jak wygląda organizacja produkcji? Z jakich maszyn i oprogramowania korzystacie?
Sławomir Szczuplak: W zakładzie w Mirkowie stosujemy dwa rodzaje linii: w pełni automatyczne, gdzie operacje montażowe wykonywane są niezależnie od operatorów, oraz półautomatyczne, gdzie część procesu wykonywana jest przez pracowników. Nasz ciąg technologiczny zaczyna się od maszyn obróbczych CNC, następnie obejmuje proces anodowania i końcowego montażu zespołów mocy. W pierwszym etapie montujemy części hydrauliczne (pompy TMC), gdzie wymagane jest zachowanie najwyższych standardów czystości, a następnie całe zespoły mocy.
W zakładzie używamy najnowszych rozwiązań produkcyjnych, zaś Industry 4.0 jest jednym z elementów naszej strategii rozwoju. Poziom produkcji z roku w rok rośnie. W tym roku planujemy wolumen na poziomie 4 milionów sztuk, natomiast w 2021 przekroczymy poziom 5,5 miliona wytworzonych produktów.
Dariusz Downer: Bosch rozwinął system klasy MOM - Nexeed MES, który zapewnia informacje o procesach produkcyjnych w czasie rzeczywistym. Dostępność danych jest podstawą udanej optymalizacji, planowania i kontroli procesów. Nexeed MES daje nam dokładne informacje, których potrzebuje nasz zakład w zakresie jego aktywnego nadzorowania, płynnej dokumentacji, śledzenia, zapewnienia jakości i kontroli całego strumienia wartości produkcji.
Celem jest ciągła optymalizacja procesów w oparciu na tych danych, tak aby szybko reagować na zmiany. System zapewnia integrację pionową od czujnika aż do chmury obliczeniowej, w rezultacie stanowiąc połączenie między poziomem sterowania maszynami a systemami ERP.
- Czy wykorzystywanie systemów MES wiąże się z koniecznością ścisłego rejestrowania produkcji i względami bezpieczeństwa?
DD: W sektorze motoryzacyjnym istnieje obowiązek zbierania szeregu informacji o procesie produkcyjnym, przy czym parametry związane z produktem muszą być przechowywane przez 15 lat po zakończeniu produkcji seryjnej. We Wrocławiu zaczęliśmy korzystać z systemu MES w 2006 roku, natomiast w Grupie Bosch - kilka lat wcześniej.
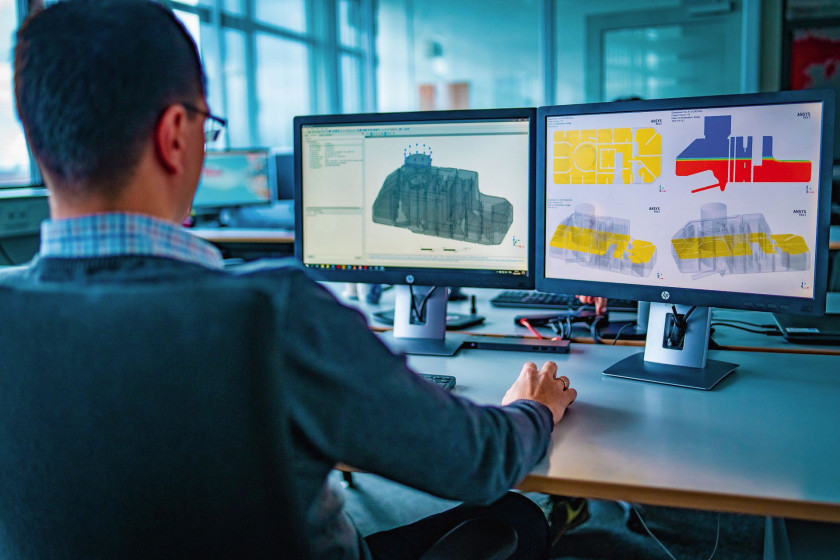
WG: Wymaganiem w branży automotive jest możliwość śledzenia odtworzenia parametrów produkcji i wyników testów dla wyrobów wysłanych do klienta. Jest to tzw. parts traceability. Dla każdej pojedynczej wyprodukowanej części jesteśmy w stanie odtworzyć określone, kluczowe kroki procesu wytwarzania oraz testowania wyrobu - np. momenty dokręcania śrub, wyniki testów szczelności, itd.
- Porozmawiajmy o Przemyśle 4.0 - jak rozumiecie to pojęcie i z czym w praktyce się ono wiąże?
DD: Wdrażanie rozwiązań Industry 4.0 traktujemy jako proces wieloetapowy, który rozpoczyna się od podłączenia maszyn do systemów zbierania i analizy danych, wdrożenia odpowiedniego oprogramowania oraz gromadzenia informacji i tworzenia wiedzy. Dzisiaj w zakładzie w Mirkowie jesteśmy na tym poziomie, natomiast punktem docelowym jest automatyzacja procesów podejmowania decyzji.
Chodzi tu przykładowo o algorytmy bazujące na sztucznej inteligencji, które zaproponują ścieżki do osiągnięcia danego celu. W praktyce przykładem może być: "za ileś dni na danej maszynie nastąpi awaria i należy podjąć następujące działania: wdrożyć to i to, przeplanować produkcję, dokonać korekty procesu, itd. Omawiane algorytmy mogłyby być również stosowane w planowaniu w innych obszarach - np. związanych z dostawami, procesami logistycznymi czy harmonogramowaniem pracy ludzi.
Piotr Pyzio: Może zacznę od tego, czym na pewno nie jest Industry 4.0. Już od dłuższego czasu odnoszę wrażenie, że wiele organizacji chce określać wszystko mianem Przemysłu 4.0. Przykładem może być raport godzinowy pracowników fabryki, który dawniej był na kartce papieru, a teraz zapisuje się go w Excelu na laptopie. Takie działanie, podobnie jak wstawienie kilku monitorów na produkcję, to jeszcze nie Industry 4.0.
Według mnie granicą, którą należy przekroczyć, aby rozwiązanie określić mianem "4.0", jest możliwość przewidywania zdarzeń, które mogą wystąpić w procesach produkcyjnych. Przykładem może być prognoza żywotności wrzeciona w centrum obróbczym.
Na podstawie sygnałów rejestrowanych przez maszynę, a także w oparciu na analizie danych historycznych powinniśmy otrzymać informację o wymianie wrzeciona przed awarią, która może kosztować setki tysięcy złotych. Podobnie analiza danych w procesach "in-directowych" może przynieść wymierne korzyści w zarządzaniu firmą. Kolejnym etapem będzie wykorzystanie w tych procesach elementów sztucznej inteligencji.
- Jaka jest metodologia wdrażania projektów z omawianego obszaru? Czy zmiany te są wymagane przez koncern globalnie?
PP: Jesteśmy zobowiązani, aby co roku podnosić naszą produktywność. O ile jeszcze dekadę temu wydajność procesów produkcyjnych mogła być zwiększana tradycyjnymi metodami, o tyle obecnie jesteśmy w punkcie - a mówimy tu o wskaźniku utylizacji zbliżającym się do 90% - że osiągnięcie dalszych usprawnień staje się trudne. W takiej sytuacji standardowe podejście do optymalizacji pracy czy zadań z obszaru utrzymania ruchu nie daje już rezultatów i coraz częściej musimy stosować rozwiązania, dzięki którym możemy zupełnie inaczej analizować fakty i kojarzyć zmienne.
Z jednej strony mamy w organizacji centralną komórkę, która ma całe portfolio rozwiązań technologicznych. Z drugiej strony bardzo istotna jest międzynarodowa współpraca i wykorzystanie potencjału lokalnych specjalistów, które po procesie standaryzacji zasilają globalną bazę dostępnych rozwiązań. W fabryce pod Wrocławiem także pracujemy nad projektami, które w przyszłości mogą przynosić korzyści zakładom zlokalizowanych na całym świecie. Co roku realizujemy kilka tego typu projektów.
- Jakie wdrożenia zrealizowaliście? Jak wygląda cyfryzacja produkcji?
DD: Pierwsze kroki polegały na łączeniu maszyn z systemem MES (Manufacturing Execution System). Chodziło tu o zbieranie danych operacyjnych i maszynowych, takich jak: przestoje techniczne i organizacyjne, informacje o awariach i ich przyczynach, o wdrożonych działaniach utrzymania ruchu, o wytworzonych produktach, itd. Dzięki temu użytkownicy zyskują ważne informacje, które pozwalają optymalizować produkcję.
Kolejnym wyzwaniem było usprawnienie przepływu informacji. Zdecydowaliśmy się na wdrożenie Active Cockpit, gdzie dane są zbierane według określonej grupy docelowej i udostępniane zgodnie z przeznaczeniem. Interaktywne narzędzie do pracy grupowej pozwala na wielowarstwowe zarządzanie eskalacją oraz zapewnia szybkie wykrywanie wszelkich odchyleń.
Dane z systemu MES transferowane są automatycznie przed codziennymi spotkaniach operacyjnymi. Pracownicy oszczędzają czas na przygotowanie się do spotkania, dzięki czemu mogą się skupić na tym, co dla nich najważniejsze, a środowisko zyskuje na zaoszczędzonym papierze.
Zastanawiamy się nad wdrożeniem rozwiązań używanych w innych zakładach Boscha, tj. Nexeed PPM (Production Performace Manager). Oprogramowanie umożliwia zbieranie danych z maszyny, a następnie pozwala wyodrębnić spersonalizowane informacje i automatycznie zastosować zebraną wiedzę. Przetworzone informacje są udostępniane użytkownikowi do określonych celów. W związku z tym można skrócić czasy reakcji i zapobiegać błędom.
- Czy do tych zmian musieliście się przygotowywać - np. modernizując park maszynowy?
SSz: Tak, był to kompleksowy projekt. Konsekwentnie wprowadzamy usprawnienia w całym zakładzie. Wszystkie maszyny i stacje musiały zostać podłączone do systemu, a całość odpowiednio zaprogramowana. Proces integracji starych maszyn nie był prosty, w części przypadków musieliśmy też rozszerzać oprogramowanie.
Aczkolwiek Bosch ma tutaj kilka ciekawych rozwiązań, takich jak choćby IoT Gateway. Umożliwia on zbieranie danych przesyłanych w sieci, przy czym nie trzeba ingerować w oprogramowanie maszyn. Moduł nasłuchuje komunikatów w sieci, przechwytuje odpowiednie i przesyła informacje do systemu MES.
Drugą z istotnych grup zmian były te dotyczące procesów. Wprowadziliśmy między innymi levelling produkcji, zastosowaliśmy rozwiązania do kontroli zapotrzebowania i przepływu materiałów, zaś trzecim etapem było wdrożenie RFID. Kluczem do sukcesu był dobry plan i konsekwentne działania.
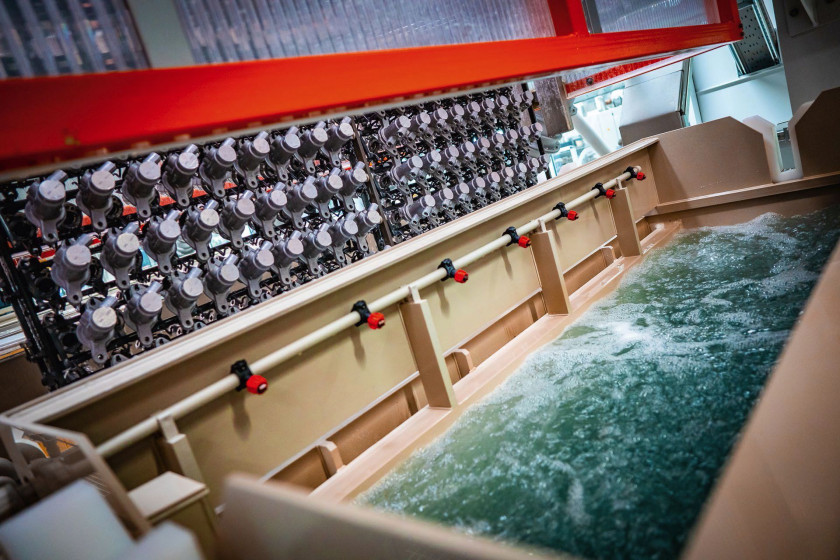
- Z jakich rozwiązań RFID korzystacie?
Jakub Jerzyk: Rozbudowujemy system RFID automatyzujący zadania produkcyjne i intralogistyczne. Wykorzystujemy go do identyfikacji obiektów takich jak kanbany produkcyjne, które odpowiadają za transfer komponentów i wyrobów pomiędzy kolejnymi obszarami fabryki.
Dawniej proces potwierdzeń wymagał tu stosowania skanerów mobilnych oraz dostępu do komputera, które operator wykorzystywał w celu "potwierdzenia na stan" przyjęć w systemie. Było to niezbędne ze względu na wymogi śledzenia przepływu produktów - przy fizycznym przesuwaniu towarów musiał też następować ich "ruch" w systemie ERP.
Jeżeli przyjmiemy, że jedna operacja zapisu w systemie to kilkadziesiąt sekund i przemnożymy nawet kilkaset takich zdarzeń w skali zmiany, to sumaryczne czasy były długie. Tymczasem kanban wyposażony w tag RFID pozwala zapewnić automatyzację przepływu towarów, zapewniając aktualne informacje o ich lokalizacji i stanie. Korzystamy również z tzw. e-kanbanów, dzięki którym dostawca komponentów jest informowany o konsumpcji produktów na linii. W efekcie zamówienia (tzw. replenishments) są tworzone i wysyłane automatycznie.
Wdrażanie RFID zaczęliśmy w 2017 roku i na razie mamy kilkadziesiąt czytników wdrożonych w części zakładu. Oceniamy, że ich implementacja pozwoliła na zmniejszenie liczby manualnych operacji zapisów blisko o połowę! W 2019-2020 rozszerzymy zastosowania RFID na kolejne obszary - m.in. obróbki skrawaniem, na pozostałe linie montażu finalnego oraz na magazyn wyrobów gotowych.
- Właśnie - jak wygląda to w zakresie logistyki? Tego typu projekty również realizowane były w zakładzie Boscha w Blaichach…
JJ: W naszym zakładzie również mamy bramkę RFID zainstalowaną w części magazynowej. Umożliwia ona automatyczne przyjmowanie transportów komponentów bez konieczności manualnego przetwarzania. Wystarczy, że pracownik logistyki przejedzie wózkiem przez bramkę, a całość dostawy zostaje wtedy zaksięgowana jako przyjęcie magazynowe. Oczywiście taki proces wymaga odpowiedniej umowy z dostawcą komponentów.
Obecnie w ten sposób współpracujemy z wewnętrznym dostawcą modułów ECU z Niemiec. Są to bardzo drogie elementy i nie są one magazynowane - trafiają praktycznie bezpośrednio na linię produkcyjną.
Dzięki temu mogliśmy znacząco ograniczyć zapasy, a w rezultacie też ponoszone koszty. Docelowo chcielibyśmy, aby wszystkie podzespoły pochodzące z różnych zakładów były automatycznie zapisywane w systemie podczas przyjęć. Jest to dla nas temat do zrealizowania w najbliższej przyszłości.
- Czy wykorzystanie RFID dotyczy też innych obszarów?
Robert Łucyszyn: Rozwiązania komunikacji radiowej stosujemy coraz szerzej również w maszynach i obszarze utrzymania ruchu. Dobrym przykładem są narzędzia skrawające do maszyn CNC, które są bardzo kosztowne i wymagają regularnej kontroli. Korzystamy z chipów Balluffa montowanych w oprawkach narzędziowych, które przechowują dane o narzędziu i jego nastawach. Zapewnia to pełną identyfikowalność oraz kontrolę zużycia narzędzi.
Poprzedni proces zapisu danych był ręczny na etykiecie przyklejonej do oprawki i ręcznie wprowadzany do maszyny CNC, co mogło powodować błędy. Dodatkowo etykiety na narzędziach miały tendencje do ścierania się i odrywania. Mając chipy, jesteśmy pewni, jaką historię ma każde narzędzie. Również jeżeli dojdzie do uszkodzenia narzędzia, to znamy okoliczności z tym związane. Dzięki temu możemy zminimalizować ryzyko defektów oraz zwiększać jakość produktów.
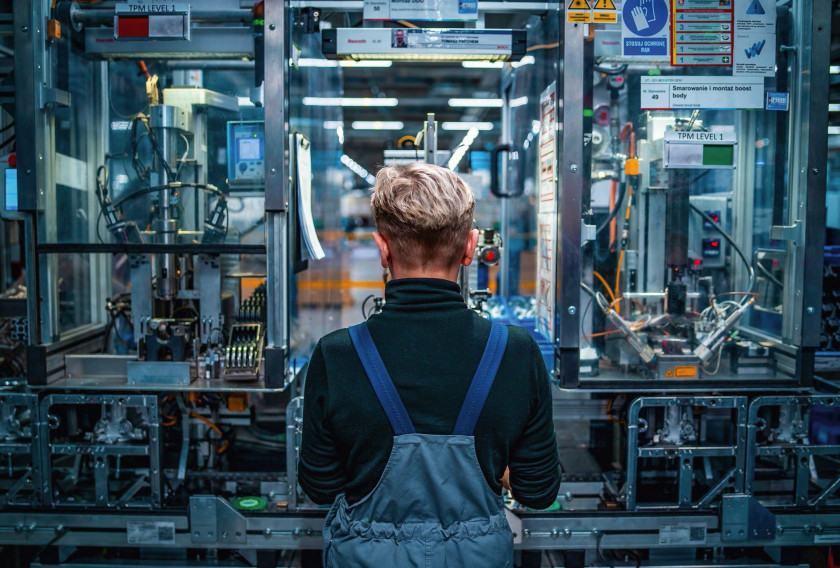
- Czy policzyliście finansowe korzyści z tego wynikające?
RŁ: Tak - uzyskujemy średni wzrost OEE o około 1,5%, co wynika m.in. ze zmniejszenia długości przezbrojeń maszyn oraz skrócenia czasu raportowania. Koszt inwestycji zawraca się po 1,5 roku tylko z oszczędności na narzędziach skrawających.
Dodam, że stosujemy również rozwiązanie upraszczające zgłaszanie awarii. Dawniej operator maszyny, aby zgłosić awarię lub inne zakłócenie, musiał podejść do komputera, zalogować się i wygenerować zgłoszenie w SAP. Obecnie każda maszyna ma naklejkę z kodem QR, który może być zeskanowany z wykorzystaniem smartfona.
Po zeskanowaniu operator otrzymuje automatycznie autoryzację do SAP wraz z danymi maszyny i pozostaje mu tylko napisać krótką informację o zdarzeniu, może również dołączyć zdjęcie lub film i wysłać zamówienie do SAP. A służby utrzymania ruchu mogą na miejscu odczytać kod QR, zyskując dostęp do całej historii maszyny, a także do dokumentacji technicznej. Całość zdecydowanie przyspiesza procesy utrzymania ruchu i poprawia dostępność maszyn do produkcji.
- W halach produkcyjnych stosujecie też wspomniane rozwiązania Active Cockpit - duże, interaktywne ekrany wyświetlające informacje produkcyjne. Jaka jest ich rola?
Krzysztof Serwatka: Active Cockpit stanowi dla nas punkt CIP, czyli Continous Improvement Point. System zbiera informacje produkcyjne, procesowe i inne, i codziennie rano odbywają się przy nim grupowe spotkania. Pierwszym omawianym punktem są tematy bezpieczeństwa - jeżeli zdarzają się takie alarmy, to widzimy je automatycznie.
Kolejnymi punktami są m.in.: jakość, reklamacje, przegląd braków oraz cele. Możemy też na bieżąco obliczać i wyświetlać statystyki dotyczące wydajności w podziale na różne parametry i dla różnych osób - np. planistów, team leaderów, zarządu. W ten sposób szybko rozwiązujemy potencjalne problemy i planujemy przyszłe działania.
SSz: Idea stojąca za wdrożeniem systemów Active Cockpit była taka, aby danych, raportów i innych informacji nie przygotowywać i nie rozwieszać ręcznie. Zadania te wykonywali codziennie team leaderzy oraz inne osoby - czasami wręcz zatrudniane tylko w tym celu!
Gdy wprowadziliśmy nowe rozwiązanie, mogliśmy usunąć tradycyjne tablice, zaś pracownicy zyskali możliwość zajęcia się czymś bardziej satysfakcjonującym niż drukowanie raportów. Dodatkowo wszyscy zainteresowani automatycznie otrzymują po spotkaniach tzw. minutki.
- We Wrocławiu realizujecie również autorskie projekty, które później mogą być wykorzystywane w innych oddziałach firmy - jak to wygląda?
PP: Obecnie tworzymy projekt związany z zarządzaniem pracownikami, co powiązane jest z koniecznością nadzoru nad kompetencjami. Zagadnienie jest o tyle istotne, że w naszym regionie mamy do czynienia z dużym popytem na pracowników, a rotacja jest dzisiaj nieco większa niż w latach ubiegłych.
Ponadto w zakładzie produkujemy komponenty bezpieczeństwa. Stąd też chcemy, aby każda z osób miała identyfikator, który będzie ją dopuszczał do pracy na danej linii produkcyjnej - pod kątem posiadanych kompetencji, przeszkolenia a nawet ważnych badań lekarskich. Sądzimy, że znacząco uprości to pracę team leaderów, a także osób w dziale HR.
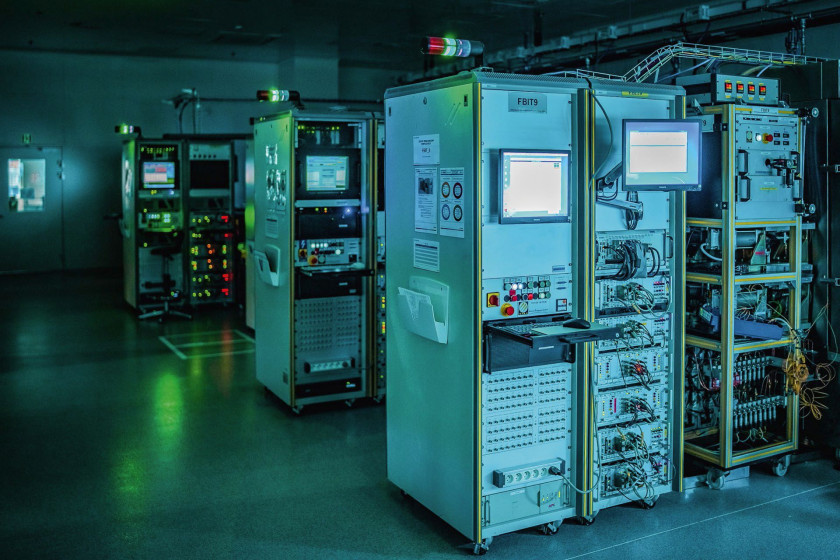
- Co zmienia się w obszarze zarządzania na skutek wprowadzanych zmian?
PP: Z perspektywy managementu cyfryzacja daje dwojakie korzyści - możemy porównywać się do innych fabryk i linii produkcyjnych, zaś lokalnie uzyskujemy ogromną dostępność i transparentność danych. Każdy proces decyzyjny to kilka pytań: "gdzie jesteśmy?, "gdzie chcemy być?" i "jakie podjąć działania, aby się tam znaleźć?". Dzięki cyfryzacji mamy praktyczne gotowe odpowiedzi na pierwsze z pytań i możemy skupić się na wypracowaniu lepszych rozwiązań.
Dodam, że o ile dawniej wiele osób korzystało równolegle z systemu MES i tradycyjnej dokumentacji, o tyle obecnie praktycznie nikt nie myśli o stosowaniu raportów papierowych czy tych w Excelu. Wszystko zapisujemy i rozwiązujemy w ramach posiadanego systemu, również z niego pozyskujemy wszystkie dane.
DD: Zautomatyzowane zbieranie danych i raportowanie pozwala na eliminowanie błędów oraz wpływu ludzi na wskaźniki. Możemy zwiększać wydajność, przy czym nie chodzi tu o zwiększanie tempa pracy, ale lepsze korzystanie z zasobów, które już mamy. Sądzę, że dzięki cyfryzacji mogliśmy uniknąć dodatkowych inwestycji, a jednocześnie podwyższać naszą produktywność.
- A jeżeli chodzi o porównywanie się z innymi zakładami - czy to również robicie?
PP: Zdecydowanie tak. Korzystamy z cross benchmarkingu linii produkcyjnych - u nas i w innych zakładach - i jest to moim zdaniem jeden z największych benefitów związanych z posiadaniem "zdigitalizowanej" produkcji. Możemy wzajemnie podpatrywać najlepsze rozwiązania. Stanowi to również świetny motywator do wprowadzania zmian, bowiem wiemy, że wyznaczane cele są osiągalne.
Omawiane podejście sprzyja również dodatkowej innowacyjności i wypracowywaniu własnych pomysłów, tak aby realizować efekt. Jeżeli później zestawi się nowe koncepcje pochodzące z całego świata, to okazuje się, że suma wytworzonej w organizacji wiedzy jest większa niż w przypadku osobnych zakładów, które rozwijałyby się samodzielnie.
DD: Porównywanie ze sobą fabryk zapewnia oderwanie się od subiektywnej oceny, a digitalizacja umożliwia porównanie wskaźników według tej samej miary. Benchmark pomiędzy zakładami lub grupami produktowymi daje możliwość optymalizacji dostępnych zasobów i ułatwia planowanie inwestycji.
- Jak cyfryzacja wpływa na pozycję polskiego zakładu w ramach Grupy Bosch?
SSz: O ile dawniej postrzegano nas jako producenta prostszych, mechanicznych wyrobów, o tyle dzięki wprowadzanym zmianom i cyfryzacji produkcji udowodniliśmy, że potrafimy być innowacyjni. Sądzę, że było to istotnym powodem otrzymania możliwości produkowania iBoostera pierwszej generacji.
Wtedy też wdrożyliśmy nowy system MES, z czym dobrze sobie poradziliśmy. W efekcie zostaliśmy też wytypowani do produkcji kolejnej generacji wyrobów. Audytujący nas klienci widzą, że fabryka jest nowoczesna i korzysta z rozwiązań cyfrowych. Wszystko to korzystnie wpływa na nasz wizerunek na rynku.
WG: Sądzę, że digitalizacja to kolejny etap naszego rozwoju. Produkcja coraz silniej opiera się na cyfryzacji i od tego nie uciekniemy. W tym roku we Wrocławiu tworzona jest też komórka rozwijająca kompetencje z obszaru MES. Uważam, że to właśnie lokalna kadra projektantów, specjalistów oraz innych pracowników stanowi o naszej sile i daje nam dobre perspektywy również na przyszłość.
- Dziękujemy za rozmowę.