Jak widać - pierwszym krokiem przed przystąpieniem do jakichkolwiek działań jest pozyskanie danych, na bazie których stworzone zostaną procedury optymalizacji. W zakładach poważnym pretendentem do roli uniwersalnego standardu komunikacji w automatyce przemysłowej jest OPC UA.
Rys. 1.
Integracja danych z urządzeń zainstalowanych na maszynach, a obsługiwanych przez lokalne układy sterowania, z systemami nadrzędnymi i dalej z systemami MES i ERP, powinna być wykonywana w sposób w pełni zautomatyzowany i niewidoczny dla użytkownika.
Koszt wdrożenia systemu obsługującego wymianę danych nie może przekraczać oczekiwanych korzyści, więc ważne jest zastosowanie rozwiązań wymagających jak najmniejszych nakładów na sprzęt, oprogramowanie oraz czas potrzebny na konfigurację.
Istnieje duże prawdopodobieństwo, że poprawa efektywności w zakładzie przemysłowym będzie przeprowadzana metodą prób i błędów, ponieważ trudno określić, które działania będą miały pozytywny wpływ na wyniki finansowe. Wymagana jest więc elastyczność w przetwarzaniu i interpretacji rejestrowanych danych, możliwość wyznaczania nowych wskaźników efektywności i adaptacji do zmieniającej się sytuacji w zakładzie i rosnącej wiedzy na temat przyczyn nieoptymalnej pracy.
Opracowanie uniwersalnego modelu komunikacji wydaje się rozwiązaniem optymalnym z punktu widzenia kosztów wdrażania systemów służących poprawie efektywności zakładu. Integracja danych często jest niełatwym zadaniem ze względu na obecność na rynku znacznej liczby dostawców systemów automatyki, stosujących różne standardy komunikacji.
Jeśli w zakładzie przemysłowym zachowywana jest standaryzacja w zakresie na przykład sterowników PLC, układów I/O i napędów dostarczanych przez jednego producenta, komunikacja pomiędzy tymi urządzeniami zwykle jest ułatwiona dzięki możliwości zastosowania standardowego dla urządzeń danego producenta protokołu komunikacji.
Łatwiej też wypracować dobre praktyki w zakresie adresacji urządzeń i nazewnictwa zmiennych. W praktyce nie jest możliwe zastosowanie jednego protokołu komunikacji, ponieważ pewna liczba urządzeń nie będzie obsługiwać standardowego protokołu preferowanego w zakładzie. Mogą być to na przykład liczniki energii lub inne urządzenia pomiarowe.
W zakładzie przemysłowym, w którym dane ze wszystkich urządzeń miałyby być dostępne w systemach MES lub ERP, zawsze będzie występować konieczność konwersji przynajmniej części danych na inny protokół komunikacji. Docelowym rozwiązaniem jest możliwość przekazywania danych z czujników, napędów, itp. bezpośrednio do systemów, które będą wykorzystywać zebrane dane za pośrednictwem jak najmniejszej liczby urządzeń pośrednich, które są kosztowne i wymagają konfiguracji.
Dotyczy to również wymiany danych pomiędzy maszynami (na przykład wchodzącymi w skład jednej linii produkcyjnej). W idealnej sytuacji dane powinny być dostępne dla wszystkich uprawnionych do ich przetwarzania odbiorców, zarówno na poziomie zakładu przemysłowego (wymiana danych między maszynami), jak i na poziomie zarządzania produkcją (przesyłanie danych np. do systemu MES).
Można wyobrazić sobie model, w którym konfiguracja komunikacji i przypisywanie zmiennych będzie ograniczać się tylko do wybrania konkretnej nazwy z rozwijanej listy, zamiast żmudnego przepisywania adresów rejestrów, przypisywania nazw zmiennych i pilnowania kolejności adresowania przy konwersji pomiędzy kolejnymi protokołami. Krokiem w tę stronę jest zastosowanie w OPC UA modelu obiektu, wprowadzenie klas i metod. Dzięki architekturze zorientowanej na usługi wykorzystywane są tylko te funkcje, które są aktualnie potrzebne.
Celem jest sytuacja, w której sukcesem nie jest poprawna konfiguracja, integracja i uruchomienie systemu, ale realizacja postawionych mu zadań w jak najkrótszym czasie, przy jak najniższych nakładach finansowych i z możliwie najlepszym skutkiem.
Przesunięcie w tło i minimalizacja zadań związanych z projektowaniem, realizacją i uruchomieniem systemu na rzecz zwiększonej pracy nad osiągnięciem wymaganego rezultatu jest jednym z podstawowych problemów dostawców rozwiązań Przemysłu 4.0.
Architektura PUBSUB
Jednym z podstawowych założeń IIoT jest wymiana danych pomiędzy dużymi liczbami inteligentnych urządzeń z zastrzeżeniem, że nie muszą to być urządzenia mające dużą moc obliczeniową, na przykład inteligentne czujniki. Konsekwencją ograniczonej mocy obliczeniowej jest konieczność minimalizacji zużycia pamięci i mocy procesora.
27 marca 2018 OPC Foundation opublikowała specyfikację modelu wymiany danych Publish-Subscribe (PubSub), w której w odróżnieniu od architektury klient/serwer nie jest wymagane utrzymywanie stałego połączenia, co pozwala na zmniejszenie zużycia pamięci. W architekturze PubSub wiadomości są rozgłaszane do całej sieci, a urządzenia lub programy, które mają je wykorzystać, subskrybują się na dany typ wiadomości.
To dobre rozwiązanie w sytuacji, w której jedna aplikacja gromadzi dane z wielu publikujących je urządzeń. Obsługiwane są protokoły MQTT, AMQP lub UDP. Zachowana jest kompatybilność z modelem klient/serwer.
Standard TSN
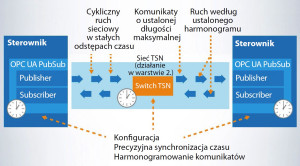
Rys. 2.
Niedoskonałości klasycznego Ethernetu w zakresie niezawodności i determinizmu doprowadziły do powstania pewnej liczby standardów Ethernetu przemysłowego. Niestety technologie te, opracowywane przez niezależnych od siebie dostawców systemów automatyki, nie są ze sobą kompatybilne. Współczesne przemiany w podejściu do rejestracji i obsługi danych z maszyn zmuszają do integracji systemów różnych producentów.
Konwersja danych jest związana z opóźnieniami w transmisji, obniżoną niezawodnością i jest kosztowna ze względu na konieczność stosowania dodatkowego sprzętu i oprogramowania oraz poświęcenia czasu potrzebnego na konfigurację komunikacji.
Rozwiązaniem może stać się TSN (Time-Sensitive Networking) - opracowywany przez IEEE nowy uniwersalny standard przemysłowego Ethernetu o dużej niezawodności, nastawiony na determinizm i dostarczanie komunikatów w określonym z góry czasie z niewielkim opóźnieniem i bez strat. Jest to istotne w zastosowaniach przemysłowych, gdzie synchronizacja w czasie danych pochodzących z różnych urządzeń może mieć kluczowe znaczenie dla prowadzonego procesu.
Zastosowanie TSN do transmisji danych za pomocą OPC UA ma stanowić sposób na umożliwienie komunikacji w systemach IIoT pomiędzy urządzeniami różnych producentów, niezależnie od platformy sprzętowej i stosowanego oprogramowania. Użycie modelu PubSub umożliwi tworzenie systemów działających w czasie rzeczywistym. Standard TSN ma zachowywać kompatybilność ze standardowym Ethernetem, dzięki czemu możliwe będzie wykorzystanie istniejących sieci.
Integracja z systemami Industry 4.0
Posiadanie danych i możliwość przesyłania ich w bezpieczny sposób to jednak dopiero początek. Do pełnego wykorzystania gromadzonych informacji potrzebne są narzędzia do ich przetwarzania i prezentacji w formie umożliwiającej wykorzystanie zdobytej wiedzy. Mogą być to na przykład systemy informatyczne klasy ERP lub MES oraz przemysłowe systemy diagnostyczne lub eksploatacyjne.
Standard OPC UA jest wspierany przez Microsoft, chociaż nie jest już, tak jak poprzednia wersja, ściśle związany z systemem operacyjnym Windows. Komunikacja za pośrednictwem OPC UA jest podstawowym sposobem połączenia urządzeń automatyki przemysłowej z usługami Microsoftu stworzonymi do cyfryzacji zakładów przemysłowych przy użyciu platformy Azure.
Dzięki Azure IoT Connected Factory możliwe jest połączenie urządzeń znajdujących się w zakładzie z usługami Microsoft Azure. Jest to zestaw rozwiązań pozwalający na połączenie z chmurą, dzięki współpracy Microsoftu z kilkoma renomowanymi dostawcami gatewayów IoT. Dostępne są narzędzia pozwalające na szybkie przeprowadzenie symulacji w celu identyfikacji potencjalnych korzyści, następnie połączenie danych z urządzeń z chmurą i finalnie wizualizację gromadzonych danych.
Standard OPC UA jest również wykorzystywany przez SAP jako sposób na implementację rozwiązań IIoT i M2M w oprogramowaniu tej firmy. Zestaw narzędzi SAP Plant Connectivity umożliwia przesyłanie danych pomiędzy maszynami mającymi odrębne systemy sterowania oraz na połączenie z narzędziami zawartymi w pakiecie SAP Manufacturing.
W zależności od potrzeb jednostki podłączone do Plant Connectivity mogą być serwerami lub klientami OPC UA, ewentualnie pełnić obie funkcje jednocześnie, jeśli jest to wymagane. Dzięki temu możliwa jest wymiana tagów, zdarzeń i wywoływanie metod, a w praktyce przesyłanie zleceń produkcyjnych, danych do receptur, wartości zadanych z systemu MES do maszyn, a także wymiana danych pomiędzy maszynami i urządzeniami, na przykład pomiędzy systemem wizyjnym a robotem.
OPC UA jest wykorzystywane przez czołowych dostawców oprogramowania przemysłowego korzystającego z IIoT. Zastosowanie standardu, którego twórcom przyświecała idea jak najszerszego upowszechnienia, może być też sposobem na przyspieszenie i zmniejszenie kosztów wdrożenia dla mniejszych firm opracowujących swoje rozwiązania Industry 4.0. Czas i koszty mogą być w wielu przypadkach poważną barierą.
Dostawcy branży automatyki przemysłowej współpracują
Wiodący producenci z branży automatyki przemysłowej, między innymi Rockwell Automation, ABB, B&R, KUKA, National Instruments, Phoenix Contact, Pilz i Schneider Electric, nawiązali niedawno współpracę w celu opracowania standardu wykorzystującego OPC UA TSN umożliwiającego bezproblemową integrację danych w systemach łączących dane z maszyn z aplikacjami w chmurze.
Czas pokaże, czy OPC UA stanie się powszechnym standardem Przemysłu 4.0. Specyfikacja jest bardzo obszerna, a dotychczas istniejące implementacje korzystają z niej w sposób wybiórczy, wykorzystując część usług i metod, co nie sprzyja kompatybilności. Pojawiają się również wątpliwości co do bezpieczeństwa danych (o tym w kolejnej części artykułu).
Działania OPC Foundation oraz współpracujących z nią firm mają na celu dopracowanie specyfikacji, ujednorodnienie implementacji, stworzenie dobrych praktyk i rozpropagowanie OPC UA. O ile zastosowanie OPC UA w urządzeniach klasy sterowników PLC lub w oprogramowaniu zainstalowanym na komputerach przemysłowych zdobyło już pewną popularność, o tyle zejście na sam dół, do poziomu przetworników pomiarowych czy elementów wykonawczych, wymagać będzie jeszcze sporo czasu.
Piotr Ziółkowski